Self-Cleaning Coatings for Space or Earth
Materials and Coatings
Self-Cleaning Coatings for Space or Earth (KSC-TOPS-99)
Transparent Electrodynamic Dust Shields Usable for Solar Cells
Overview
Reducing dust accumulation on any surface is key for lunar missions as dust can damage or impair the performance of everything from deployable systems to solar cells on the Moon’s surface. Electrodynamic dust shields (EDSs) are a key method to actively clean surfaces by running high voltages (but low currents) through electrodes on the surface. The forces generated by the voltage efficiently remove built up, electrically charged dust particles.
Innovators at the NASA Kennedy Space Center have developed a new transparent EDS for removing dust from space and lunar solar cells among other transparent surfaces. The new coatings operate at half the voltage of existing EDSs while being 90% thinner. These capabilities are enabled by an innovative combination of electrode patterning and a thin silica protective layer. The reduced thickness and lower voltage operation expands possibilities for integrating EDSs onto transparent surfaces across industries.
The Technology
The new transparent EDS technology is lighter, easier to manufacture, and operates at a lower voltage than current transparent EDS technologies. The coating combines an optimized electrode pattern with a vapor deposited protective coating of SiO2 on top of the electrodes, which replaces either polymer layers or manually adhered cover glass (see figure on the right). The new technology has been shown to achieve similar performances (i.e., over 90% dust clearing efficiency) to previous technologies while being operated at half the voltage.
The key improvement of the new EDS coating comes from an innovative method to successfully deposit a protective layer of SiO2 that is much thinner than typical cover glass. Using vapor deposition enables the new EDS to scale more successfully than other technologies that may require more manual manufacturing methods. The EDS here has been proven to reduce dust buildup well under vacuum and may be adapted for terrestrial uses where cleaning is done manually. The coatings could provide a significant improvement for dust removal of solar cells in regions (e.g., deserts) where dust buildup is inevitable, but water access is limited. The EDS may also be applicable for any transparent surface that must remain transparent in a harsh or dirty environment.
The related patent is now available to license. Please note that NASA does not manufacturer products itself for commercial sale.

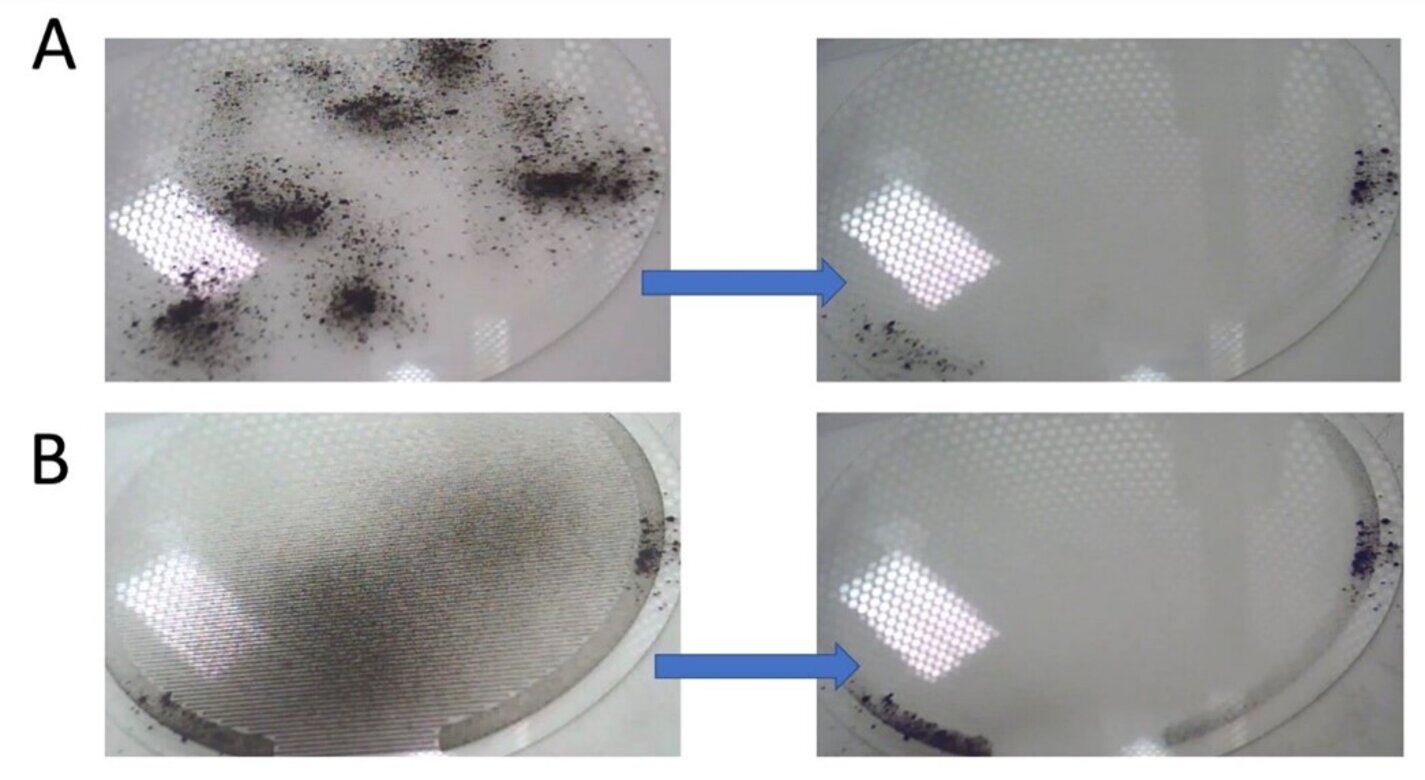
Benefits
- Energy savings and enhanced safety: Operates at half the voltage of current EDS technologies.
- High performance: Demonstrated over 90% dust removal efficiency.
- Manufacturing scalability: Vapor deposition process enables large scale manufacturing.
- Versatility: Applicable to a wide range of transparent surfaces including solar cells, glass, and other materials.
Applications
- Aerospace: solar cells, windows for spacecraft and stations, or spacesuit visors
- Terrestrial power: solar farms and rooftop solar panels
- Architecture: building windows
- Agriculture: windshields on farming equipment and windows or roofs of greenhouses
- Automotive: headlights, windshields, mirrors, and sensors on vehicles
Technology Details
Materials and Coatings
KSC-TOPS-99
KSC-14465
Tags:
|
Similar Results

