Highly Accurate Position Detection and Shape Sensing with Fiber Optics
instrumentation
Highly Accurate Position Detection and Shape Sensing with Fiber Optics (LAR-TOPS-79)
Novel method for determining position, shape, and curvature
Overview
NASA's Langley Research Center has demonstrated a patent pending method and apparatus for determining the position, in three dimensions, of any point on an optical fiber. The new method uses low reflectance Fiber Bragg Grating (FBG) strain sensors in a multi-core fiber to determine how any point
along that fiber is positioned in space. The characteristics of optical fibers and the FBGs vary with curvature, and by sensing the relative change of FBGs in each of three or more fiber cores, the three-dimensional change in position can be determined. By using this method in monitoring applications where optical fibers can be deployed--such as in structures, medical devices, or robotics--precise deflection, end position, and location can be determined in near real time. This innovative position detection method offers 10 times greater positional accuracy than comparable optical techniques.
The Technology
NASA's novel method was developed to more accurately measure the position and shape of optical fibers. Multi-core optical fibers contain multiple light-guiding cores arranged symmetrically. Sensors, such as FBGs, are embedded into each of the cores (Figure 1). Such an arrangement allows for the measurement of strain in each core of the fiber at specific axial locations along the fiber. When a multi-core fiber is subjected to bending, the strain imposed in each core relative to one another is used to provide position information (Figure 2).
In the past, shape-sensing measurements using optical fibers estimated bending at sequential points along the fiber, and the resulting measurement had many discontinuities and errors. The combination of these errors resulted in a very poor indication of actual fiber position in three-dimensional space. NASA's patent-pending algorithms and apparatus incorporate not only fiber bending measurements, but fiber twisting measurements as well, to eliminate previous sources of error. The uniqueness of the algorithm is in how the curvature, bend-direction, and twisting information of the fiber are all brought together to obtain a highly accurate 3-D location and shape characterization. The new methods have been demonstrated to significantly improve the accuracy of multi-core fiber optic shape sensors.
