Search
Information Technology and Software
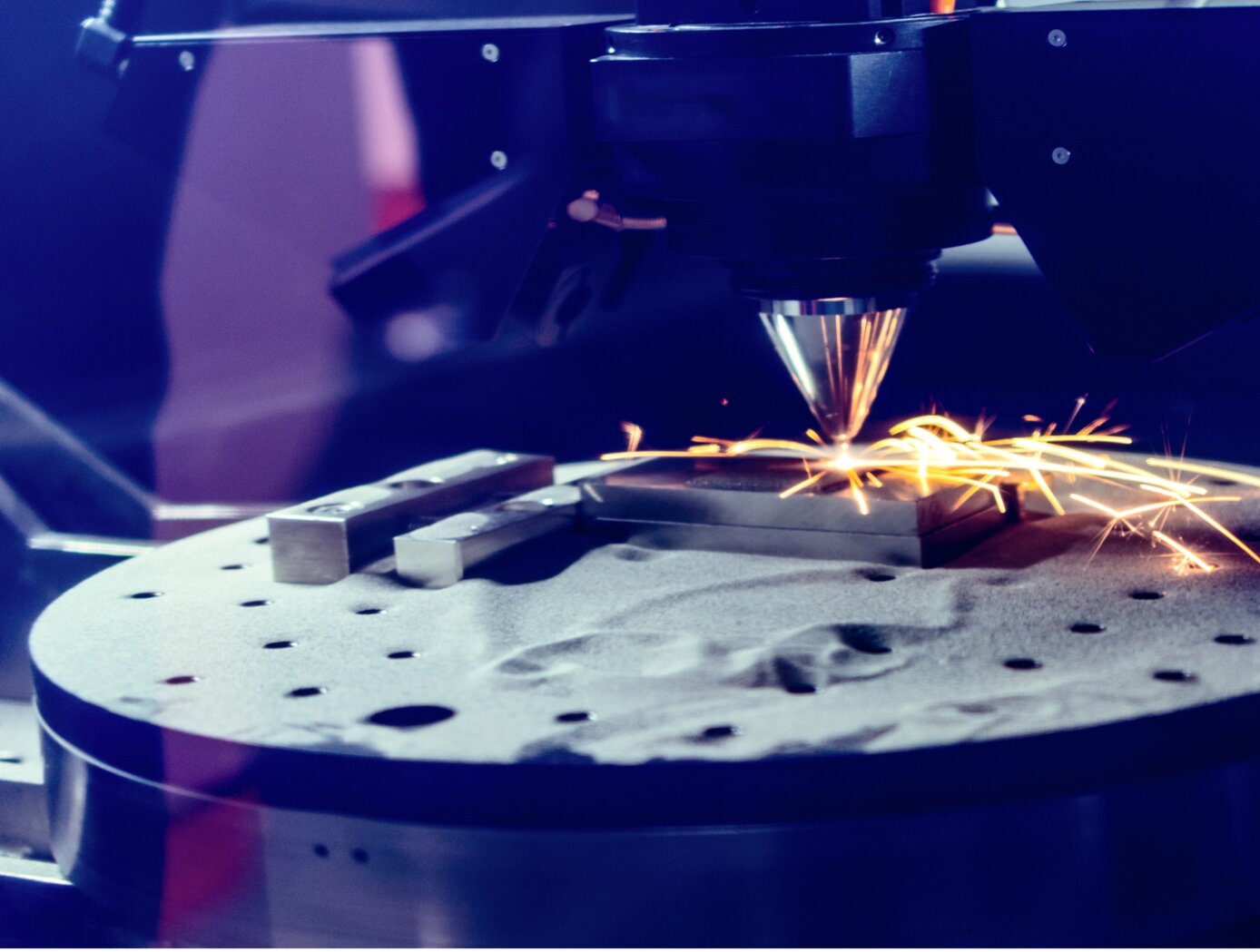
Additive Manufacturing Model-based Process Metrics (AM-PM)
Modeling additive manufacturing processes can be difficult due to the scale difference between the active processing point (e.g., a sub-millimeter melt pool) and the part itself. Typically, the tools used to model these processes are either too computationally intensive (due to high physical fidelity or inefficient computations) or are focused solely on either the microscale (e.g., microstructure) or macroscale (e.g., cracks). These pitfalls make the tools unsuitable for fast and efficient evaluations of additive manufacturing build files and parts.
Failures in parts made by laser powder bed fusion (L-PBF) often come when there is a lack of fusion or overheating of the metal powder that causes areas of high porosity. AM-PM uses a point field-based method to model L-PBF process conditions from either the build instructions (pre-build) or in situ measurements (during the build). The AM-PM modeling technique has been tested in several builds including a Ti-6Al-4V test article that was divided into 16 parts, each with different build conditions. With AM-PM, calculations are performed faster than similar methods and the technique can be generalized to other additive manufacturing processes.
The AM-PM method is at technology readiness level (TRL) 6 (system/subsystem model or prototype demonstration in a relevant environment) and is available for patent licensing.
