Spacecraft with Artificial Gravity Modules
Aerospace
Spacecraft with Artificial Gravity Modules (TOP2-311)
Spacecraft capable of generating artificial gravity environments
Overview
Space travel is becoming increasingly accessible in recent years with the advancement of private space programs as well as NASA space programs such as the Mars Exploration Program. For both space tourism and space exploration, there is an interest in generating artificial gravity in space for entertainment, recreational, and scientific purposes, as well as to counter the health concerns of extended exposure to a microgravity environment. Conventional systems for generating artificial gravity in space involve large rotating space stations that create an inertial force that mimics the effects of a gravitational force. In such examples, the entire space station rotates to generate the artificial gravity that creates several critical engineering and safety issues. NASA Ames Research Center has developed a novel technology that can help provide solutions to these and other problems by a system and approach for creating artificial gravity using a non-rotating spacecraft with connected moving modules, which can be used for habitation and other purposes.
The Technology
Conventionally, the approaches of creating artificial gravity in space was envisioned as a large rotating space station that creates an inertial force that mimics the effects of a gravitational force. However, generating artificial gravity with large rotating structures poses problems, including (1) the need to mass balance the entire rotating spacecraft in order to eliminate or minimize rotational imbalance causing gyroscopic precession/nutation motions and other oscillations of the rotating spacecraft; (2) the potentially prohibitive cost, time and schedule to build such a large rotating system; (3) the need to mass balance the spacecraft in real-time so as to minimize passenger discomfort and structural stress on the spacecraft; (4) the difficulty in docking other spacecraft to the rotating spacecraft; (5) the absence or minimal presence of non-rotating structure for 0G research and industrial use; and (6) the generation of extraneous Coriolis effect on spacecraft inhabitants. The novel technology can help solve the problems referenced above and other problems by (1) providing a non-rotating space station or structure, and connecting modules that generate artificial gravity by traveling along a circular path around the non-rotating space station; (2) providing modules that are more easily built and balanced; (3) providing a stationary structure that can provide a platform for other components that do not need gravity to function; (4) providing capability to actively interrogate what levels of mass imbalance are acceptable, for use in determining operational constraints; and (5) reducing or eliminating Coriolis effect on occupants in habitation modules. The concepts of the invention are very cost-effective and allow for building a minimal initial system to produce artificial gravity at the first phases of construction, before the full structure is built. An additional benefit is that construction and assembly of new capabilities can be performed without disrupting the ongoing artificial gravity environment of the existing structure.
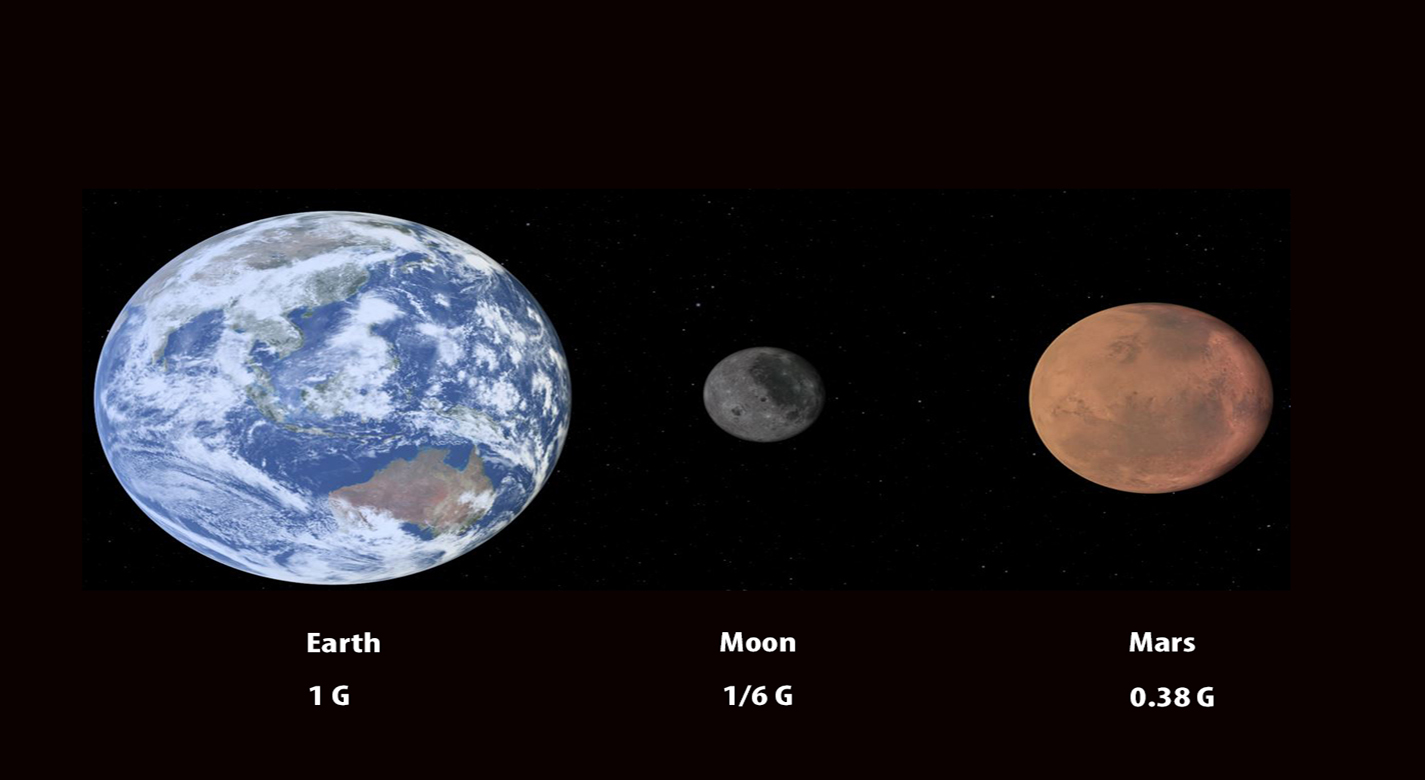
Benefits
- Practical and cost-effective approach: basic configuration can be easily expanded over time to accommodate more space station inhabitants and more capabilities without perturbing the ongoing artificial gravity
- Mass balancing task is much simpler when compared to mass balancing a rotating vehicle
