Shape Memory Alloy (SMA)-Enabled Actuators
mechanical and fluid systems
Shape Memory Alloy (SMA)-Enabled Actuators (LEW-TOPS-153)
SMA tube elements to drive rotary and ring gear motion in compact, powerful actuators
Overview
Researchers at NASA Glenn pioneered and matured SMAs to enable future aircraft with morphing airfoil surfaces and adaptive wings that fold to respond to different flight condition demands. SMAs are functional metals with unique properties that can go through solid-state phase transformations—stretched, bent, heated, cooled—and recover their original shape. NASA now has two novel mechanical actuators with SMA transmission elements to move parts with rotational angular twisting, delivering the same power as traditional actuators but in a lightweight, smaller footprint form factor. The new rotary actuator and ring drive actuator move in response to external stimuli, such as heating. The rotary actuator uses nested tubes of SMA to provide torque output or angular displacement; the ring drive actuator uses SMA tubes in a drive gear element to provide continual rotary output in either clockwise or counterclockwise directions. Despite the smaller footprint, the SMA tubes achieve higher power density and similar power output to larger actuators, enabling new designs based on compact actuators.
The Technology
Actuators typically have large footprints and mass to meet the power output needed for operation, leading to design hurdles for aircraft and space applications. Innovators at NASA Glenn developed two novel actuators with different configurations of tubes of SMA to provide rotary output. The SMA tubes are deformed in their martensitic condition and when exposed to a thermal stimulus, the tubes will revert to their original state while providing rotary motion.
One variation of the innovation nests the SMA tubes within a rotary actuator imparting several technical benefits. Nested SMA tubes can decrease the length of the actuator while achieving the same twist angle. For the same actuator length, a nested configuration of SMA tubes can multiply the twist angle and improve the power output. A second variation utilizes SMA components as transmission elements in a ring drive gear to enable continuous rotation in one direction. Previous similar SMA actuators rotate in one direction while heating and the other while cooling, which can limit the output of the rotary actuator. The innovation developed by NASA allows for continuous rotation in ANY direction, thereby allowing the rotational output capability to be independent from the amount of cyclic angular twist provided by the SMA tubes.

