Search
Robotics Automation and Control
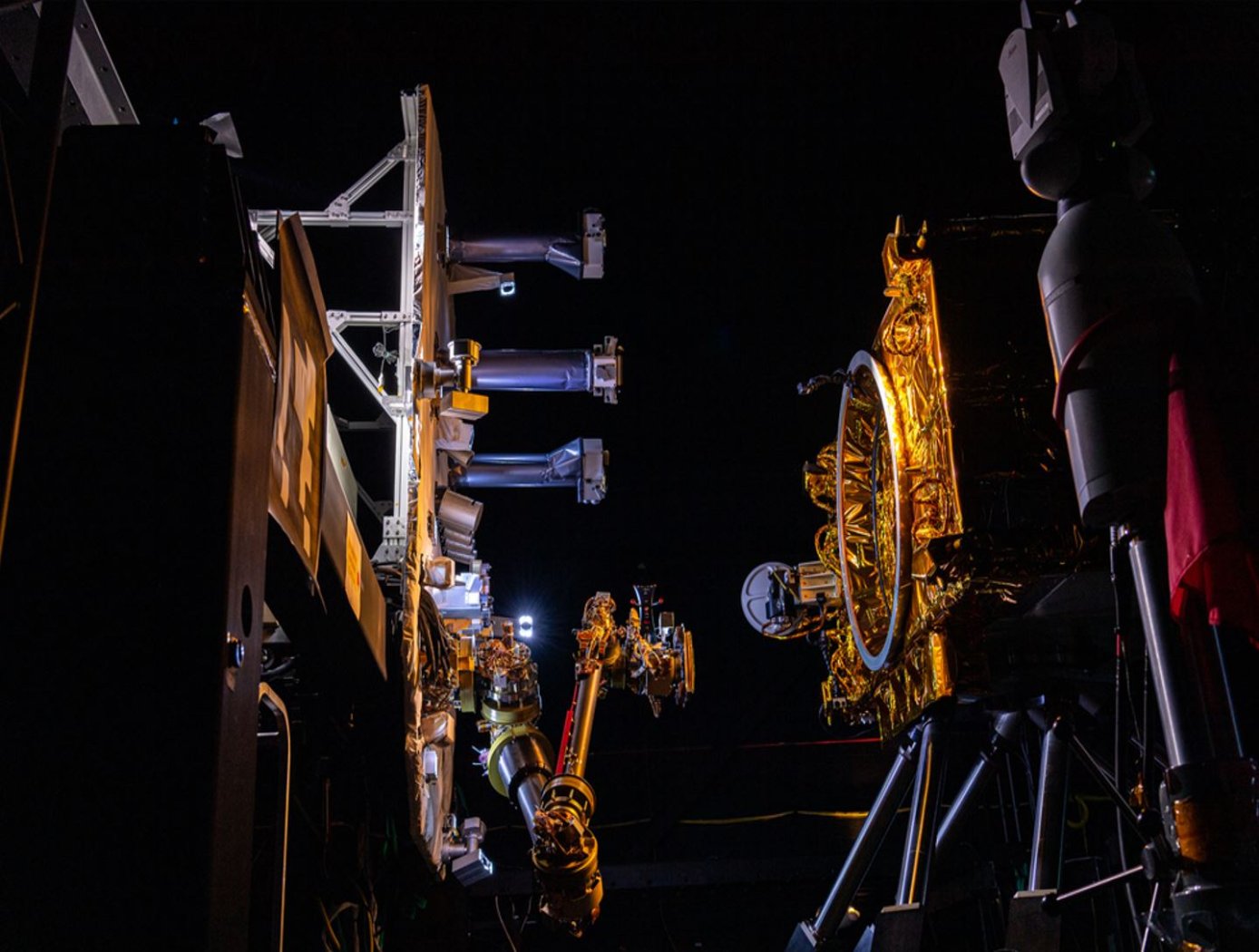
New motors for next-generation in-space servicing
Satellites and other spacecraft require maintenance and service after being deployed in orbit, requiring a wide variety of tools that perform multiple maintenance tasks (grip, cut, refuel, etc.). Current drive systems for the tool interfaces on the robotic arms that perform these service tasks are not as robust nor packaged properly for use in the ATDS. The ATDS is one part of a larger in-space servicing system (example shown in the figure below) that must be versatile and perform multiple jobs.
