Search
PATENT PORTFOLIO
Ruggedized Infrared Camera
This new technology applies NASA engineering to a FLIR Systems Boson® Model No. 640 to enable a robust IR camera for use in space and other extreme applications. Enhancements to the standard Boson® platform include a ruggedized housing, connector, and interface. The Boson® is a COTS small, uncooled, IR camera based on microbolometer technology and operates in the long-wave infrared (LWIR) portion of the IR spectrum. It is available with several lens configurations. NASA's modifications allow the IR camera to survive launch conditions and improve heat removal for space-based (vacuum) operation. The design includes a custom housing to secure the camera core along with a lens clamp to maintain a tight lens-core connection during high vibration launch conditions. The housing also provides additional conductive cooling for the camera components allowing operation in a vacuum environment. A custom printed circuit board (PCB) in the housing allows for a USB connection using a military standard (MIL-STD) miniaturized locking connector instead of the standard USB type C connector. The system maintains the USB standard protocol for easy compatibility and "plug-and-play" operation.

Self-aligning Poppet
Without improvements in valve technologies, propellant and commodity losses will likely make long-duration space missions (e.g., to Mars) infeasible. Cryogenic valve leakage is often a result of misalignment and the seat seal not being perpendicular relative to the poppet. Conventional valve designs attempt to control alignment through tight tolerances across several mechanical interfaces, bolted or welded joints, machined part surfaces, etc. However, because such tight tolerances are difficult to maintain, leakage remains an issue.
Traditional poppets are not self-aligning, and thus require large forces to “crush” the poppet and seat together in order to overcome misalignment and create a tight seal. In contrast, NASA’s poppet valve self-aligns the poppet to the valve seat to minimize leakage. Once the poppet and seat are precisely self-aligned, careful seat crush is provided. Owing to this unique design, the invention substantially reduces the energy required to make a tight seal – reducing size, weight, and power requirements relative to traditional valves. Testing at MSFC showed that NASA’s poppet reduces leakage rates of traditional aerospace cryogenic valves (~1000 SCIM) by three orders of magnitude, resulting in leakage rates suitable for long-duration space missions (~1 SCIM).
NASA’s self-aligning poppet was originally targeted for aerospace cryogenic valve systems, especially for long-duration manned space missions – making the invention an attractive solution for aerospace valve vendors. The invention may also find use in the petrochemical or other industries that require sealing to prevent critical or hazardous chemicals from leaking into the environment. Generally, the invention may be suitable for any application requiring low-leak and/or long duration storage of expensive or limited resource commodities (e.g., cryogenic gases, natural gas, nuclear engines, etc).
.jpg)
Interim, In Situ Additive Manufacturing Inspection
The in situ inspection technology for additive manufacturing combines different types of cameras strategically placed around the part to monitor its properties during construction. The IR cameras collect accurate temperature data to validate thermal math models, while the visual cameras obtain highly detailed data at the exact location of the laser to build accurate, as-built geometric models. Furthermore, certain adopted techniques (e.g., single to grouped pixels comparison to avoid bad/biased pixels) reduce false positive readings.
NASA has developed and tested prototypes in both laser-sintered plastic and metal processes. The technology detected errors due to stray powder sparking and material layer lifts. Furthermore, the technology has the potential to detect anomalies in the property profile that are caused by errors due to stress, power density issues, incomplete melting, voids, incomplete fill, and layer lift-up. Three-dimensional models of the printed parts were reconstructed using only the collected data, which demonstrates the success and potential of the technology to provide a deeper understanding of the laser-metal interactions. By monitoring the print, layer by layer, in real-time, users can pause the process and make corrections to the build as needed, reducing material, energy, and time wasted in nonconforming parts.

Ultrasonic Stir Welding
Ultrasonic Stir Welding is a solid state stir welding process, meaning that the weld work piece does not melt during the welding process. The process uses a stir rod to stir the plasticized abutting surfaces of two pieces of metallic alloy that forms the weld joint. Heating is done using a specially designed induction coil. The control system has the capability to pulse the high-power ultrasonic (HPU) energy of the stir rod on and off at different rates from 1-second pulses to 60-millisecond pulses. This pulsing capability allows the stir rod to act as a mechanical device (moving and stirring plasticized nugget material) when the HPU energy is off, and allowing the energized stir rod to transfer HPU energy into the weld nugget (to reduce forces, increase stir rod life, etc.) when the HPU energy is on. The process can be used to join high-melting-temperature alloys such as titanium, Inconel, and steel.