- The paired module configuration minimizes any mass imbalance that would perturb the 0G environment of the vehicle
- The active interrogation capability determines the levels of mass imbalance that are acceptable, to establish operational constraints such as space inhabitants movement and congregation
- The resources required for motion control of each module (e.g., propellant, sensors, software) are much fewer and simpler than for motion control of a large rotating spacecraft
- The invention simplifies the implementation of important systems, such as articulated solar power systems, heat rejection systems, guidance, navigation and control systems
Applications
- Space industry
- Spacecraft manufacturing companies
- Artificial gravity spaceport developers to serve as a gateway for space exploration to other planets
- 0G environment for research and industrial use
- Platform for spacecraft refueling/resupply, housing a fleet of spacecrafts, and space telescope observatory; platform for waste management system, supply and equipment storage, etc.
- Platform for waste management system, supply and equipment storage
- Space construction industry
- Artificial gravity space station
Technology Details
Aerospace
TOP2-311
ARC-18632-1
Wilson, E., Mah, R.W., Automatic Balancing and Intelligent Fault Tolerance for a Space-Based Centrifuge, AIAA Guidance, Navigation, and Control Conference, San Francisco, August 2005. https://www.researchgate.netpublication268554961_Automatic_Balancing_and_Intelligent_Fault_Tolerance_for_a_Space-Based_Centrifuge
Mah, R.W., et. al., Development of Telescope Balancing Methodologies for SOFIA, Astronomical Telescopes and Instrumentation, Kona, Hawaii, March 1998. Also published in Society of Photo-optical Instrumentation Engineers, Volume 3354-127.
https://spie.org/Publications/Proceedings/Paper/10.1117/12.317238
Tags:
|
|
Related Links:
|
Similar Results

Full-Size Reduced Gravity Simulator For Humans, Robots, and Test Objects
The Active Response Gravity Offload System (ARGOS) provides a simulated reduced gravity environment that responds to human-imparted forces. System capabilities range from full gravity to microgravity. The system utilizes input/feedback sensors, fast-response motor controllers, and custom-developed software algorithms to provide a constant force offload that simulates reduced gravity.
The ARGOS system attaches to a human subject in a gimbal and/or harness through a cable. The system then maintains a constant offload of a portion of the subjects weight through the cable to simulate reduced gravity. The system supports movements in all 3 dimensions consistent with the selected gravity level. Front/back and left/right movements are supported via a trolley on an overhead runway and bridge drive system, and up/down movements are supported via a precisely positioned cable. The system runs at a very high cycle rate, and constantly receives feedback to ensure the human subjects safety.

Passive Porous Tube Nutrient Delivery System
The Passive Porous Tube Nutrient Delivery System is a plant growth technique that delivers a nutrient solution to the roots of plants via capillary action. The system was designed for use in microgravity. This new system utilizes a ceramic porous tube and water/nutrients bags connected in a loop. No electricity or moving parts are required. Instead, the nutrients are pumped in through a combination of capillary force and evapotranspiration from the plant. The porous tube supplies the plants with the water and nutrients needed to germinate and grow. This system provides an autonomous plant growth apparatus that is simple to assemble, plant and harvest, minimizing the amount of intervention needed in micro-gravity.

