Search
Mechanical and Fluid Systems
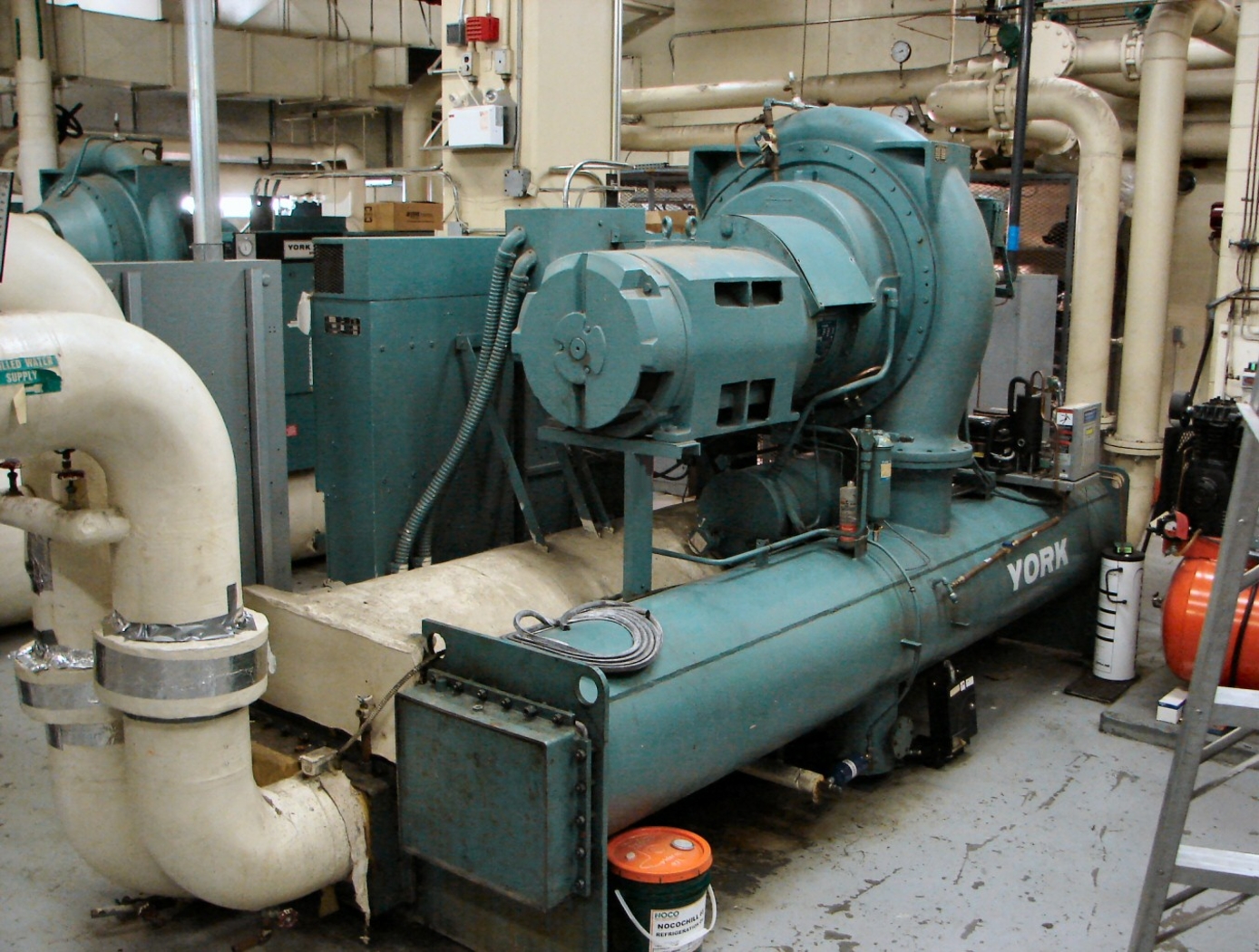
Variable-Aperture Reciprocating Reed (VARR) Valve
The VARR valve has been designed to provide a variable-size aperture that proportionately changes in relation to gas flow demand. When the pressure delta between two chambers is low, the effective aperture cross-sectional area is small, while at high delta pressure the effective aperture cross-sectional area is large. This variable aperture prevents overly restricted gas flow. As shown in the drawing below, gas flow through the VARR valve is not one way. Gas flow can traverse through the device in a back-and-forth reversing flow manner or be used in a single flow direction manner. The contour shapes and spacing can be set to create a linear delta pressure vs. flow rate or other pressure functions not enabled by current standard orifices. Also, the device can be tuned to operate as a flow meter over an extremely large flow range as compared to fixed-orifice meters. As a meter, the device is capable of matching or exceeding the turbine meter ratio of 150:1 without possessing the many mechanical failure modes associated with turbine bearings, blades, and friction, etc.