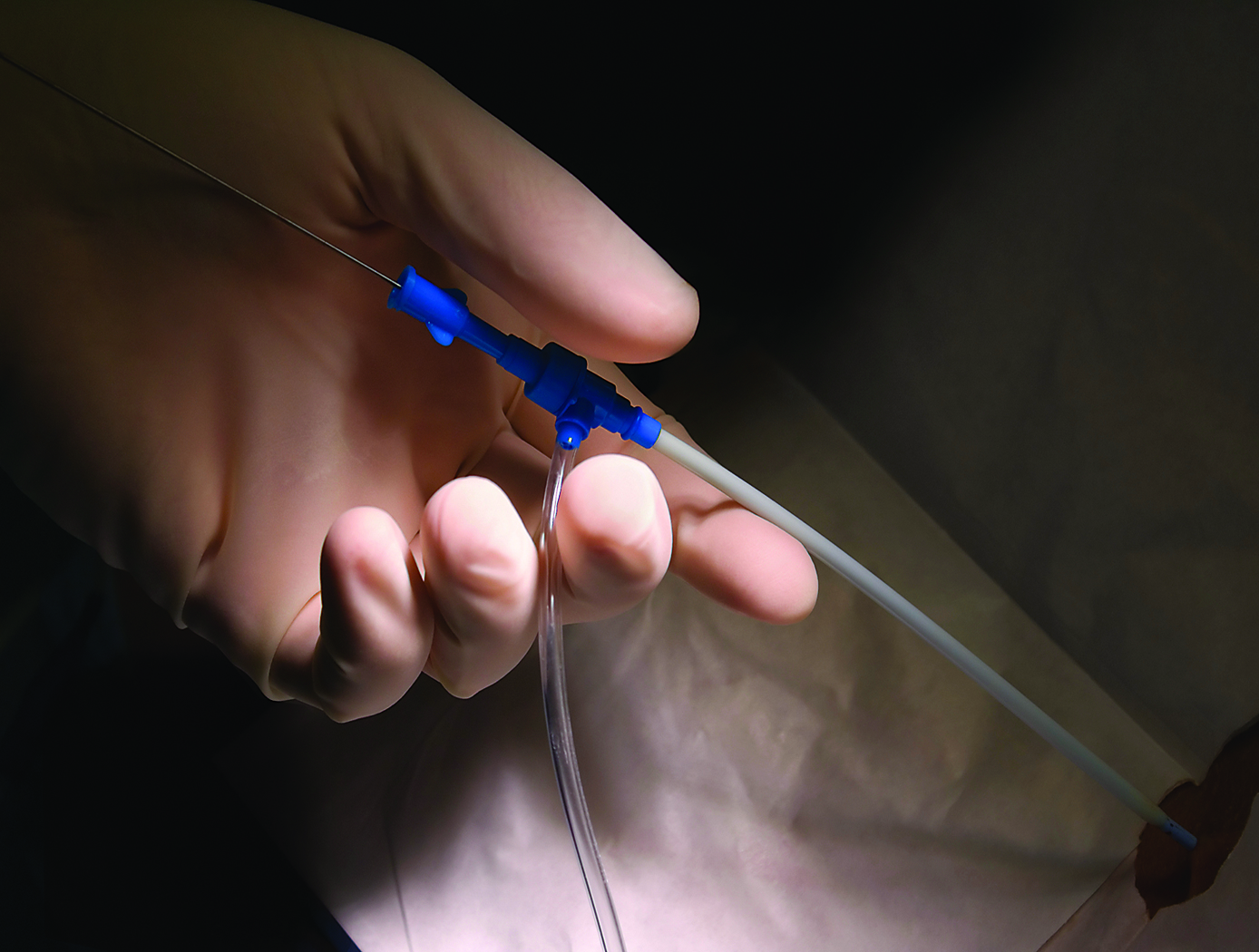
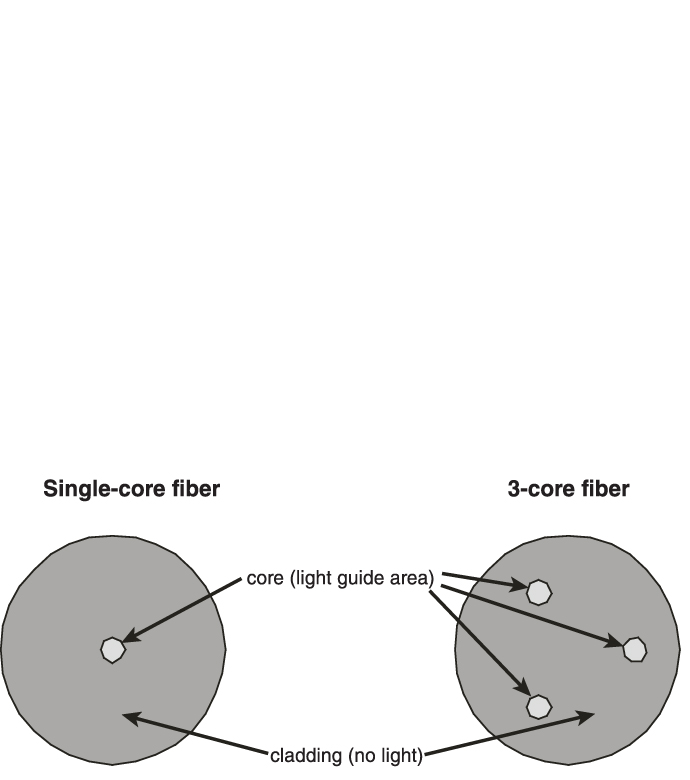
Benefits
- Accuracy is improved for measuring position changes and complex shapes
- Allows position and shape visualization of embedded or hidden fiber optics
- Positional accuracy ( less than 1mm) is 10x better than comparable fiber-based techniques
- Provides high spatial resolution for fibers up to 10 meters in length
- Novel algorithm avoids the accumulation of errors due to fiber twisting, thermal gradients, and other error sources
- Can be extended to other forms of cable
Applications
- Aerospace safety - aircraft and spacecraft integrated vehicle health management systems
- Medical - minimally invasive surgical devices; end-effector tracking
- Cabled remote vehicle - robot position tracking for collapsed buildings or mineshaft search and rescue
- Space exploration - tethered instrument position tracking
Similar Results

Compact, Temperature-Tuned OFDR Laser
Because OFDR-based fiber interrogation systems rely upon interferometry between sensors with respect to a unique reference length, the excitation source (laser) must lase at a single longitudinal mode (SLM). If the excitation source contains multiple modes, the resulting beat frequency becomes a super-position of the multiple frequencies caused by the modes; as a result, the sensor cannot be accurately defined in the Fourier domain. For OFDR systems with high sensing ranges, a continuous wavelength tunable laser must be used to accommodate the resonant wavelength shift of the fiber sensors due to environmental changes. External cavity lasers (ECLs) have been used due to their narrow linewidth and ability to lase at a SLM with no mode-hopping between steps. However, the mechanical complexity associated with tuning, susceptibility to vibration and shock, and high price point leave much to be desired.
To overcome the limitations of OFDR-based FOSS systems resulting from non-ideal excitation sources, NASA has developed a narrow linewidth solid-state laser based on the Distributed Feedback (DFB) laser. NASAs laser is continuously tuned by manipulating the laser cavitys temperature via a thermal-electric cooler feedback system. This continuous wavelength tuning generates a clean clock signal within an auxiliary interferometer, while the laser simultaneously interrogates multiple FBGs to produce a clean sensing interferometer. A Fourier domain spectrograph is used to show the unique frequency (i.e., location) of each FBG.
