Advanced Supercritical Water Oxidation Reactor
environment
Advanced Supercritical Water Oxidation Reactor (LEW-TOPS-146)
Based on a Hydrothermal Flame-Piloted Vortex Flow
Overview
Innovators at the NASA Glenn Research Center, in conjunction with Case Western Reserve University, have designed the Supercritical Water Oxidation - Flame Piloted Vortex (SCWO-FPV) Reactor. The SCWO-FPV Reactor operates at temperatures and pressures above the thermodynamic critical point of water, enabling organic material to become highly soluble, effectively oxidizing all carbonaceous waste in liquid material introduced into the reactor. NASA's new technology addresses problems that have long plagued SCWO-based systems by implementing an innovative design to limit temperatures on the reactor walls, which minimizes the typical issues of scaling, corrosion, and fouling of heat transfer surfaces. While the SCWO-FPV Reactor is being considered for space exploration missions, it has great potential for a variety of terrestrial applications across many industries, especially for water reclamation, water treatment, and waste destruction in liquid waste streams.
The Technology
NASA's Supercritical Water Oxidation - Flame Piloted Vortex (SCWO-FPV) Reactor implements a unique design where heating is primarily supplied by the energetics of the waste stream through the control of a hydrothermal flame in the core of the reactor with the injection of fuel and oxidizer. Once the hydrothermal flame is initiated and stabilized, an outer-core "wash" stream, consisting primarily of water, is injected near the walls at the base of the reactor. This "wash" stream maintains subcritical conditions at the reactor walls, while also dissolving and/or flushing from the reactor any precipitate and non-soluble inorganic materials generated from the supercritical reactor core. Mixing between the core region and the outer subcritical flow region is largely eliminated due to the great differences in density and viscosity. The flow configuration is further stabilized by the generation of a vortex using internal structures on the inside of the reactor wall. An aspirator assembly is positioned at the top of the supercritical core region to extract treated water and un-extracted material is recirculated through the reactor. The rate and amount of aspiration will be determined by product monitoring and will depend on waste stream content and overall operating conditions. Key aspects of the technology have been demonstrated and a prototype reactor is under development.
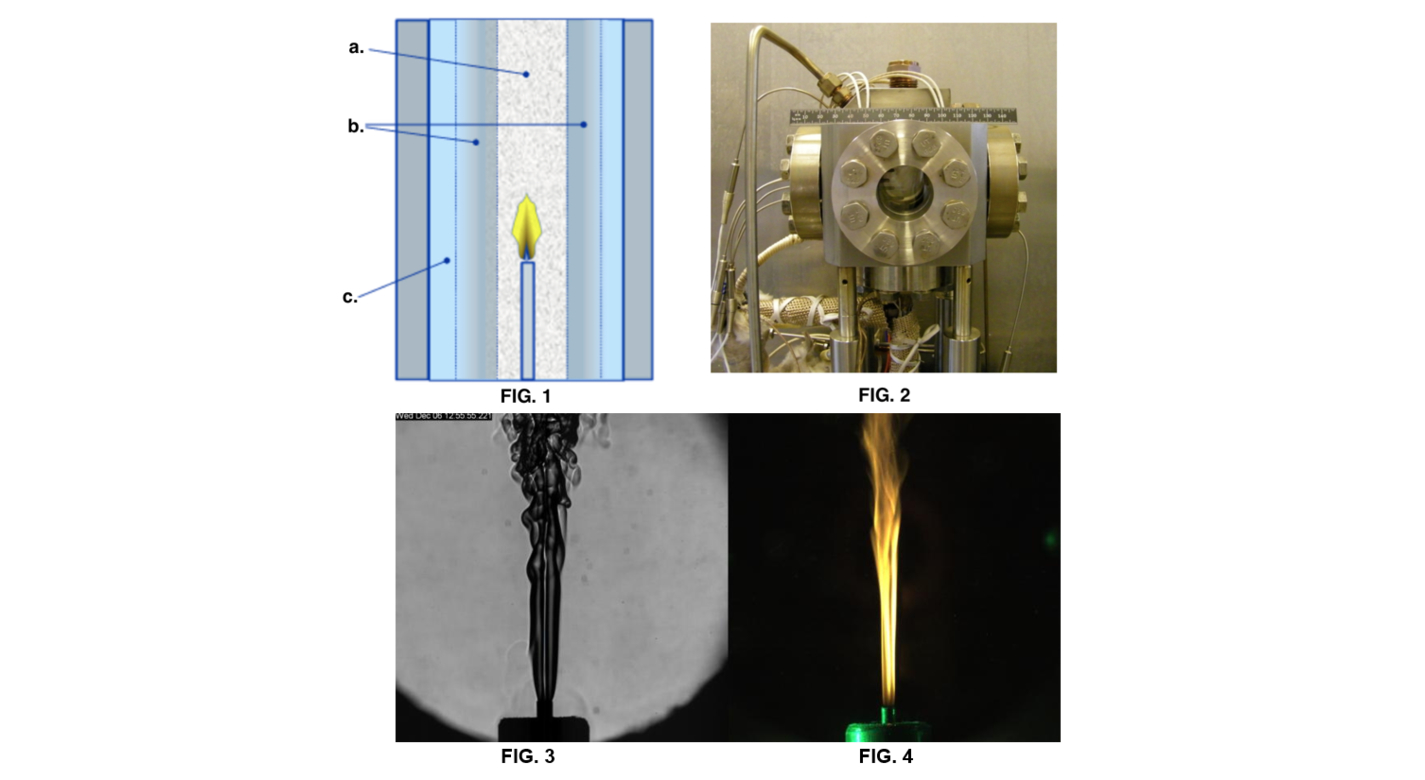
Benefits
- Offers significant advantages over typical closed-loop systems for water-processing: The SCWO-FPV Reactor has improved recovery efficiency over classic closed-loop systems, eliminates all residual microbial contamination, and avoids typical limitations due to waste stream preconditions
- Eliminates wear on reactor components in conventional SCWO systems: The use of controlled regions in the reactor minimizes scaling and eliminates much of the need to protect the inner surfaces from the highly corrosive nature of supercritical water, allowing the reactor vessel to be constructed from thinner and more common materials than typical SCWO systems
- Provides a "green" design: The SCWO-FPV Reactor separates inorganic materials, oxidizes essentially all organic materials, and eliminates microbial contamination. It does not produce pollutants that require further scrubbing, such as NOx or SOx, whereas previously designed SCWO systems occasionally released pollutants due to unstable heating mechanisms
Applications
- Aerospace: water processing and reclamation for human spaceflight
- Agriculture: treatment and reclamation of agricultural runoff
- Manufacturing: treatment of waste streams from making chemicals, pharmaceuticals, semiconductors, paper, and food
- Marine: treatment of discharge to conform to international treaties
- Military: destroying hazardous waste during weapons demilitarization
- Oil, Gas and Power: treatment and reclamation of water used for fracking and treatment of radiation contaminated organic waste streams
- Purification: water treatment and reclamation (e.g., desalination of unusable aquifers, treatment of algae blooms in freshwater lakes, etc.)
- Waste Management: sewage processing and water treatment and reclamation
Technology Details
environment
LEW-TOPS-146
LEW-19801-1
LEW-19801-2
"Spontaneous Ignition of Hydrothermal Flames in Supercritical Ethanol Water Solutions," M.C. Hicks, et al., April 23, 2017,
https://ntrs.nasa.gov/search.jsp?R=20170006847
"Hydrothermal ethanol flames in Co-flow jets," M.C. Hicks, et al., December 11, 2018,
https://ntrs.nasa.gov/search.jsp?R=20190030838
https://ntrs.nasa.gov/search.jsp?R=20170006847
"Hydrothermal ethanol flames in Co-flow jets," M.C. Hicks, et al., December 11, 2018,
https://ntrs.nasa.gov/search.jsp?R=20190030838
Tags:
|
Similar Results

