Multi-Objective Flight Control Optimization Framework
aerospace
Multi-Objective Flight Control Optimization Framework (TOP2-282)
Method for Drag Optimization, Load Alleviation Control, and Modal Suppression for Flexible Aircraft
Overview
As aircraft wings become more flexible, adverse aerodynamic interactions with the wing structure can result in changes in the wing shapes due to aeroelastic deflections that can prevent the optimal aerodynamic performance from being realized. The flexible wing structure can also be more susceptible to vibration due to atmospheric turbulence and wind gusts which can affect passenger ride comfort and compromise the structural integrity. NASA Ames Research Center has developed a new multi-objective flight control optimization framework that can achieve multiple control objectives simultaneously. These control objectives comprise rigid-aircraft stability augmentation control, flexible mode suppression, drag optimization, and maneuver / gust load alleviation, while still maintaining traditional pilot command-tracking tasks. The technology addresses the operational constraints and the efficiency goal of modern transports simultaneously in order to arrive at optimal flight control solutions.
The Technology
Composite materials are being used in aerospace design because of their high strength-to-weight ratio. On modern airplanes, composite wings offer a greater degree of aerodynamic efficiency due to weight savings, but at the same time introduce more structural flexibility than their aluminum counterparts. Under off-design flight conditions, changes in the wing shape due to structural flexibility cause the wing aerodynamics to be non-optimal. This effect could offset any weight saving benefits realized by the composite wings. Structural flexibility could also cause adverse interactions with flight control and structural vibration which can compromise aircraft stability, pilot handling qualities, and passenger ride quality. NASA Ames Research Center has developed a novel technology that employs a new multi-objective flight control optimization framework to achieve multiple control objectives simultaneously. This technology leverages the availability of distributed flight control surfaces in modern transports. The multi-objective flight control technology comprises the following objectives all acting in a synergistic manner: 1) traditional stability augmentation and pilot command-following flight control, 2) drag minimization, 3) aeroelastic mode suppression, 4) gust load alleviation, and 5) maneuver load alleviation. Each of these objectives can be a major control system design in its own right. Thus, the multi-objective flight control technology can effectively manage the complex interactions of the individual single-objective flight control system design and take into account multiple competing requirements to achieve optimal flight control solutions that have the best compromise for these requirements. In addition, a real- time drag minimization control strategy is included in the guidance loop. This feature utilizes system identification methods to estimate aerodynamic parameters for the on-line optimization. The aerodynamic parameters are also used in the multi-objective flight control for drag minimization and maneuver/ gust load alleviation control.
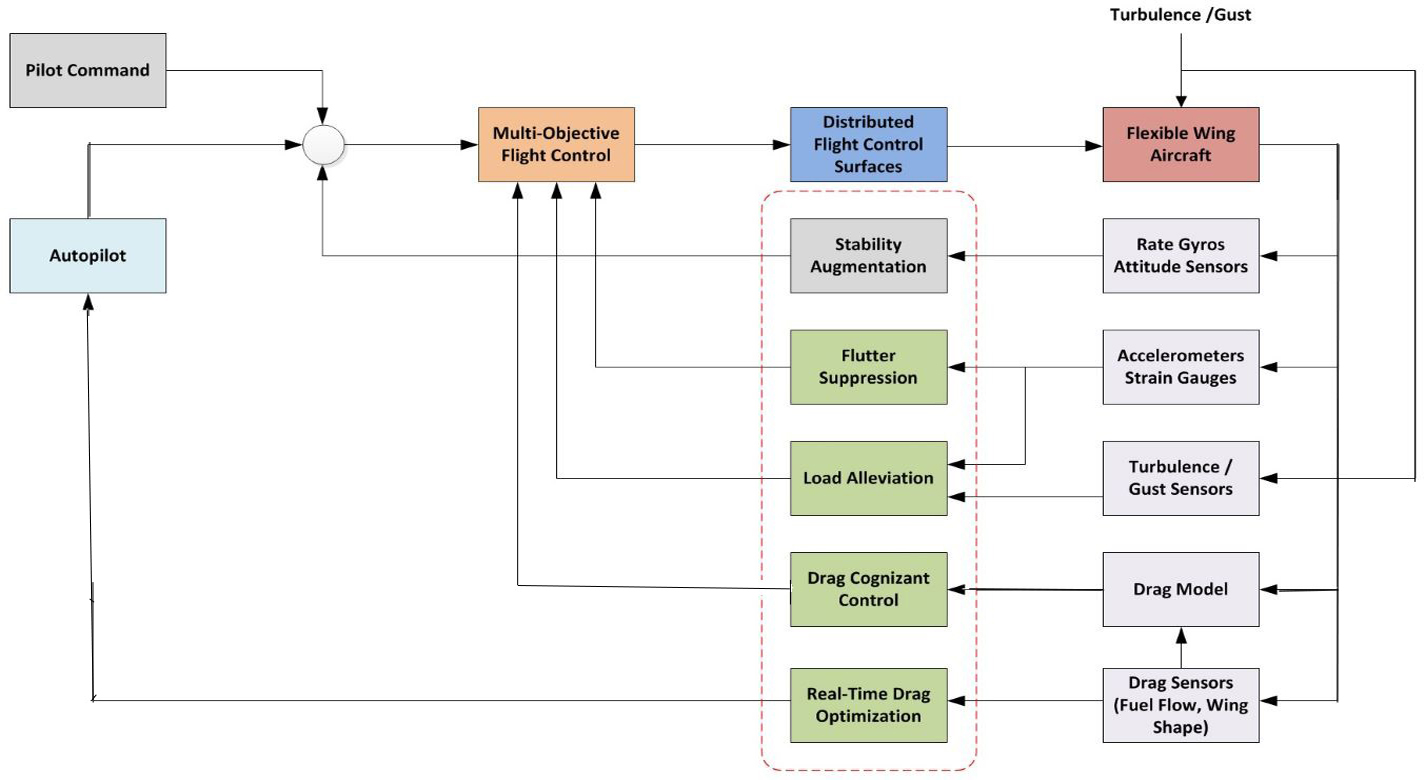
Benefits
- Offers reduced drag and increased fuel efficiency
- Provides increased safety and better operations
