Shape Sensing Innovations Dramatically Improve Structural Design Tools
sensors
Shape Sensing Innovations Dramatically Improve Structural Design Tools (DRC-TOPS-24)
Useful for transportation, infrastructure, and aerospace
Overview
Advances in fiber optic shape sensing developed at NASA's Armstrong Flight Research Center are enabling the development of next-generation flexible aircraft wings that maximize structural efficiency and reduce weight, improving fuel efficiency. These same advances will help engineers design stronger bridges, buildings, ocean vessels, and more. Fast algorithms use distributed fiber optic wavelength data to determine shape deformation of large curved and flexible structures. Dramatically improving upon earlier two- and three-dimensional (2D and 3D) shape-sensing tools by tracking multiple orientation angles—displacement, twist, and rotation—at the same time, Armstrong's technology converts distributed surface strain data into deformed shapes that can be displayed and analyzed in real time. Developed to help NASA researchers characterize complex test articles and design new aerospace structures, the innovations also will be useful for multiple applications in the transportation, infrastructure, and medical industries.
The Technology
Armstrong's technologies provide a convenient way to calculate distributed deformed orientation angles—that is, roll, pitch, and yaw—as well as determine the deformed shape of an object in 3D space. Developed to facilitate monitoring and control of flexible aircraft designs when used in conjunction with Armstrong's multi-patented FOSS technology, these new tools improve shape-sensing accuracy for highly deformable structures such as bridges, wind turbines, robotic instruments, and much more. These tools also can be integrated into commercial fiber optic sensing systems.
How It Works
Researchers developed a technology that uses curved displacement transfer functions to determine 3D shape and calculate the operational load of a structure. It works by dividing the structure into multiple small domains, whose junctures match sensing stations, so that data is collected in a piecewise, nonlinear fashion. The innovation calculates structural stiffness (bending and torsion) and operational loads (bending moments, shear loads, and torques) in near real time.
The method tracks rotations and orientation by employing quaternion mathematical operations, a faster process than rotation matrices used in previous shape-sensing algorithms. The result is an algorithm that can track multiple angles—displacement, twist, and rotation—at the same time to enable curvilinear shaping sensing. Armstrong researchers have validated the method on the large-scale passive aeroelastic tailored (PAT) wing.
