Search
Aerospace
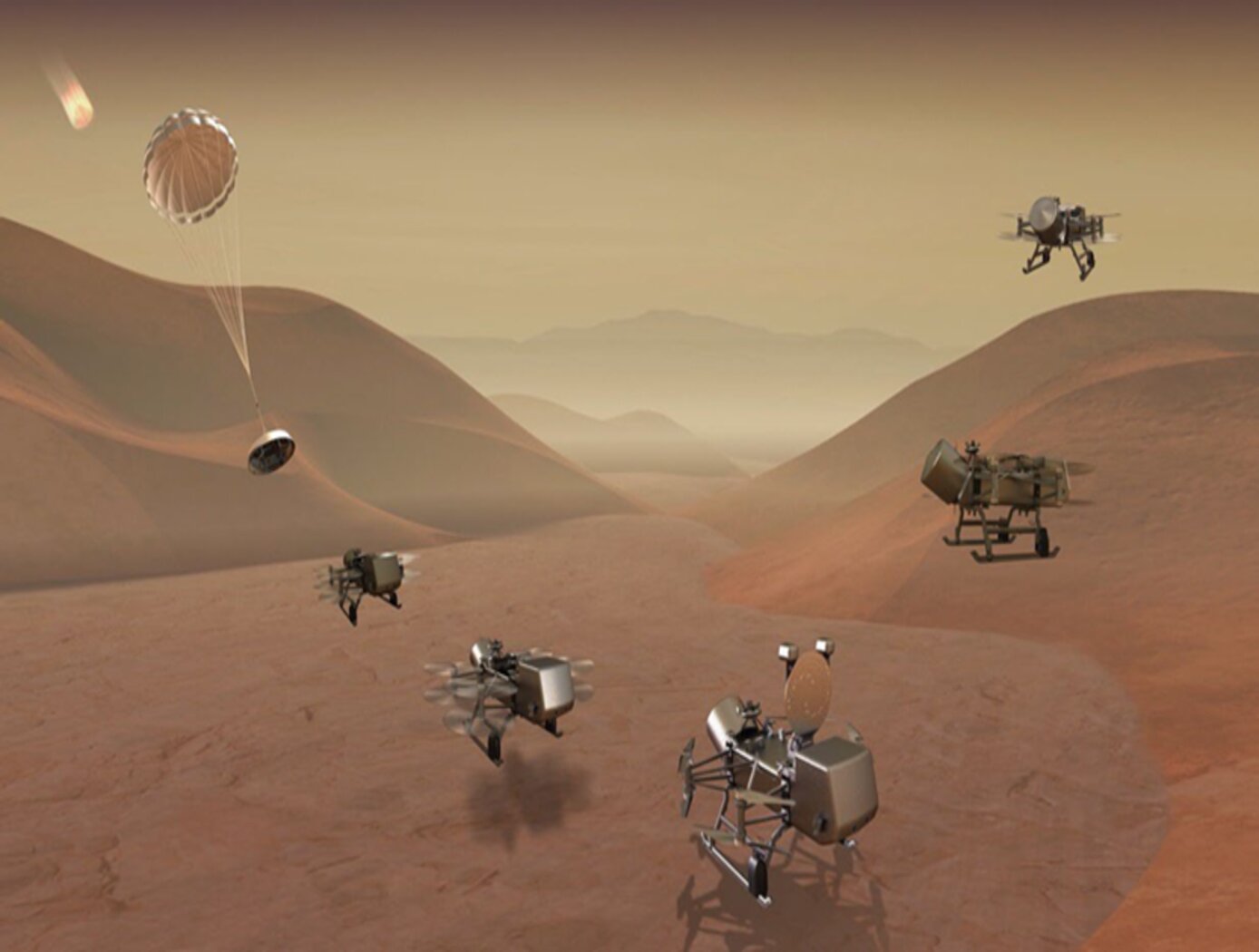
3D Lidar for Autonomous Landing Site Selection
Aerial planetary exploration spacecraft require lightweight, compact, and low power sensing systems to enable successful landing operations. The Ocellus 3D lidar meets those criteria as well as being able to withstand harsh planetary environments. Further, the new tool is based on space-qualified components and lidar technology previously developed at NASA Goddard (i.e., the Kodiak 3D lidar) as shown in the figure below.
