Electron Beam Free Form Fabrication (EBF3)
Manufacturing
Electron Beam Free Form Fabrication (EBF3) (LAR-TOPS-164)
Metal deposition apparatus to build metallic components directly from CAD
Overview
Electron Beam Freeform Fabrication, or EBF3, is a process that uses an electron beam gun, a dual wire feed and computer controls to manufacture metallic structures for building parts or tools in hours, rather than days or weeks. EBF3 can manufacture complex geometries in a single operation and provides efficient use of power and feedstock. The technology has a wide range of applications, including automotive, aerospace, and rapid prototyping. It can build large metallic parts measuring feet in length, and has been reduced in size and power to enable 0-gravity experiments conducted on NASA's Reduced Gravity aircraft.
The Technology
EBF3 works in a vacuum chamber, where an electron beam is focused on a constantly feeding source of metal wire, which is melted and applied by drawing one layer at a time on a computer-controlled positioning table until the part is complete. By controlling the raster pattern, the e-beam selectively heats the outer edges of the wire if it strays from the melt zone. With such selective heating, the wire automatically curls away from the high heat outer edge and back into the region of the molten pool. Thus, with a fixed raster pattern, the process becomes self-correcting without any sensing or external control of process parameters. EBF3 can handle two different sources of metal feedstock at the same time, which can be controlled independently to allow precise control of mixing of materials during deposition.
EBF3 incorporates the following technologies, which can also be licensed individually: (1) a vapor-barrier vacuum isolation system that maintains a vacuum in the electron beam column adjoined to another chamber at higher pressure without loss of vacuum; (2) a system that controls and measures the height of an additive layer of metal using an electron beam in combination with a sensor and image processor; (3) a gas phase alloying system for wire fed joining & deposition, which is being developed for the controlled introduction of gases into molten metals in order to selectively impart beneficial properties to the final product (e.g. strength, corrosion resistance, etc.); and (4) a closed-loop system that is being developed to detect various fabrication anomalies and automatically send feedback to the fabrication system to modify the input parameters to maintain process consistency.
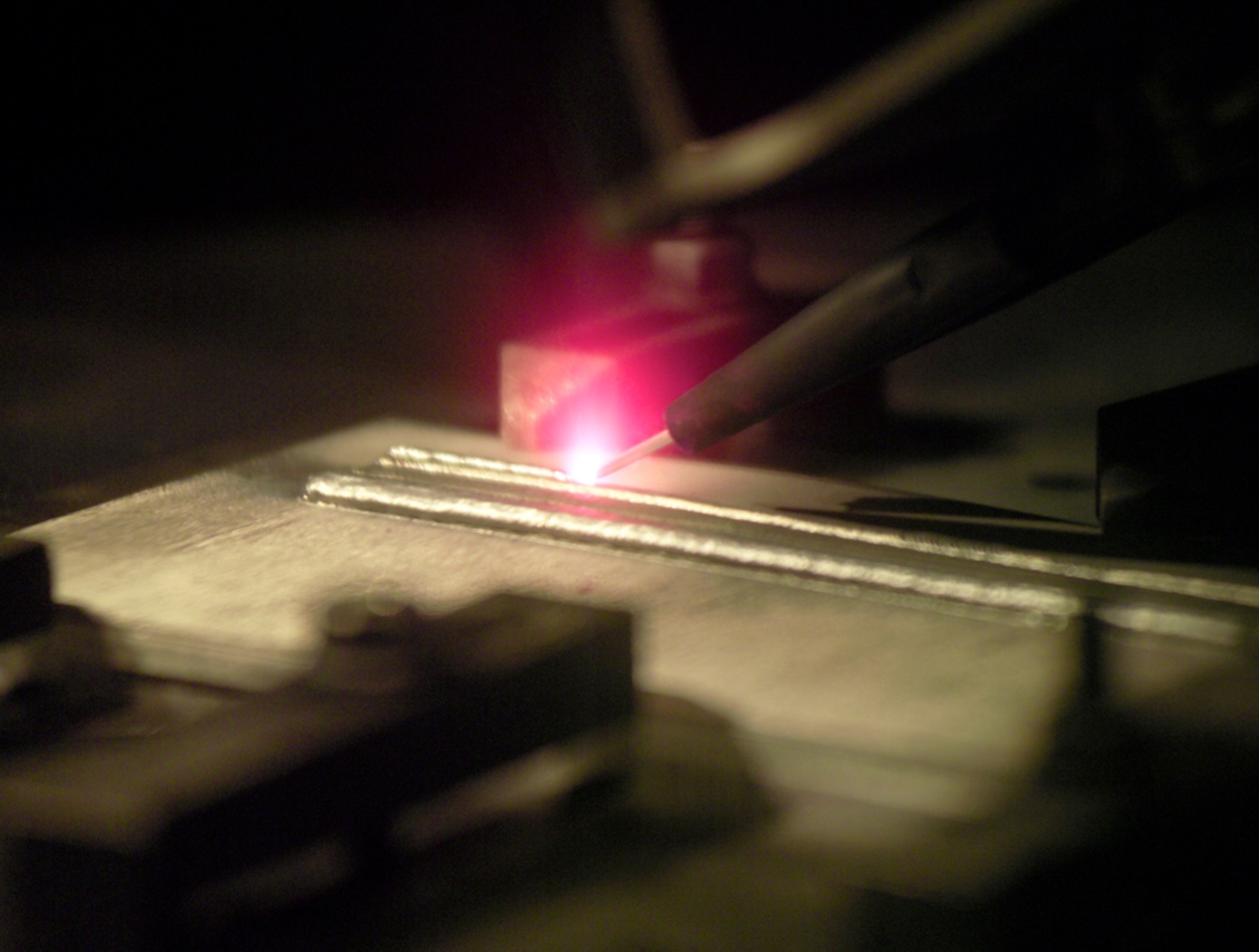
Benefits
- Self-correcting stabilization and optimization of e-beam during the deposition process
- Provides continuous and predictable deposition pattern
- Simplifies deposition of complex geometries
- Optimizes microstructural control of the solidified molten metal
- Provides efficient use of power and feedstock
- Improves automated operation
Applications
- Welding of metal structures for automotive, aerospace, and other industrial and commercial manufacturing
- Free-form fabrication of complex metal components in remote locations
- Near-net shape manufacturing and rapid prototyping
- Applicable to variety of metal fabrication markets, from automotive and aerospace to sporting goods and medical devices
Technology Details
Manufacturing
LAR-TOPS-164
LAR-18871-1
LAR-18871-1
Similar Results

