Search
Robotics Automation and Control
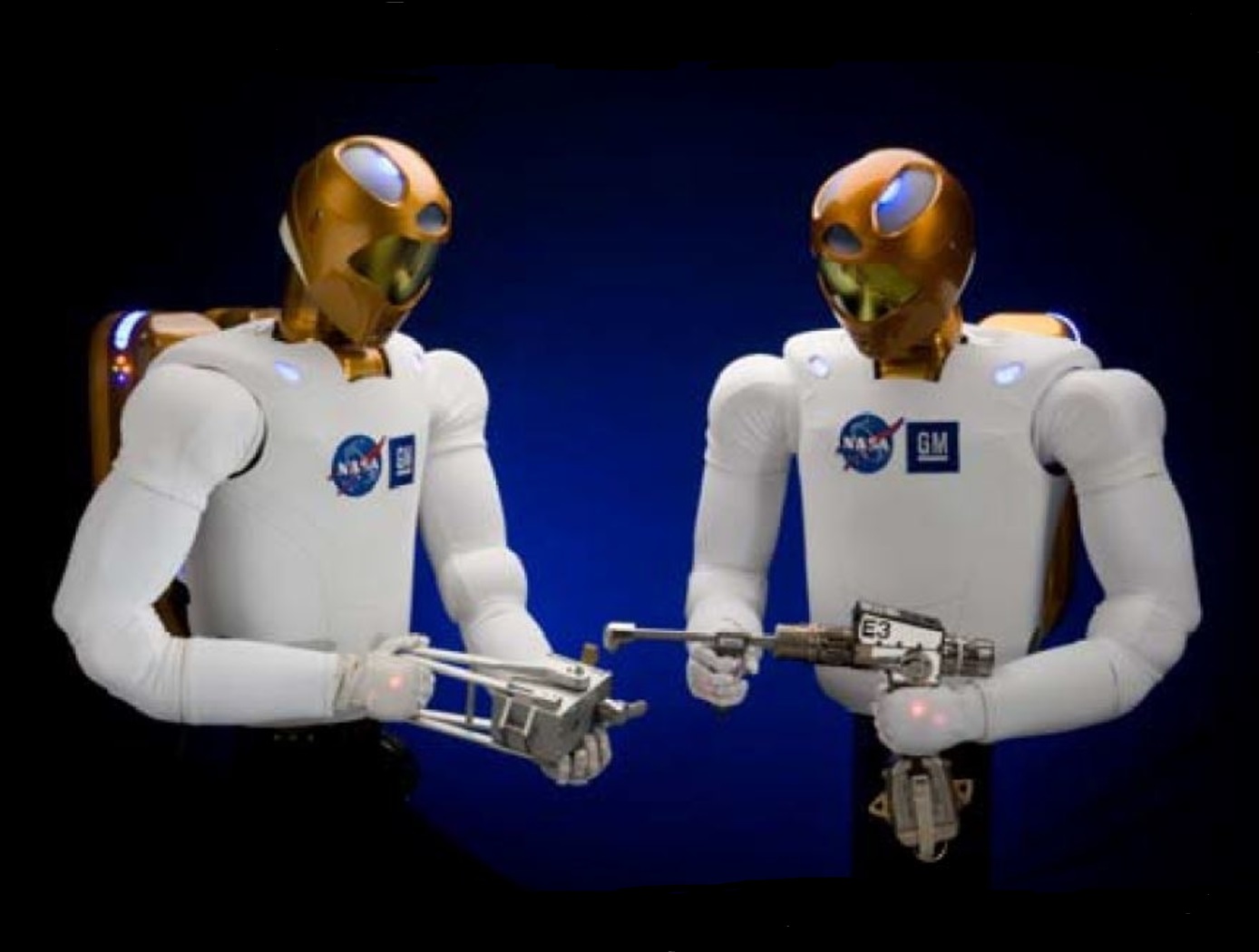
Advanced Humanoid Robotic Arm Technologies
R2 uses brushless DC motors, harmonic drive gear reductions, and electromagnetic failsafe brakes as the building blocks for the powerful, torque-dense actuators in its human-scale, 5 DoF upper arms. Moreover, the use of series elastic actuators and novel tension sensing & control systems represent some of the most innovative technologies present in the humanoid robotic arms of R2.
Series Elastic Actuators (SEAs): R2’s SEAs achieve fine torque sensing at each of its joints without sacrificing strength or payload capacity. Such capabilities are enabled through the development of several advanced technologies. Specifically, novel planar torsion springs (U.S. Patent No. 8,176,809) are integrated into each rotary series elastic actuator (U.S. Patent No. 8,291,788), while two absolute angular position sensors, calibrated using a novel technique (U.S. Patent No 8,250,901), measure the deflection of each spring. Force and Impedance Control Systems (U.S. Patent No. 8,525,460): These systems use position sensor signals for sending position data to an embedded processor that determines the positional orientation of the load relative to a motor shaft and its related torque on a string. A FPGA-based controller (U.S. Patent No. 8,442,684) provides a high-speed (10 KHz) control loop for the electric motor and gear reduction assembly present in R2 joints.
