Free-Form Fabrication Using Electrically Conductive Filaments
manufacturing
Free-Form Fabrication Using Electrically Conductive Filaments (LAR-TOPS-252)
A method for the free-form fabrication of articles out of electrically conductive filaments using localized heating
Overview
The use of multifunctional composites such as mechanically reinforced, electrically and thermally conductive parts is of interest in a range of application areas. Especially interesting and important is where tailorability of function is achieved by strategic placement of materials with unique functionality in locations that may not be accessible by conventional manufacturing techniques. Examples include embedded conductive paths interspersed in components to act as sensing elements, or as heaters, or to carry current to power to permit other components to be plugged in. The processing of these materials requires adhesion of filaments to each other, as well as to a substrate.
The Technology
Free form fabrication of articles often requires the application of heat to melt the fabrication material feedstock, and controlled cooling to ensure that once the material is put into place, the fabricated structure does not suffer from distortion. Investigators at LaRC have developed a simple method to apply localized heat, by using an electrically conductive nozzle and a conductive plate as the electrodes for electrically conductive filaments. This method is intended to be used for laying down electrically conductive filaments in a fast, accurate and controlled manner with localized heat.
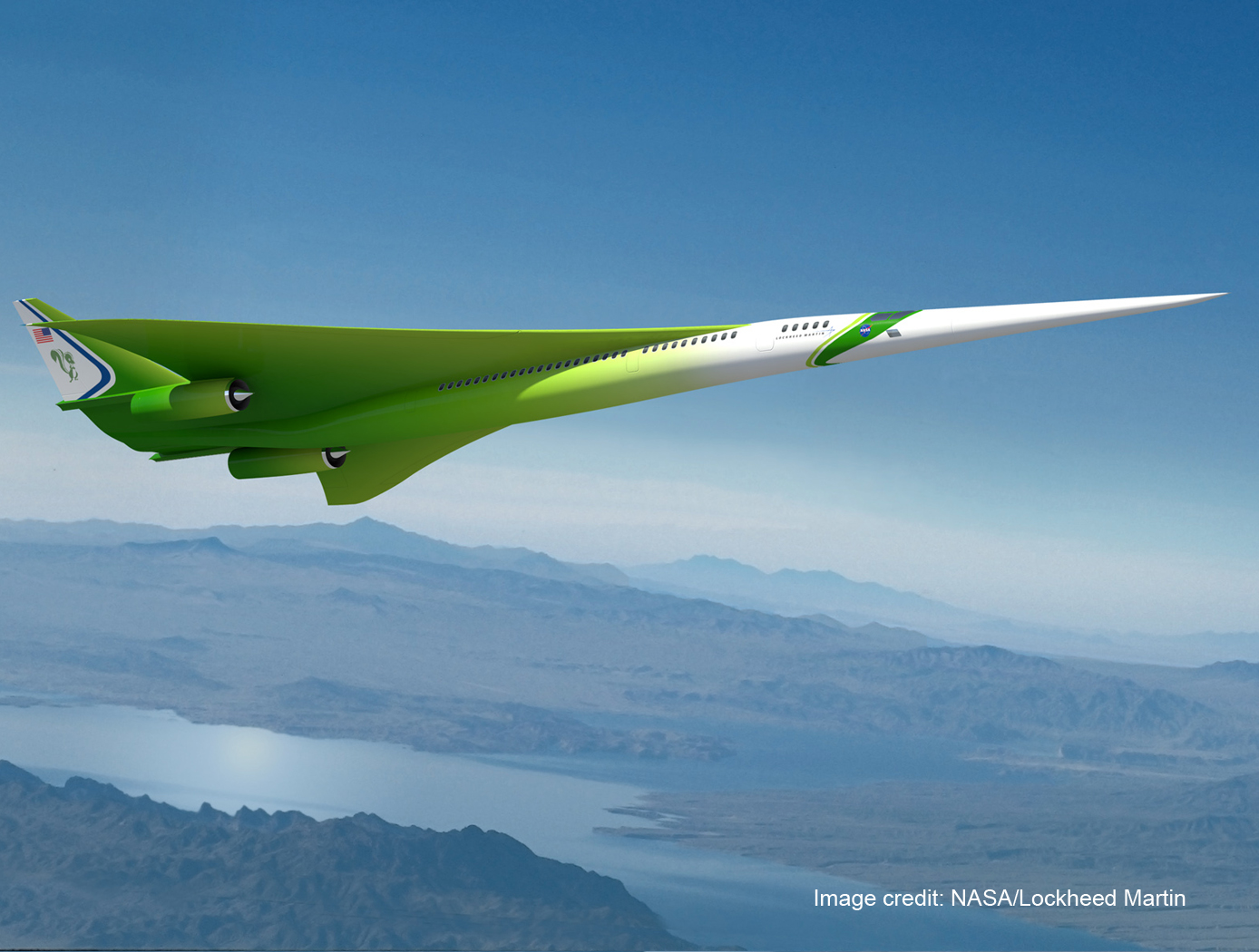
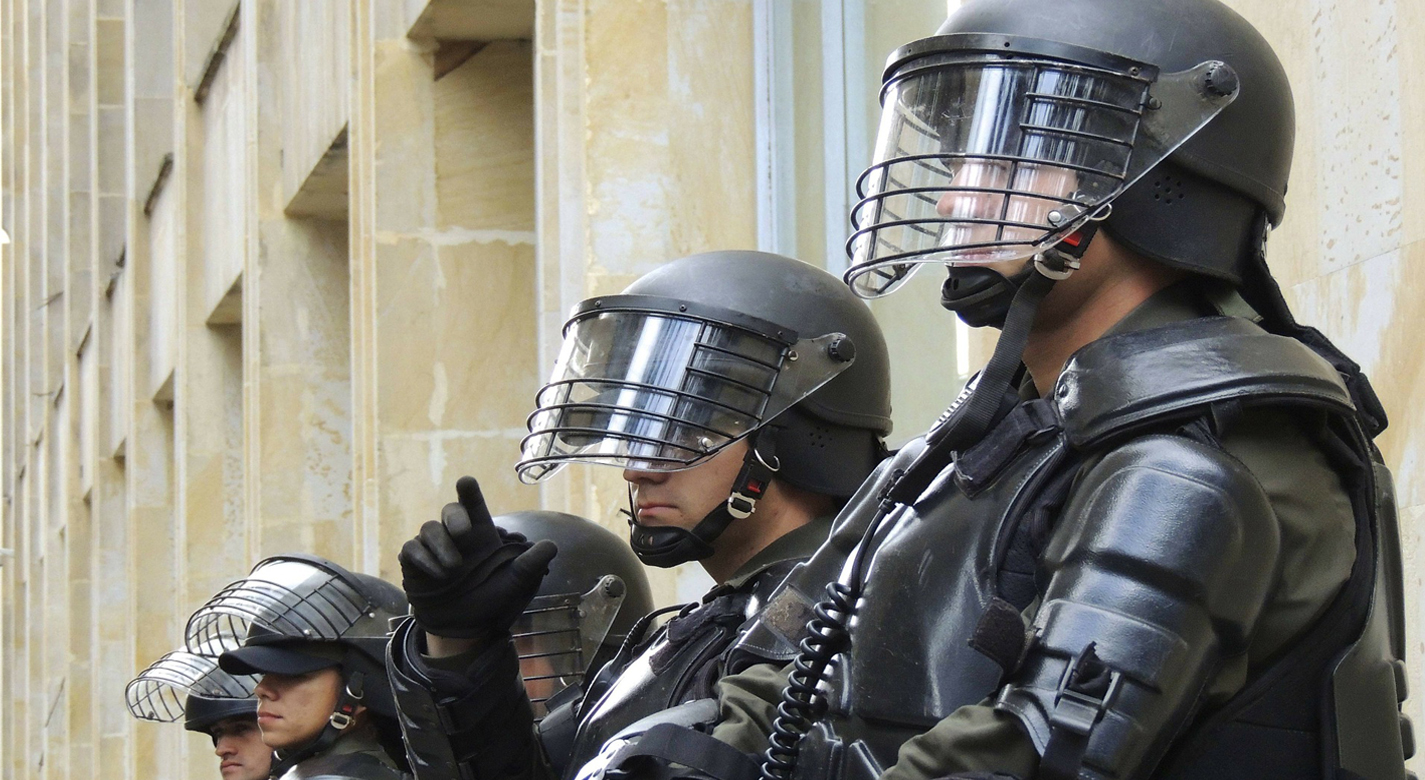
Benefits
- Confirms the viability of using a-C to form stable connections between BNNT using electron beam irradiation as a method of structural repair
- Mechanical properties of a-C joint on BNNT structures are comparable with those of currently available structural fibers such as CNT yarn, carbon fibers, and carbon fiber reinforced composites
- a-C welding represents an approach for transferring load between the tubes for future structural material designs
Applications
- Light-weight structural material for aerospace vehicles including high altitude and space exploration
- Neutron radiation shielding materials -- automobile, solar energy, cosmetics, clothing, blankets, helmets
- Military applications -- light weight armor
- Lightning protection for aerospace vehicles
- Flexible structural materials
- Highly conductive flexible materials for electrodes and supercapacitors
- Thermally conductive material applications
- Catalysts embedded in flexible membranes
Similar Results