- Improves pilot handling qualities and passenger ride comfort
- Offers solutions to flexible high-aspect ratio wing designs for modern transport aircraft
- Reduced structural responses due to wing flexibility
- Multi-objective flight control means that the aircraft flight control system can achieve multiple control objectives simultaneously (rather than one at a time) by trading competing requirements
Applications
- Aerospace industry /aircraft manufacturers (commercial and military, large and small, etc.); especially aircraft designed with flexible high-aspect ratio wing technology (perhaps using composites)
- Unmanned Aerial Vehicle (UAVs) industry
- Urban Air Mobility (UAM) industry
- Flight control system providers
- Avionics industry
Tags:
|
Similar Results

Real-Time Drag Opti-mization Control Framework
According to the International Air Transport Association statistics, the annual fuel cost for the global airline industry is estimated to be about $140 billion in 2017. Therefore, fuel cost is a major cost driver for the airline industry. Advanced future transport aircraft will likely employ adaptive wing technologies that enable the wings of those aircraft to adaptively reconfigure themselves in optimal shapes for improved aerodynamic efficiency throughout the flight envelope. The need for adaptive wing technologies is driven by the cost of fuel consumption in commercial aviation. NASA Ames has developed a novel way to address aerodynamic inefficiencies experienced during aircraft operation. The real-time drag optimization control method uses an on-board, real-time sensor data gathered from the aircraft conditions and performance during flight (such as engine thrust or wing deflection). The sensor data are inputted into an on-board model estimation and drag optimization system which estimates the aerodynamic model and calculates the optimal settings of the flight control surfaces. As the wings deflect during flight, this technology uses an iterative approach whereby the system continuously updates the optimal solution for the flight control surfaces and iteratively optimizes the wing shape to reduce drag continuously during flight. The new control system for the flight control surfaces can be integrated into an existing flight control system. This new technology can be used on passenger aircraft, cargo aircraft, or high performance supersonic jets to optimize drag, improve aerodynamic efficiency, and increase fuel efficiency during flight. In addition, it does not require a specific aircraft math model which means it does not require customization for different aircraft designs. The system promises both economic and environmental benefits to the aviation industry as less fuel is burned.

Improved Fixed-Wing Gust Load Alleviation Device
Gust loads may have detrimental impacts on flight including increased structural and aerodynamic loads, structural deformation, and decreased flight dynamic performance. This technology has been demonstrated to improve current gust load alleviation by use of a trailing-edge, free-floating surface control with a mass balance. Immediately upon impact, the inertial response of the mass balance shifts the center of gravity in front of the hinge line to develop an opposing aerodynamic force alleviating the load felt by the wing. This passive gust alleviation control covering 33% of the span of a cantilever wing was tested in NASA Langleys low speed wind tunnel and found to reduce wing response by 30%.