Solid State Sensor for Detection and Characterization of Electric Fields
This equilibrium-reversing-gate field effect transistor (ergFET) deploys an electrode near the gate of the transistor to control and reverse leakage currents which are typical in transistors and can lead to measurement errors. It can be built into an array to enable higher resolution imaging and is a solid state device free of moving parts. This enables portable and hand held sensor designs.

Novel Overhang Support Designs for Powder-Based Electron Beam Additive Manufacturing (EBAM)
EBAM technology is capable of making full-density, functional metallic components for numerous engineering applications; the technology is particularly advantageous in the aerospace, automotive, and biomedical industries where high-value, low-volume, custom-design productions are required. A key challenge in EBAM is overcoming deformation of overhangs that are the result of severe thermal gradients generated by the poor thermal conductivity of metallic powders used in the fabrication process. Conventional support structures (Figure 1a) address the deformation challenge; however, they are bonded to the component and need to be removed in post- processing using a mechanical tool. This process is laborious, time consuming, and degrades the surface quality of the product.
The invented support design (Figure 1b) fabricates a support underneath an overhang by building the support up from the build plate and placing a support surface underneath an overhang with a certain gap (no contact with overhang). The technology deposits one or more layers of un-melted metallic powder in an elongate gap between an upper horizontal surface of the support structure and a lower surface of the overhang geometry. The support structure acts as a heat sink to enhance heat transfer and reduce the temperature and thermal gradients. Because the support structure is not connected to the part, the support structure can be removed freely without any post-processing step.
Future work will compare experimental data with simulation results in order to validate process models as well as to study process parameter effects on the thermal characteristics of the EBAM process.

