Cryogenic Selective Surfaces
Materials and Coatings
Cryogenic Selective Surfaces (KSC-TOPS-59)
Maintaining Cryogenic Temperatures in Deep Space Using a Novel Thermal Coating
Overview
Thermal control coatings, i.e. coatings with different visible versus infrared emission, have been used by NASA on the Orbiter and Hubble Telescope to reflect sunlight, while allowing heat rejection via infrared emission. However, these coatings absorb at least 6% of the Sun's irradiant power, limiting the minimum temperature that can be reached to about 200 K. NASA needs better solar reflectors to keep cryogenic fuel and oxidizers cold enough to be maintained passively in deep space for future missions. This new thermal control coating material, developed for use as a spray on coating or rigid tiles, reflects essentially all solar radiation in the space environment. The novel material has the potential to be an enabler for long-term storage of cryogenic liquids and propellants in space. It can also support the long-term operation of low-temperature devices and systems used on space craft.
The Technology
These materials, which are composed of highly optically transmissive materials, are engineered to provide near-perfect reflection of the full solar spectrum in space. The materials are finely divided such that they scatter and reflect the incoming radiation from the UV down into the mid-IR and are also coated in some fashion with silver to extend the reflectance down into the far IR region of the solar spectrum. With this near-perfect reflectance of the complete solar spectrum, the scientists envision use of these materials for maintaining cryogenic temperatures for extended periods of time in space. The materials have also been developed into highly flexible, moisture resistant selective surface paint.The use and storage of cryogenics fluids is critical to many space operations, and while there are thermal control coatings in use today for spacecraft, none can provide this near-perfect reflection required for long-term maintenance of cryogenic temperatures.
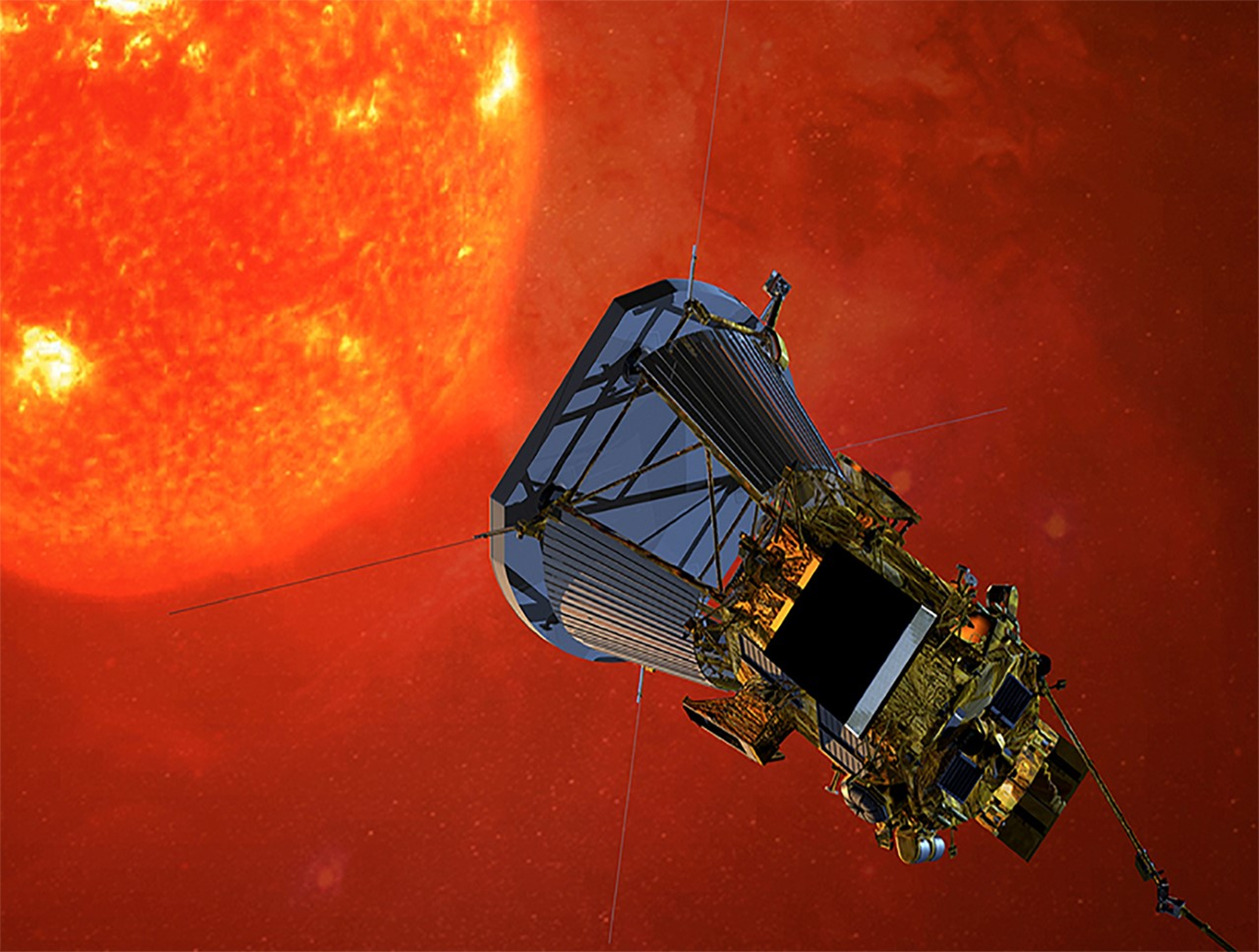
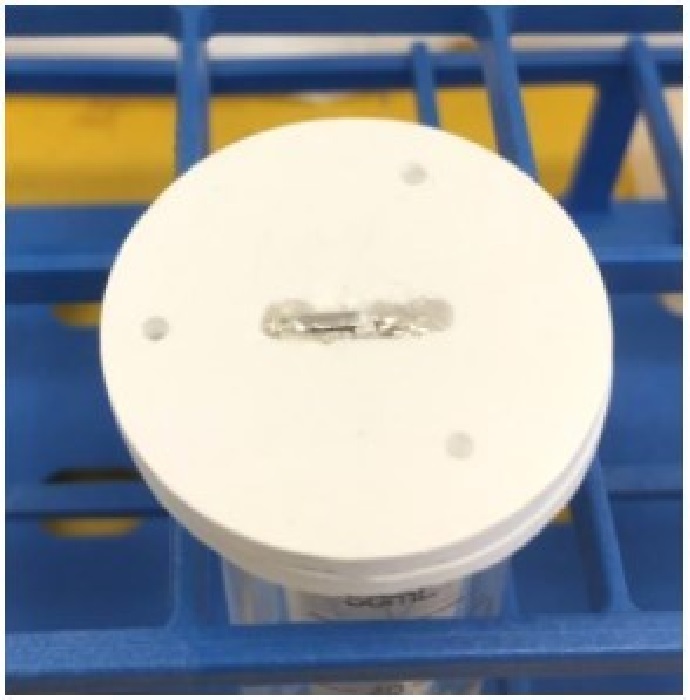
Benefits
- 0.1% absorption of the suns energy
- Surfaces coated with these new coatings can reach much lower temperatures than achievable through the use of existing materials
- This technology would allow superconductors to operate and would allow LOX storage to occur at higher density or at lower pressure.
- Reflects solar radiation, while maximizing infrared emittance
- On earth cooling ranges of -50 C below ambient
- Highly flexible and moisture resistant
Applications
- Coating on space vehicles for long duration trips
- Coating on liquid oxygen storage in a deep space depot.
- Coating on liquid oxygen storage tank on the surface of the Moon.