Low-Temperature Oxidation/
Reduction Catalysts
The low-temperature oxidation catalyst technology employs a novel catalyst formulation, termed platinized tin oxide (Pt/SnOx). The catalysts can be used on silica gel and cordierite catalyst supports, and the latest developments provide sprayable formulations for use on a range of support types and shapes. Originally developed for removal of CO, the catalyst has also proven effective for removal of formaldehyde and other lightweight hydrocarbons.
NASA researchers have also extended the capability to include reduction of NOx as well as developed advanced chemistries that stabilized the catalyst for automotive catalytic converters via the engineered addition of other functional components. These catalyst formulations operate at elevated temperatures and have performed above the EPA exhaust standards for well beyond 25,000 miles. In addition, the catalyst can be used in diesel engines because of its ability to operate over an increased temperature range.
For use as a gas sensor, the technology takes advantage of the exothermic nature of the catalytic reaction to detect formaldehyde, CO, or hydrocarbons, with the heat being produced proportional to the amount of analyte present.

New Concepts in Film Cooling for Turbine Blades
In one of NASA Glenn's innovations, a shaped recess can be formed on a surface associated with fluid flow. Often V-shaped, this shaped recess can be configured to create or induce fluid effects, temperature effects, or shedding effects. For example, the shaped recess can be paired (upstream or downstream) with a cooling channel. The configuration of the shaped recess can mitigate the lift-off or separation of the cooling jets that are produced by the cooling channels, thus keeping the cooling jets trained on turbine blades and enhancing the effectiveness of the film-cooling process. The second innovation produced to improve film cooling addresses problems that occur when high-blowing ratios, such as those that occur during transient operation, threaten to diminish cooling effectiveness by creating jet detachment. To keep the cooling jet attached to the turbine blade, and also to spread the jet in the spanwise direction, NASA Glenn inventors have successfully used cooling holes that reduce loss by blowing in the upstream direction. In addition, fences may be used upstream of the holes to bend the cooling flow back toward the downstream direction to further reduce mixing losses. These two innovations represent a significant leap forward in making film cooling for turbine blades, and therefore the operation of turbine engines, more efficient.

