Thermal Management for Aircraft Propulsion Systems
power generation and storage
Thermal Management for Aircraft Propulsion Systems (LEW-TOPS-110)
Novel thermoacoustic engine uses waste heat to cool and power components
Overview
Innovators at NASA's Glenn Research Center have developed a lightweight, reliable thermal management system, for both ambient and cryogenic propulsion systems, that increases overall fuel efficiency from 40 to 60 percent. Conventional aircraft propulsion systems struggle to keep high-powered electric motors and electronics cool without resorting to extra mass and complexity that negate the benefits of electric propulsion in aircraft. Glenn's thermal management system uses the normally wasted energy from turbofan propulsion to cool electronics and power equipment. The waste heat produces a high-intensity acoustic wave, created from the temperature gradient between the hot and cold heat exchangers. This acoustic wave energy propagates through thermoacoustic power tubes, where it can be used for component cooling or converted to electric power via a linear alternator. Glenn's system can provide highly efficient electric power to aircraft components while cooling the aircraft's propulsion system without added mass and complexity.
The Technology
Aircraft thermal management systems typically comprise over half the mass associated with full electric power propulsion systems, with significant negative impact on fuel efficiency. In addition, the traditional method of using jet fuel to cool aircraft generators does not provide enough cooling for use in flight-weight cryogenic systems. Lastly, the much higher bus voltages required for flight-weight systems (4.5 kV vs. 270 V) introduce additional spark-ignition hazards associated with alternative cryogenic cooling fuels, including liquid methane or liquid hydrogen. The Glenn flight-weight thermal management system addresses all of these problems by using the considerable waste heat energy from turbogenerators to create a pressure wave thermoacoustically. This wave can then be delivered quietly and efficiently via routed ductwork to hollow pulse-tube coolers located near any component in the aircraft that requires cooling. The tubes can be fabricated in any length and can be curved to fit any space. This technology also allows waste heat energy to be used in at least four ways: 1) the waste heat energy can drive a thermoacoustics-based ambient or cryogenic heat pump; 2) it can be channeled directly into a thermoacoustic engine that generates power; 3) it can convectively preheat the fuel/ or air supplied to the aircraft engine; 4) it can drive a pulse-tube generator providing power. The delivered thermoacoustic power can provide cabin cooling as well as ambient/cryogenic cooling of converter, cables, and motors. In addition, this power can be converted to local electric power through the use of a transducer (such as a linear alternator) or piezoelectrics. Further, the efficient thermal management system enables the size, mass, and resultant cost of the radiating fins to be reduced. Glenn's system offers an efficient method of cooling next-generation flight-weight electric aircraft with significant benefits for fuel efficiency and safety.

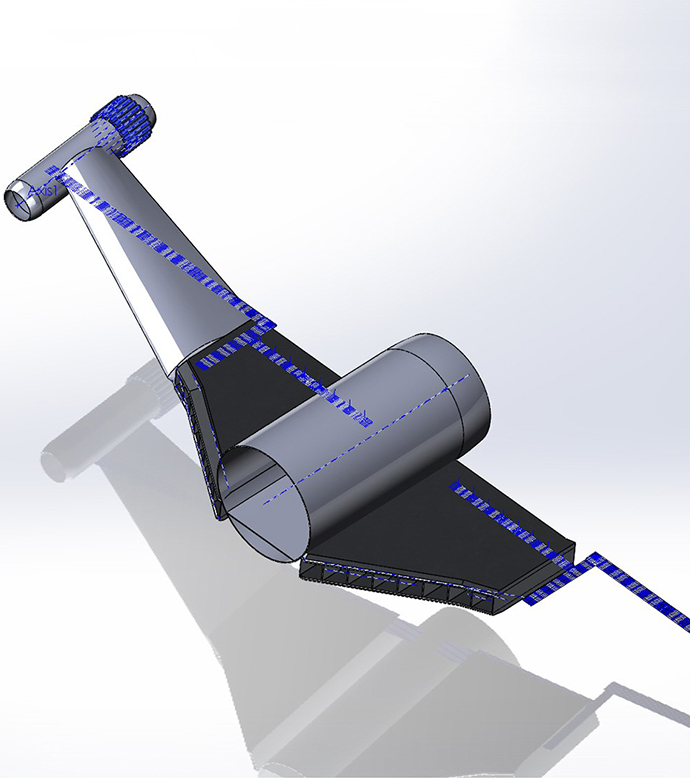
Benefits
- Compact: Lightweight design is easily integrated into aircraft
- Efficient: Overall system efficiency increases from 40% to 60%
- Safe: The system does not require cryogenic cooling fuels, which are highly flammable and explosive
- Reliable: This technology has no hot moving parts, plumbing, or wiring and is therefore virtually maintenance-free
- Low cost: The system achieves significant savings in fuel, material, and maintenance costs
Applications
- Aerospace (e.g., electric aircraft, aircraft auxiliary power units, aircraft thermal management)
- Unmanned vehicles
- Satellites
Technology Details
power generation and storage
LEW-TOPS-110
LEW-19353-1
LEW-19353-2
Similar Results

Stirling Thermoacoustic Power Converter and Magnetostrictive Alternator
Glenn's thermoacoustic power converter reshapes the conventional Stirling engine from a toroidal shape into a straight colinear arrangement. Instead of relying on failure-prone mechanical inertance and compliance tubes, this design achieves acoustical resonance by using electronic components. In a typical Stirling engine, the acoustical wave travels around a toroid and reflects back, forming a standing wave. In Glenn's device, by contrast, the wave instead travels in a straight plane where a transducer receives the acoustical wave and electrical components modulate the signal. A second transducer on the diametrically opposed side reintroduces the acoustic wave with the correct phasing to achieve amplification and resonance. Glenn's design allows the transducers to operate at high frequency while presenting a mass rather than stiffness impedance.
Glenn's magnetostrictive alternator uses stacked magnetostrictive materials under a biased magnetic and stress-induced compression. The acoustic energy from the engine travels through an impedance-matching layer (which can be formed from aerogel materials) that is physically connected to the magnetostrictive mass. Compression bolts keep the structure under compressive strain, allowing for the micron-scale compression of the magnetostrictive material and eliminating the need for bearings. The alternating compression and expansion of the magnetostrictive material creates an alternating magnetic field that then induces an electric current in a coil wound around the stack. This alternator produces electrical power from the acoustic pressure wave and, when the resonant frequency is tuned to match the engine, can replace the linear alternator to great effect.

