Fabrication of Fiber-Metal Laminates with Non-Autoclave Processes
manufacturing
Fabrication of Fiber-Metal Laminates with Non-Autoclave Processes (LAR-TOPS-6)
VARTM-based technique enables larger, less expensive hybrid laminate parts
Overview
NASAs Langley Research Center developed a new technique that enables the preparation of metal/composite hybrid laminates, also known as fiber-metal laminates (FML), through a one-step processing method. Currently FMLs are prepared by a compression process using a press or autoclave with metallic layers sandwiched between layers of glass or graphite prepreg (preimpregnated fibers with a matrix resin). NASAs process essentially eliminates the need to produce prepreg prior to the production of a hybrid laminate. It also allows the production of large, net shape structures that were previously not possible with autoclave or press technologies due to size constraints. This infiltration and infusion process can be accomplished using pressure (resin transfer molding [RTM]), or a vacuum induced pressure differential (vacuum assisted resin transfer molding [VARTM]).
The Technology
The FMLs resulting from the NASA process have similar properties to traditionally produced metal/composite hybrid laminates including, as compared to either the composite or metal only structures, improved load carrying capability, lighter weight, improved stiffness, improved impact resistance and damage tolerance, and improved permeation resistance. The NASA process can be applied to various FML types, including GLARE (glass, aluminum, epoxy), and TIGR (titanium, graphite). Typical manufacturing processes are costly and complex shapes are hard to produce, whereby the NASA process enables use of these kinds of laminates without an autoclave or press, thus increasing the size that can be produced and decreasing the cost.