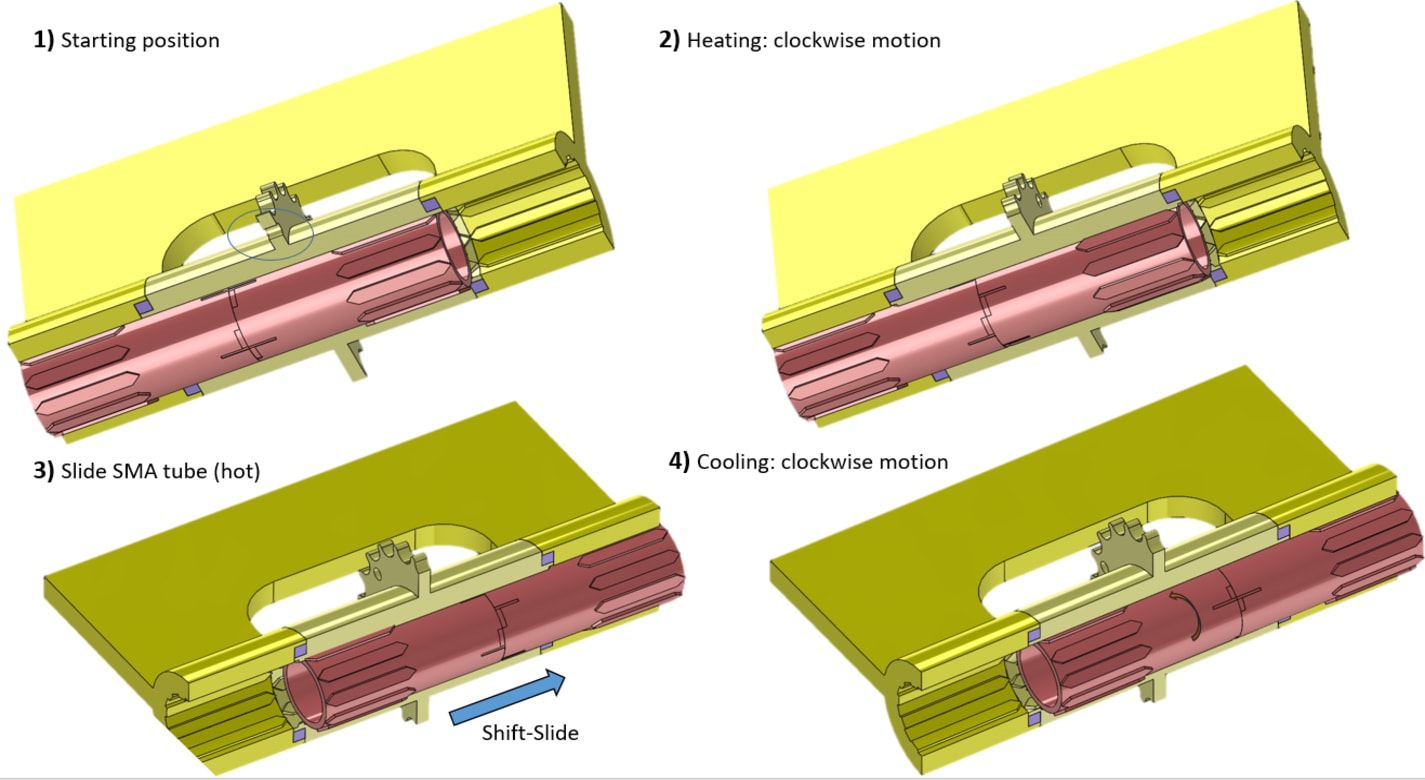
Benefits
- Compact: enables the design of lighter and smaller actuators with increased applications
- Efficient: achieves similar if not higher power output with smaller footprints than state-of-the-art actuators
- Reliable: reduces the risk of mechanical failure and improves the reliability of the rotary actuators
- Simple: does not require the input of a fuel source or pressure-fed fluid, and can provide rotary motion from heating and cooling alone
Applications
- Aeronautics: smart winglets on sub-sonic air transport to large folding wing sections with reduced rudder configurations
- Space: folding structures such as solar panels, antennas, and booms
- Automotive: door handles and hood lifts
- Marine: doors, compartments, hood lifts
- General: any application utilizing motors, small engines, or any rotary actuation* *Only applies to the continuous rotation actuator
Technology Details
mechanical and fluid systems
LEW-TOPS-153
LEW-19605-1
LEW-19596-1
Tags:
|
Similar Results
.jpg)
Shape Memory Alloy Mechanisms for CubeSats
Most spacecraft feature release, retention, and deployment devices as key components, because these devices achieve on-demand configurability of solar panels, probes, antennas, scientific instruments, fairings, etc. Until now, designing and using such devices in small spacecraft has been a challenge, because their mass, volume, and power requirements are significant and can impose design constraints. CubeSats, in particular, often need to deploy several structures (such as solar arrays) simultaneously, which prior-art deployment devices have not been able to manage effectively. Glenn's innovation embeds SMAs within the components so the structures can be retained during launch, then released and deployed in orbit. The release and retention device is controlled by an SMA activated pin puller to disengage the release plate from the hooks holding the solar arrays. Once released, the SMA hinge is passively enabled to the deployed state. When ready on orbit, the mechanism is commanded to release and electrical power is sent to the SMA actuator, releasing the component to its deployed state. The component is deployed to its final position through the use of hinges, which are activated passively with SMA spring strips. The retention and release device and hinge are substantially smaller and lighter than deployment mechanisms have ever been and can deploy simultaneously with great reliability. Having already been successfully deployed on a NASA mission, Glenn's innovation is a game-changing technology for CubeSats and other small satellites.

How to Train Shape Memory Alloys
Glenn researchers have optimized how shape memory alloys (SMAs) are trained by reconceptualizing the entire stabilization process. Whereas prior techniques stabilize SMAs during thermal cycling, under conditions of fixed stress (known as the isobaric response), what Glenn's innovators have done instead is to use mechanical cycling under conditions of fixed temperature (the isothermal response) to achieve stabilization rapidly and efficiently. This novel method uses the isobaric response to establish the stabilization point under conditions identical to those that will be used during service. Once the stabilization point is known, a set of isothermal mechanical cycling experiments is then performed using different levels of applied stress. Each of these mechanical cycling experiments is left to run until the strain response has stabilized. When the stress levels required to achieve stabilization under isothermal conditions are known, they can be used to train the material in a fraction of the time that would be required to train the material using only thermal cycling. As the strain state has been achieved isothermally, the material can be switched back under isobaric conditions, and will remain stabilized during service. In short, Glenn's method of training can be completed in a matter of minutes rather than in days or even weeks, and so SMAs become much more practical to use in a wide range of applications.