mechanical and fluid systems
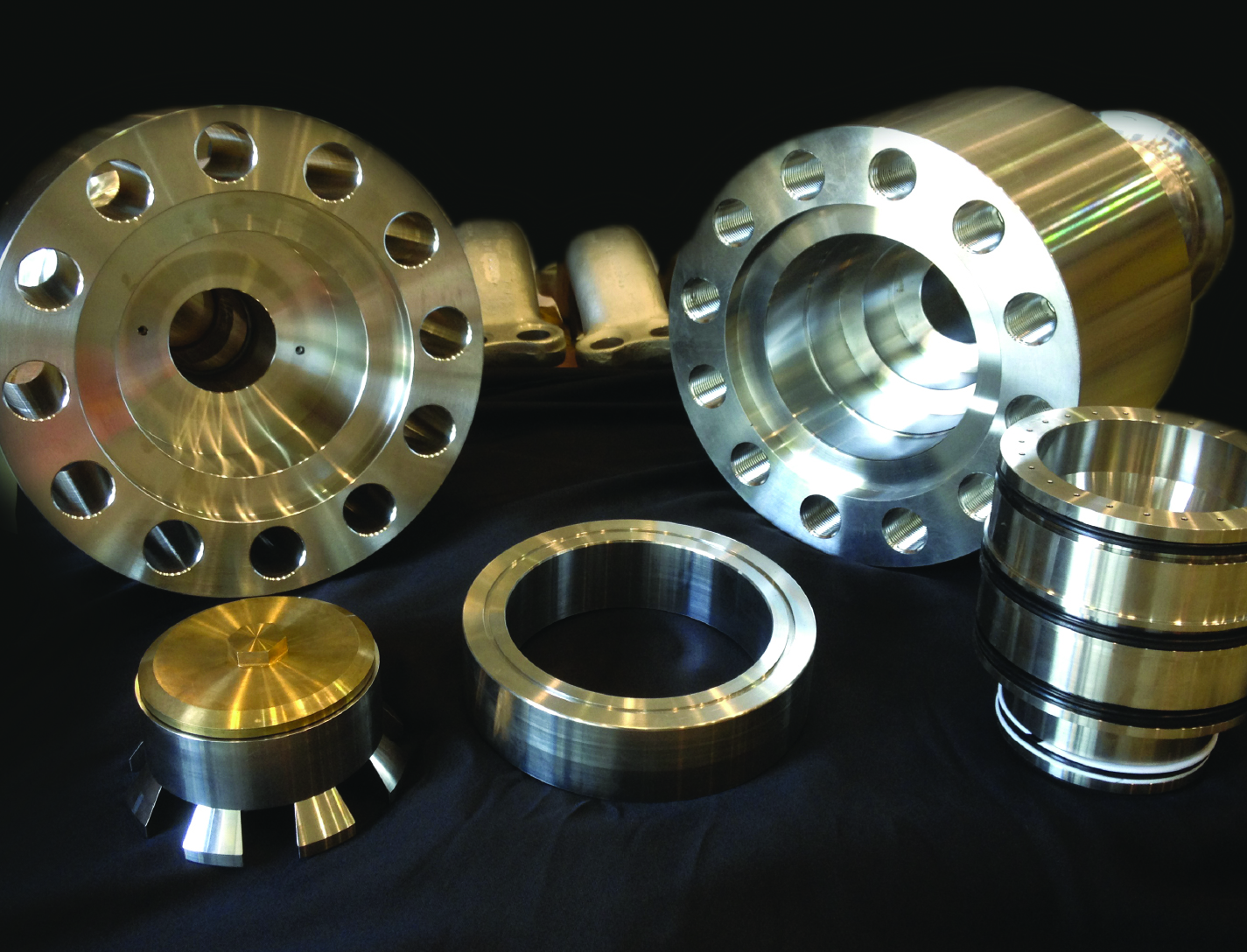
Floating Piston Valve
Instead of looking to improve current valve designs, a new type of valve was conceived that not only addresses recurring failures but could operate at very high pressures and flow rates, while maintaining high reliability and longevity. The valve design is applicable for pressures ranging from 15-15,000+ psi, and incorporates a floating piston design, used for controlling a flow of a pressurized working fluid.
The balanced, floating piston valve design has a wide range of potential applications in all sizes and pressure ranges. The extremely simple design and few parts makes the design inherently reliable, simple to manufacture, and easy to maintain. The valve concept works with soft or hard metal seats, and the closing force is easily adjustable so that any closing force desired can be created. The fact that no adjustment is required in the design, ensures valve performance throughout valve life and operation.
This valve has many unique features and design advantages over conventional valve concepts:
- The largest advantage is the elimination of the valve stem and any conventional actuator, reduces physical size and cost.
- It is constructed with only 5 parts.