The resin pathways in the foils enable connection between the plies that can improve the interlaminar strength of the final part. Functionally the NASA process creates resin columns in the transverse direction of the plies. NASA is working to optimize the final properties by varying the size and distribution of the pathways.
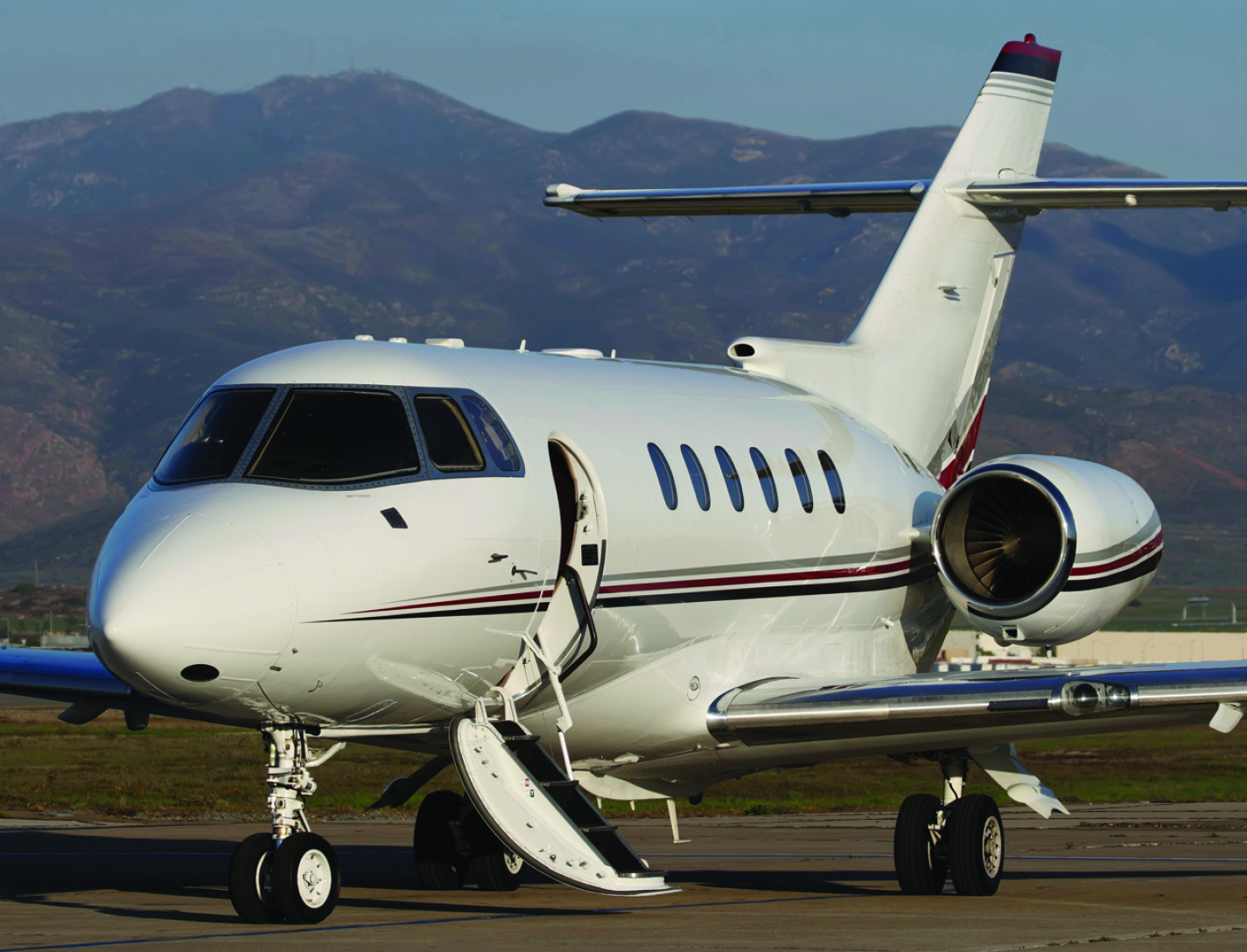
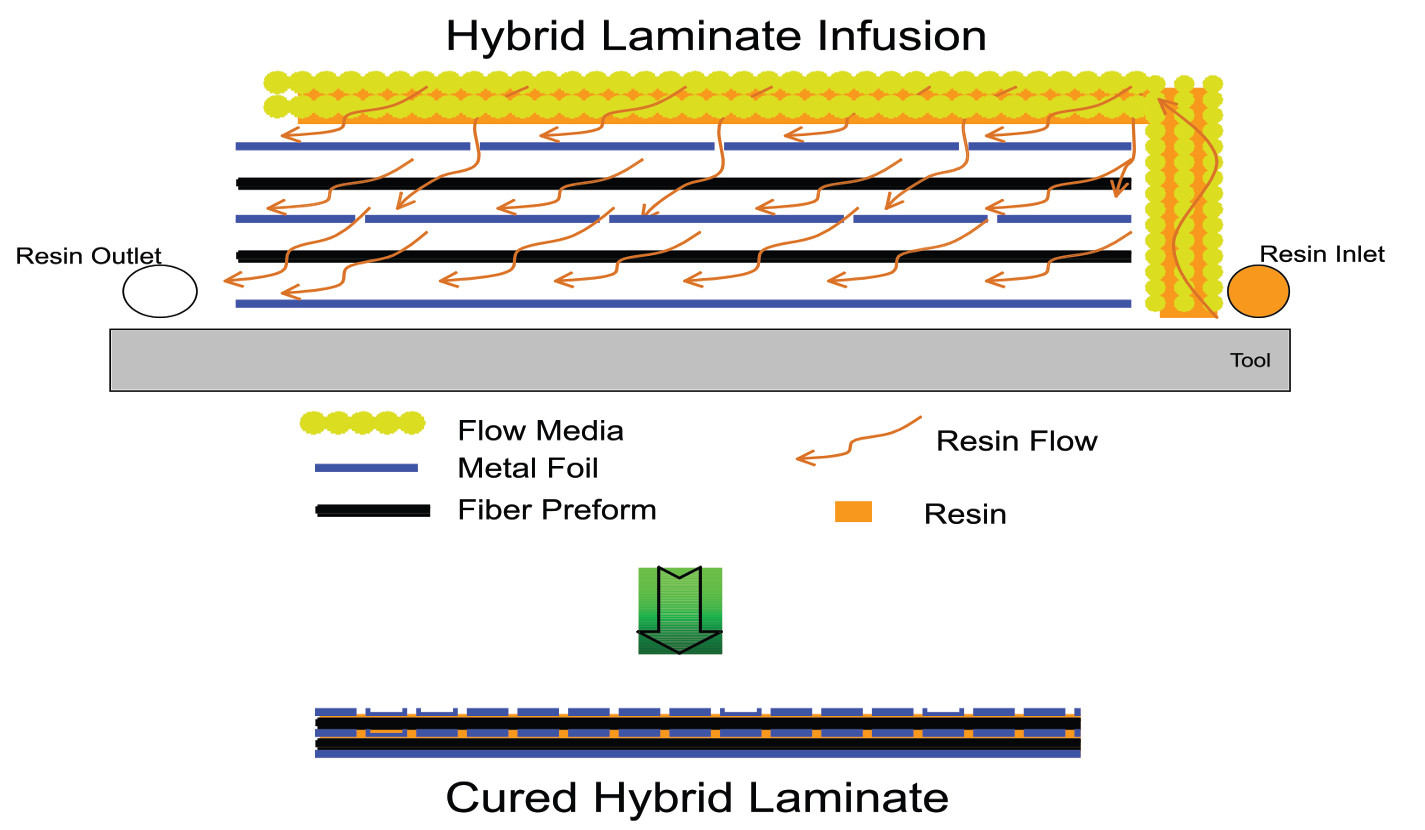
Benefits
- Part sizes can be larger than those possible from autoclave or press processing
- Eliminates the need for complex tooling (as needed in autoclave or press processing) and thus is less expensive
- Produces high quality, low void content hybrid laminates with high fiber volumes without need for previously prepared prepreg
- Requires no autoclaves or presses
- Can be used to produce curved laminate structures and complex shapes
Applications
- The technology offers wide-ranging market applications, including:
- Aeronautics and aerospace structures - e.g., fuselage, floors, liners, cargo containers
- Pressure vessels and storage tanks
- Automotive structures
- Ballistic protection - explosives, bomb containment
Tags:
|
Similar Results

Plasma Deposition of Metal in Composite Panels
NASA's plasma-deposition process provides the ability to tailor various properties while designing functional parts by selecting specific materials and processing parameters to meet the end goal. Specifically, the plasma process deposits metal particles that are heated as they travel axially at low velocity through an inert gas plasma. The accelerated powder particles become molten, strike the substrate fabric (uniaxial, biaxial, and multiaxial) and rapidly solidify, imparting very little heat to the substrate while forming a metal-to-fiber bond, as well as a metal-to-metal bond. The resulting metal-coated fabric is porous, so the polymer matrix can pass through the product precursor during the infusion process. The amount of metal deposited can be