Tension Sensing & Control of Tendon-Based Robotic Manipulators: NASA has also developed technologies to provide tension sensing & control of humanoid robotic arms. First, a tendon tension sensor (U.S. Patent No. 8,371,177) measures strain on tendons (strings) employed in robotic arms. A novel calibration system (U.S. Patent No. 8,412,378) calibrates the tendon tension sensors. Finally, joint space impedance control systems (U.S. Patent Nos. 8,170,718 & 8,060,250) provide closed-loop control of joint torques or joint impedances without inducing dynamic coupling between joints, as well as programmable Cartesian arm stiffness.
Materials and Coatings

Precipitation Strengthened
Ni-Ti-Pd Shape Memory Alloys
Shape memory alloys (SMAs) are metals that can return to their original shape following thermal input and are largely used as actuators for various applications across industries including space, aeronautics, automotive, and biomedical. These alloys can require long processing times to stabilize through repeated training cycles and suffer from loss of strength and stability during use. Precipitation strengthening (using heat treatments to grow small nanoscale regions of distinct metal phases within the base alloy) is one way to mitigate these issues.
The NASA inventors have combined a modification of typical NiTi compositions by introducing Palladium (Pd) and small amounts of other metals and specific heat treatments to produce a novel SMA with improved properties. Specifically, the alloy is inherently stable, reducing both the need for extended processing times to stabilize the metal and the possibility of failure during high numbers of actuation cycles. Further, the SMA is specifically designed to have significantly lower hysteresis (the temperature difference between the heating and cooling) than current state of the art SMAs, i.e., at or below 10°C compared to 20°C or above. These properties combine for a SMA with enhanced properties usable across various industries and applications for reliable actuation.
The related patent is now available to license. Please note that NASA does not manufacturer products itself for commercial sale.
mechanical and fluid systems

Shape Memory Alloy (SMA)-Enabled Actuators
Actuators typically have large footprints and mass to meet the power output needed for operation, leading to design hurdles for aircraft and space applications. Innovators at NASA Glenn developed two novel actuators with different configurations of tubes of SMA to provide rotary output. The SMA tubes are deformed in their martensitic condition and when exposed to a thermal stimulus, the tubes will revert to their original state while providing rotary motion.
One variation of the innovation nests the SMA tubes within a rotary actuator imparting several technical benefits. Nested SMA tubes can decrease the length of the actuator while achieving the same twist angle. For the same actuator length, a nested configuration of SMA tubes can multiply the twist angle and improve the power output. A second variation utilizes SMA components as transmission elements in a ring drive gear to enable continuous rotation in one direction. Previous similar SMA actuators rotate in one direction while heating and the other while cooling, which can limit the output of the rotary actuator. The innovation developed by NASA allows for continuous rotation in ANY direction, thereby allowing the rotational output capability to be independent from the amount of cyclic angular twist provided by the SMA tubes.
Materials and Coatings
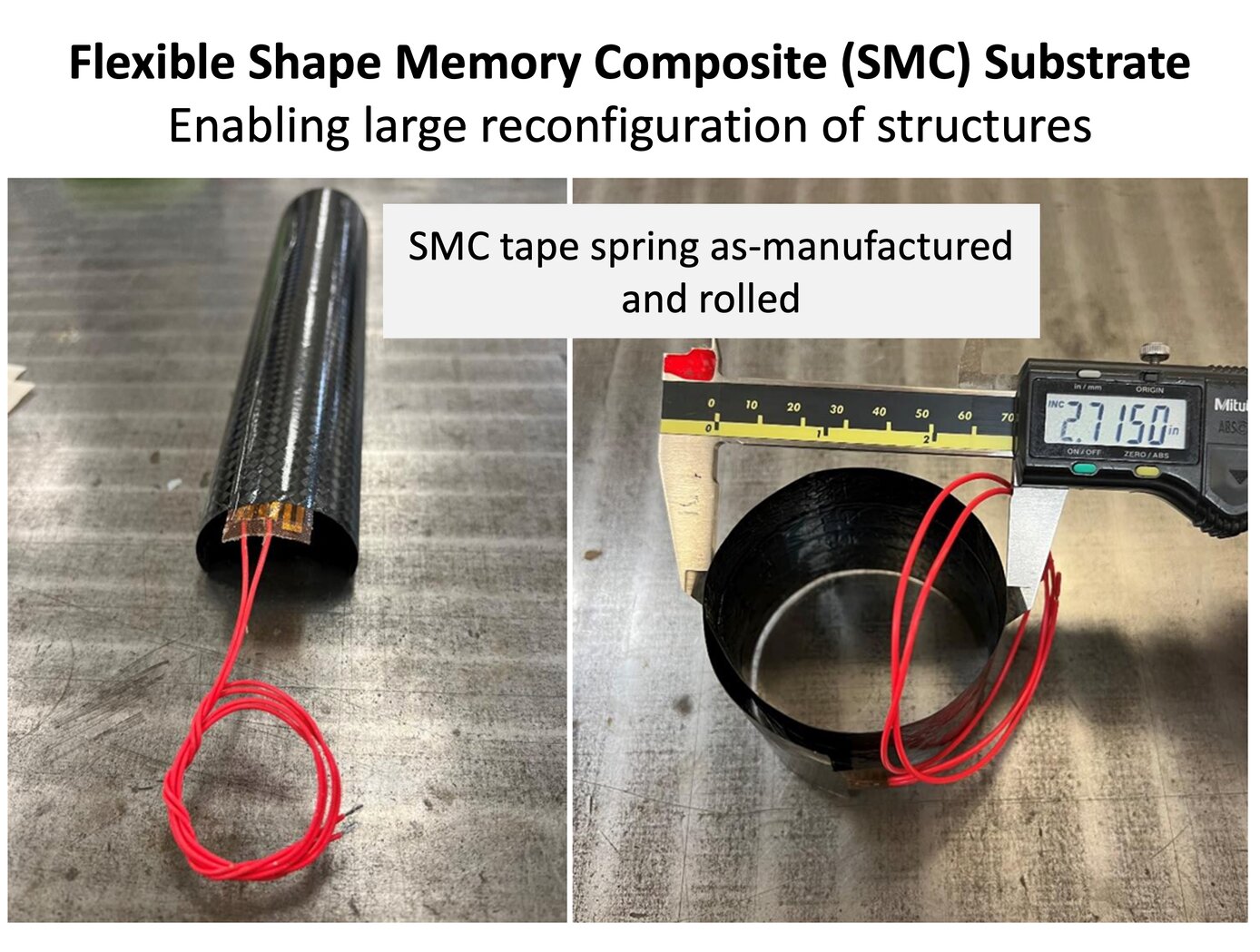
Novel Shape Memory Composite Substrate
The new SMC substrate has four components: a shape memory polymer separately developed at NASA Langley; a stack of thin-ply carbon fiber sheets; a custom heater and heat spreader between the SMC layers; and integrated sensors (temperature and strain). The shape memory polymer allows the as-fabricated substrate to be programmed into a temporary shape through applied force and internal heating. In the programmed shape, the deformed structure is in a frozen state remaining dormant without external constraints. Upon heating once more, the substrate will return slowly (several to tens of seconds) to the original shape (shown below).