- It eliminates the need for many seals, which reduces failure, downtime and maintenance while increasing reliability and seat life.
- The flow path is always axially and radially symmetric, eliminating almost all of the flow induced thrust loads - even during transition from closed to open.
materials and coatings
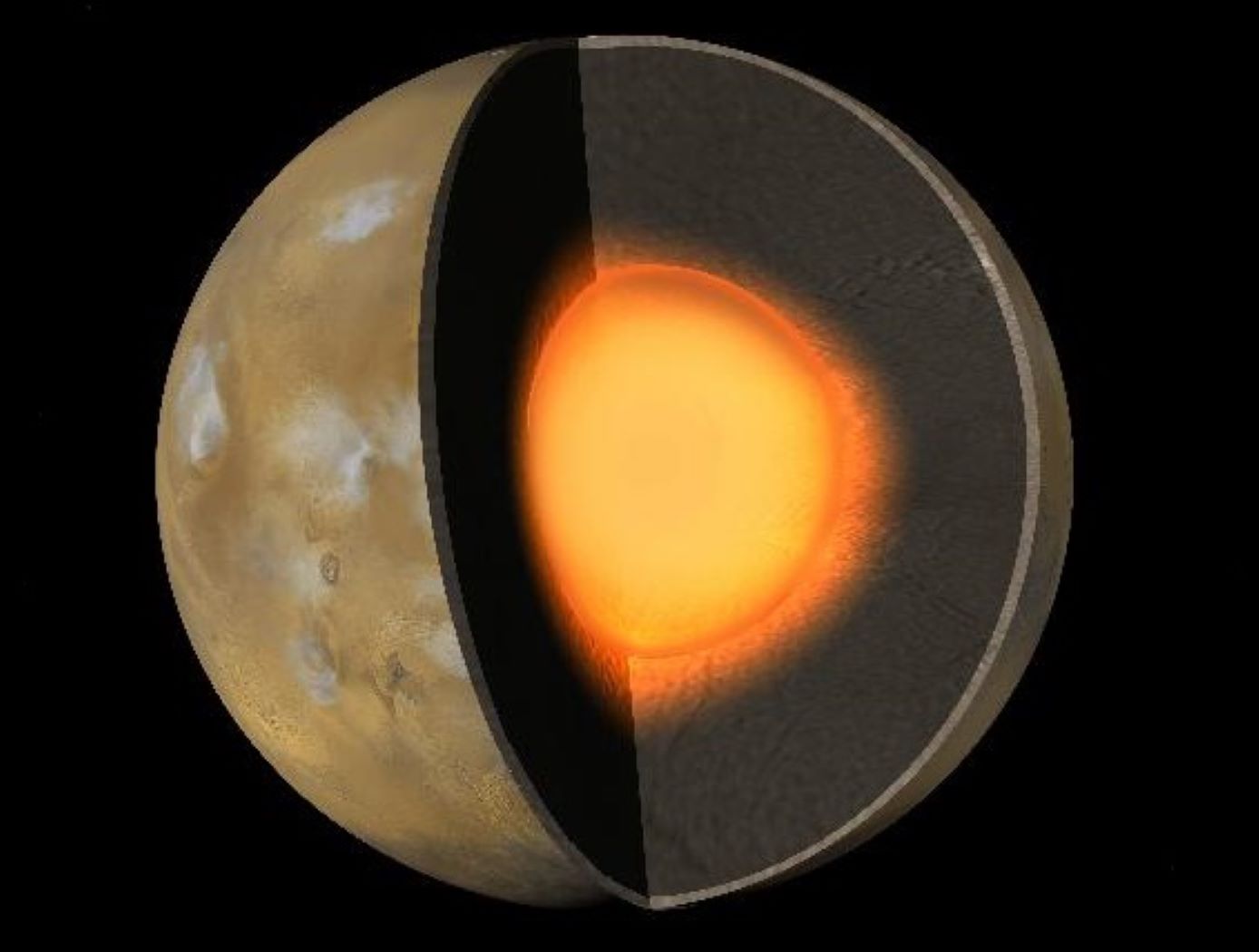
Diamond Maker Technology Simulates Alien Geology in Laboratories
Given the significant impact of fO2 on material properties, it is important to perform studies at fO2 values relevant to the sample of interest. However, current systems used to control fO2 in solid media assemblies (e.g., sliding sensors, graphite capsule buffering) have limited ability to produce the wide fO2 ranges necessary to simulate more extreme planetary interiors.
NASA's fO2 control system implements a modified double capsule design that utilizes a wide range of solid metal-oxide buffers to control fO2 across a wide range of conditions. The approach is a modification of the previous double capsule design wherein the outer capsule itself acts as the metal component of the buffer assemblage, and the inner capsule to which the astromaterial sample of interest is placed resides within the outer capsule.
To achieve higher experimental temperatures above the melting point of more traditional noble metal capsule materials, outer capsules of the control assembly are comprised of refractory (high melting point) metals such as Ni, Co, W, Fe, Mo, V, Cr, Nb and Ta. Resultant experiments have reliably achieved temperatures exceeding 1600 degrees C, and when used in conjunction with a multi-anvil press, system pressures of over 20 GPa can be obtained lending researchers the ability to simulate on or off-world geologic conditions previously difficult to obtain in a laboratory.
NASA's fO2 control system was developed to enable high pressure, high temperature experimental studies of astromaterials at fO2 values relevant to the sample of interest. However, it may also be useful for the synthesis of materials where fO2 control is required (e.g., synthesis of crystal structures that might be stable under higher oxygen pressure). Further use cases may include mineral or melt syntheses, metal-silicate or mineral-melt element partitioning, phase equilibria studies, and the possible development of new chemical and mineral compounds that could not be manufactured in laboratories before.
This fO2 control system technology is at a technology readiness level (TRL) 6 (system/subsystem prototype demonstration in a relevant environment). The innovation is now available for your company to license. Please note that NASA does not manufacture products itself for commercial sale.