While ongoing experimental work with new laser sensing technologies is predicted to similarly reduce gust load, simplicity of design of the present invention may be advantageous for certification processes. Additionally, this passive technology may provide further gust alleviation upon extending the use of the control to the entire trailing edge of the wing or upon incorporation with current active gust alleviation systems.
Importantly, the technology can be easily incorporated into to the build of nearly all fixed wing aircrafts and pilot control can be maintained through a secondary trim tab. Though challenging to retrofit, passive gust alleviation could enable use of thinner, more efficient wings in new plane design.
Method And System for Enhancing Vehicle Performance and Design Using Parametric Modeling and Gradient-Based Control Integration
The parametric modeling system allows for the integrated design and optimization of aerospace vehicles by unifying physical and control subsystems within a single computational model. The system includes representations of the vehicle’s geometry, structural load, propulsion, energy storage, and GNC systems. The system performs sensitivity analysis on key performance metrics (e.g., fuel consumption, heat load, and mechanical forces) to determine how changes in design parameters affect overall performance. By incorporating real-world conditions, such as wind variations and sensor noise, the system allows for the use of real-time feedback to refine vehicle designs. The optimization process uses a gradient-based algorithm to iteratively adjust parameters so that constraints such as structural integrity, thermal protection, and fuel capacity are met. The system generates a Pareto front representing trade-offs between performance metrics that allow engineers to visualize optimal designs for different mission profiles, which enhances design accuracy while reducing the need for expensive physical testing.

Rapid Aero Modeling for Computational Experiments
RAM-C interfaces with computational software to provide test logic and manage a unique process that implements three main bodies of theory: (a) aircraft system identification (SID), (b) design of experiment (DOE), and (c) CFD. SID defines any number of alternative estimation methods that can be used effectively under the RAM-C process (e.g., machine learning techniques, regression, neural nets, fuzzy modeling, etc.). DOE provides a statistically rigorous, sequential approach that defines the test points required for a given model complexity. Typical DOE test points are optimized to reduce either estimation error or prediction error. CFD provides a large range of fidelity for estimating aircraft aerodynamic responses. In initial implementations, NASA researchers “wrapped” RAM-C around OVERFLOW, a NASA-developed high-fidelity CFD flow solver. Alternative computational software requiring less time and computational resources could be also utilized.
RAM-C generates reduced-order aerodynamic models of aircraft. The software process begins with the user entering a desired level of fidelity and a test configuration defined in terms appropriate for the computational code in use. One can think of the computational code (e.g., high-fidelity CFD flow solver) as the “test facility” with which RAM-C communicates with to guide the modeling process. RAM-C logic determines where data needs to be collected, when the mathematical model structure needs to increase in order, and when the models satisfy the desired level of fidelity.
RAM-C is an efficient, statistically rigorous, automated testing process that only collects data required to identify models that achieve user-defined levels of fidelity – streamlining the modeling process and saving computational resources and time. At NASA, the same Rapid Aero Modeling (RAM) concept has also been applied to other “test facilities” (e.g., wind tunnel test facilities in lieu of CFD software).

Green aviation - improved aerodynamic efficiency and less fuel burn
Currently, as fuel is burned, wing loading is reduced, thereby causing the wing shape to bend and twist. This wing-shape change causes the wings to be less aerodynamically efficient. This problem can be further exacerbated by modern high-aspect flexible wing design. Aircraft designers typically address the fuel efficiency goal by reducing aircraft weights, improving propulsion efficiency, and/or improving the aerodynamics of aircraft wings passively. In so doing, the potential drag penalty due to changes in the wing shapes still exists at off-design conditions. The unique or novel features of the new concepts are:
1. Variable camber flap provides the same lift capability for lower drag as compared to a conventional flap. The variable camber trailing edge flap (or leading edge slat) comprises multiple chord-wise segments (three or more) to form a cambered flap surface, and multiple span-wise segments to form a continuous trailing edge (or leading edge) curve with no gaps which could be prescribed by a mathematical function or the equivalent with boundary conditions enforced at the end points to minimize tip vortices
2. Continuous trailing edge flap (or leading edge slat) provides a continuously curved trailing edge (or leading edge) with no gaps to minimize vortices that can lead to an increase in drag.
3. The active wing-shaping control method utilizes the novel flap (or slat) concept described herein to change a wing shape to improve aerodynamic efficiency by optimizing span-wise aerodynamics.
4. An aeroelastic wing shaping method for analyzing wing deflection shape under aerodynamic loading is used in a wing-control algorithm to compute a desired command for the flap-actuation system to drive the present flap (or slat) system to the correct position for wing shaping.