Particle Contamination Mitigation Methods
The following methods can be used individually or in combination to generate superhydrophobic surfaces:
Synthesis of novel copolyimide oxetanes with unique surface properties
The technology is the synthesis of a polyimide coating or film with a modified surface chemistry shown in Figure 1. A minor amount of an oxetane reactant containing fluorine is added to the polyimide, and the oxetane preferentially migrates to the surface, enabling relatively high concentrations of fluorine at the surface, without compromising the functional performance of the bulk of the polymide coating/film.
The copolymers exhibit mitigation of particle adhesion and fouling from exposure to various particulate and biological contaminants and exhibit reduced surface energy and increased surface fluorine content at extremely low oxetane loadings relative to the imide matrix (see Figure 2). Additionally, the short fluorinated carbon chains do not bioaccumulate, reducing the environmental impact of these materials.
Modifying surface energy via laser ablative surface patterning
This method uses a laser to create nanoscale patterns in the surface of a material to increase the hydrophobicity of the surface (see Figure 2). The benefits of hydrophobic surfaces include decreases in friction and increases in self-cleaning properties. This is an advantageous method of surface modification because it is fast and single-step, promises to be scalable, requires no chemicals, could be applied to a variety of materials, and does not require a planar surface for patterning.

Alternative Transparent Coating Lotus Suitable for Optics with Vacuum Deposition Layer
In addition to previous LOTUS coating formulations, an additional optical formulation may be applied via vacuum deposition. This coating forms a top layer and may be applied in different thicknesses that serve to enhance its hydrophobic properties. The vacuum deposited material may comprise fluorinated ethylene propylene or a similar material. This coating is transparent and can be used on optical components or any other applications requiring a clear coating.