Why It Is Better
These new technologies advance the ability of fiber optic sensing systems to determine the shape and operational loads of nonlinear flexible surfaces. They can improve the structural integrity of a range of large structures—from buildings and bridges to ocean vessels and aircraft. These innovations reliably provide highly accurate critical information in real time, enabling corrective action to avert disasters.
For more information about the full portfolio of FOSS technologies, see DRC-TOPS-37 or visit https://technology-afrc.ndc.nasa.gov/featurestory/fiber-optic-sensing
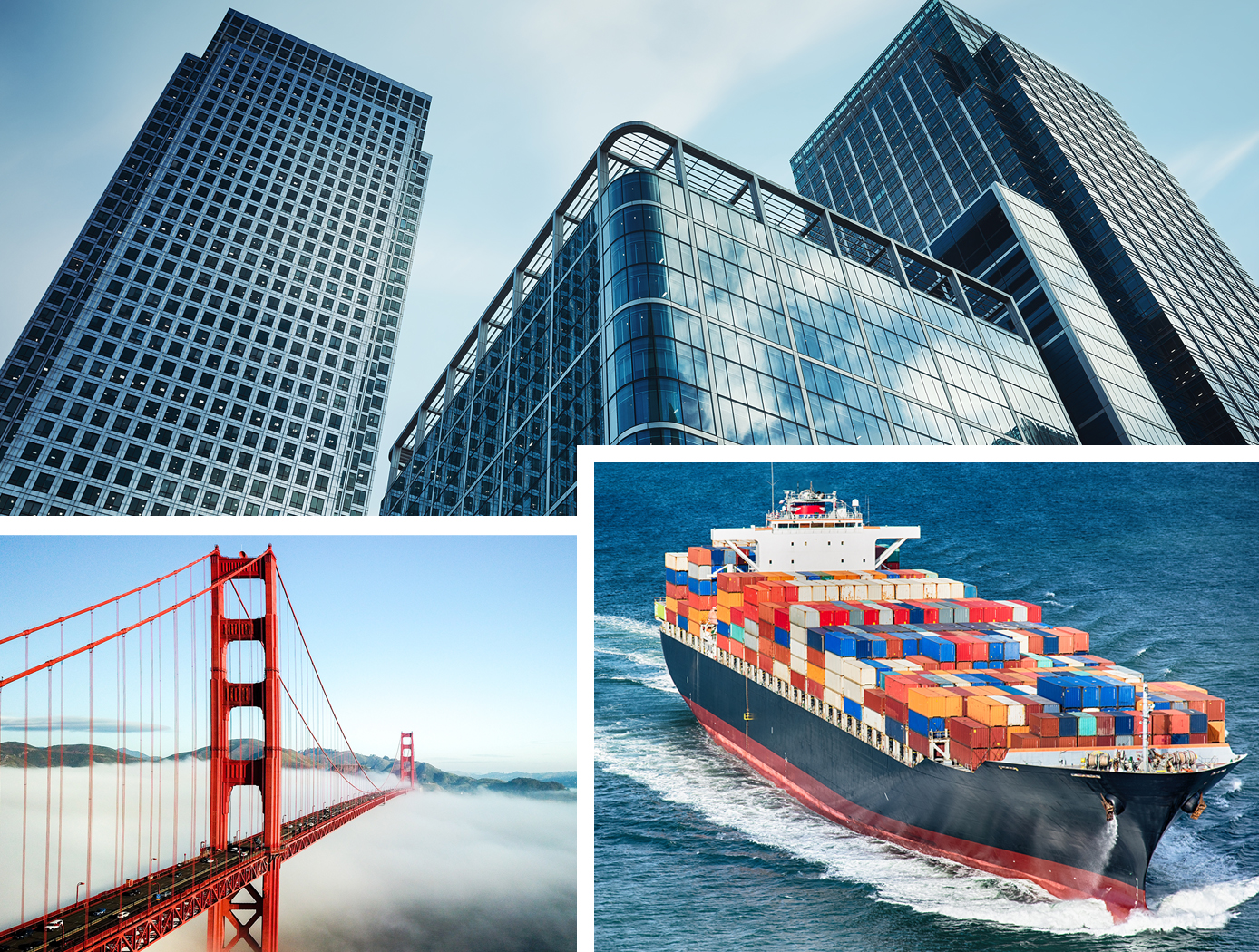
Benefits
- Improved safety: Monitors structural deformations of large structures
- Increased accuracy: Improves 3D shape-sensing accuracy for highly flexible structures by recording distributed twist
- Real time: Enables quaternion-based mathematical operations, which are computationally faster than more commonly used rotation matrices
- Compatible: Works with a range of fiber optic sensing systems, including NASA's award-winning Fiber Optic Sensing System (FOSS) portfolio
Applications
- Transportation and Infrastructure Structural health monitoring of buildings, bridges, oil platforms, ocean vessels, wind turbines, and other large structuresLoad balancing on cargo shipsDesigning truck and automobile frames and suspension for dynamic control and handling
- AerospaceReal-time structural health monitoring Controlling flexible aircraft wings and morphing structuresRefueling unmanned aerial vehicles (UAVs) in flightDesigning aircraft structures
- MedicalPerforming robotic surgeryEvaluating anthropomorphic test figures
Technology Details
sensors
DRC-TOPS-24
DRC-016-040
DRC-017-024
Presentation of wing load test results, January 2019 https://ntrs.nasa.gov/archive/nasa/casi.ntrs.nasa.gov/20190000062.pdf
Paper presented at AIAA SciTech Forum 2019 https://ntrs.nasa.gov/archive/nasa/casi.ntrs.nasa.gov/20190000082.pdf
Paper presented at AIAA SciTech Forum 2019 https://ntrs.nasa.gov/archive/nasa/casi.ntrs.nasa.gov/20190000082.pdf
Similar Results

Lightweight Fiber Optic Sensors for Real-Time Monitoring of Structural Health
How It Works
The FOSS technology employs efficient, real-time, data driven algorithms for interpreting strain data. The fiber Bragg grating sensors respond to strain due to stress or pressure on the substrate. The sensors feed these strain measurements into the systems algorithms to determine shape, stress, temperature, pressure, strength, and operational load in real time.