The Ocellus 3D lidar quickly scans a near infrared laser across a planetary surface, receives that signal, and translates it into a 3D point cloud. Using a laser source, fast scanning MEMS (micro-electromechanical system)-based mirrors, and NASA-developed processing electronics, the 3D point clouds are created and converted into elevations and images onboard the craft. At ~2 km altitudes, Ocellus acts as an altimeter and at altitudes below 200 m the tool produces images and terrain maps. The produced high resolution (centimeter-scale) elevations are used by the spacecraft to assess safe landing sites.
The Ocellus 3D lidar is applicable to planetary and lunar exploration by unmanned or crewed aerial vehicles and may be adapted for assisting in-space servicing, assembly, and manufacturing operations. Beyond exploratory space missions, the new compact 3D lidar may be used for aerial navigation in the defense or commercial space sectors. The Ocellus 3D lidar is available for patent licensing.
Optics
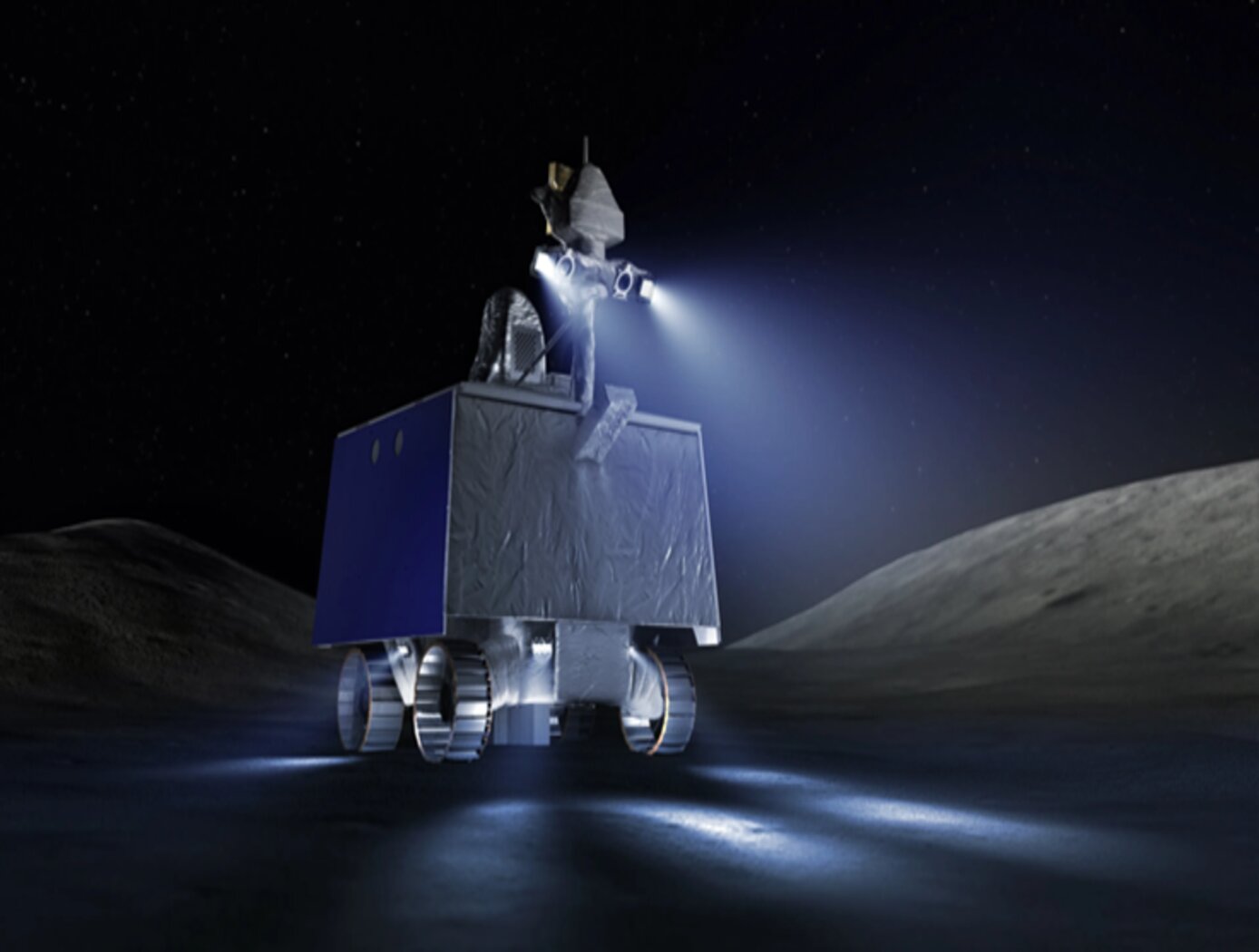
3D Lidar for Improved Rover Traversal and Imagery
The SQRLi system is made up of three major components including the laser assembly, the mirror assembly, and the electronics and data processing equipment (electronics assembly) as shown in the figure below. The three main systems work together to send and receive the lidar signal then translate it into a 3D image for navigation and imaging purposes.