Advanced Materials for Electronics Insulation
Many researchers have attempted to use polymer-ceramic composites to improve the thermal and dielectric performance of polymer insulation for high voltage, high temperature electronics. However, using composite materials has been challenging due to manufacturing issues like incomplete mixing, inhomogeneous properties, and void formation. Here, NASA has developed a method of preparing and extruding polymer-ceramic composites that results in high-quality, flexible composite ribbons.
To achieve this, pellets of a thermoplastic (e.g., polyphenylsulfone or PPSU) are coated with an additive then mixed with particles of a ceramic (e.g., boron nitride or BN) as shown in the image below. After mixing the coated polymer with the ceramic particles, the blended material was processed into ribbons or films by twin-screw extrusion. The resulting ribbons are highly flexible, well-mixed, and void free, enabled by the coated additive and by using a particle mixture of micronized BN and nanoparticles of hexagonal BN (hBN).
The polymer-ceramic composite showed tunable dielectric and thermal properties depending on the exact processing method and composite makeup. Compared to the base polymer material, the composite ribbons showed comparable or improved dielectric properties and enhanced thermal conductivity, allowing the composite to be used as electrical insulation in high-power, high-temperature conditions.
The related patent is now available to license. Please note that NASA does not manufacturer products itself for commercial sale.

