Cooperative Service Valve for In-orbit Cooperative Satellite Fueling
robotics automation and control
Cooperative Service Valve for In-orbit Cooperative Satellite Fueling (GSC-TOPS-170)
Enables tele-robotic operated resupplying of media (such as propellants and pressurant) to cooperative satellites.
Overview
NASA Goddard Space Flight Center has developed the Cooperative Service Valve (CSV) to facilitate the resupply of media, such as propellants and pressurants, to satellites. The CSV replaces a standard spacecraft fill and drain valve. Spacecraft outfitted with the CSV enable in-orbit servicing with less risk, lower costs, and a much higher chance of success. The tools used to interface with the CSV, both on the ground and in space, were also designed and tested by NASA.
The CSV architecture and approach is extensible to all space assets that could potentially be fueled/re-fueled on and off the ground, including manned crew vehicles, planetary rovers, and space habitats.
The Technology
The CSV replaces a standard spacecraft Fill and Drain Valve to facilitate cooperative servicing. The CSV offers various advantages over standard service valves: a robotic interface, three individually actuated seals, a self-contained anti-back drive system, and built-in thermal isolation. When mounted to a spacecraft as designed, the CSV transfers all operational and induced robotic loads to the mounting structure. An anti-back drive mechanism prevents the CSV seal mechanism from inadvertent actuation. Alignment marks, thermal isolation, and a mechanical coupling capable of reacting operational and robotic loads optimize the CSV for tele-robotic operations. Unique keying of the mating interface prevents mixing of media where more than one configuration of the CSV is used. Color-coding and labels are also used to prevent operator error.