Sublimable Propellant Source for Iodine-fed Ion Propulsion System
NASAs iodine vapor feed system is based on a mechanism that holds and maintains the solid iodine is contact with a heated surface, in this case the walls of the propellant tank. The mechanism provides a robust and reliable steady-state delivery of sublimated iodine vapor to the ion propulsion system by ensuring good thermal contact between the solid iodine and the tank walls.
To date, the technology development effort includes extensive thermal, mechanical and flow modelling together with testing of components and subsystems required to feed iodine propellant to a 200-W Hall thruster. The feed system has been designed to use materials that are resistant to the highly-reactive nature of iodine propellant. Dynamic modeling indicates that the feed system tubing can be built is such a way as to reduce vibrationally-induced stresses that occur during launch. Thermal modeling has been performed to demonstrate that the feed system heater power levels are sufficient to heat the tank and propellant lines to operating temperatures, and sublime the iodine in the storage tank to supply propellant for reliable and long-term operation.
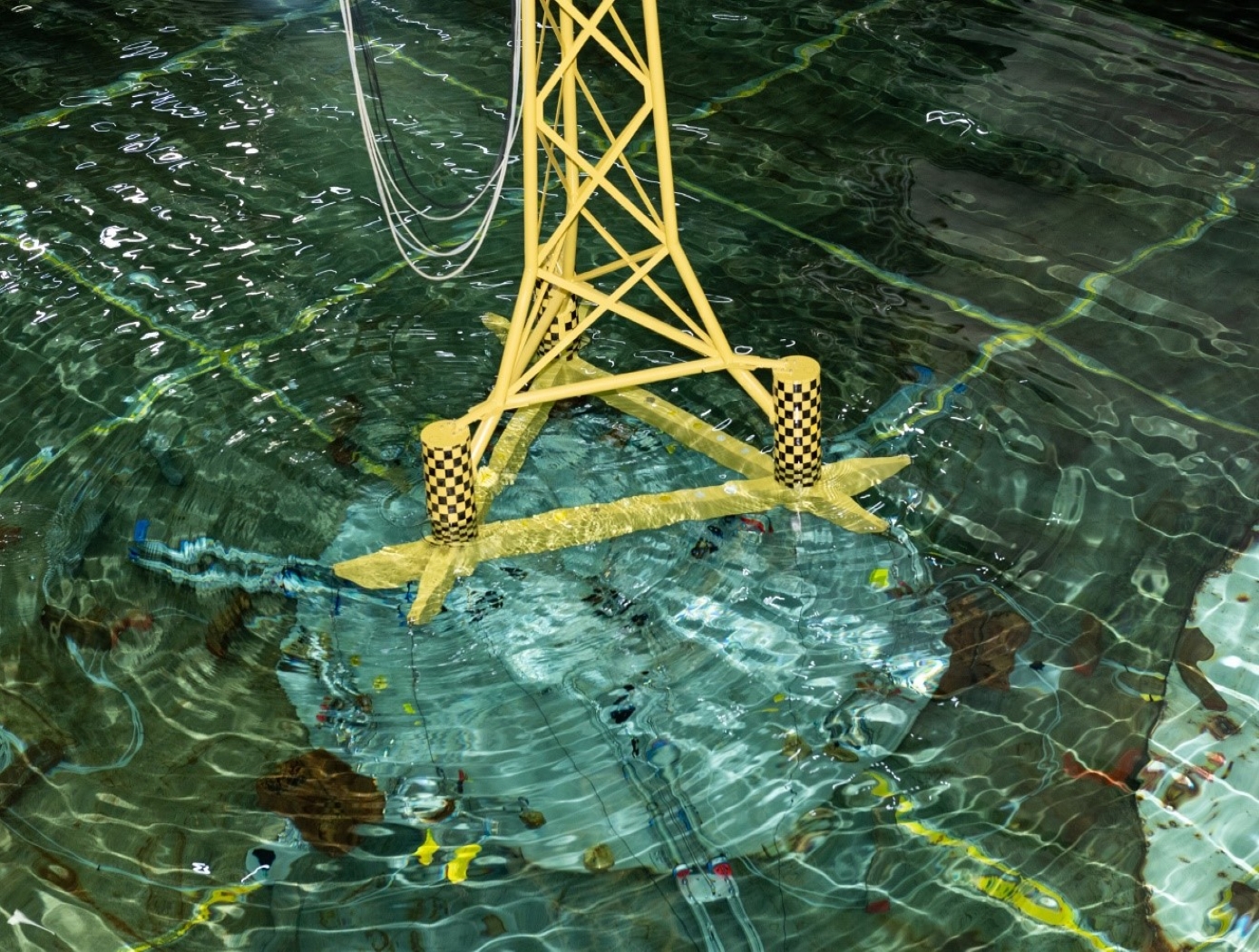
Tension Element Vibration Damping
NASAs Tension Element Vibration Damping technology presents a novel method of managing the dynamic behavior of structures by capturing the vibrational displacement of the structure via a connecting link and using this motion to drive a resistive element. The resistive element then provides a force feedback that manages the dynamic behavior of the total system or structure. The damping force feedback can be a tensile or compressive force, or both. Purely tensile force has advantages for packaging and connection alignment flexibility while combined tensile/compression forces have the advantage of providing damping over a complete vibratory cycle.