Double-Acting Extremely Light Thermo-Acoustic (DELTA) Convertor
Glenn's innovative DELTA convertor uses a double-action push/pull piston, in which an acoustic wave - or sound wave generated by heat - pushes both ends of a single piston. When sound waves are propagated down a narrow tube, they transfer energy along the tube. Conversely, when a heat gradient is introduced, it will generate sound waves that will cause the push/pull piston to oscillate. Using thermoacoustics to oscillate the push/pull piston simplifies engine operation by eliminating moving parts such as hot displacers and heavy springs. The double-action piston is contained by multiple thermo-acoustic stages in series that form a delta-shaped triangular loop. One side of the piston creates an acoustic wave while simultaneously receiving acoustic power on the opposing side, enabling increased power on the single piston as compared to a single-action piston. The simple design consists of a helium-filled tube, heat exchangers, regenerators, and a single, non-contact, oscillating piston. Operating at 400Hz, this convertor can produce four times more power than conventional engines operating at 100Hz, with no hot moving parts, maintenance, lubrication, or electric feedback required. At this higher frequency, the output current is minimized and the specific power is maximized enabling an order of magnitude increase in specific power over conventional engines. Glenn's novel DELTA convertor offers this significantly increased specific power in a compact, lightweight, maintenance-free package that has considerable commercial potential.

New Concepts in Film Cooling for Turbine Blades
In one of NASA Glenn's innovations, a shaped recess can be formed on a surface associated with fluid flow. Often V-shaped, this shaped recess can be configured to create or induce fluid effects, temperature effects, or shedding effects. For example, the shaped recess can be paired (upstream or downstream) with a cooling channel. The configuration of the shaped recess can mitigate the lift-off or separation of the cooling jets that are produced by the cooling channels, thus keeping the cooling jets trained on turbine blades and enhancing the effectiveness of the film-cooling process. The second innovation produced to improve film cooling addresses problems that occur when high-blowing ratios, such as those that occur during transient operation, threaten to diminish cooling effectiveness by creating jet detachment. To keep the cooling jet attached to the turbine blade, and also to spread the jet in the spanwise direction, NASA Glenn inventors have successfully used cooling holes that reduce loss by blowing in the upstream direction. In addition, fences may be used upstream of the holes to bend the cooling flow back toward the downstream direction to further reduce mixing losses. These two innovations represent a significant leap forward in making film cooling for turbine blades, and therefore the operation of turbine engines, more efficient.

High-Voltage Power System for Hybrid Electric Aircraft Propulsion
Glenn's novel system supports the NASA Aeronautics Research Mission Directorate (ARMD) strategic plan to leverage advancements in technologies over the next 25 years and beyond, leading to new aircraft configurations with enhanced performance, improved energy efficiency, and reduced CO2 emissions. The electric system is a multi-megawatt micro-grid that converts mechanical energy to electric via generators, and electric energy to mechanical via motor-driven fans. This innovation would use the variation in aircraft throttle settings to produce a high-voltage (20 kilovolts), variable-frequency 9-phase AC distribution system. Using doubly fed electric machines (generator, propulsor, and flywheel) allows for field excitation that can cause variable-frequency or variable speed operation around the commanded throttle setting. The flywheel enables an energy storage system that recovers and reuses energy, while the flywheel slews with the throttle control using the electromagnetic torque produced by the doubly fed electric machine. This design permits both sub-synchronous and super-synchronous operation using limited field excitation power provided through power converters. Finally, the reduced switchgear mass facilitated through the use of a high-frequency AC system, setting-less protection zones, and simplified switches for fault clearance provides enhanced operational capability. This system can be controlled so that fault energy is minimized, preventing collateral damage to aircraft structures even with high voltage distribution. Glenn's innovative system adds performance, efficiency, reliability, and cost savings to cutting-edge hybrid electric technology.
This is an early-stage technology requiring additional development, and Glenn welcomes co-development opportunities.

Ruthenium-Doped Thermoelectric Materials
Solid state power conversion devices, such as thermoelectrics, depend upon temperature gradients for their operation. For example, aeronautic gas turbine engines maintain the necessary temperature gradients throughout their systems due to the enthalpic processes of combustion, which offers the possibility of generating electrical power for use in primary and secondary electrical systems in the aircraft. However, until now thermoelectric materials have not been able to withstand the combination of high temperatures and oxidative environments present in gas turbine engines. Glenn's innovation overcomes these limitations by using a doped oxide pyrochlore (crystal compound) semiconductor as the thermoelectric material. The material has a low thermal conductivity, which allows it to maintain a thermal gradient and sufficient electrical conductivity to produce an electromotive force. The pyrochlore allows the thermoelectric material to be present within a gas turbine engine, converting heat directly into electricity and functioning at high temperatures without oxidizing in air. Glenn's innovative thermoelectric material permits the benefits of solid-state power conversion devices to improve fuel efficiencies for a broader range of applications than has ever been possible. This innovation is in the early stages of development, and Glenn welcomes opportunities for co-development.