Search
Mechanical and Fluid Systems

ActiVator: A High-Performance Line Climber for Kite-Based Atmospheric Sensing
The ActiVator is a rigid-wing system designed to transport sensor or instrument packages along a kite line using the lift generated by apparent wind. Unlike flexible, sail-like structures, the ActiVator maintains its aerodynamic shape throughout its flight, except for a movable elevator control surface that adjusts the angle of attack to regulate aerodynamic lift. The structural design leverages principles from aircraft wing engineering, incorporating a reinforced spar capable of withstanding lift-induced bending and drag forces, an aerodynamically optimized leading edge, and a thin trailing edge to achieve higher lift coefficients than typical sail-based designs. The ActiVator can be constructed using a variety of materials, including wood with plastic covering, molded foam with reinforcements, or other lightweight composites tailored for both aerodynamic performance and structural integrity.
The control system mirrors conventional aircraft design, using a movable surface for pitch control, thereby adjusting lift to facilitate climbing or descending. Currently, the ActiVator operates via radio-controlled inputs, but it can also be configured for preprogrammed flight sequences, allowing autonomous operation without active user control.
By offering a stable, compact, and lightweight platform, the ActiVator enables high-performance instrument deployment across diverse wind conditions. Potential applications include air-quality monitoring, atmospheric boundary layer research, distributed weather observations, and remote sensing, such as optimizing the field of view and resolution of a fixed-lens camera. The technology is at Technology Readiness Level (TRL) 4 (validated in a laboratory environment) and is available for patent licensing.
sensors
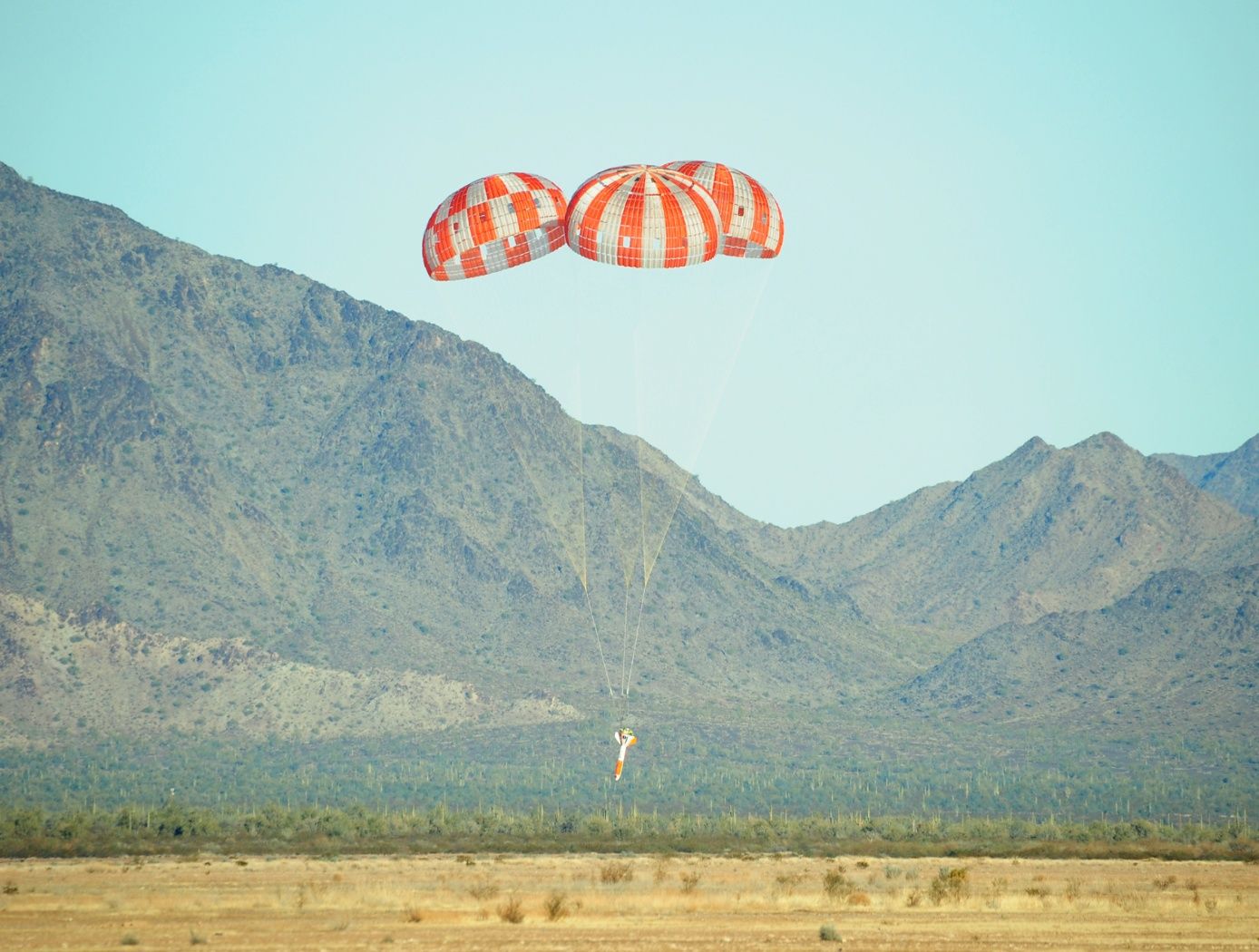
Cord Tension Measurement Device (C-Gauge)
The C-Gauge is made of a 3D-printed aluminum body with strain gauges attached to the inner and outer walls of the connecting beam. The legs of the gauge attach firmly to the cord. When the cord is stretched, the tension in the cord goes through the legs and into the beam, causing it to bend. This bending creates a tension and compression stress in the bottom and top surface of the beam, respectively. The strain gauges capture the tension and compression, which are then used to determine the tension in the cord. The use of multiple strain gauges mitigates any torsion loading of the gauge and provides a direct measurement of the axial tension load of the cord.
