3D Printed Polymer Aerogels
Manufacturing
3D Printed Polymer Aerogels (LEW-TOPS-171)
Additive manufacturing-enabled rapid fabrication of polymer aerogels with complex, tailored geometries
Overview
Aerogels are low density, highly porous, ultra-lightweight materials first invented in the 1930s. More recently, inventors at NASA’s Glenn Research Center (GRC) have created a variety of polymer aerogel formulations with broad applications including thermal insulation, acoustic barriers, vibration mitigation, and much more. Conventionally, aerogels are fabricated using a molding process, which requires separate, often costly, manufacturing of the mold itself. The geometry of aerogels that can be fabricated using molding processes are limited in complexity by difficulty removing the gel from mold. This inhibits the ability to rapidly prototype complex, application-specific aerogel structures with tailored geometries (e.g., conformal geometries around existing components), limiting the rate of iterative design and innovation.
To address these challenges, researchers at NASA GRC developed methods to rapidly prototype and fabricate polymer aerogel structures using 3D printing techniques (e.g., direct ink writing) that retain the microstructural, mechanical, and thermal properties of polymer aerogels fabricated via conventional molding processes. 3D printing provides a host of advantages including the ability to produce intricate polymer aerogel architectures with complex geometries in a rapid manner and without the need for a mold.
The Technology
NASA GRC has developed several different 3D printing techniques to fabricate polymer aerogel structures; different techniques are suitable for different polymer aerogel formulations. In general, the methods entail forming a first liquid comprising a polymer precursor and cross-linker, forming a second liquid comprising a catalyst for reacting a polymer precursor to form a polymer, then 3D printing the aerogel structure with a mixture of the two liquids onto or into a medium.
Specifically, NASA's polymer aerogel 3D printing techniques include: direct syringe printing, dual-syringe printing with static mixing head, direct syringe printing of photocurable formulations, and a unique rapid prototyping method involving a sacrificial bath. The direct syringe process relies upon gelation to occur once the gel is extruded from the print head to the substrate. In the dual-syringe printing process, one syringe contains polyamic acid and the other contains a catalyst. These are mixed in a static mixing head to allow for curing/gelation upon extrusion. For direct syringe printing of photocurable polymer aerogel formulations, a UV pen and array follow the printed gel during extrusion to induce gelation. Finally, the rapid prototyping method uses a bath of highly viscosity, low shear gel that provides a low drag, flexible yet supportive medium in which to print the polymer aerogel. In other embodiments, a bath of polyamic acid is used while cross-linkers and catalysts are introduced via printing, or vice versa (polyamic acid is introduced via printing into a bath of cross-linkers and catalysts).
In addition to complex geometries, these layered 3D printing processes allow for the fabrication of chemically-bonded (cross-linked) structures composed of layers of different polymer aerogel formulations (i.e., fabrication of structures with tailored chemistries / properties). Previously, joining different polymer aerogel formulations into a single structure required the fabrication of different formulations using individual molds and joining them using an adhesive, potentially introducing weak fracture points.
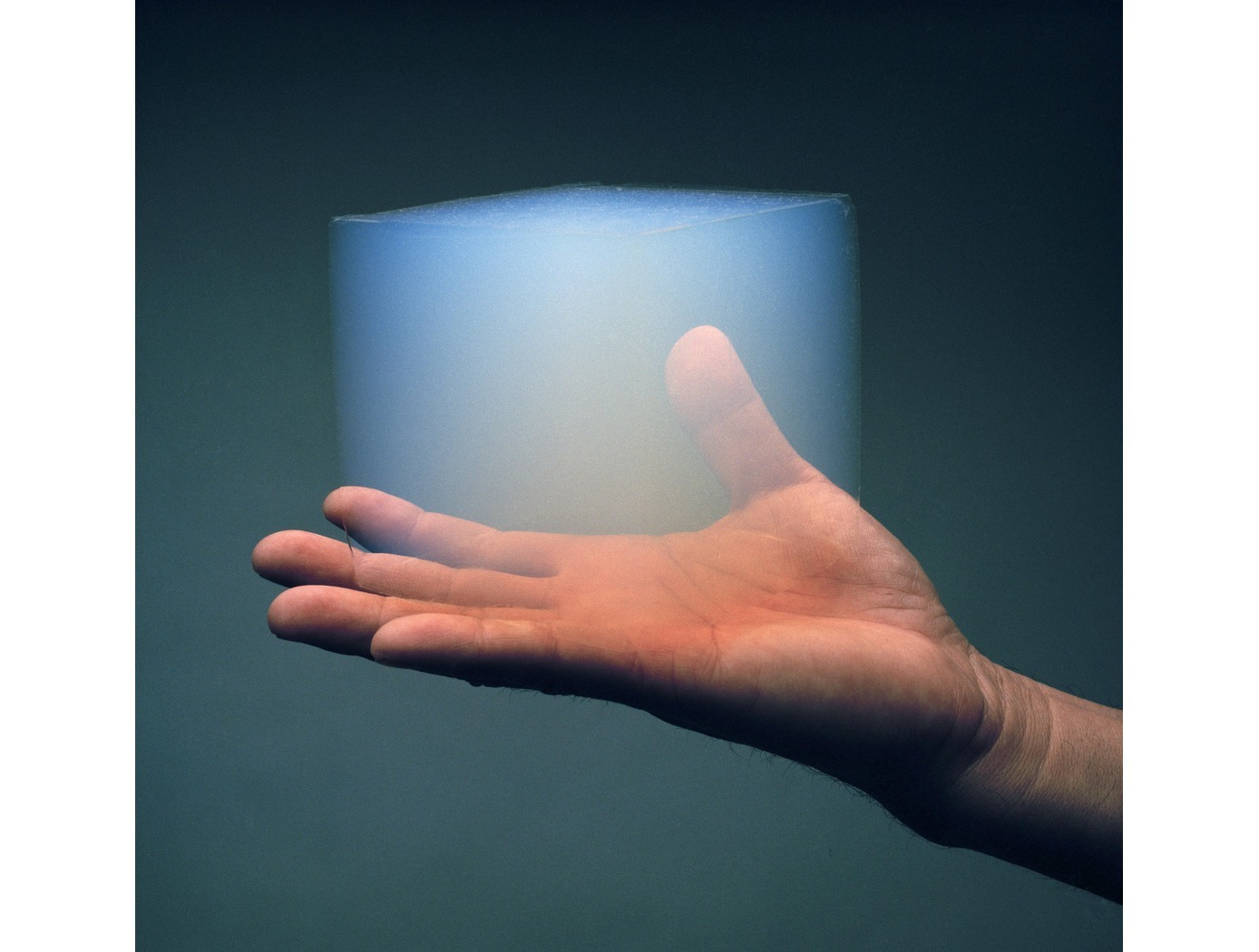