Outer Aileron Yaw Damper
Rudders have long served as the primary flight control surface as is pertains to aircraft yaw. Breaking this mold, NASA's SAW technology is a game-changing development in aircraft wing engineering that reduces rudder motion required to control aircraft. The benefits of reduced rudder dependency led NASA to develop the outer aileron yaw damper to further decrease or eliminate rudder dependency for aircraft using SAWs.
As mentioned, SAWs use shape memory alloy actuators to articulate the outer portion of the wing, effectively creating a movable wingtip. NASA's invention uses an outer aileron located on the wingtips, which is driven (along with the inner ailerons) by a novel control algorithm. The control algorithm, taking into account the wingtip positions, manipulates the outer ailerons to achieve the desired yaw rate. At the same time, it positions the inner ailerons to counter roll rate resulting from the outer aileron. In other words, the control algorithm calculates a control surface ratio (i.e., position of inboard aileron and outboard aileron) that produces desired yaw and roll accelerations.
The system can also be used to offset the existing rudder in current or future aircraft designs. A second part of NASAs novel outer aileron control algorithm modifies the aircrafts rudder loop gain in proportion to outer aileron usage. This allows the outer ailerons and rudder to work in tandem, while at the same time reducing rudder usage.
As a result of this NASA invention, required rudder usage can be reduced or eliminated for aircraft with SAWs. Consequently, the size of rudders and vertical tail structures can be reduced, which in turn reduces weight and parasitic drag. The result is an aircraft with increased performance and fuel efficiency.

Shape Memory Alloy Tubular Structure
The Glenn technology utilizes SMA structural elements (wires and springs) interlocked via a unique layering pattern, allowing the structure to take on tubular geometries while exhibiting the same ride performance as traditional tires. Though previous tires have used SMA elements as load-carrying members, this new design offers an improved structural pattern - consisting of two layers of SMA elements. The primary layer is a single wire shape set into a coil and wrapped circumferentially around a wheel, which sets the overall tire geometry and provides added strength in the radial and axial directions. The secondary layer consists of smaller SMA springs interlocked with each other as well as the primary coil, acting as a sheath that sets the coil spacing and provides the necessary shear stiffness.
SMAs are superelastic in nature and can take up to 8% effective reversible strain without yielding. The SMAs can handle up to 30x more strain, allowing the tire structure to undergo high levels of deformation without permanent damage. Because these tires do not rely on air, the risks associated with a flat tire are eliminated, and tire stiffness never varies (the tires never run 'under-inflated'). Furthermore, this airless tire design may enable the redesigning of wheel and braking systems. The first bicycle tire prototype was estimated to have a tire stiffness comparable to a road bike tire inflated to 75 psi, but with improved lateral and shear stiffness. By varying the SMA wire geometry, a wide range of tire sizes and stiffnesses is achievable. Rubber tread surfaces may be attached to the outside of the SMA tire for sufficient traction on a variety of terrain.

Shape Memory Alloy Rock Splitters (SMARS)
Glenn's revolutionary SMARS device is fabricated from nickel-titanium-halfnium (NiTiHf), nickel-titanium-zirconium compositions, or a combination. These compositions contain a secondary, nanometer-sized precipitate phase, which is produced through processes of compositional control and ageing heat treatments. Glenn's novel materials and processes have yielded a SMA composition that produces much higher stresses than other SMAs on the commercial market.
The SMARS device is composed of 1) SMA material as the actuating member; 2) a casing heater placed around the SMA member; 3) a DC or AC power source to provide current through the heater; 4) pointed tips for acute penetration into rock formations; and 5) a hand-press to reset the SMA element after each use. In the rock-splitting process, a hole equal to the diameter of the SMA element is drilled in the portion of the rock where the fracture is desired. Next, the pre-compressed SMA is inserted into the hole, and AC or DC current is applied to energize the devices heaters. Once the heater achieves the critical transformation temperature, the SMA will begin to expand within seconds. Since its expansion is constrained by the rock walls, the SMA will eventually exert up to 1500 MPa of stress, splitting the rock apart. When the current is removed and the heater cools, the SMA material returns to its pre-compressed state. At this point, the material can be recovered, so the process is repeatable after reshaping. The SMA actuating members were also designed to achieve displacement greater than the materials strain output. Glenns SMARS device provides high-powered rock fracturing that is controllable, reliable, and comparatively simple without the use of explosives, hydraulics, or chemicals.