- Protection of temperature-sensitive devices for deep space missions
- Development of solar thermal control materials to enable long-term storage of cryogenics propellants for future space missions
- Passive Cooling of High Temperature Superconductors in Space
Technology Details
Materials and Coatings
KSC-TOPS-59
KSC-13994
KSC-14090
KSC-14106
KSC-14173
KSC-14189
KSC-14477
KSC-13972
"A Cryogenic Deep Space Thermal Control Coating", R.C. Youngquist, M. A. Nurge, W. L. Johnson, T.L. Gibson, J. M. Surma, 2017.
Similar Results

Atomic Layer Deposition-Enhanced Far-to-Mid Infrared Camera Coating
The ALD-Enhanced Far-to-Mid IR Camera Coating is fabricated by first applying a conductively loaded epoxy binder ~500 microns thick onto a conductive metal substrate (e.g., Cu, Al). This serves to provide high absorptance and low reflectance at the longest wavelength of interest, as well as to provide a mechanical buffer layer to reduce coating stress. Borosilicate glass microspheres are coated with a thin film metal via ALD, essentially turning the microspheres into resonators. That film is optically thin in the far infrared and approximates a resistive (~200 ohms per square) coating. Light trapped in the borosilicate glass microspheres is reflected back and forth within the glass–at each contact point, the light is attenuated by 50%. A monolayer of thin metal film-coated borosilicate glass microspheres is applied to the epoxy binder and cured, forming a robust mechanical structure that can be grounded to prevent deep dielectric charging by ionizing radiation in space. Once cured, the far-to-mid IR absorber structure can be coated with a traditional ~20-to-50 microns “black” absorptive paint to enhance the absorption band at short wavelengths, or a “white” diffusive paint to reject optical radiation. At this thickness and broad tolerance, the longwave response of the coating is preserved. Tailoring the electromagnetic properties of the coating layers and geometry enables realization of a broad band absorption response where the mass required per unit area has been minimized.
While NASA originally developed the ALD-Enhanced Far-to-Mid IR Camera Coating for the Stratospheric Observatory for Infrared Astronomy mission, its robustness, absorptive qualities, and optical performance make it a significant addition to IR and terahertz imaging systems. The IR camera coating is at Technology Readiness Level (TRL) 3 (experimental proof-of-concept) and is available for patent licensing.
Printable Heat Shield Formulations Advance Spacecraft Construction
One inner insulative layer, and one outer robust ablative layer comprise the AMTPS technology. When applying the heat shield to the surface of a spacecraft, the insulative layer is printed first and primarily functions to reduce the amount of heat soak into the vehicle. The formulation of the insulative layer has a slightly lower density (as compared to the robust layer) and is adjusted using a differing constituent ratio of phenolic and/or glass microballoon material. Both formulations combine a phenolic resin with various fillers to control pre- and post-cure properties that can be adjusted by varying the carbon and/or glass fiber content along with rheology modifiers to enhance the fluid flow for deposition systems.
The robust layer is applied next and functions as the ablative layer that ablates away or vaporizes when subjected to extremely high temperatures such as those achieved during atmospheric entry. The formulation of the robust layer produces a gas layer as it vaporizes in the extreme heat that acts as a boundary layer. This boundary prevents heat from further penetrating the remaining robust material by pushing away the even hotter shock layer. The shock layer is a region of super-heated compressed gas, positioned in front of the Earth-facing bottom of the spacecraft during atmospheric entry, that results from the supersonic shockwave generated.
Commercial space applications for this AMTPS technology include use on any spacecraft that transits a planetary or lunar atmosphere such as Mars or Saturn’s moon Titan. Additionally, the invention may be useful for launch system rockets to provide heat shielding from atmospheric reentry or to protect ground equipment on the launch pad from rocket exhaust plumes. As the number of government and commercial space missions to primary Earth orbits, the Moon, and the Solar System increase, there will be a growing need for cost-effective, on-demand, and timely fabrication of heat shields for space-related activities.
AMTPS Formulations – Insulative and Robust Variation is at a technology readiness level (TRL) 5 (component and/or breadboard validation in laboratory environment) and is now available for patent licensing. Please note that NASA does not manufacture products itself for commercial sale.