Mechanical and Fluid Systems
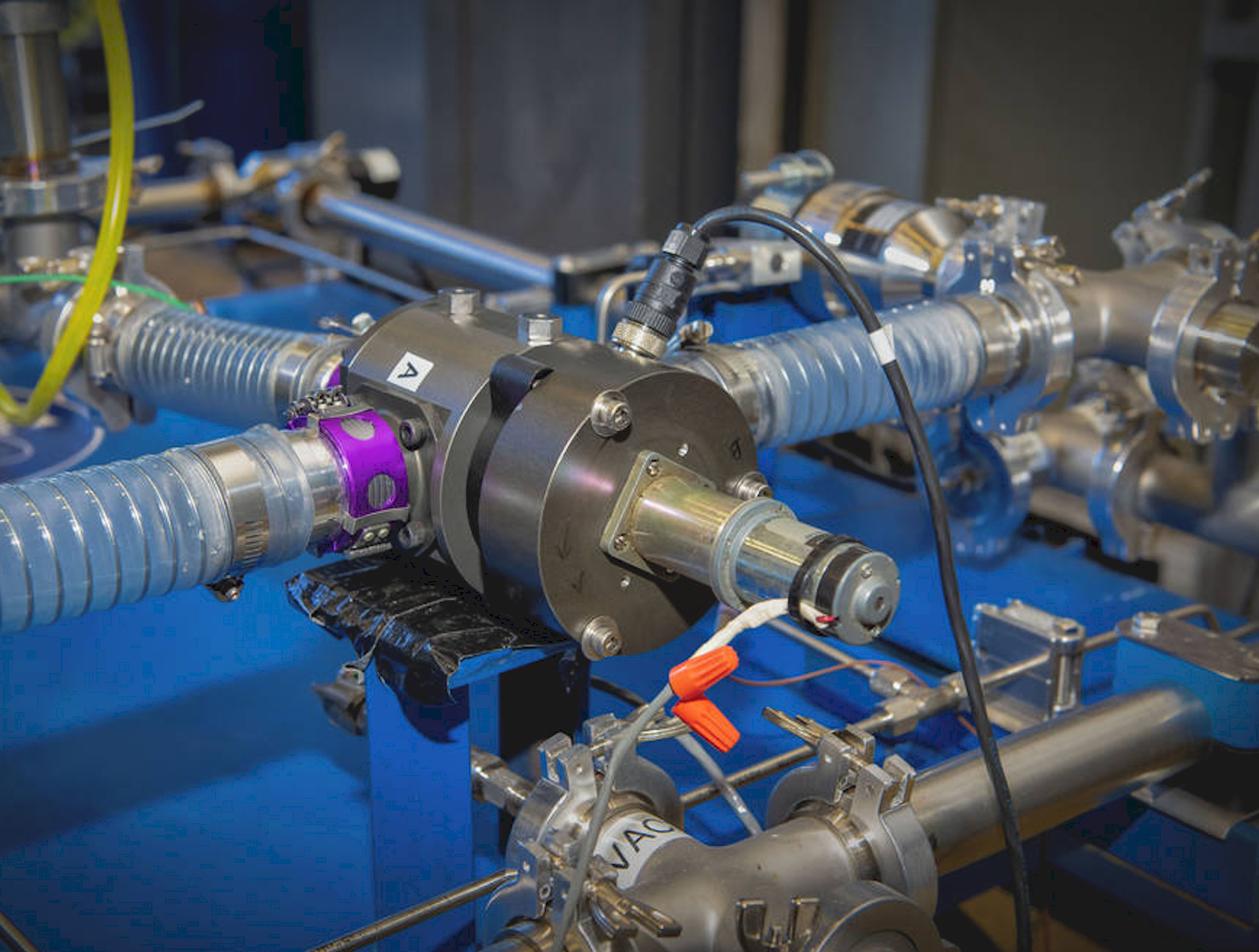
Debris-Tolerant Valve
NASA's Debris-Tolerant Valve is designed for use in machines/environments with a large quantity of airborne dust or other contaminants. Valves subjected to airborne contaminants tend to have limited lifetime due to damaged seals, bearings, and other internal components. The Debris-Tolerant Valve design addresses this problem with four core improvements over existing commercial valves that are typically used in dusty or debris-laden processes: (1) a new cylinder design that substantially decreases dust collection within the valve; (2) a rotational valve design that minimizes grinding and packing experienced by the standard ball valve; (3) the use of elastomeric seals rather than the Teflon-based seals used in existing valves which are prone to scratching and subsequent leakage; and (4) a bleed port for fluid intake that allows pressure to build slowly in the valve and eliminates the stirring of dust commonly caused by rapid inflow of air in existing valves.
The operational lifetime of NASA's Debris-Tolerant Valve exceeds the lifetime of a standard commercial valve and the existing selector valve used on the ISS by 12X and 6X, respectively. NASA's valve design has fewer parts than existing valves and could be disassembled without tools, enabling easier servicing and maintenance. The Debris-Tolerant Valve is only about one-seventh (1/7) the cost of the existing ISS selector valve.