Benefits
- Enables fabrication of complex polymer aerogel geometries: NASA's 3D printing techniques enable fabrication of polymer aerogel structures with complex, tailored geometries that would be infeasible using molding processes.
- Enables fabrication of complex multi-chemistry polymer aerogels: Using NASA's processes, different polymer aerogel formulations can be layered while in a gel state, chemically bonding (cross-linking) them immediately, eliminating the need for adhesives.
- Allows on-demand, on-site manufacturing: The ability to 3D print polymer aerogels using common additive manufacturing equipment (e.g., direct ink writing printers) enables on-demand fabrication of polymer aerogels at the point-of-use.
- Allows polymer aerogel 3D-printing using existing infrastructure: Many of NASA’s polymer aerogel 3D printing techniques can be practiced using conventional direct ink writing printers without the need for additional specialized hardware.
- Eliminates solvent removal step some polymer aerogel formulations: Using NASA’s 3D printing techniques, solvent removal (e.g., supercritical fluid extraction) is not required to fabricate some formulations (this would be required using other techniques). Removing this step reduces infrastructure needs, allowing for easier on-demand fabrication.
Applications
- Thermal insulation (e.g., for electronics, batteries, buildings, spacecraft components, pipelines, aircraft)
- Acoustic insulation (e.g., for aircraft including eVTOL, buildings / architectural acoustics, automotive, aerospace, marine, consumer electronics)
- Vibration mitigation (e.g., for industrial machinery, automotive, aerospace, electronics, buildings, marine applications)
- Construction / Architectural Engineering
- Automotive
- Aerospace
- Antennas
- Sensors
- Energy storage / power devices
- Electronics
Technology Details
Manufacturing
LEW-TOPS-171
LEW-20156-1
Tags:
|
Similar Results

Polymer Cross-Linked Aerogels (X-Aerogels)
Researchers at NASA's Glenn Research Center have developed an approach to significantly improve the mechanical properties and durability of aerogels without adversely affecting their desirable properties. This approach involves coating conformally and cross-linking the individual skeletal aerogel nanoparticles with engineering polymers such as isocyanates, epoxies, polyimides, and polystyrene. The mechanism of cross-linking has been carefully investigated and is made possible by two reactions: a reaction between the cross-linker and the surface of the aerogel framework and a reaction propagated by the cross-linker with itself. By tailoring the aerogel surface chemistry, Glenn's approach accommodates a variety of different polymer cross-linkers, including isocyanates, acrylates, epoxies, polyimides, and polystyreneenabling customization for specific mission requirements. For example, polystyrene cross-linked aerogels are extremely hydrophobic, while polyimide versions can be used at higher temperatures. Recent work has led to the development of strong aerogels with better elastic properties, maintaining their shape even after repeated compression cycling. By tailoring the internal structure of the silica gels in combination with a polymer conformal coating, the aerogels may be dried at the ambient condition without supercritical fluid extraction.