Thin Film Sensor for Ultra High-Temp Measurement
The thin film sensor’s principal advantage lies in its potential to take high frequency temperature measurements from the surface of a reentering spacecraft while simultaneously withstanding the high temperature and oxidizing environment encountered. This data provides engineers with operational phase measurements used to refine the spacecraft’s operational envelope and track flight hardware behavior in addition to providing high frequency temperature measurements that can inform the physics of a boundary layer.
Mismatches in coefficients of thermal expansion (CTE) are expected in TPS-based sensor applications because the metallic materials used for temperature sensing have thermal expansion rates that differ from the rates of the substrate and coating materials in the TPS. At high temperatures during reentry, this mismatch in CTE can create a significant strain differential between the metallic sensor, sensor leads, and the materials to which the sensor and leads are bonded.
High frequency response temperature measurements on the surface of entry spacecraft are not currently possible above ~700 F with existing measurement capabilities. This shortcoming is primarily due to the need for robust sensor behavior at temperatures of several thousand degrees F. The sensor design of this technology preserves the integrity of sensor components while enhancing its high temperature functionality.
The thin film temperature sensor has a technology readiness level (TRL) 5 (Component and/or breadboard validation in relevant environment) and is now available for patent licensing. Please note that NASA does not manufacture products itself for commercial sale.

High Atomic Number Coatings for Fabrics
High atomic number materials, such as tantalum, do not bond well to oxygen- and hydroxyl-rich surfaces, such as glass fibers. These metals often form surface oxides when layered on glass fabric, resulting in flaking of the high atomic number material off the fabric during cutting, folding, and/or handling.
To improve coating durability, this invention applies a lower atomic number metal as a tie down layer first before applying the high atomic number metal layer. The tie down layer reduces oxide formation between the substrate and the high atomic number material, promoting adhesion. Titanium has shown strong adhesion with different metals and is effective at reducing oxide formation when diffusion bonded to itself or other materials. It has been shown to be effective at improving durability when thermally sprayed onto a glass fiber fabric as a tie down layer for a subsequent tantalum layer (also applied via RF plasma spray). The titanium layer is only approximately 1 mil thick but results in strong adhesion of the tantalum layer by inter-metallic or diffusion bonding. A thermal spray process may be used, as well.
This innovation enables the delivery of high atomic metal coating on glass fiber fabrics and other polymeric substrates that are lower cost, lighter weight, and durable to form a flexible cloth material with Z-graded radiation shielding. Coated samples have been produced and the technology is currently at a technology readiness level (TRL) of 4 (prototype).

Oil-Free Lubricants
In applying PS400 using the plasma spray-coating process, a 0.010 inch layer is deposited onto a metal surface. This composite coating often includes a metallic-based binder, a metal-bonded hardener, a high-temperature lubricant, and/or a low- temperature lubricant. PS400's improved metallic-based binder alloy greatly increases the structural strength and durability of the composite with respect to the operating temperature and the bearing load, and provides superior dimensional stability. PS400's metal-bonded oxide hardening agent provides additional hardness, wear resistance, and thermal stability, while also exhibiting a low coefficient of friction when used in sliding contacts. It is also significantly less expensive in terms of both acquisition and grinding processes.
Depending on the desired environment, high- and low-temperature lubricants may be added to the composite coating. The preferred high-temperature lubricant is a metal fluoride and the optional optional low-temperature lubricant is composed of metals, such as silver or copper, that are soft enough to provide lubrication at low temperature while maintaining oxidation resistance with a sufficiently high melting point. These qualities permit the materials to be used over a broad temperature range. Once the spray coating has been applied, the metal surface is ground and polished to produce a smooth, self-lubricating surface before use. Unlike some coatings that must be diamond-ground, PS400 is readily ground with a substantially less expensive abrasive, such as silicon carbide. This grinding process generally yields a coating thickness of 200 to 400 micrometers.
In instances when a coating is not convenient or possible, powder metallurgy techniques using PM400 can be used to make freestanding self-lubricating components such as bushings and wear plates.