While NASAs excitation source provides several performance advantages over conventional lasers used in OFDR, it is also highly compact and one eighth the cost of the ECLs traditionally used as excitation sources in OFDR-based systems. The laser has no moving parts, which also substantially improves system reliability.
Originally developed to demonstrate a low-cost interrogator for liquid level sensing in oil tanks, NASAs compact, temperature-tuned OFDR laser can be applied wherever OFDR-based fiber optic sensing is desirable. Additional applications may include temperature distribution sensing, strain sensing, pressure sensing, and more.
NASA AFRC has strong subject matter expertise in fiber optic sensing systems, and has developed several patented technologies that are available for commercial licensing. For more information about the full portfolio of FOSS technologies, visit:
https://technology-afrc.ndc.nasa.gov/featurestory/fiber-optic-sensing

Lightweight Fiber Optic Sensors for Real-Time Monitoring of Structural Health
How It Works
The FOSS technology employs efficient, real-time, data driven algorithms for interpreting strain data. The fiber Bragg grating sensors respond to strain due to stress or pressure on the substrate. The sensors feed these strain measurements into the systems algorithms to determine shape, stress, temperature, pressure, strength, and operational load in real time.
Why It Is Better
Conventional strain gauges are heavy, bulky, spaced at distant intervals (which leads to lower resolution imaging), and unable to provide real-time measurements. Armstrong's system is virtually weightless, and thousands of sensors can be placed at quarter-inch intervals along an optical fiber the size of a human hair. Because these sensors can be placed at such close intervals and in previously inaccessible regions (for example, within bolted joints, embedded in a composite structure), the high-resolution strain measurements are more precise than ever before. The fiber optic sensors are non-intrusive and easy to install—thousands of sensors can be installed in less time than conventional strain sensors and the system is capable of processing information at the unprecedented rate of 100 samples per second. This critical, real-time monitoring capability enables an immediate and informed response in the event of an emergency and allows for precise, controlled monitoring to help avoid such scenarios.
