Stronger Plug for Friction Pull Plug Welding of Thick Plates
Manufacturing
Stronger Plug for Friction Pull Plug Welding of Thick Plates (MFS-TOPS-97)
Hybrid Plug with Steel Shank Enables Thicker Welds of Different Alloys
Overview
NASA and Geocent, LLC innovators adapted a plug to improve aluminum friction pull plug welding (FPPW). The rugged plug is less vulnerable to snapping off and helps reduce chatter. FPPW is the process that is necessary to plug the hole that is left behind as a friction stir weld (FSW) joint is completed and the pin tool of the welder retracts from the joint. The inventors have replaced the plug support with steel to improve its strength to endure the forces of the FPPW process. NASA adapted the plug to enable FPPW processing for the thicker welds and different alloys needed for NASA’s new Space Launch System (SLS). This new plug helps solve the well-known FPPW challenges of plug welding on thicker plates that have caused weld defects in the past such as substantial plug necking and plug rotational stalling. The new plug has been tested and used in building NASA equipment.
The Technology
Friction Pull Plug Welding (FPPW) is the process necessary to plug the hole that is left behind as a friction stir weld (FSW) joint is completed and the pin tool of the welder retracts from the joint. FPPW involves a small, rotating part (plug) being spun and simultaneously pulled (forged) into a hole in a larger part. Much work has been done to fully understand and characterize the process and its limitations. FPPW worked very well for building large rocket sections such as the circumferential welds of the upper stages of NASA's Ares rocket, and to repair the external tank. Engineers were challenged to adapt FPPW to accommodate the thicker plates new alloy combinations of the SLS. The new hybrid plug solves the issue of the plugs snapping due to the increase torsion and moment stresses when joining thicker plates. The new hybrid plug, with a steel shank, makes FPPW more practical and robust. The new plug has been used to make space-qualified parts at NASA, and the plug welds are as strong as initial welds.

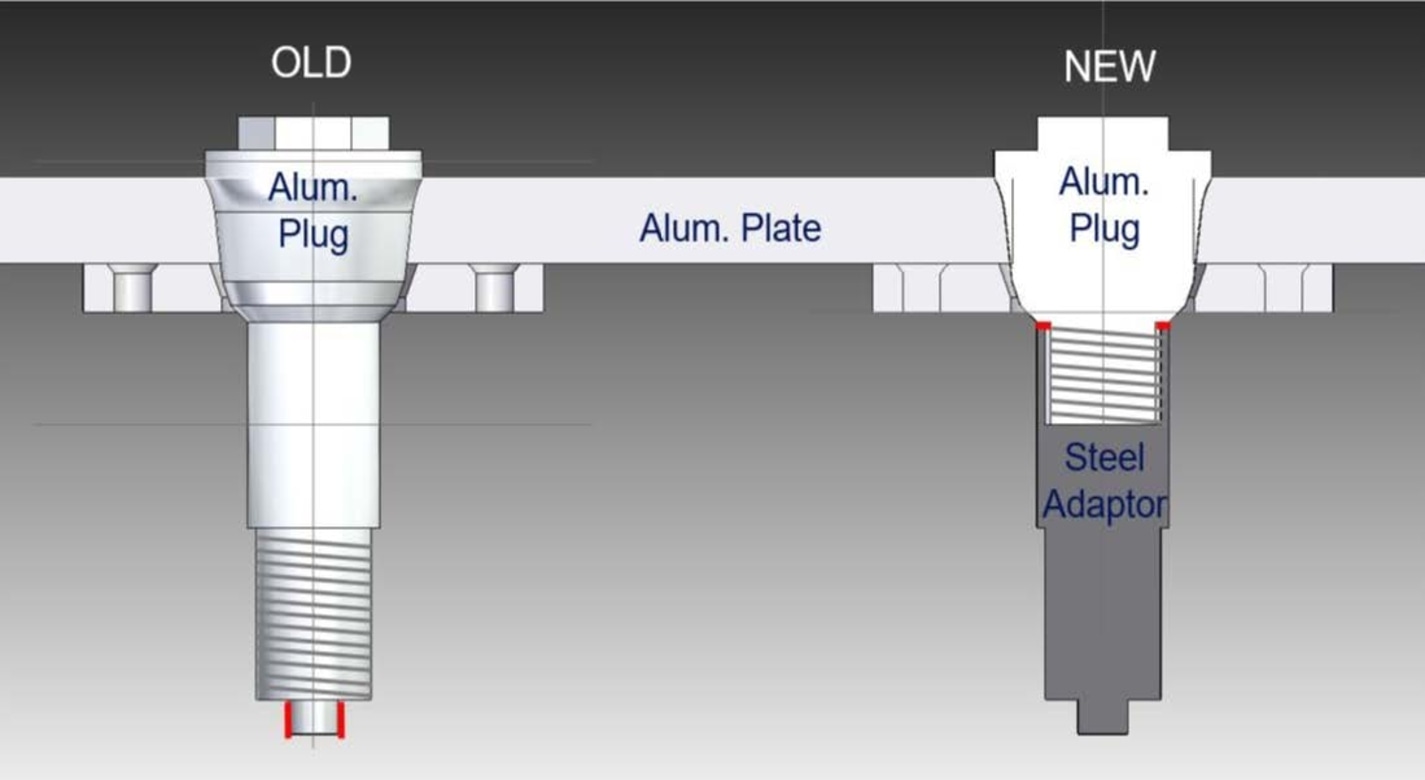
Benefits
- Supports Thicker Welds of up to 0.625" (of 2019 Aluminum)
- Enables FPPW on More Alloys of Aluminum including 2019, 2025
- Reduces vulnerability to breaking via lower torsion and normal stresses on the plug's threads
- Reduces Plug Necking and Plug Rotational Stalling
- Helps Make the FPPW Process More Practical and Robust
- Prevents the plug chattering and related stalling
Applications
- FPPW is mostly used on cylindrical and pressurized vehicles in the following industries
- Aerospace: NASA, military/defense applications
- Future commercial ships: large aluminum vessels for transport
- Army lightweight vehicles and hybrid armor (Humvee, e.g.)
- Naval ships and littoral combat ships that also use thick aluminum plates
Technology Details
Manufacturing
MFS-TOPS-97
MFS-33218-1
Tags:
|
Similar Results

