Search
Sensors
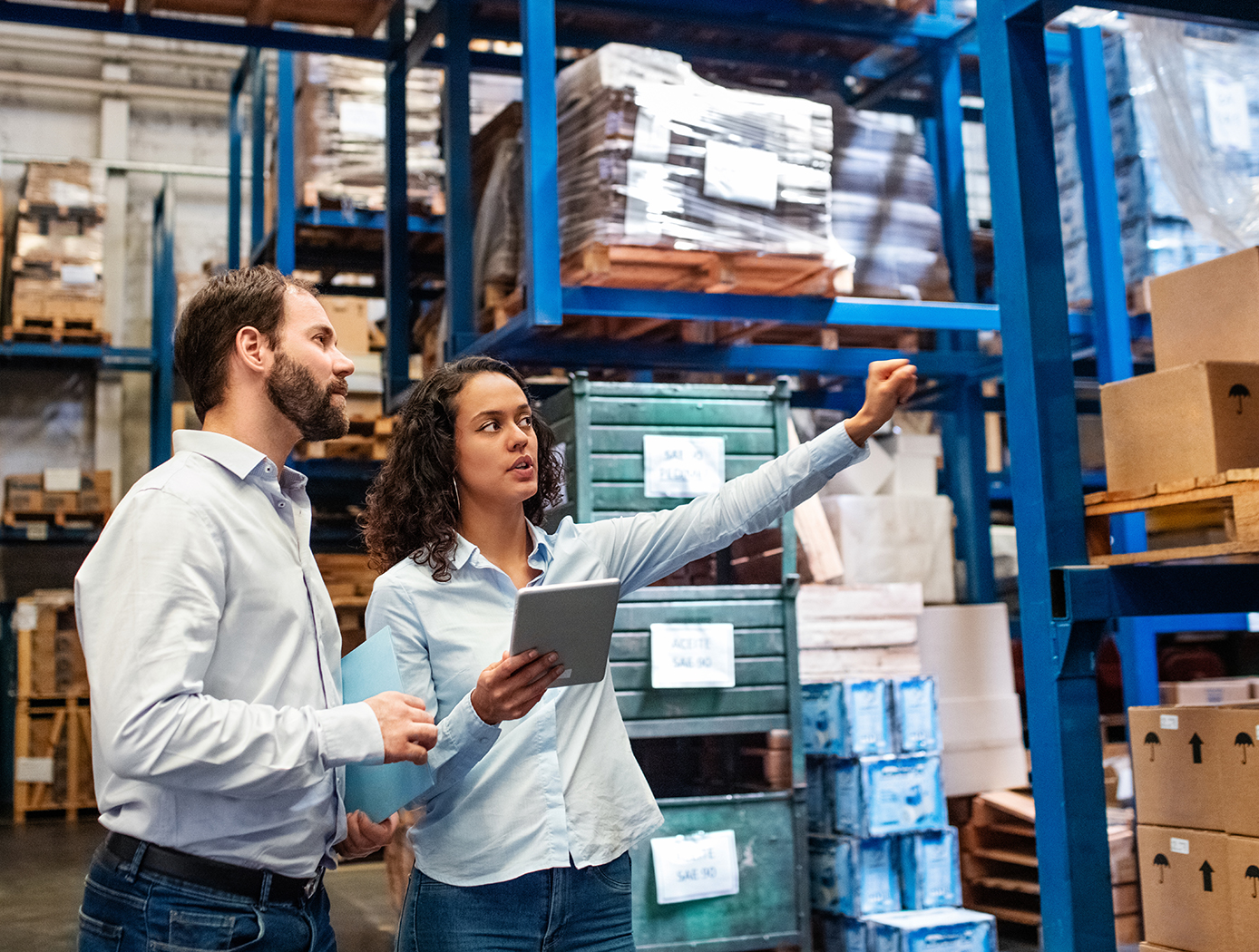
Hyper-Distributed RFID Antenna (HYDRA) System
Components of the HYDRA system include an RFID reader (aka an RFID transceiver or interrogator), RF cables, antennas, and one or more Intelligent Multiplexer Modules (IMMs). The IMM is the core building block of the HYDRA system. In one of its basic embodiments, the IMM comprises an RF directional coupler, RF switch, RFID chip, micro-controller, and power generation and management hardware. In this basic implementation, a single RF port from the RFID reader is attached to the IMM and transfers power thereto. Internally within the IMM, the RF directional coupler diverts a small amount of RF power to rectification and power management circuitry for conversion to DC power that drives the RFID chip, microcontroller, and RF switch. The RFID chip enables communication with the RFID reader and allows the reader to administer changes to the microcontroller‘s embedded software. The microcontroller controls the RF switch, which passes power along to one or more output channels. Connections to the output channels can include antennas, additional IMMs, or other sensors.
The HYDRA system may include numerous alternate embodiments to enhance and customize the basic functionality. In one embodiment, the microcontroller is replaced with a simple timer. In another embodiment, the switch has multiple output ports to connect to a distributed chain of HYDRA system or local antennas. Also, the entirety of RF power exiting a HYDRA module can be rectified and used to power a local sensor node, which could be implemented via WiFi or Bluetooth Low Energy (BLE). Features of the HYDRA system include the ability to cover both open regions and enclosures, the ability to switch RF power to an unused load for assisting in the resolution of tag antenna ambiguities, and the ability to accept plug-and-play add-ons such that the reader’s software can use the system without requiring any embedded modifications.
The HYDRA system is technology readiness level (TRL) 7 (system prototype demonstrated in an operational environment) and is now available for patent licensing. Please note that NASA does not manufacture products itself for commercial sale.
Sensors

RFID Tags Collaborate for Data Retrieval
Commonly used RFID protocols are widely accepted because they are inexpensive and easy to implement. However, the associated low transmit power and narrow bandwidth typically result in coarse local-ization estimates. Often it is desirable to know the precise location of assets without reverting to an entirely different and more expensive protocol. Additionally, many industrial and other applications may desire technology that confirms the mating of components. This new program-mable sensor tag technology facilitates both precise localization and mating confirmation in-part by allowing the RFID sensor tag to become a type of distributed low-cost reader.
To determine a tag attachment, this innovation utilizes a fixed location RFID sensor tag that incorporates a receptacle node to measure an electrical “influence” through resistance, capacitance, inductance, etc. Assets for which localization is desired are outfitted with “influence tags” – devices that produce a set of distinguishable responses when placed in the receptacle region of the RFID sensor tag. Mating or connections are confirmed when electrodes from an influence tag become attached to matching electrodes on a sensor tag’s receptacle node. Information obtained by the RFID sensor tag is stored in its local memory bank through which a dedicated reader can retrieve influence tag information.
Potential applications exist for this technology where specific assets need to be precisely located and/or confirmation is needed when two parts have been correctly connected or attached. This RFID tag technology allows the retrieval of inventory status information in an energy efficient manner from inexpensive, small form factor hardware. Robotic retrieval of assets can be more easily facilitated with this innovation.