For more information about the full portfolio of FOSS technologies, see DRC-TOPS-37 or visit https://technology-afrc.ndc.nasa.gov/featurestory/fiber-optic-sensing

Sensing Magnetic Fields
This technology is part of Armstrong's portfolio of fiber optic sensing technologies known as FOSS. The innovation leverages Armstrong's cutting edge work in this area, including its patented FBG interrogation system, which allows for a diverse set of engineering measurements in a single compact system. In addition to magnetic field, other measurements include structural shape and buckling modes, external loads, and cryogenic liquid level. The system and measurement technology is commercially available for research applications. In addition to capitalizing on the significant advancements in fiber optic and laser technologies that have been made to support the telecommunications industry, Armstrong has also partnered with UCLA's Active Materials Lab (AML) to tap their expertise in the field of magnetics.
For more information about the full portfolio of FOSS technologies, see DRC-TOPS-37 or visit https://technology-afrc.ndc.nasa.gov/featurestory/fiber-optic-sensing

Flexible Body Control Using Fiber Optic Sensors (FlexFOS)
Aerospace vehicles experience flexible dynamics that have adverse effects on guidance, navigation, and control. Vehicles that include automated control are further affected by flexible modes and structural vibrations. Flexible dynamics become even more critical as demand for larger and more fuel efficient vehicles increases.
Using fiber optic technology to collect both flexible and rigid body information enables increased knowledge (data) of the state of a vehicle, a more robust collection method against weather conditions, and a more cost-effective measurement method. This technology could potentially be applied to aerospace vehicles as well as commercial space structures, commercial aerospace structures, cranes, buildings, or bridges - anything with a large cross sectional ratio.
The RSS is the key to developing a sensor which provides flexible body kinematics. A reference structure must be chosen that minimizes weight impacts while retaining structural integrity. The reference structure material must also be very predictable and repeatable. Once this geometry has been optimized, analyzed, and mapped it is integrated with strain sensors making it a Reference Strain Structure. The RSS must then be integrated into an adaptive structure, which both protects and provides a connection to the desired structure to be measured.
The RSS combined with the properly designed algorithms provides the capability and portability to be installed on any of the aforementioned structures alleviating unique engineering and calibration required for each structure or vehicle. It also provides the capability to employ actuators to counteract the effects of structural vibrations. FlexFOS provides a simple, portable solution adaptable to any structure.

Shape Sensing Innovations Dramatically Improve Structural Design Tools
Armstrong's technologies provide a convenient way to calculate distributed deformed orientation angles—that is, roll, pitch, and yaw—as well as determine the deformed shape of an object in 3D space. Developed to facilitate monitoring and control of flexible aircraft designs when used in conjunction with Armstrong's multi-patented FOSS technology, these new tools improve shape-sensing accuracy for highly deformable structures such as bridges, wind turbines, robotic instruments, and much more. These tools also can be integrated into commercial fiber optic sensing systems.
How It Works
Researchers developed a technology that uses curved displacement transfer functions to determine 3D shape and calculate the operational load of a structure. It works by dividing the structure into multiple small domains, whose junctures match sensing stations, so that data is collected in a piecewise, nonlinear fashion. The innovation calculates structural stiffness (bending and torsion) and operational loads (bending moments, shear loads, and torques) in near real time.
The method tracks rotations and orientation by employing quaternion mathematical operations, a faster process than rotation matrices used in previous shape-sensing algorithms. The result is an algorithm that can track multiple angles—displacement, twist, and rotation—at the same time to enable curvilinear shaping sensing. Armstrong researchers have validated the method on the large-scale passive aeroelastic tailored (PAT) wing.
Why It Is Better
These new technologies advance the ability of fiber optic sensing systems to determine the shape and operational loads of nonlinear flexible surfaces. They can improve the structural integrity of a range of large structures—from buildings and bridges to ocean vessels and aircraft. These innovations reliably provide highly accurate critical information in real time, enabling corrective action to avert disasters.
For more information about the full portfolio of FOSS technologies, see DRC-TOPS-37 or visit https://technology-afrc.ndc.nasa.gov/featurestory/fiber-optic-sensing