The CSV has four configurations for different working fluids, all with essentially unchanged geometry and mechanics.
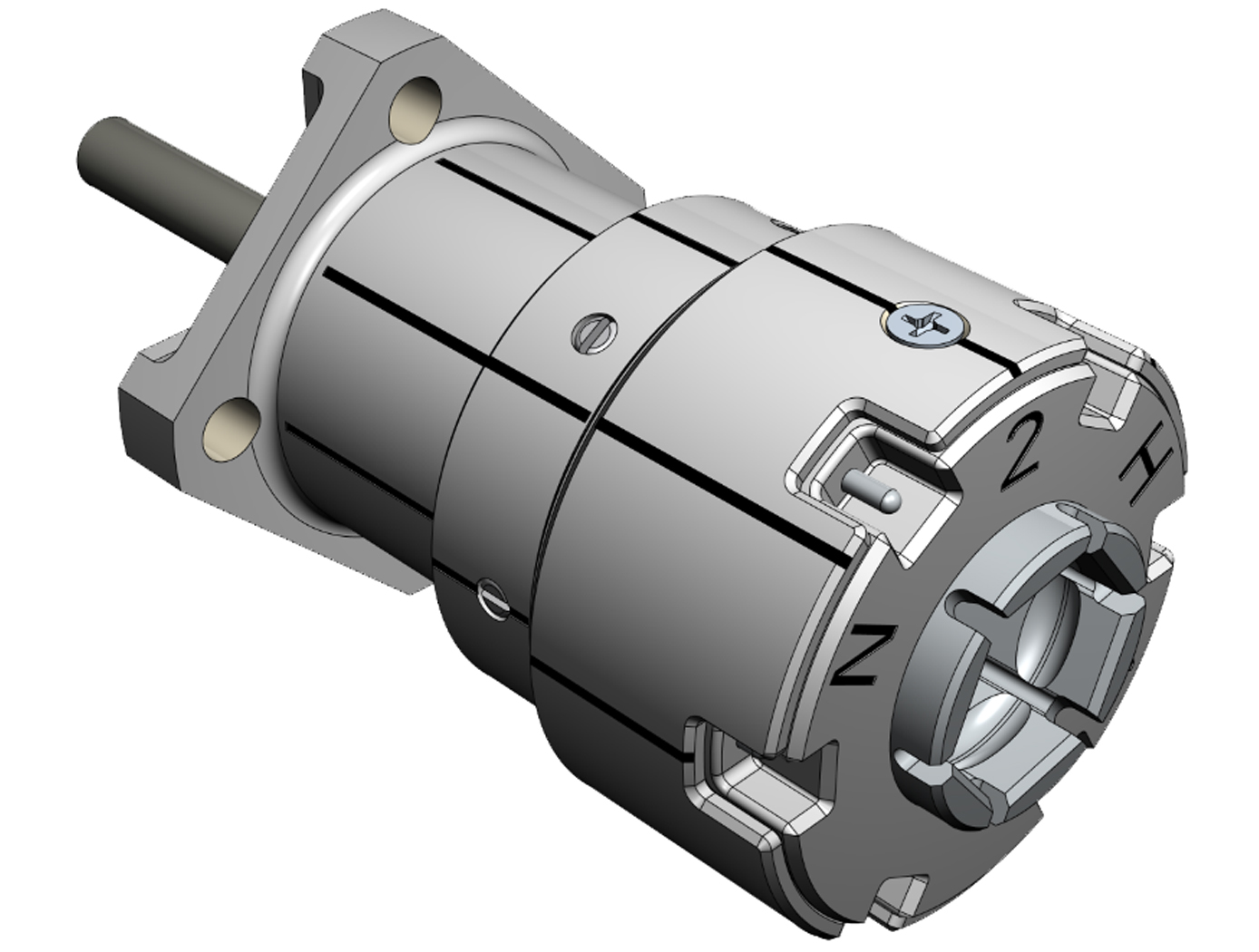
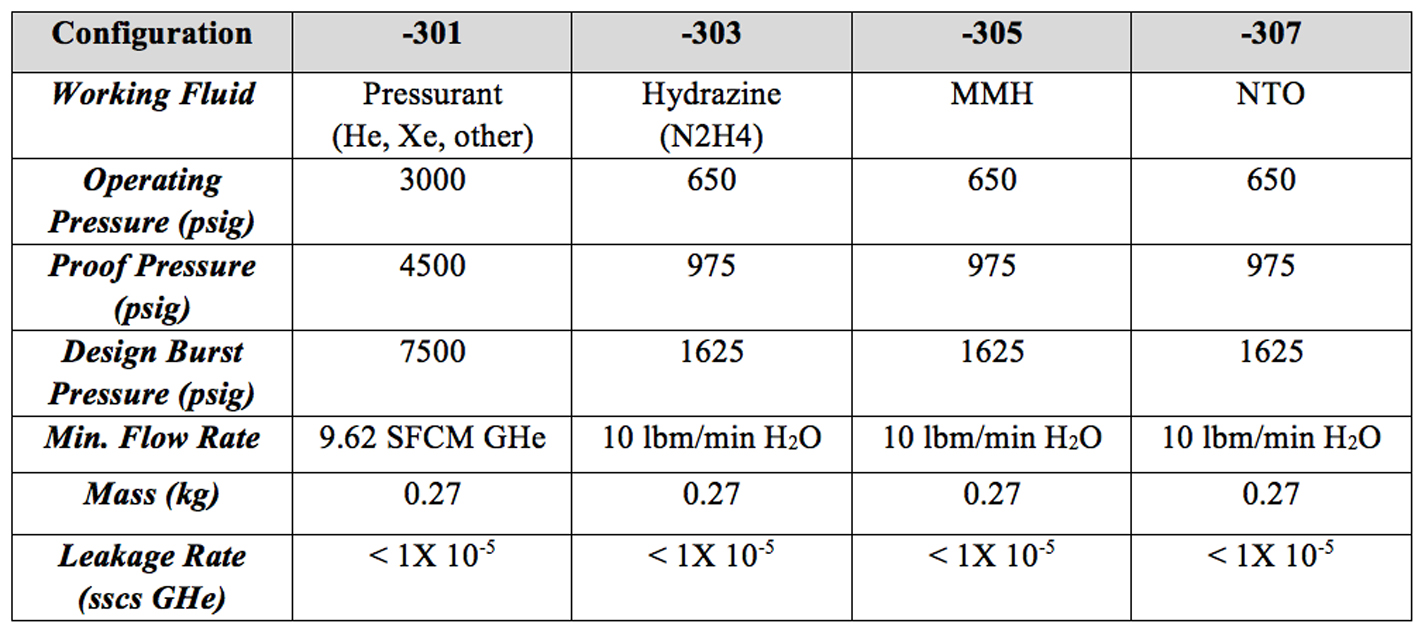
Benefits
- Designed for human and robotic access
- Replaces standard fill and drain valves
- Requires no caps or wires
- Inherent thermal isolation
- Compatible with common spacecraft propellants and pressurants including xenon
- Self-locking against inadvertent actuation
- Similar in size to standard valves
- 2-fault tolerant to leakage when closed, 1-fault tolerant to leakage during fueling
Applications
- Ground and launchpad fueling
- In-space satellite refueling and repair (commercial, government, military)
Similar Results

Miniature Separable Fill & Drain Valve
The Miniature Separable Fill & Drain Valve consists of two halves (ground and flight). The flight half is attached to the vehicle (i.e., CubeSat), and the ground half can be inserted into the vehicle in the same port as the flight half, connecting the two halves together. In normal state, the flight half seals the flow path. When the ground half is connected, the flow path is opened, allowing connected ground support equipment to supply fluid through the valve. The valve is manually operated.
There are redundant seals to eliminate leakage around the valve, including NASA's previously-patented Low-Cost, Long Lasting Valve Seal design (Patent No. 10,197,165; see MFS-TOPS-71 in the Links section of this flyer for more information) on the flight half. This eliminates the need for a swaged assembly process and the additional hardware and equipment that are typically required in conventional, elastomeric valve seat installations. The design also includes a cap for the flight half to ensure there is no leakage in flight configuration.