Why It Is Better
Conventional strain gauges are heavy, bulky, spaced at distant intervals (which leads to lower resolution imaging), and unable to provide real-time measurements. Armstrong's system is virtually weightless, and thousands of sensors can be placed at quarter-inch intervals along an optical fiber the size of a human hair. Because these sensors can be placed at such close intervals and in previously inaccessible regions (for example, within bolted joints, embedded in a composite structure), the high-resolution strain measurements are more precise than ever before. The fiber optic sensors are non-intrusive and easy to install—thousands of sensors can be installed in less time than conventional strain sensors and the system is capable of processing information at the unprecedented rate of 100 samples per second. This critical, real-time monitoring capability enables an immediate and informed response in the event of an emergency and allows for precise, controlled monitoring to help avoid such scenarios.
For more information about the full portfolio of FOSS technologies, see DRC-TOPS-37 or visit https://technology-afrc.ndc.nasa.gov/featurestory/fiber-optic-sensing

Flexible Body Control Using Fiber Optic Sensors (FlexFOS)
Aerospace vehicles experience flexible dynamics that have adverse effects on guidance, navigation, and control. Vehicles that include automated control are further affected by flexible modes and structural vibrations. Flexible dynamics become even more critical as demand for larger and more fuel efficient vehicles increases.
Using fiber optic technology to collect both flexible and rigid body information enables increased knowledge (data) of the state of a vehicle, a more robust collection method against weather conditions, and a more cost-effective measurement method. This technology could potentially be applied to aerospace vehicles as well as commercial space structures, commercial aerospace structures, cranes, buildings, or bridges - anything with a large cross sectional ratio.
The RSS is the key to developing a sensor which provides flexible body kinematics. A reference structure must be chosen that minimizes weight impacts while retaining structural integrity. The reference structure material must also be very predictable and repeatable. Once this geometry has been optimized, analyzed, and mapped it is integrated with strain sensors making it a Reference Strain Structure. The RSS must then be integrated into an adaptive structure, which both protects and provides a connection to the desired structure to be measured.
The RSS combined with the properly designed algorithms provides the capability and portability to be installed on any of the aforementioned structures alleviating unique engineering and calibration required for each structure or vehicle. It also provides the capability to employ actuators to counteract the effects of structural vibrations. FlexFOS provides a simple, portable solution adaptable to any structure.

Fiber Optic Sensing Technologies
The FOSS technology revolutionizes fiber optic sensing by using its innovative algorithms to calculate a range of useful parameters—any and all of which can be monitored simultaneously and in real time. FOSS also couples these cutting-edge algorithms with a high-speed, low-cost processing platform and interrogator to create a single, robust, stand-alone instrumentation system. The system distributes thousands of sensors in a vast network—much like the human body's nervous system—that provides valuable information.
How It Works
Fiber Bragg grating (FBG) sensors are embedded in an optical fiber at intervals as small as 0.25 inches, which is then attached to or integrated into the structure. An innovative, low-cost, temperature-tuned distributed feedback (DFB) laser with no moving parts interrogates the FBG sensors as they respond to changes in optical wavelength resulting from stress or pressure on the structure, sending the data to a processing system. Unique algorithms correlate optical response to displacement data, calculating the shape and movement of the optical fiber (and, by extension, the structure) in real time, without affecting the structure's intrinsic properties. The system uses these data to calculate additional parameters, displaying parameters such as 2D and 3D shape/position, temperature, liquid level, stiffness, strength, pressure, stress, and operational loads.
Why It Is Better
FOSS monitors strain, stresses, structural instabilities, temperature distributions, and a plethora of other engineering measurements in real time with a single instrumentation system weighing less than 10 pounds. FOSS can also discern between liquid and gas states in a tank or other container, providing accurate measurements at 0.25-inch intervals. Adaptive spatial resolution features enable faster signal processing and precision measurement only when and where it is needed, saving time and resources. As a result, FOSS lends itself well to long-term bandwidth-limited monitoring of structures that experience few variations but could be vulnerable as anomalies occur (e.g., a bridge stressed by strong wind gusts or an earthquake).