controlled, as can the number of plies of fabric that are ultimately stacked to produce the preform for the polymer matrix infusion process. A variety of infusion processes can be utilized to prepare the FML, including resin transfer molding (RTM), resin film infusion (RFI), and vacuum-assisted resin transfer molding (VARTM). The tailorable aspect of the process allows for specific product design. By varying the combination of metal particle, fiber, fabric type, metal layer thickness, fabric direction, number of layers, polymer matrix resin, infusion process, and cure conditions, the characteristics of the final part can meet the needs of various applications.

Advanced Isothermally Produced Next-Gen Composites
Next generation aircraft are anticipated to be largely made with composite components, requiring significant increases in manufacturing rates of composites to meet the demand for a new fleet of aircraft. The higher rate manufacturing will require multiple advances, including rapid curing and lower processing temperatures. These requirements can be enabled by new processing methods such as isothermal rapidly cured composite parts.
NASA has developed materials and methods that meet those stringent requirements for high-rate manufacturing. The innovators have demonstrated at least two families of new resin formulations that meet the expected high-rate manufacturing needs. These new formulations have been engineered to be infused and cured at the same (i.e., isothermal) temperature, below that of commercially available materials. The materials can then be removed from the mold while still hot without distorting the shape, thereby reducing the processing times by eliminating the need for cooling to occur in the mold. After a post-cure process - which takes 4 hours or less and can be performed in batches - the mechanical properties of NASA's next-gen composites.