The rover sensing instrument makes use of a unique fiber optic laser assembly with high, adjustable output that increases the dynamic range (i.e., contrast) of the lidar system. The commercially available mirror setup used in the SQRLi is small, reliable, and has a wide aperture that improves the field-of-view of the lidar while maintaining a small instrument footprint. Lastly, the data processing is done by an in-house designed processor capable of translating the light signal into a high-resolution (sub-millimeter) 3D map. These components of the SQRLi enable successful hazard detection and navigation in visibility-impaired environments.
The SQRLi is applicable to planetary and lunar exploration by unmanned or crewed vehicles and may be adapted for in-space servicing, assembly, and manufacturing purposes. Beyond NASA missions, the new 3D lidar may be used for vehicular navigation in the automotive, defense, or commercial space sectors. The SQRLi is available for patent licensing.
environment
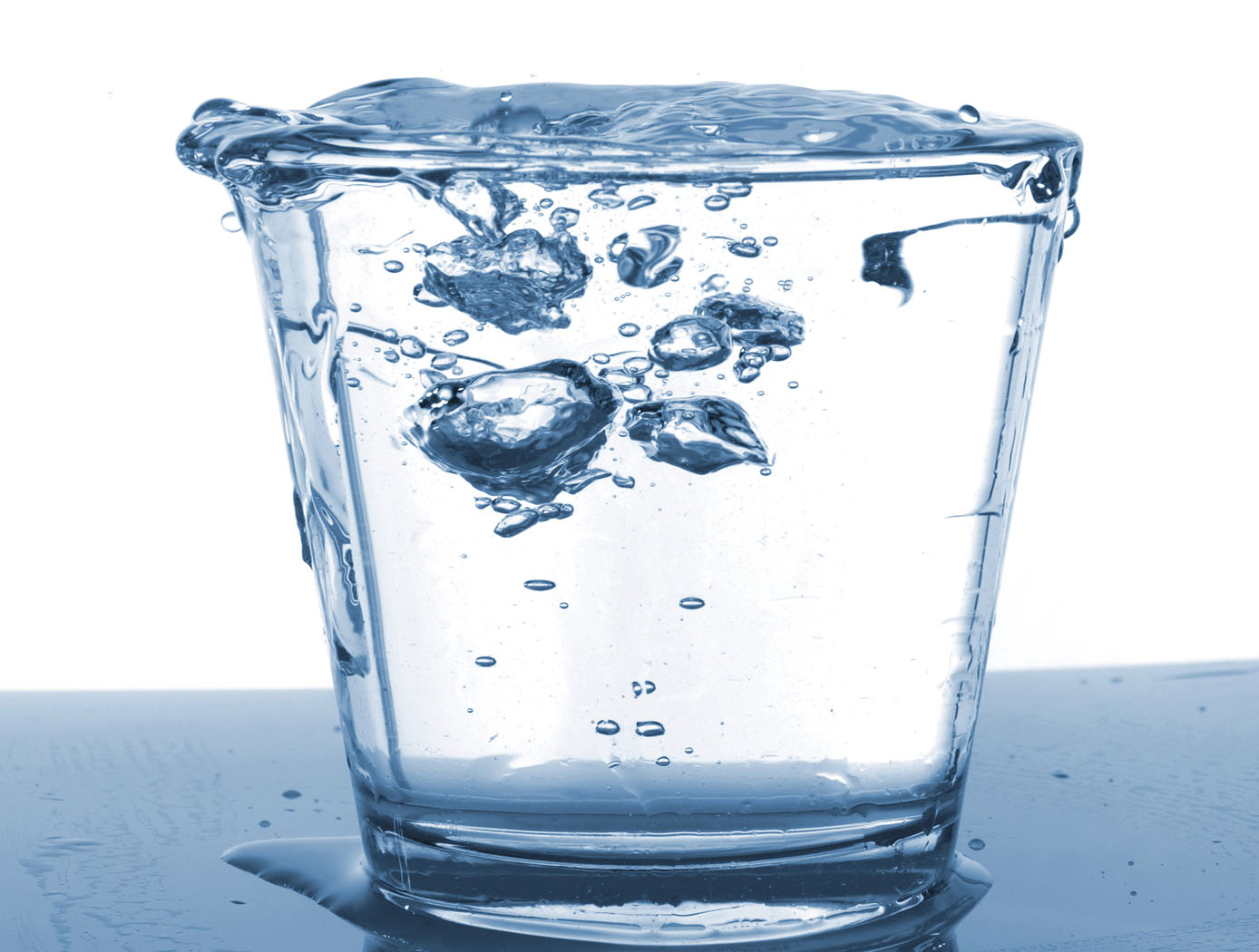
Pre-Treatment Solution for Water Recovery
The pre-treatment solution increases the solubility of calcium in urine brines by reducing the concentration of sulfates. When the solution is properly dosed, it enables biological, physical, and chemical stabilization of flushed urine for storage and distillation up to a steady 87% water recovery, as realized aboard the U.S. segment of the ISS, without precipitation of minerals such as gypsum.
Turning wastewater or seawater into potable water requires three important steps shared by the UPA and Water Recovery System (WRS) aboard the ISS: 1) pre-treatment, 2) distillation or membrane filtration, and 3) transport and storage of potable water and brine. Added during the first step, the pre-treatment solution improves the efficiency of the UPA by reducing the formation of solid precipitates caused by urinary calcium, sulfate ions, and sulfuric acid. This reduction in-turn creates less acidic brines which means more water can be recovered along with less surface scaling and clogging, further increasing recovery. As an added benefit, the solution contains a biocide that prevents the growth of bacteria and fungus, thereby increasing storage time of the treated urine.