Liquid Sorbent Carbon Dioxide Removal System
NASA's Liquid Sorbent Carbon Dioxide Removal System was designed as an alternative to the current CO2 removal technology used on the International Space Station (ISS), which uses solid zeolite media that is prone to dusting, has a low absorption capacity, and requires high regeneration temperatures and frequent maintenance. Motivated by CO2 removal systems on submarines, NASA innovators began investigating the use of liquid sorbents. Liquid sorbents have a capacity four times greater than solid zeolites, require low regeneration temperature, and need fewer unreliable moving mechanical parts than solid based systems. While submarine CO2 scrubbers spray an adsorbing chemical directly into the air stream and allow the liquid to settle, NASA's new system uses a capillary driven 3D printed microchannel direct air/liquid contactor in a closed loop system. The Liquid Sorbent Carbon Dioxide Removal System is robust and reliable, while being low in weight, volume, and power requirements. The system is capable of reaching equilibrium when the liquid sorbent surface is being regenerated at a rate equal to the rate of absorption into the liquid.

Cryogenic Flux Capacitor
Storage and transfer of fluid commodities such as oxygen, hydrogen, natural gas, nitrogen, argon, etc. is an absolute necessity in virtually every industry on Earth. These fluids are typically contained in one of two ways; as low pressure, cryogenic liquids, or as a high pressure gases. Energy storage is not useful unless the energy can be practically obtained ("un-stored") as needed. Here the goal is to store as many fluid molecules as possible in the smallest, lightest weight volume possible; and to supply ("un-store") those molecules on demand as needed in the end-use application. The CFC concept addresses this dual storage/usage problem with an elegant charging/discharging design approach.
The CFC's packaging is ingeniously designed, tightly packing aerogel composite materials within a container allows for a greater amount of storage media to be packed densely and strategically. An integrated conductive membrane also acts as a highly effective heat exchanger that easily distributes heat through the entire container to discharge the CFC quickly, it can also be interfaced to a cooling source for convenient system charging; this feature also allows the fluid to easily saturate the container for fast charging. Additionally, the unit can be charged either with cryogenic liquid or from an ambient temperature gas supply, depending on the desired manner of refrigeration. Finally, the heater integration system offers two promising methods, both of which have been fabricated and tested, to evenly distribute heat throughout the entire core, both axially and radially.
NASA engineers also applied the CFC to a Cryogenic Oxygen Storage Module to store oxygen in solid-state form and deliver it as a gas to an end-use environmental control and/or life support system. The Module can scrub out nuisance or containment gases such as carbon dioxide and/or water vapor in conjunction with supplying oxygen, forming a synergistic system when used in a closed-loop application. The combination of these capabilities to work simultaneously may allow for reduced system volume, mass, complexity, and cost of a breathing device.

3D-Printed Injector for Cryogenic Fluid Management
NASA's TVS Augmented Injector includes an internal heat exchanger, a fluid injector spray head, and an external surface condensation heat exchanger - all combined with multiple intertwined flow paths containing liquid, two-phase, and gaseous working fluid. The TVS provides a source of coolant to the injector, which chills the incoming fluid flow. This cooled flow promotes condensation of the tank ullage dropping pressure and maintains incoming fluid flow. The system eliminates the potential for a stalled fill condition and reduces tank pressure during cryogenic fluid transfer. During fill operations, the tank vent can be closed early in the process before fluid is introduced, and, in some cases, the tank vent may not even need to be opened. Furthermore, the TVS Augmented Injector can remove sufficient thermal energy to reach a 100% liquid level in the receiver tank. A cryo-cooler can be used in place the TVS flow circuit for a zero-loss system. The TVS Augmented Injector couples internal fluid flow cooling and external surface ullage gas condensation into a single, compact package that can be mounted to small tank flanges for minimal impact insertion into any vessel. The injector is printed as one part using additive manufacturing, resulting in part count reduction, improved reproducibility, shorter lead times, and reduced cost compared to conventional approaches.
The injector may be of particular interest in applications where cryogenic fluid is expensive, fluid loss through vents is problematic, and/or achieving high filling levels would be helpful. The injector can benefit typical cryogenic fluid transfer between containers or, alternatively, can serve as a tank pressure control device for long-term storage using a fluid recirculation system that pumps fluid through the injector and sprays cooled liquid back into the tank. Additionally, where ISRU processes are employed, the injector can be used to liquefy incoming propellant streams.