Self-Cleaning Seals
This NASA innovation applies the concepts of electrodynamic dust shielding (EDS) to develop seals (e.g., O-rings) with active self-cleaning capabilities. NASA’s self-cleaning seals are manufactured in the following manner: A seal with a conductive surface (or otherwise fabricated to be conductive) is generated and an electrical connection, lead or electrode is attached. Next, a dielectric material is coated or placed over the conductive surface of the seal. (NOTE: Using conductive elastomer materials eliminates the need for a conductive cover layer) A high voltage (nominally >1kV) power supply is connected to the conductive layer on the seal and grounded to the metallic groove or gland that houses the seal.
Given the design, dust accumulates on the outer dielectric layer (a high-voltage insulator) of the seal. To clean the seal, a time varying alternating voltage is applied from the power supply, through the high voltage lead and onto the conductive layer of the seal. When this voltage is applied, the resulting electric field produces Coulomb and dielectrophoretic forces that cause the dust to be repelled from the sealing surface. In practice, NASA’s self-cleaning seals could be operated in continuous cleaning mode (actively repelling dust at all times, preventing it from ever contacting the seal surface) or in a periodic cleaning cycle mode (removing dust from the seal surface at regular intervals).
NASA’s self-cleaning seals have been prototyped and demonstrated to be highly effective at dust removal. The invention could serve as the basis of an active, self-cleaning seal product line marketed for in-space and/or terrestrial applications. Additionally, companies developing space assets destined for operation on dusty planetary surfaces (e.g., the Moon) may be interested in leveraging the technology to protect seals from dust/regolith accumulation, ensuring continuous low leakage operations.

Lunar Experiment Support System and Handling (LESSH) Battery Charger Module (BCM)
NASA’s LESSH BCM is a compact, high-performance, ruggedized system designed to support extended science operations in harsh lunar environments. With a mass of 9.4 kg and dimensions of 50 x 25 x 10 cm, the BCM is engineered for seamless integration with the interface bank on the HLS. A 1.5-meter flexible harness with an EVA-compatible connector and removable dust cover enables reliable operation in austere environments. Astronaut-operated controls, such as a guarded power switch and LED indicators, simplify usability and reduce the potential for errors during high-stakes lunar operations.
The BCM is optimized for safety and efficiency, incorporating state-of-the-art power and charging capabilities. It supports charging of 28V astronaut-rated batteries with a power output rated at 215W and integrates a battery pre-heater to maintain optimal performance in extreme temperatures. The BCM features a 4-hour charge time with software adjustability for charging parameters such as current, voltage, overvoltage, and undervoltage setpoints. Battery longevity is ensured through passive rebalancing of cell voltages and advanced safety features. Its 2-fault tolerant hardware and adjustable safety setpoints safeguard against potential hazards. Additionally, the BCM supports 1000BASE-T Ethernet pass-through for high-speed data transfer.
Originally designed to extend the length of lunar surface science experiments by enabling astronauts to recharge instrumentation, NASA’s LESSH BCM may be desired by companies seeking to operate sensors on the lunar or Martian lunar surface. The design may also be suitable for terrestrial applications involving harsh environments where interchangeable sealed sensors must operate on their own or with rovers, robotics, and drones. The BCM is at technology readiness level (TRL) 4 (component and/or breadboard validation in lab) and is available for patent licensing.

Multi-Stage Filtration System
While HEPA filter elements can last for years without intervention, pre-filtering systems that remove larger particles before they reach the HEPA filter need to be treated (most often by cleaning or replacement) as often as once a week. These treatments can be resource-intensive and expensive, especially in extreme environments. Glenn's innovative system combines a pre-filtration impactor and a scroll filter that reduces the need to replace the more sensitive or expensive filters, extending the system's working life. The system uses an endless belt system to provide the impaction surface. A thin layer of low-toxicity grease is applied to the impaction surface to increase particle adhesion. A high flow turning angle near the impaction surface causes relatively large particles to impact and stick to the surface while smaller particles stay within the air flow. When the surface is covered with particles - or if a layer of particles has grown to a thickness that impairs adhesion - the surface is regenerated. The band is rotated so that the loaded surface passes by a scrapper, removing the layer of particles and a clean segment of the band revolves to become the new impaction surface.
A further innovation is the scroll filter which allows the filtration media to be rotated out of the airflow when fully loaded, providing multiple changes of the filter through a motorized scrolling or indexing mechanism. When nearly fully loaded with dust particles, the exposed media is mechanically rolled up on one side of the filter to both contain and compactly store the dust. The spools that hold the clean and spent filter media are mounted on roller bearings to facilitate the scrolling operation and reduce motor power requirements. Nearly any grade of filter media can be used to meet the desired filtration specification. Additional media rolls can be added after the original roll is spent to further increase filter life.