The Miniature Separable Fill & Drain Valve has been prototyped and provides valuable benefits for CubeSat applications. The valve could also have applications in the industrial processing industry where low flow devices are commonly used. The design is also scalable to larger applications where the removal of the actuation device would be desired.

Low-Cost, Long-Lasting Valve Seal
NASA's technique simplifies the seat installation process by requiring less installation equipment, eliminating the need for unnecessary apparatus such as fasteners and retainers. Multiple seals can be installed simultaneously, saving both time and money.
NASA has tested the long-term performance of a solenoid actuated valve with a seat that was fitted using the new installation technique. The valve was fabricated and tested to determine high-cycle and internal leakage performance for an inductive pulsed plasma thruster (IPPT) application for in-space propulsion. The valve demonstrated the capability to throttle the gas flow rate while maintaining low leakage rates of less than
10-3 standard cubic centimeters per second (sccss) of helium (He) at the beginning of the valves lifetime. The IPPT solenoid actuated valve test successfully reached 1 million cycles with desirable leakage performance, which is beyond traditional solenoid valve applications requirements. Future design iterations can further enhance the valve's life span and performance.
The seat seal installation method is most applicable to small valve instruments that have a small orifice of 0.5 inches or less.

Hypergol Refueling Tool (HRT) and Quick Disconnect (QD) System
The HRT and QD System was designed for satellite Fill and Drain Valves (FDVs), however, the architecture and approach are extensible to all space assets that could potentially be fueled/re-fueled on and off the ground, including but not limited to manned crew vehicles, planetary rovers, and space habitats. In the same vein, the solution is extensible to spacecraft propellants, pressurants, and other media beyond hypergolic fuels. It can be used in the delivery or receipt of media.
The HRT-QD is a separate end adapter onto the HRT; the HRT-QD interfaces with the client FDV. The HRT utilizes two rotary drives to actuate the HRT-QD such that the HRT-QD can affect a seal to the FDV, and open/close the FDV while maintaining this seal. The HRT also has linear drive actuated mechanisms that locks/releases the HRT-QD from the HRT. The HRT is mated to a flexible fuel hose. The fuel hose allows propellant to be transferred from the servicer propellant transfer assembly into the HRT, and further into the HRT-QD and into the client spacecraft via the FDV. This system is mated to, and actuated, by Advanced Tool Drive System 2.0.

Debris-Tolerant Valve
NASA's Debris-Tolerant Valve is designed for use in machines/environments with a large quantity of airborne dust or other contaminants. Valves subjected to airborne contaminants tend to have limited lifetime due to damaged seals, bearings, and other internal components. The Debris-Tolerant Valve design addresses this problem with four core improvements over existing commercial valves that are typically used in dusty or debris-laden processes: (1) a new cylinder design that substantially decreases dust collection within the valve; (2) a rotational valve design that minimizes grinding and packing experienced by the standard ball valve; (3) the use of elastomeric seals rather than the Teflon-based seals used in existing valves which are prone to scratching and subsequent leakage; and (4) a bleed port for fluid intake that allows pressure to build slowly in the valve and eliminates the stirring of dust commonly caused by rapid inflow of air in existing valves.
The operational lifetime of NASA's Debris-Tolerant Valve exceeds the lifetime of a standard commercial valve and the existing selector valve used on the ISS by 12X and 6X, respectively. NASA's valve design has fewer parts than existing valves and could be disassembled without tools, enabling easier servicing and maintenance. The Debris-Tolerant Valve is only about one-seventh (1/7) the cost of the existing ISS selector valve.
Feedthrough for Severe Environments and Temperatures
Space and ground launch support related hardware often operate under extreme pressure, temperature, and corrosive conditions. When dealing with this type of equipment, it is frequently necessary to run wiring, tubes, or fibers through a barrier separating one process from another with one or both operating in extreme environments. Feedthroughs used to route the wiring, tubes, or fibers through these barriers must meet stringent sealing and leak tightness requirements.
This affordable NASA feedthrough meets or exceeds all sealing and leak requirements utilizing easy-to-assemble commercial-off-the-shelf hardware with no special tooling. The feedthrough is a fully reconfigurable design; however, it can also be produced as a permanent device. Thermal cycling and helium mass spectrometer leak testing under extreme conditions of full cryogenic temperatures and high vacuum have proven the sealing capability of this feedthrough with or without potting (epoxy fill) on the ends. Packing material disks used in the construction of the device can be replaced as needed for rebuilding a given feedthrough for another job or a different set of feeds if potting is not used for the original feedthrough build. (Potting on one or both sides of the sleeve provides double or triple leak sealing protection). Variable Compression Ratio (VCR) connectors were adapted for the pressure seal on the feedthrough; however, any commercial connector can be similarly adapted. The design can easily be scaled up to larger (2" diameter) and even very large (12" or more) sizes.