The related patent is now available to license. Please note that NASA does not manufacturer products itself for commercial sale.

Fiber-Metal Laminate Manufacturing Technique
Fiber-Metal Laminates (FMLs) are composite materials that consist of conventional fiber reinforced plastics with the addition of a metal component, typically a foil or mesh layer(s). The metal component offers the advantage of incorporating metal-like properties to the composite construction. While a range of potential advantages and applications have been discussed for FMLs, the primary application to date has been for aircraft structures, with one potential advantage being the lightning strike protection (LSP) offered by the improved electrical conductivity. As aircraft construction has moved to composite structures, there has been an increasing need for such conductive composites. Similarly, with increasing use of composites for other large structures, e.g. wind turbines, there are an increasing number of potential applications for lightning strike protection materials. Other advantages of FML are improved impact and fire resistance.
This innovation provides a method for making FML materials that incorporate nanotube reinforcement. The method involves the use of RF plasma spray to directly form and deposit nanotube materials onto fibers/fabrics, which can then be manufactured into composite structures by infiltrating the fiber with resin, and consolidating the structure via autoclave processing or via the use Vacuum Assisted Resin Transfer Molding (VARTM) composite manufacturing methods. Nanotubes incorporated into the structure in this manner can be of several types, for example boron nitride or carbon nanotubes. The objective of this innovation is to incorporate the nanotube materials in the FML in order to improve the mechanical properties.

Automated Tow/Tape Placement System
This NASA invention enables several benefits that mitigate limitations associated with conventional ATP systems, including the following: (1) avoids obtuse head rotation or cross-tool translation when laying adjunct tape plies, (2) simultaneously places tape on both sides of a part via two robots, (3) eliminates external anchoring frame requirements, and (4) translates parts during build while also translating the applicator head. The ability to perform simultaneous layup on opposite sides of the component, as well as reduction of head rotation reversal during bidirectional tape layup, offers increased layup speed. The invention offers increased placement accuracy as a result of reduced movement between tape layup operations and the eliminated need for an anchoring frame (facilitated by simultaneous pressure extrusion of prepreg by the two robots).
NASA’s automated tow/tape placement system has two key unique features: the use of two opposed ATP cars to enable a tool-less process, and an on-the-fly reversal tape/tow laydown tooling head. The system uses two opposing (i.e., underside-to-underside) ATP cars, and can build parts vertically, horizontally, or at any other angle, depending on the workspace available. The ATP die wheels can be reversed or turned to draw the composite back and forth at different angles to create a layer-by-layer composite structure. Both cars can dispense TPC tape – thus, either car can function as an opposing tool surface while the other performs prepreg lay-up. For structures that do not vary in thickness, both cars can lay tape at the same time – doubling layup speed. Current ATP robots must rotate the large tooling head, or traverse panels without layering tape to achieve bidirectional layup, where each additional movement introduces alignment error. To increase layup rate while simultaneously minimizing misalignment, NASA’s system incorporates an on-the-fly reversal tape/tow laydown tooling head to enable efficient bidirectional layup.

Damage Simulation Tool For Composite Laminates
The simulation combines existing fracture mechanics based damage propagation techniques with a discrete approach to modeling discontinuities in finite elements. Additionally, the use of an advanced laminate theory recovers deformation and stress information that would normally require a high fidelity model.
To accomplish this, the same theoretic and analytical concepts that a high fidelity numerical simulation tool utilizes for laminate damage simulation are placed in the context of a low fidelity finite element. In taking this approach, a laminate can be modeled as a single layer low fidelity shell mesh that has the ability to locally increase fidelity and represent a delamination based damage process but only if it is determined that one should occur.
The numerical simulation tool's performance has been validated against numerical benchmarks as well as experimental data.