Search
Sensors

Optical Mass Sensor for Multi-Phase Flows
Unlike commercial turbine and Venturi-type sensors, which are flow intrusive and prone to high error rates, NASA's new flow sensor technology uses an optical technique to precisely measure the physical characteristics of a liquid flowing within a pipe. It generates a reading of the flows density, which provides a highly accurate mass flow measurement when combined with flow velocity data from a second optical sensor.
NASA's sensor technology provides both a void fraction measurement, which is a measurement of the instantaneous gas/liquid percentage of a static volume and a quality measurement, which is the fraction of flow that is vapor as part of a total mass flow. It also provides a direct measurement of the gas/liquid concentration within the flow, making it suited for real-time measurement of multi-phase flows.
The technology was originally developed to accurately determine the flow rates and tank levels of multi-phase cryogenic fuels used on various NASA vehicles including the Space Shuttle and in ground-based propulsion testing. It can also be used for a wide range of gas/liquid ratios, flows with complex cross sectional profiles, flows containing bubbles or quasi-solids, and essentially any liquid, gas, or multi-phase flow that can be optically characterized. Because it is insensitive to position, the new technology also has potential for use in zero-gravity tank level sensors.
Mechanical and Fluid Systems
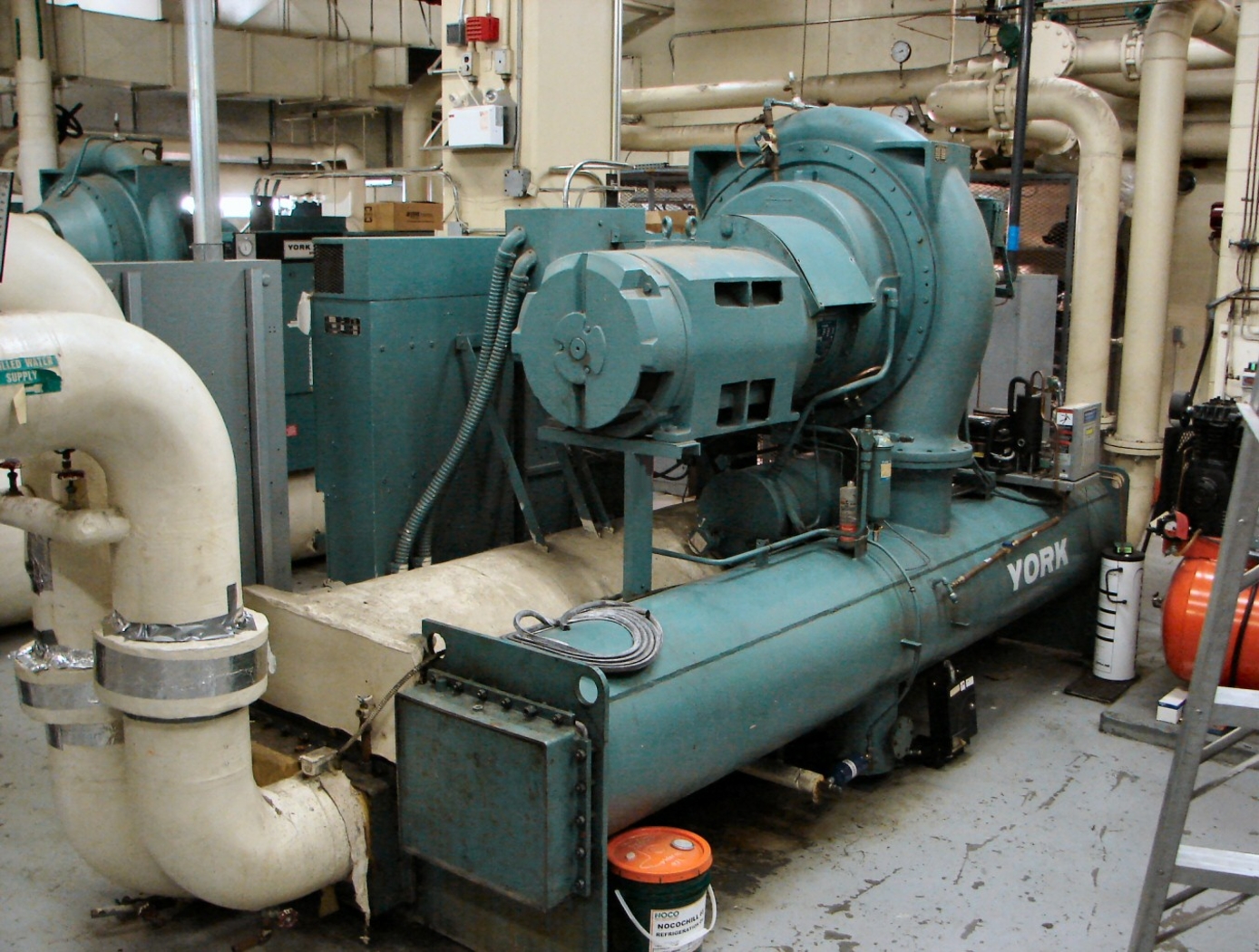
Variable-Aperture Reciprocating Reed (VARR) Valve
The VARR valve has been designed to provide a variable-size aperture that proportionately changes in relation to gas flow demand. When the pressure delta between two chambers is low, the effective aperture cross-sectional area is small, while at high delta pressure the effective aperture cross-sectional area is large. This variable aperture prevents overly restricted gas flow. As shown in the drawing below, gas flow through the VARR valve is not one way. Gas flow can traverse through the device in a back-and-forth reversing flow manner or be used in a single flow direction manner. The contour shapes and spacing can be set to create a linear delta pressure vs. flow rate or other pressure functions not enabled by current standard orifices. Also, the device can be tuned to operate as a flow meter over an extremely large flow range as compared to fixed-orifice meters. As a meter, the device is capable of matching or exceeding the turbine meter ratio of 150:1 without possessing the many mechanical failure modes associated with turbine bearings, blades, and friction, etc.
