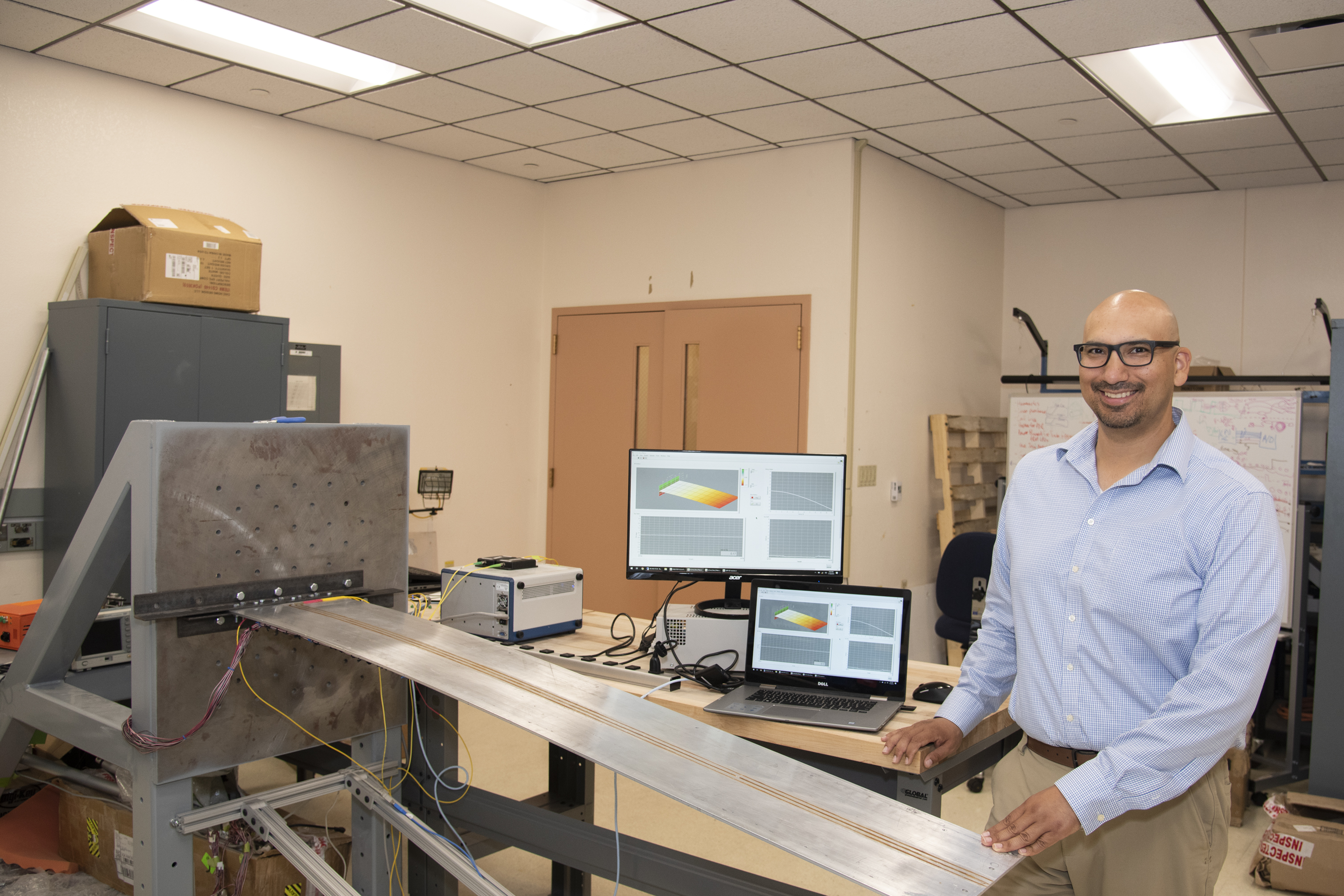
NASA Innovator Frank Pena working in his lab at AFRC.
I am an aerospace engineer in the Aerostructures Branch at NASA’s Armstrong Flight Research Center. I was inspired from an early age to pursue engineering. So, I decided to get my undergraduate degree in mechanical engineering from the University of California at Santa Barbara.
What brought you to NASA?
I always wanted to work at NASA. After undergrad, I had a job certifying aircraft components, and that’s when I really knew aerospace was an interest. So, I went on to get a master’s degree at California State University, Los Angeles. In 2012 I had the opportunity to intern at NASA. When I finished up my degree, I applied for and was selected for a position at Armstrong.
Tell us about your research.
I’ve been working on the shape-sensing algorithms used in the Fiber Optic Sensing System (FOSS). FOSS uses optical fibers attached to a structure to distribute thousands of sensors in a vast network—much like the human body’s nervous system—that provides real-time information about a wide range of parameters. I have developed new algorithms that use the sensors’ measurements of elongation—or stretch—to render the shape of the overall structure.
What does this invention do?
My new algorithms improve the accuracy of 3D shape-sensing for highly flexible structures. They do this by providing a convenient way to calculate distributed deformed orientation angles—that is, roll, pitch, and yaw—as well as determine the deformed shape of an object in 3D space. I employed quaternion mathematical operations, which is a faster process than rotation matrices used in previous shape-sensing algorithms.
By tracking displacement, twist, and rotation all at the same time, the technology can convert distributed surface strain data into deformed shapes that can be displayed and analyzed in real time.
What problem does this technology solve?
The goal was to be able to more accurately determine 3D shape and calculate the operational load of nonlinear flexible surfaces, such as aircraft wings. In fact, we validated the new algorithm on the large-scale passive aeroelastic tailored (PAT) wing. By reliably providing highly accurate information in real time, this technology enables the structural integrity of large structures to be monitored, allowing engineers to take corrective action to avert disasters.
Who else might benefit from this technology? What other applications do you envision?
It has the potential to be used for structural health monitoring of buildings, bridges, oil platforms, ocean vessels, wind turbines, and other large structures. It also could be used in designing car and truck frames and suspension for dynamic control and handling. It could even be used to ensure loads are balanced safely on cargo ships.
Do you have any future plans to continue development of this technology?
As we work on NASA-specific projects, we also try to evaluate how FOSS could potentially address industry challenges. For example, we’ve been looking at some medical applications—FOSS could be used in robotic surgery or in vascular procedures. Whatever the unique scenario, the algorithm is revised to meet it.
Is there anything else you want us to know about your innovation?
It was originally developed to be used in conjunction with Armstrong’s FOSS technology, but it can be integrated into commercial fiber optic sensing systems.
Whom should I contact if I want to know more about this technology?
The Technology Transfer Office at NASA’s Armstrong Flight Research Center.
Learn more about this technology here.