The thin carbon fiber laminate and in situ heating solve three major pitfalls of shape memory polymers: low actuation forces, low stiffness and strength limiting use as structural components, and relatively poor heat transfer. The key benefit of the technology is enabling efficient actuation and control of the structure while being a structural component in the load path. Once the SMC substrate is heated and releases its frozen strain energy to return to its original shape, it cools down and rigidizes into a standard polymer composite part. Entire structures can be fabricated from the SMC or it can be a component in the system used for moving between stowed and deployed states (example on the right). These capabilities enable many uses for the technology in-space and terrestrially.
sensors

Split-Ring Torque Sensor
The SRTS enables measurement of position, velocity, and torque of a rotating system (e.g., actuator, motor, crankshaft, rotor, etc.) using two optical sensors and a single, custom-designed split-ring rather than the standard dual-ringed systems commonly used for similar applications. The split-ring is comprised of two structural arcs positioned in a concentric, coplanar relationship, wherein each arc is attached to a component capable of rotation (e.g., a lower leg and upper leg, where the SRTS acts as a knee). The two arcs contain indications or codes on their outer surfaces that are read by the optical sensors to determine the relative deflection of the structural arcs as they rotate.
The SRTS configuration discussed above is limited to 180-degree applications. The addition of a third structural arc and a third optical reader, however, would enable 360-degree functionality.
Tests have shown the SRTS has a high degree of tolerance to temperature differences and provides higher resolution measurements than competing technologies.
Mechanical and Fluid Systems

Active Flow Control System for Simple-hinged Flaps
Although simple-hinged flaps represent optimal high-lift systems for reducing cruise drag, previous attempts to design flow control systems enabling such technology in transport aircraft have been unsuccessful. This is largely because such systems generally require a tradeoff between (a) the ability to achieve the required lift performance, and (b) possessing sufficiently low pneumatic power to enable feasible aircraft system integration (i.e., avoiding excess weight penalties associated with high pneumatic power). For example, electrically powered AFC systems (e.g., plasma actuators, synthetic jet actuators) have practical power requirements, but with limited control authority, making such systems ineffective for highly deflected flaps. On the other hand, circulation control systems can provide necessary lift for airfoils or wings with high flap deflections, but require too much pneumatic power for aircraft integration. NASA’s HELP AFC system represents a breakthrough in flow separation control technology – to efficiently achieve necessary lift performances while requiring low pneumatic power relative to alternative flow control techniques.
NASA’s HELP AFC system uses a unique two-row actuator approach comprised of upstream sweeping jet (SWJ) actuators and downstream discrete jets, which share the same air supply plenum. The upstream (row 1) SWJ actuators provide good spanwise flow-control coverage with relatively mass flow, effectively pre-conditioning the boundary layer such that the downstream (row 2) discrete jets achieve better flow control authority. The two row actuator system, working together, produce a total aerodynamic lift greater than the sum of each row acting individually. The result is a system that generates sufficient lift performance for simple-hinged flaps with pneumatic power requirements low enough to enable aircraft integration.