sensors
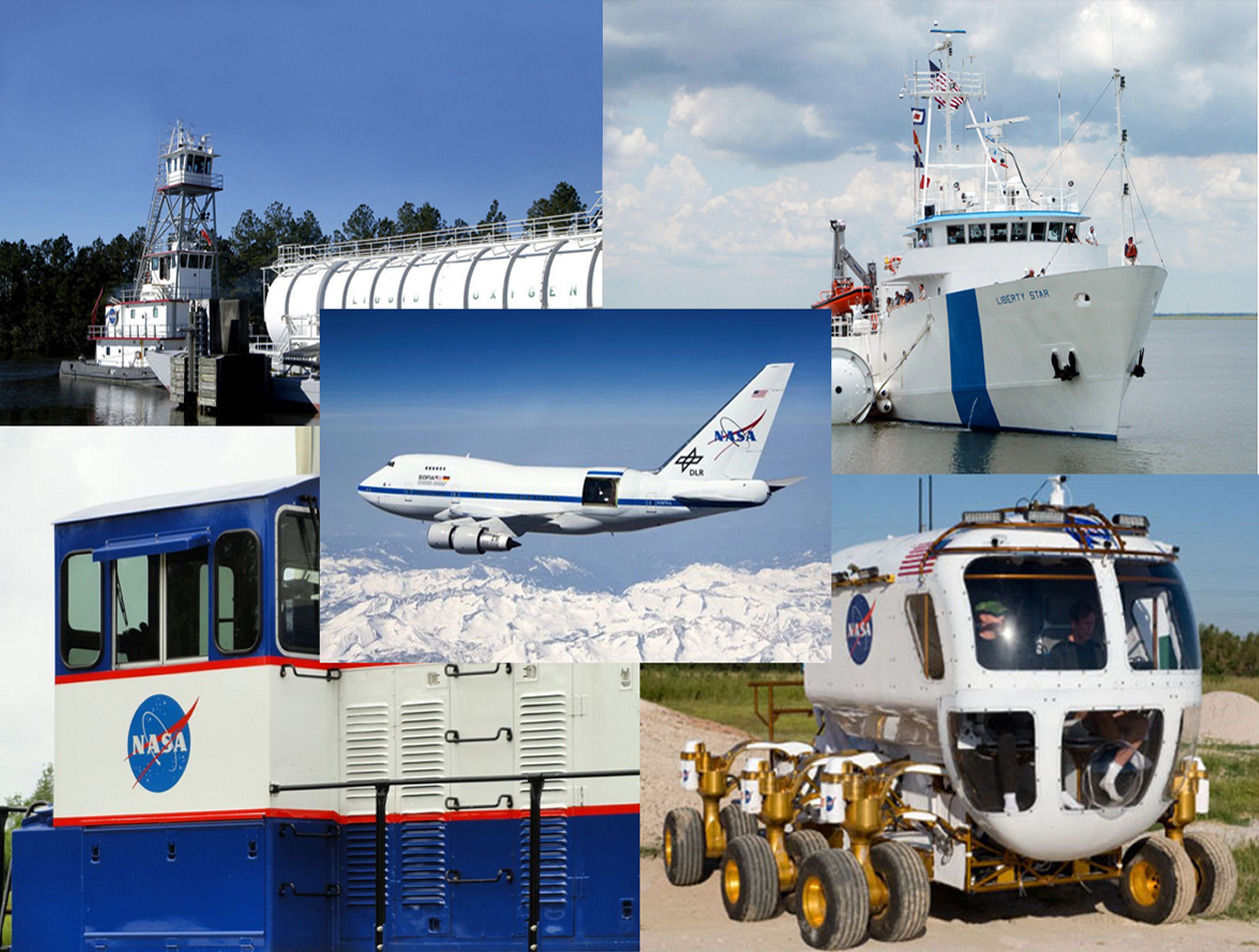
In Situ Performance Monitoring of Piezoelectric Sensors and Accelerometers
On occasion, anomalies may appear in the highly dynamic test data obtained during rocket engine tests, which are investigated and corrective action may be mandated before subsequent testing. Also, it is often unclear if anomalies in recorded signals are due to differences between the Low and High Speed Data Acquisitions Systems, difference between the transducers, a failed transducer, or if everything is working correctly and the system were actually accurately recording real events. Commercial test equipment suitable for testing piezoelectric sensors is expensive and requires that the sensor be removed from the test article for evaluation. With the monitoring system developed, degraded sensor performance can be quickly and economically identified.
This system can evaluate installed piezoelectric sensors, without requiring physical contact with or removing them from their mounted locations. Tests are conducted through cabling. Since it is not necessary to remove the device, data that reflect the devices specific physical configuration (such as as-mounted resonant frequency) are retained, and devices that are physically inaccessible can still be tested. The testing system is not limited to identifying degraded performance in the sensors piezoelectric elements; it can detect changes within the entire sensor, and sensor housing.
The system can be made portable, in a battery powered sealed box, for testing in the field. Since physical contact with the sensor is not necessary, therefore, monitoring can be done as far away as 250 feet, or longer if certain provisions are made.