As a single example of the value FOSS can provide, consider oil and gas drilling applications. The FOSS technology could be incorporated into specialized drill heads to sense drill direction as well as temperature and pressure. Because FOSS accurately determines the drill shape, users can position the drill head exactly as needed. Temperature and pressure indicate the health of the drill. This type of strain and temperature monitoring could also be applied to sophisticated industrial bore scope usage in drilling and exploration.
For more information about the full portfolio of FOSS technologies, see visit https://technology-afrc.ndc.nasa.gov/featurestory/fiber-optic-sensing

Adaptive Spatial Resolution Enables Focused Fiber Optic Sensing
This technology can be applied to most optical frequency domain reflectometry (OFDR) fiber optic strain sensing systems. It is particularly well suited to Armstrong's FOSS technology, which uses efficient algorithms to determine from strain data in real time a variety of critical parameters, including twist and other structural shape deformations, temperature, pressure, liquid level, and operational loads.
How It Works
This technology enables smart-sensing techniques that adjust parameters as needed in real time so that only the necessary amount of data is acquired—no more, no less.
Traditional signal processing in fiber optic strain sensing systems is based on fast Fourier transform (FFT), which has two key limitations. First, FFT requires having analysis sections that are equal in length along the whole fiber. Second, if high resolution is required along one portion of the fiber, FFT processes the whole fiber at that resolution. Armstrong's adaptive spatial resolution innovation makes it possible to efficiently break up the length of the fiber into analysis sections that vary in length. It also allows the user to measure data from only a portion of the fiber. If high resolution is required along one section of fiber, only that portion is processed at high resolution, and the rest of the fiber can be processed at the lower resolution.
Why It Is Better
To quantify this innovation's advantages, this new adaptive method requires only a small fraction of the calculations needed to provide additional resolution compared to FFT (i.e., thousands versus millions of additional calculations). This innovation provides faster signal processing and precision measurement only where it is needed, saving time and resources. The technology also lends itself well to long-term bandwidth-limited monitoring systems that experience few variations but could be vulnerable as anomalies occur.
More importantly, Armstrong's adaptive algorithm enhances safety, because it automatically adjusts the resolution of sensing based on real-time data. For example, when strain on a wing increases during flight, the software automatically increases the resolution on the strained part of the fiber. Similarly, as bridges and wind turbine blades undergo stress during big storms, this algorithm could automatically adjust the spatial resolution to collect more data and quickly identify potentially catastrophic failures.
This innovation greatly improves the flexibility of fiber optic strain sensing systems, which provide valuable time and cost savings to a range of applications.
For more information about the full portfolio of FOSS technologies, see DRC-TOPS-37 or visit https://technology-afrc.ndc.nasa.gov/featurestory/fiber-optic-sensing

Highly Accurate Position Detection and Shape Sensing with Fiber Optics
NASA's novel method was developed to more accurately measure the position and shape of optical fibers. Multi-core optical fibers contain multiple light-guiding cores arranged symmetrically. Sensors, such as FBGs, are embedded into each of the cores (Figure 1). Such an arrangement allows for the measurement of strain in each core of the fiber at specific axial locations along the fiber. When a multi-core fiber is subjected to bending, the strain imposed in each core relative to one another is used to provide position information (Figure 2).
In the past, shape-sensing measurements using optical fibers estimated bending at sequential points along the fiber, and the resulting measurement had many discontinuities and errors. The combination of these errors resulted in a very poor indication of actual fiber position in three-dimensional space. NASA's patent-pending algorithms and apparatus incorporate not only fiber bending measurements, but fiber twisting measurements as well, to eliminate previous sources of error. The uniqueness of the algorithm is in how the curvature, bend-direction, and twisting information of the fiber are all brought together to obtain a highly accurate 3-D location and shape characterization. The new methods have been demonstrated to significantly improve the accuracy of multi-core fiber optic shape sensors.