Micro-Organ Device Mimics Organ Structures for Lab Testing
The MOD platform technology represents a small, lightweight, and reproducible in vitro drug screening model that could inexpensively mimic different mammalian tissues for a multitude of applications. The technology is automated and imposes minimal demands for resources (power, analytes, and fluids). The MOD technology uses titanium isopropoxide to bond a microscale support to a substrate and uses biopatterning and 3D tissue bioprinting on a microfluidic microchip to eliminate variations in local seeding density while minimizing selection pressure. With the MOD, pharmaceutical companies can test more candidates and concentrate on those with more promise therefore, reducing R&D overall cost.
This innovation overcomes major disadvantages of conventional in vitro and in vivo experimentation for purposes of investigating effects of medicines, toxins, and possibly other foreign substances. For example, the MOD platform technology could host life-like miniature assemblies of human cells and the effects observed in tests performed could potentially be extrapolated more readily to humans than could effects observed in conventional in vivo cell cultures, making it possible to reduce or eliminate experimentation on animals.
The automated NASA developed technology with minimal footprint and power requirements, micro-volumes of fluids and waste, high throughput and parallel analyses on the same chip, could advance the research and development for new drugs and materials.

Compact Science Experiment Module
The Compact Science Experiment Module (CSEM) provides a suitable experiment platform consisting of an enclosure that contains all the required components to perform science experiments that can house either living biological samples or other samples on both the ground and on the International Space Station (ISS). The invention provides required instrumentation for video capture and data storage, environmental monitoring, inclusive of sensing temperature in degree Celsius, relative humidity as a percentage, carbon dioxide in parts per million and oxygen in percentage format. Data can be stored within the module and retrieved after the experiment or can be transmitted to the ground as for example from the ISS, by connecting to the ISS telemetry system.
The Compact Life Science Experiment Module has been fully developed at NASA Ames Research Center and tested on the ISS. In general, fruit fly studies can provide information about the effects of spaceflight at the biochemical, cellular and organismal levels. Using fruit fly spaceflight hardware, researchers are able to investigate the role of spaceflight on development, growth, reproduction, aging, neurobehavioral responses, immunity, heart function, etc. The fruit fly genome matches the human disease genome by almost 77%, and flies have, therefore, been a useful tool for scientists to understand the genetics, and molecular biology of more complex biological systems like humans. The Compact Science Experiment Module is extremely adaptable to other model specimens and samples as well, and has also flown plant experiments on the ISS. The software can be tailored to accommodate different experiment scenarios by adjusting video imaging times, LED light cycles, data storage and telemetry etc.
ARC ANGEL Reduces Gravity’s Effect on Arms
ARC ANGEL is an active robotic system like ARGOS; however, its electric motor is not mounted overhead to a runway and bridge system, but instead is mounted to the test subject’s backpack-like PLSS where the motor(s) supplies real-time actuation torque off-loading to the upper arms via cabling. If a test subject picks-up a hammer, the system will react immediately to offload the weight of the hammer relative to the programmed environment.
The ARC ANGEL system is comprised of an electric motor(s), soft goods, electronics hardware, firmware, and software. To provide a smoothly operating arm offloading analog and optimize system performance, engineers at JSC coded software that leverages kinematic algorithms and closed-loop architecture for motor control, along with custom computer language scripts to ingest sensor data. This allows ARC ANGEL’s subsystems to be seamlessly integrated and accurately simulate one to zero G environments.
During operation, compact tension sensors and inertial measurement units detect arm weight and motion and provide a closed-loop control system that feeds data to a single-board computer and requisite firmware for processing. A custom graphical user interface was also developed in-house to provide controls for inputting desired arm offload values. Additionally, ARC ANGEL features its own power supply that provides power to its subcomponents without external cables. This allows the ability to function independently from ARGOS and further lends itself to potential terrestrial applications.
This work directly correlates to active exosuit development that is being implemented for rehabilitation and/or assistive medical devices. ARC ANGEL is essentially providing a desired assistance (offload) while maintaining a subject’s full range of motion. The system hardware and software can be modified to custom-fit an individual without a spacesuit and toward limb-assisted movement – not just arm offloading. ARC ANGEL may already meet a higher physical demand and robustness given that it is engineered to perform in challenging environments with greater loads.
ARC ANGEL is at a technology readiness level (TRL) 5 (component and/or breadboard validation in laboratory environment) and is now available for patent licensing. Please note that NASA does not manufacture products itself for commercial sale.