New Methods in Preparing and Purifying Nanomaterials
Materials and Coatings
New Methods in Preparing and Purifying Nanomaterials (LEW-TOPS-107)
New processes greatly improve the properties of boron nitride nanomaterials
Overview
Innovators at NASA's Glenn Research Center have made several breakthroughs in treating hexagonal boron nitride (hBN) nanomaterials, improving their properties to supplant carbon nanotubes in many applications. These inventors have greatly enhanced the processes of intercalation and exfoliation. Both processes are crucial in creating usable nanomaterials and tailoring them for specific engineered applications. In addition, Glenn's researchers have devised a means of fabricating exfoliated hBN-alumina ceramic composites, which have great potential as high-thermal-conductivity electrical insulators, as well as a new method to remove impurities from nanomaterials without causing damage to their structures. All of these advances have hBN nanomaterials set to transform applications such as heat sinks, electrical insulators, lightweight piezoelectric polymers for satellites and unmanned aerial vehicles, ceramic composites for jet engines, biomedical components, and radiation shielding technology.
The Technology
Sometimes called white graphite, affordable and plentiful hBN possesses the same kind of layered molecular structure as graphite. In graphite, this structure has allowed next-generation nanomaterials like carbon nanotubes and graphene to be produced. With hBN, however, the process of converting the substance into boron nitride nanotubes (BNNT) has been too difficult to yield commercial quantities. Glenn innovators have created several new methods that could enable greater adoption of this unique nanomaterial. In the initial stage, the starter reactant is mixed with a selected set of chemicals (a metal chloride, for example) and an activation agent (such as sodium fluoride). This mixture causes hBN to become less resistant to intercalation. The intercalated product can then be exfoliated by heating the material in air, and giving the material a final rinse with a liquid-phase ferric chloride salt to dissolve any embedded impurities without damaging its internal structure. These efficiently exfoliated nanomaterials can be used to form advanced composite materials (e.g., layered with aluminum oxide to form hBN/alumina ceramic composites). Nanomaterials fabricated from hBN can also take advantage of the material's unique combination of being an electrical insulator with high thermal conductivity for applications ranging from microelectronics to energy harvesting. Glenn's innovations have enabled a significantly improved matrix composite material with the potential to make a significant impact on the commercial materials market.
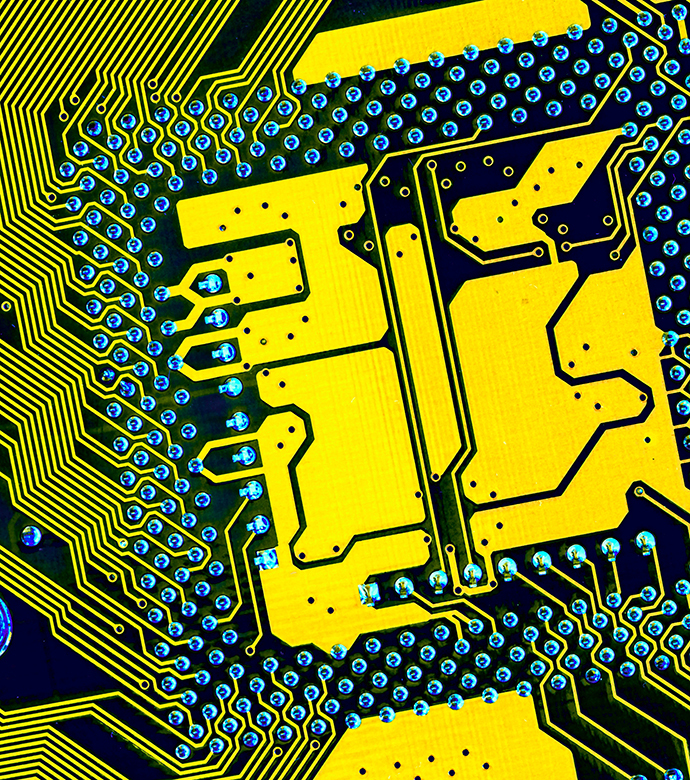
Benefits
- Durability: allows hBN nanomaterials to retain their strength even in much higher temperatures and higher stress conditions
- Unique properties: produces high thermal conductivity nanomaterials that are simultaneously effective electrical insulators, unlike similar state-of-the-art nanomaterials
- Versatility: permits materials to be tailored more closely to the needs of specific applications
- Outstanding piezoelectric properties: matrix composites made using hBN have improved performance generating energy from vibration and heat
- Simple manufacturing: simplifies process steps of intercalation and exfoliation, making it easier to produce larger volumes of ultra-pure nanomaterial
Applications
- Advanced composite materials for use in aircraft engines, coatings, and armor
- Microelectronics
- Piezoelectric devices, including sensors and robotics
- Thermal management
- Electrical insulators
- High temperature seals and gaskets
- Biomedical treatments and therapies
- Radiation and UV shielding devices
- Energy harvesting
Technology Details
Materials and Coatings
LEW-TOPS-107
LEW-18970-1
LEW-18970-2
LEW-18970-3
LEW-18970-4
Tags:
|
Similar Results