Here, innovators at the NASA Goddard Space Flight Center have developed new BLDC motors to provide the torque necessary to drive the wide variety of tools needed for in-space servicing. The four motors provide torque to the coupler drive, linear drive, inner rotary drive, and outer rotary drive of the ATDS. The new BLDC motors will enable the tools attached to the ATDS to be operated in multiple modes of operation.
Each of the four motors have been customized with different speed and torque capabilities to meet the different performance requirements of the various actuator drive trains while maintaining a common gearhead across all the motors. Further, the packaging surrounding the motors has been tailored to reduce the overall weight of the motors and reduce the motor footprint to meet the needs of the ATDS. The BLDC motors for the ATDS are available for patent licensing.
Robotics Automation and Control

Client Berthing System (CBS)
The Client Berthing System (CBS) was originally designed for NASA’s On-orbit Servicing, Assembly, and Manufacturing 1 (OSAM-1) spacecraft, which will grapple and refuel the LandSat 7 satellite. After the OSAM-1 spacecraft has rendezvoused with LandSat 7, a robotic arm equipped with a gripper tool will autonomously grapple the satellite’s Marman ring (launch separation ring) and affix it to the CBS in the appropriate refueling position. The CBS is comprised of three posts protruding from the servicing satellite, each with integrated berthing mechanisms, distributed in a radial pattern of 120° along the client’s Marman ring diameter. Each berthing mechanism includes a rotary clamping jaw with a drawdown and radial contact portion. The clamping jaws are actuated by a motor-driven leadscrew and guided by recirculating linear ball bearings.
After the servicing spacecraft’s robotic arm has placed the client satellite Marman ring into the CBS berthing box, the clamping jaws simultaneously move radially inward towards the center of the ring. The lead-in features of the jaws exert downward pressure on the ring, driving it towards the jaw palms as the lead-in portion rises over the surface of the ring flange. Once the flange is drawn down such that it contacts the radial clamp surface of the jaws, force is exerted causing the jaws to pivot, driving the underside of the lead-in surfaces into contact with the upper flange surface. As the jaw mechanisms continue to drive, increased axial load squeezes the ring flange between the lead-in-feature and palm of the jaws, stabilizing the connection. At a predetermined load, brakes are engaged, and system motors shut off. A NASA-developed Marman ring location detection system is employed to guide the berthing process.
NASA has developed a suite of cutting-edge technologies that can help your business develop robust satellite servicing offerings. For additional information, please see the <i>NASA Satellite Servicing Technologies Available for Licensing</i> link provided.
Robotics Automation and Control

Visual Inspection Posable Invertebrate Robot (VIPIR)
Initially developed as a close quarters inspection tool capable of accessing hard to reach, tight, or visibly restricted, areas of satellites, the VIPIR system can be used to remotely inspect inaccessible locations such as behind a sheet of thermal blanketing material, into a satellites plumbing, or perhaps even deep inside the otherwise unreachable crevasses of a spacecraft bus. The VIPIR system incorporates a number of subassemblies for incredible operational freedom and capabilities for imaging and dissemination of componentry.
VIPIR’s Video Borescope Assembly (VBA) is a flexible snake-camera capable of multidirectional articulations, making steering and control simple and intuitive for an operator. The VBA also includes at least one imaging sensor and lighting to see in dark, confined spaces. Real-time, high-resolution visual information can be fed back to an operator for live analysis. A reel system extends and retracts the VBA with the use of a spool, and includes position indicators for deployment tracking. The Tendon Management System (TMS), not unlike human tendons, utilizes pulleys and tensioners to articulate the VBA in the confined spaces. A seal system ensures the VBA is free of contamination.
VIPIR underwent space-based testing on the ISS during the Robotic Refueling Phase 2 (RRM-2) mission designed to showcase and test several NASA advanced robotic satellite servicing technologies. During this mission, VIPIR demonstrated state-of-the-art near and midrange inspection capabilities. NASA’s VIPIR system is available for licensing to industry, and may be desirable to companies focused on satellite servicing, on-orbit assembly, and other applications requiring detailed inspection of assets in space.