Electroactive Scaffold
Current scaffold designs and materials do not provide all of the appropriate cues necessary to mimic in-vivo conditions for tissue engineering and stem cell engineering applications. It has been hypothesized that many biomaterials, such as bone, muscle, brain and heart tissue exhibit piezoelectric and ferroelectric properties. Typical cell seeding environments incorporate biochemical cues and more recently mechanical stimuli, however, electrical cues have just recently been incorporated in standard in-vitro examinations. In order to develop their potential further, novel scaffolds are required to provide adequate cues in the in-vitro environment to direct stem cells to differentiate down controlled pathways or develop novel tissue constructs. This invention is for a scaffold that provides for such cues by mimicking the native biological environment, including biochemical, topographical, mechanical and electrical cues.

Optimization of X-Ray CT Measurement Accuracy for Metal AM Components
This NASA innovation is a method for quantifying and improving accuracy of X-Ray CT-based metal AM part inspection by comparing X-Ray CT data with a high-fidelity 2D surface imaging technique such as surface profilometry. Using surface profilometry that has a NIST-traceable calibration, the technique guarantees a specific level of high fidelity, allowing surface profilometry data to serve as a ground truth reference with which to judge X-Ray CT accuracy and detectability.
To deploy the method, both 3D X-Ray CT data and 2D high-fidelity surface images are acquired on the same metal AM part. 3D X-Ray CT data is then segmented and reoriented to extract a 2D X-Ray CT surface image. Measurements of features (e.g., surface-breaking porosity) are then made in both datasets, followed by a comparison of various metrics. This comparison serves two purposes: (a) quantifying the accuracy of the X-Ray CT inspection performed, and (b) providing an objective function which can be minimized to optimize X-Ray CT inspection. The objective function allows engineers to tune X-Ray CT parameters to minimize the function. These optimized parameters can then be implemented to achieve higher accuracy and defect detection reliability in X-Ray CT imaging. Once an X-Ray CT process is optimized for a specific metal AM component, analysis and certification can be accelerated.
This technology helps develop X-Ray CT-based metal AM part inspection processes with high accuracy and reliable detectability. Industries for which metal AM parts are desirable and safety, reliability, and fatigue life is of concern (e.g., aerospace, commercial space, automotive, medical) could benefit from the invention. Companies including X-Ray CT inspection system manufacturers using optical sensors and software, NDE data analysis software providers, and end-users in the industries may be interested in licensing this NASA invention.

Electric Field Imaging System
The EFI imaging platform consists of a sensor array, processing equipment, and an output device. By registering voltage differences at multiple points within the sensor array, the EFI system can calculate the electrical potential at points removed from the sensor. Using techniques similar to computed tomography, the electrical potential data can be assembled into a three-dimension map of the magnitude and direction of electric fields. Since objects interact with electric fields differently based on their shape and dielectric properties, this electric field data can then be used to understand shape,
internal structure, and dielectric properties (e.g., impedance, resistance) of objects in three dimensions.
The EFI sensor can be used on its own to see electric fields or image electric fieldemitting objects near the sensor (e.g., to evaluate leakage from poorly shielded wires or casings). For evaluation of objects that do not produce an electric field, NASA has developed generator that emits a low-current, human-safe electrostatic field for snapshot evaluation of objects. Additionally, an alternative EFI system optimized to evaluate electric fields at significant distances (greater than 1 mile) is being developed for weather-related applications.