Rapid Fabrication of Boron Nitride Fine Fibers
Polymer derived ceramics (PDCs) refers to ceramic materials formed through the pyrolysis of a pre-ceramic polymer. The use of the PDC process enables the fabrication of complex, lightweight, mechanically robust shapes that are too difficult to machine otherwise. The PDC process also allows for granular control over the chemistry, resulting in better fiber homogeneity and allowing for application-specific tailoring.
NASA’s PDC process to rapidly fabricate multifunctional h-BN nanofibers entails the following steps. First a liquid-based polymer precursor solution containing boron and nitrogen is made. Next, the precursor undergoes a forcespinning process, which causes the solvent to evaporate, leaving behind only polymeric nanofiber preforms. These preforms are then cured via UV exposure or other means to link the polymer chains to one another. Finally, the crosslinked polymers are heat treated under specific conditions to convert the polymer fibers into ceramics.
This NASA innovation offers the ability to make low-cost, layered h-BN fiber mats or weaved fabrics of flexible h-BN from spun yarns at scale. The size of the fibers (> 200 nm) makes them easier to handle and disperse relative to nanotubes or nanosheets and mitigates respiratory hazards. The process offers high yields relative to alternative fabrication processes such as electrospinning. The resulting h-BN nanofibers have a broad range of potential applications and are poised to enable the development of new, multifunctional materials.

Conductive Polymer/Carbon Nanotube Structural Materials and Methods for Making Same
Carbon nanotubes (CNTs) show promise for multifunctional materials for a range of applications due to their outstanding combination of mechanical, electrical and thermal properties. However, these promising mechanical properties have not translated well to CNT nanocomposites fabricated by conventional methods due to the weak load transfer between tubes or tube bundles.
In this invention, the carbon nanotube forms such as sheets and yarns were modified by in-situ polymerization with polyaniline, a -conjugated conductive polymer. The resulting CNT nanocomposites were subsequently post-processed to improve mechanical properties by hot pressing and carbonization. A significant improvement of mechanical properties of the polyaniline/carbon nanotube nanocomposites was achieved through a combination of stretching, polymerization, hot pressing, and carbonization.

Silicon Carbide (SiC) Fiber-Reinforced SiC Matrix Composites
Aimed at structural applications up to 2700°F, NASA's patented technologies start with two types of high-strength SiC fibers that significantly enhance the thermo-structural performance of the commercially available boron-doped and sintered small-diameter “Sylramic” SiC fiber. These enhancement processes can be done on single fibers, multi-fiber tows, or component-shaped architectural preforms without any loss in fiber strength. The processes not only enhance every fiber in the preforms and relieve their weaving stresses, but also allow the preforms to be made into more shapes. Environmental resistance is also enhanced during processing by the production of a protective in-situ grown boron-nitride (iBN) coating on the fibers. Thus the two types of converted fibers are called “Sylramic-iBN” and “Super Sylramic-iBN”.
For high CMC toughness, two separate chemical vapor infiltration (CVI) steps are used, one to apply a boron nitride coating on the fibers of the preform and the other to form the SiC-based matrix. The preforms are then heat treated not only to densify and shrink the CVI BN coating away from the SiC matrix (outside debonding), but also to increase its creep resistance, temperature capability, and thermal conductivity.
One crucial advantage in this suite of technologies lies in its unprecedented customizability. The SiC/SiC CMC can be tailored to specific conditions by down-selecting the optimum fiber, fiber coating, fiber architecture, and matrix materials and processes. In any formulation, though, the NASA-processed SiC fibers display high tensile strength and the best creep-rupture resistance of any commercial SiC fiber, with strength retention to over 2700°F.

Ruthenium-Doped Thermoelectric Materials
Solid state power conversion devices, such as thermoelectrics, depend upon temperature gradients for their operation. For example, aeronautic gas turbine engines maintain the necessary temperature gradients throughout their systems due to the enthalpic processes of combustion, which offers the possibility of generating electrical power for use in primary and secondary electrical systems in the aircraft. However, until now thermoelectric materials have not been able to withstand the combination of high temperatures and oxidative environments present in gas turbine engines. Glenn's innovation overcomes these limitations by using a doped oxide pyrochlore (crystal compound) semiconductor as the thermoelectric material. The material has a low thermal conductivity, which allows it to maintain a thermal gradient and sufficient electrical conductivity to produce an electromotive force. The pyrochlore allows the thermoelectric material to be present within a gas turbine engine, converting heat directly into electricity and functioning at high temperatures without oxidizing in air. Glenn's innovative thermoelectric material permits the benefits of solid-state power conversion devices to improve fuel efficiencies for a broader range of applications than has ever been possible. This innovation is in the early stages of development, and Glenn welcomes opportunities for co-development.

Conductive Carbon Fiber Polymer Composite
The new composite developed by NASA incorporates PGS and CNTs to enhance its thermal conductivity while preserving the mechanical properties of the underlying carbon fiber polymer composite. NASA has also improved the composite manufacturing process to ensure better thermal conductivity not only on the surface, but also through the thickness of the material. This was achieved by adding perforations that enable the additives to spread through the composite.
The process for developing this innovative, highly thermally conductive hybrid carbon fiber polymer composite involves several steps. Firstly, a CNT-doped polymer resin is prepared to improve the matrix's thermal conductivity, which is then infused into a carbon fiber fabric. Secondly, PGS is treated to enhance its mechanical interface with the composite. Thirdly, perforation is done on the pyrolytic graphite sheet to improve the thermal conductivity through the thickness of the material by allowing CNT-doped resin to flow and better interlaminar mechanical strength. Finally, the layup of PGS and CNT-CF polymer is optimized.
Initial testing of the composite has shown significant increases in thermal conductivity compared to typical carbon fiber composites, with a more than tenfold increase. The composite also has higher thermal conductivity than aluminum alloys, with more than twice the thermal conductivity of the Aluminum 6061 typically used in the aerospace industry. For this new material, NASA has completed a proof-of-concept demonstration and work continues to use the material in a heat exchanger system and further characterize the properties including longevity and radiation impact analysis.