This innovation can be readily applied to existing structures and incorporated into any given design as the connecting element is easily affixed to displacing points within the structure and the resistive element to be located in available space or a convenient location. The resistive element can be supplied by any one of either hydraulic, pneumatic or magnetic forces. As such the innovation can provide a wide range of damping forces, a linear damping function and/or an extended dynamic range of attenuation, providing broad flexibility in configuration size and functional applicability.
NASA-built prototypes have been shown to be highly effective on a 170-foot long wind turbine blade in test beds at the University of Maine.
.jpg)
Tool for Rapid Identification of TCE in Plants
Plant uptake of TCE from contaminated groundwater is a well-known phenomenon. During the photosynthesis process, plants metabolize the TCE into a byproduct called trichloroacetic acid (TCAA). TCAA has been found to be a good indicator (or surrogate) molecule for the presence of TCE because it is more stable than TCE in plants. The hyperspectral estimator is being designed to detect TCAA. The method uses a white light that is directed at the surface of a plant's leaf. The interaction between the light and the leaf produces spectral signatures that are captured using a detector. A processor that will be coupled to the detector will compare these signatures to a library/database of signatures known to be indicators of the presence of TCAA (and thus TCE). The figure below on the left shows hyperspectral images captured using the method for leaves dosed with TCE over various time periods. These images are examples of response signatures that will eventually be built into the device's reference library/database. Proof-of-concept testing has shown that the hyperspectral estimator is capable of estimating the presence/absence of TCE in plant leaves with an accuracy of 80%. Efforts are now underway to further improve the accuracy of this method and to prototype the technology. The figure below on the right shows a diagram of the planned device.
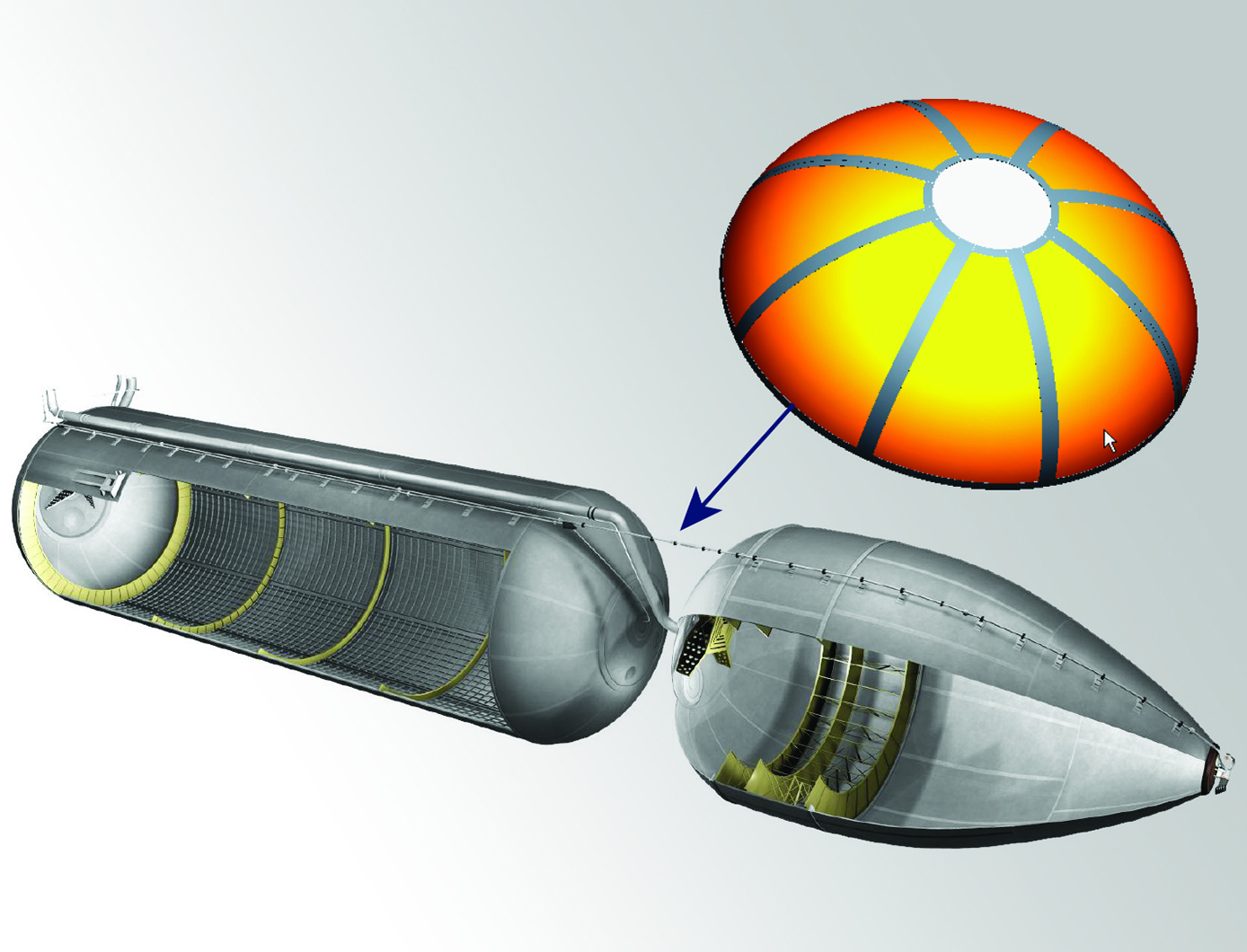
Improving Formability of Al-Li Alloys
Via this NASA innovation, a product is first heated to a temperature within the range of 204 to 343 degrees C for an extended soak of up to 16 hours. The product is then slowly heated to a second temperature within the range of 371 to 482 degrees C for a second soak of up to 12 hours. Finally, the product is slowly cooled to a final soak temperature of 204 to 343 degrees C before cooling to room temperature. The product so treated will exhibit greatly improved formability.