Although the pre-treatment solution was developed for the ISSs UPA , the technology can potentially be used on Earth to pretreat contaminated water from organic-laden, high-salinity wastewaters. Adding the solution is a simple process that can be scaled to fit demand. It has the potential to improve water recovery in many applications such as: desalination plants, brackish water treatment, mining water treatment, hydraulic fracturing operations, and more. The pre-treatment solution may also lend itself for use in the transport and storage of wastewater due to the solution's ability to prevent microbial growth.
Robotics Automation and Control

Robotic system for assembly and maintenance of lightweight reconfigurable structures
To enable the goal of autonomous assembly of high performing structures, a robot system must be able to travel across a lattice structure in all dimensions, transport and align a unit cell module to the correct location and fasten the module to the existing structure. In this system, a team of multiple mobile bipedal robots work together to carry, transfer, and place 3D-lattice modules (e.g., cuboctahedron voxels) to form a 3D lattice structure. The team of mobile bipedal robots autonomously provide transportation, placement, unpacking, and assembly of voxel modules into functional structures and systems. As the team of mobile bipedal robots live and locomote on the 3D-lattice structure, they monitor health and performance, enabling repair and reconfiguration when needed. The mobile bipedal robots work together in different roles, for example, one as a cargo transport robot and the other as a crane robot. The cargo transport robot and the crane robot work together to move the voxels from one location to another. Each robot includes at least one electronic control module that receives commands from another robot or a central control system. A central control system implements a plan to control the motion sequences of the robots to maximize efficiency and to optimize the work required to completely assemble a structure. The plan is pre-computed or computed during implementation by the central control system or the robots themselves, according to algorithms that utilize the regularity of the lattice structure to simplify path planning, align robotic motions with minimal feedback, and minimize the number of the degrees of freedom required for the robots to locomote across and throughout the 3D-lattice structure and perform structural assembly.