Highly Thermal Conductive Polymeric Composites
There has been much interest in developing polymeric nanocomposites with ultrahigh thermal conductivities, such as with exfoliated graphite or with carbon nanotubes. These materials exhibit thermal conductivity of 3,000 W/mK measured experimentally and up to 6,600 W/mK predicted from theoretical calculations. However, when added to polymers, the expected thermal conductivity enhancement is not realized due to poor interfacial thermal transfer.
This technology is a method of forming carbon-based fillers to be incorporated into highly thermal conductive nanocomposite materials. Formation methods include treatment of an expanded graphite with an alcohol/water mixture followed by further exfoliation of the graphite to form extremely thin carbon nanosheets that are on the order of between about 2 and about 10 nanometers in thickness. The carbon nanosheets can be functionalized and incorporated as fillers in polymer nanocomposites with extremely high thermal conductivities.

Conductive Polymer/Carbon Nanotube Structural Materials and Methods for Making Same
Carbon nanotubes (CNTs) show promise for multifunctional materials for a range of applications due to their outstanding combination of mechanical, electrical and thermal properties. However, these promising mechanical properties have not translated well to CNT nanocomposites fabricated by conventional methods due to the weak load transfer between tubes or tube bundles.
In this invention, the carbon nanotube forms such as sheets and yarns were modified by in-situ polymerization with polyaniline, a -conjugated conductive polymer. The resulting CNT nanocomposites were subsequently post-processed to improve mechanical properties by hot pressing and carbonization. A significant improvement of mechanical properties of the polyaniline/carbon nanotube nanocomposites was achieved through a combination of stretching, polymerization, hot pressing, and carbonization.

Conductive Carbon Fiber Polymer Composite
The new composite developed by NASA incorporates PGS and CNTs to enhance its thermal conductivity while preserving the mechanical properties of the underlying carbon fiber polymer composite. NASA has also improved the composite manufacturing process to ensure better thermal conductivity not only on the surface, but also through the thickness of the material. This was achieved by adding perforations that enable the additives to spread through the composite.
The process for developing this innovative, highly thermally conductive hybrid carbon fiber polymer composite involves several steps. Firstly, a CNT-doped polymer resin is prepared to improve the matrix's thermal conductivity, which is then infused into a carbon fiber fabric. Secondly, PGS is treated to enhance its mechanical interface with the composite. Thirdly, perforation is done on the pyrolytic graphite sheet to improve the thermal conductivity through the thickness of the material by allowing CNT-doped resin to flow and better interlaminar mechanical strength. Finally, the layup of PGS and CNT-CF polymer is optimized.
Initial testing of the composite has shown significant increases in thermal conductivity compared to typical carbon fiber composites, with a more than tenfold increase. The composite also has higher thermal conductivity than aluminum alloys, with more than twice the thermal conductivity of the Aluminum 6061 typically used in the aerospace industry. For this new material, NASA has completed a proof-of-concept demonstration and work continues to use the material in a heat exchanger system and further characterize the properties including longevity and radiation impact analysis.

Vertically Aligned Carbon Nanotubes
Formation of the inventive polymer composite matrix begins by growing carbon nanotubes directly on a veil substrate. The carbon nanotubes are grown from both sides of a non woven carbon fiber mat. The carbon nanotubes can be single or multi walled and can be grown to predetermined lengths. The veiled substrate is positioned between carbon fiber/ polymer prepreg layers such that the carbon nanotubes protrude into the reinforcement layers. The polymer composite matrix formed following curing of the resin exhibits improved interlaminar strength, fracture toughness and impact resistance. Because of the thinness of the veil layer, electricity can pass from conductive carbon nanotubes on one side of the veil to conductive carbon nanotubes on the other side of the veil. Electricity can also pass between two veils intercalated into the same reinforcement layer when the length of the nanotubes is sufficiently long enough to provide overlap within the reinforcement layers.