Friction Stir Deposition Innovations
Metal additive manufacturing may be limited by build volumes (i.e., it can be hard to make large parts), post-processing requirements, and upfront costs to buy capital equipment. The two NASA-developed technologies are add-on tools for FSW systems (reducing costs), do not require a printer or print bed, and produce parts with high quality surface finishes.
The C-FSD attachment includes a non-rotating block through which the C-FSW rotating pin is threaded, and a containment plate to hold the plasticized metal within the system. In this technique, raw metal feedstock is fed into one end of the non-rotating block, is heated and plasticized by the C-FSW pin, and is driven out the other side of the block. The C-FSW pin is used to join the new material to the pre-existing layer.
The B-FSD tool uses a dual-shoulder design to print outward from the edge of the base panel. The B-FSD process uses the same feed system as the C-FSD, but utilizes the bobbin/SR-FSW pin's dual shoulders (i.e., containing the metal on both the top and bottom) enabling more complex structures to be made, and the ability to print varying thickness depositions in a single pass.
The Additive C-FSD and B-FSD end effector tools are both at technology readiness level (TRL) 4 (component and/or breadboard validation in laboratory environment) and are available for patent licensing.

Internal Friction Reduction (IFR) Tool
During SR-FSW, the wicking of substrate material into the gap between the crown shoulder and pin can lead to pinch load shifting–an increasing difference between the applied pin load and actual pinch load. NASA's IFR Tool mitigates pinch load shifting, enabling a more robust SR-FSW process due to better agreement between the applied pin load and the actual pinch load.
As pinch loads are not dynamically measured during welding, NASA has relied on defect rates and pin tool ejection loads to demonstrate the value of the IFR Tool. Large-scale welds were performed with both the IFR Tool and a standard pin tool. Weld inspections found a 90% reduction in defect generation rate for the IFR tool, and the first defect in the standard pin tool sample occurred at 300" compared to at 900" in the IFR Tool sample. There was also a drastic improvement in mechanical properties variations along the weld.
In another study, a series of 27.5' barrel welds were performed with both the IFR Tool and a standard pin tool. After welding, ejection forces required to remove the pin tools from their fixtures were measured. The standard pin tool ejection force was 9,400 lbs., nearly 5 times larger than that of the IFR Tool at 2,000 lbs . The large difference suggests that during welding, the standard pin tool would have been less responsive to substrate surface variations than the IFR Tool. Weld inspections supported this theory, as they found a significantly lower defect rate in the IFR Tool samples.

Conventional friction stir extrusion machine
Typical metal extrusion relies on heating large metal billets and then forcing the heated billet through a dye to extrude the geometry and length of interest. These processes require high energy inputs, expensive machinery to heat and manipulate the billets, and the length of the final part is limited by billet size. Thus, new ways to cost effectively and efficiently produce extruded parts are needed.
The C-FSE machine developed by NASA encompasses a non-rotating extrusion block and a rotating pin that extends through the chamber. The extrusion block has a close tolerance fit to the rotating pin to prevent material from escaping from the ends of the block. Raw metal feedstock is fed into one side of the chamber, the rotating pin interacts with the metal to generate plastic deformation and heat, and the metal is driven out the other side of the extrusion block through a customizable die. As the C-FSE machine does not require pre-heated billets, the extruded parts may be of any desired length. Further, the extrusion machine is modular in nature and may be retrofitted onto an existing FSW system, and the die may be easily replaced for varying extrusion geometries. The C-FSE machine has been prototyped and used to produce freestanding metal parts.
The C-FSE machine is at technology readiness level (TRL) 4 (component and/or breadboard validation in laboratory environment) and is available for patent licensing.

Ultrasonic Stir Welding
Ultrasonic Stir Welding is a solid state stir welding process, meaning that the weld work piece does not melt during the welding process. The process uses a stir rod to stir the plasticized abutting surfaces of two pieces of metallic alloy that forms the weld joint. Heating is done using a specially designed induction coil. The control system has the capability to pulse the high-power ultrasonic (HPU) energy of the stir rod on and off at different rates from 1-second pulses to 60-millisecond pulses. This pulsing capability allows the stir rod to act as a mechanical device (moving and stirring plasticized nugget material) when the HPU energy is off, and allowing the energized stir rod to transfer HPU energy into the weld nugget (to reduce forces, increase stir rod life, etc.) when the HPU energy is on. The process can be used to join high-melting-temperature alloys such as titanium, Inconel, and steel.

Composite Joint Connector
This technology is a joint connector for application between two or more tubular parts, or to connect one or more tubular parts to a fixed structure. This attachment technology is more structurally efficient and reduces failure characteristics due to the uniformity of composite material across the joint. In comparison to a typical joint, this technology reduces weight while minimizing stress variations that lead to structural failure. Moreover, typical joints must be bonded or screwed together, which further reduces efficiency. The invented technology, however, is designed so that it is both bonded and mechanically locked by design rather than relying on separate mechanical fasteners. The result is a design that mitigates failure of a structural joint.