Aerogel Reinforced Composites
GRC's aluminosilicate aerogel composites are fabricated using a sol-gel technique. A sol is formed by hydrolyzing an alumina dispersion in acid solution; the alumina may be combined with a silicon precursor to create a sol.
Fabrics, papers, and felts are used as reinforcing fibers to form an aerogel composite. The aerogel adheres to the reinforcement without use of sizing or organic binders. (In the case of sized fabrics, the sizing is first removed by heat cleaning.) Composites can be fabricated in a batch process, impregnating individual layers of paper, felt or fabric with the precursor sol, or in a roll-to-roll process. The sol is allowed to gel, and then aged for several days prior to supercritical drying using liquid CO2. Heat treatment of the super critically dried composites can be used to tailor the alumina or Aluminosilicate crystal structure and pore size.
In contrast to commercially available insulations, GRC's innovation provides extremely low thermal conductivity (60 mW/m-K at 900°C in argon) at high temperatures, thus enabling use at higher temperatures and improving applicability. In addition, GRC's unique process provides very good adhesion of the aerogel to its reinforcing fibers in alumina papers and zirconia felts, eliminating the spalling seen in other aerogel composites. Finally, GRC's innovation demonstrates low density and extreme resilience to high temperatures and harsh conditions. Seven layers of composite material of 1.25 mm/layer produced a temperature drop of 700°C when tested in the 8-foot high-temperature wind tunnel (8 HTT) at NASA's Langley Research Center. The technology also has withstood heat tests of up to 1200°C. In combination with other insulators, it has withstood fluxes of up to 65 W/cm2, producing a temperature drop of 625°C across 8 mm.

Optically Transparent Polyimide Aerogels
Innovators at NASA Glenn have devised a new method for harnessing the high transmission and clarity associated with optical glasses in a robust polyimide aerogel. This process uses sol-gel synthesis technology with aromatic dianhydrides and diamines as the precursors, and a trifunctional triacid chloride that arranges itself into a three-dimensional (3D) matrix with a low refractive index. The liquid portion of the gel is then removed by supercritical fluid extraction in order to produce the polyimide aerogel and maintain the desired 3D structure without pore collapse. The result is a cross-linked polyimide aerogel that allows for light wave transmittance while retaining low thermal conductivity. This unique material can be made into thin blocks, or highly flexible films as thin as 0.5 mm. While some embodiments have a yellow color, other embodiments may be nearly colorless. When compared to high-opacity polyimide aerogels, they have much greater surface area (up to 880 m2/g) and a very homogenous pore size (10 to 20 nm) with only a minor penalty in density (0.15 g/cc vs 0.10 g/cc). These strong, optically transparent aerogels incorporate a number of unique properties with applicability to a host of potential new applications, making this innovation a game-changer in the global aerogel market. Glenn welcomes co-development opportunities.

Durable Polyimide Aerogels
Aerogels are highly porous, low-density solids with extremely small pore sizes, fabricated by forming a gel from a solution in the wet-gel state that is then converted to the dry-solid state without compaction of the porous architecture. Aerogels make excellent electrical, thermal, and acoustic insulators. However, most inorganic silica aerogels are fragile and shed dust. The NASA Glenn team is the first to synthesize three-dimensional polymer aerogel networks of polyimides cross-linked with multifunctional amine monomers. Compared to silica aerogels, these aerogels retain small pore sizes and low thermal conductivities, but are distinguished by their flexibility. Polyimide aerogels are not brittle, fragile, or dusty like silica aerogels. Plus, polyimide aerogels possess the beneficial characteristics and strength of polyimide materials. The results are cross-linked polyimide aerogels with little shrinkage, low densities, high compression and tensile strengths, and good moisture resistance. They can be fabricated or machined into net shape parts, which are strong and stiff, or cast as thin flexible films with good tensile properties. Extremely customizable, polyimide aerogels can be formed into any configuration (e.g., wrapped around a pipe, sewn into protective clothing, or molded into a panel to act as a heat shield in a car). In short, Glenn's innovation improves the performance, adaptability, and affordability of aerogels in a broad number of applications.

Polyamide Aerogels
Polyamides are polymers that are similar to polyimides (another polymer that has been developed for use in aerogels). However, because the amide link is a single chain while the imide link is a ring structure, polyamide aerogels can be made less stiff than polyimides, even though a similar fabrication process is used. The precursor materials can be made from any combination of diamine and diacid chloride. Furthermore, NASA Glenn researchers have found methods for using combinations of diamines and disecondary amines to produce polyamide aerogels with tunable glass transition temperatures, for greater control of features such as flexibility or water-resistance.
In the first step of the fabrication process, an oligomeric solution is produced that is stable and can be prepared and stored indefinitely as stock solutions prior to cross-linking. This unique feature allows for the preparation and transport of tailor-made polyamide solutions, which can later be turned into gels via the addition of a small amount of cross-linker. When the cross-linking agent is added, the solution can be cast in a variety of forms such as thin films and monoliths. To remove the solvent, one or more solvent exchanges can be performed, and then the gel is subjected to supercritical drying to form a polyamide aerogel. NASA Glenn's polyamide aerogels can be fully integrated with the fabrication techniques and products of polyimide aerogel fabrication, so hybrid materials which have the properties of both classes are easily prepared. As the first aerogels to be composed of cross-linked polyamides, these materials combine flexibility and transparency in a way that sets them apart from all other polymeric aerogels.