The C-Gauge is a low-profile, non-invasive system that can be installed onto an existing cord in a system (e.g., the suspension, reefing, or riser lines in a parachute) without the need to remove or re-install the cord. It is small and lightweight and does not add stiffness or weight to the cord and thus does not affect the dynamics of the parachute or the structural response of the system. The C-Gauge can be scaled to larger and smaller sizes to measure larger and smaller load capabilities, dependent on the cord.
The C-Gauge is at a TRL 4 (component and/or breadboard validation in a laboratory environment) and it is now available for your company to license and develop into a commercial product. Please note that NASA does not manufacture products itself for commercial sale.
Robotics Automation and Control
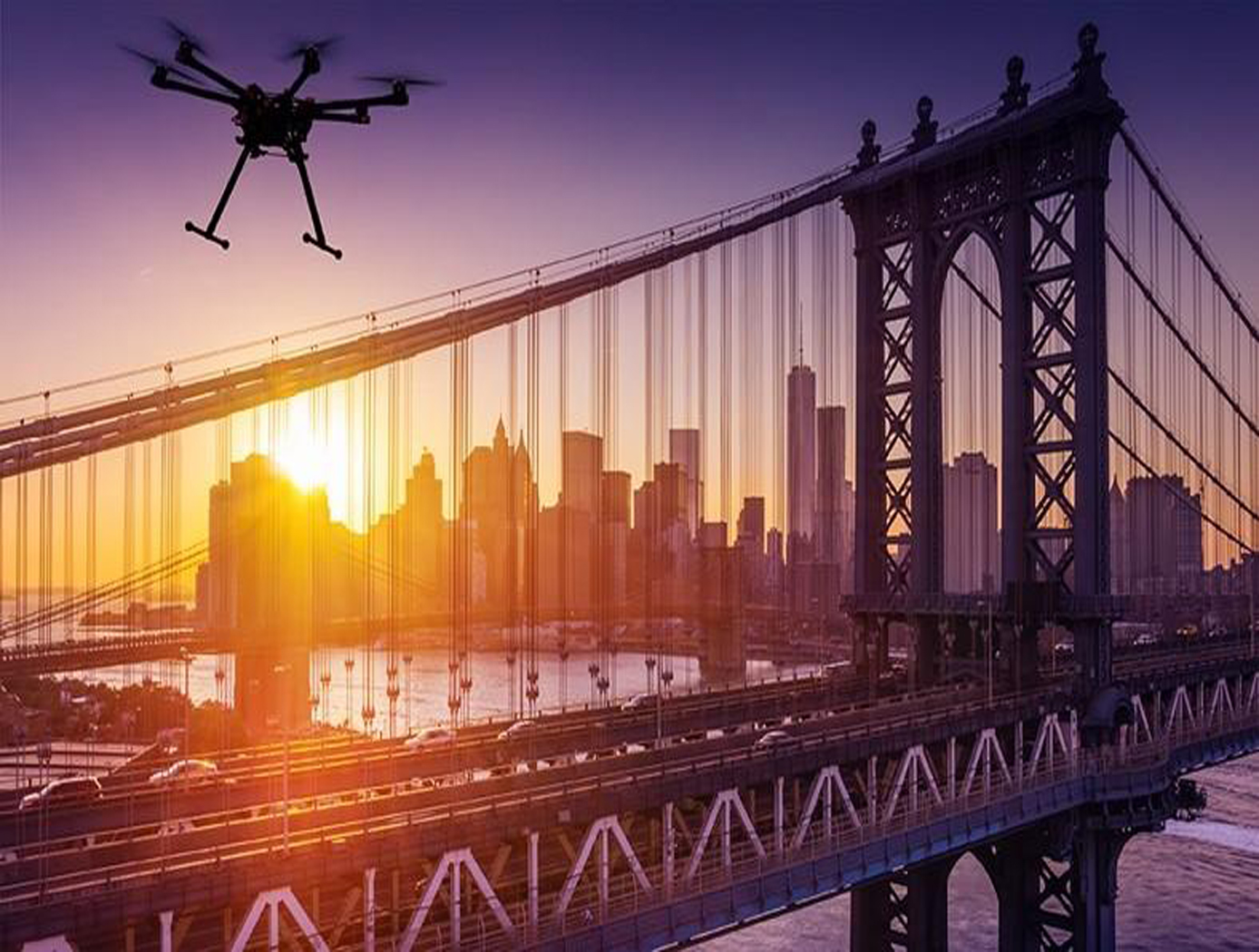
Airborne Machine Learning Estimates for Local Winds and Kinematics
The MAchine learning ESTimations for uRban Operations (MAESTRO) system is a novel approach that couples commodity sensors with advanced algorithms to provide real-time onboard local wind and kinematics estimations to a vehicle's guidance and navigation system. Sensors and computations are integrated in a novel way to predict local winds and promote safe operations in dynamic urban regions where Global Positioning System/Global Navigation Satellite System (GPS/GNSS) and other network communications may be unavailable or are difficult to obtain when surrounded by tall buildings due to multi-path reflections and signal diffusion. The system can be implemented onboard an Unmanned Aerial Systems (UAS) and once airborne, the system does not require communication with an external data source or the GPS/GNSS. Estimations of the local winds (speed and direction) are created using inputs from onboard sensors that scan the local building environment. This information can then be used by the onboard guidance and navigation system to determine safe and energy-efficient trajectories for operations in urban and suburban settings. The technology is robust to dynamic environments, input noise, missing data, and other uncertainties, and has been demonstrated successfully in lab experiments and computer simulations.