To date, the low formability issue has limited the use of lightweight Al-Li alloys for large rocket fuel tank dome applications. Manufacturing a dome by stretch forming typically requires multiple panels as well as multiple welding and inspection steps to assemble these panels into a full-scale fuel tank dome. Complex tensile and bending stresses induced during the stretch forming operations of Al-Li alloys have resulted in high rates of failure for this process. To spin form a large rocket dome, the spin blank must be prepared by joining smaller plates together using friction stir welding. However, friction stir welding produces a distinct metallurgical structure inside and around the friction stir weld that makes it very susceptible to cracking during spin forming.
.jpg)
Fluid-Filled Frequency-Tunable Mass Damper
NASA MSFC’s Fluid-Filled Frequency-Tunable Mass Damper (FTMD) technology implements a fluid-based mitigation system where the working mass is all or a portion of the fluid mass that is contained within the geometric configuration of either a channel, pipe, tube, duct and/or similar type structure. A compressible mechanism attached at one end of the geometric configuration structure enables minor adjustments that can produce large effects on the frequency and/or response attributes of the mitigation system.
Existing fluid-based technologies like Tuned Liquid Dampers (TLD) and Tuned Liquid Column Dampers (TLCD) rely upon the geometry of a container to establish mitigation frequency and internal fluid loss mechanisms to set the fundamental mitigation attributes. The FTMD offers an innovative replacement since the frequency of mitigation and mitigation attributes are established by the compressible mechanism at the end of the container. This allows for simple alterations of the compressible mechanism to make frequency adjustments with relative ease and quickness.
FTMDs were recently successfully installed on a building in Brooklyn, NYC as a replacement for a metallic TMD, and on a semi-submersible marine-based wind turbine in Maine.
The FTMD technology is available for non-exclusive licensing and partially-exclusive licensing (outside of building construction over 300 feet).
View more patents