Search
Robotics Automation and Control
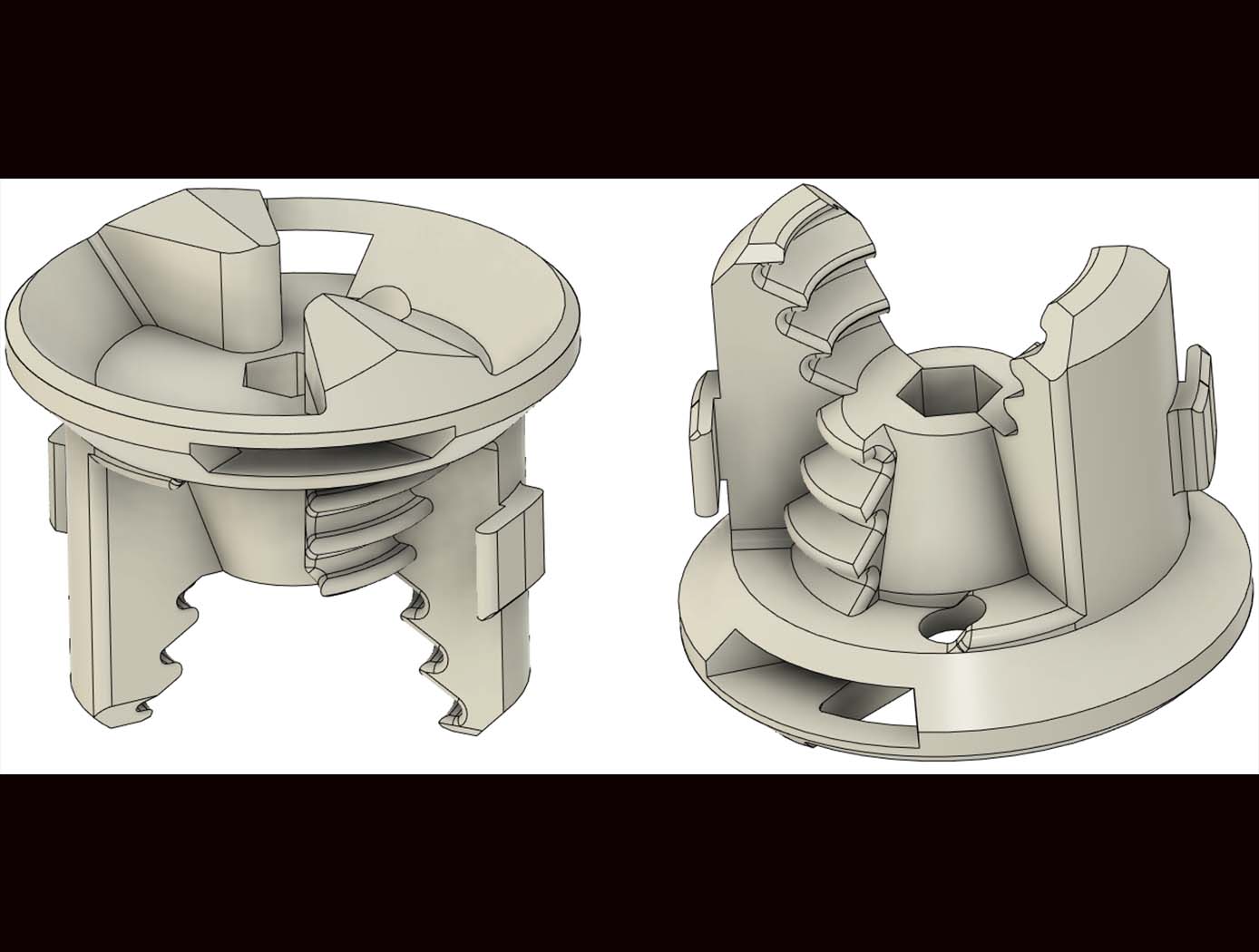
Reversible Androgynous Mechanical Fastener
The androgynous fastener is lightweight and facilitates assembly through simple actuation with large driver-positioning tolerance requirements. This fastener provides a high-strength, reversible mechanical connection and may be used in high strength-to-weight ratio structural systems, such as lattice structure systems. The androgynous fastener resists tensile and shear forces upon loading of the lattice structure system thereby ensuring that the struts of the lattice structure system govern the mechanical behavior of the system. The androgynous fastener eliminates building-block orientation requirements and allows assembly in all orthogonal build directions. This androgynous fastener may be captive in building-block structural elements thereby minimizing the logistical complexity of transporting additional fasteners. Integration of a plurality of the androgynous fasteners into a high performance, robotically managed, structural system reduces launch energy requirements, enables higher mission adaptivity and decreases system life-cycle costs. The androgynous fastener is beneficial in any application where robotic end effectors are used to join structural components (or other parts) together. It may be particularly desirable for applications requiring frequent movement of hardware to an assembly site to replace joint connections.
Robotics Automation and Control

Robotic system for assembly and maintenance of lightweight reconfigurable structures
To enable the goal of autonomous assembly of high performing structures, a robot system must be able to travel across a lattice structure in all dimensions, transport and align a unit cell module to the correct location and fasten the module to the existing structure. In this system, a team of multiple mobile bipedal robots work together to carry, transfer, and place 3D-lattice modules (e.g., cuboctahedron voxels) to form a 3D lattice structure. The team of mobile bipedal robots autonomously provide transportation, placement, unpacking, and assembly of voxel modules into functional structures and systems. As the team of mobile bipedal robots live and locomote on the 3D-lattice structure, they monitor health and performance, enabling repair and reconfiguration when needed. The mobile bipedal robots work together in different roles, for example, one as a cargo transport robot and the other as a crane robot. The cargo transport robot and the crane robot work together to move the voxels from one location to another. Each robot includes at least one electronic control module that receives commands from another robot or a central control system. A central control system implements a plan to control the motion sequences of the robots to maximize efficiency and to optimize the work required to completely assemble a structure. The plan is pre-computed or computed during implementation by the central control system or the robots themselves, according to algorithms that utilize the regularity of the lattice structure to simplify path planning, align robotic motions with minimal feedback, and minimize the number of the degrees of freedom required for the robots to locomote across and throughout the 3D-lattice structure and perform structural assembly.