Search
aerospace
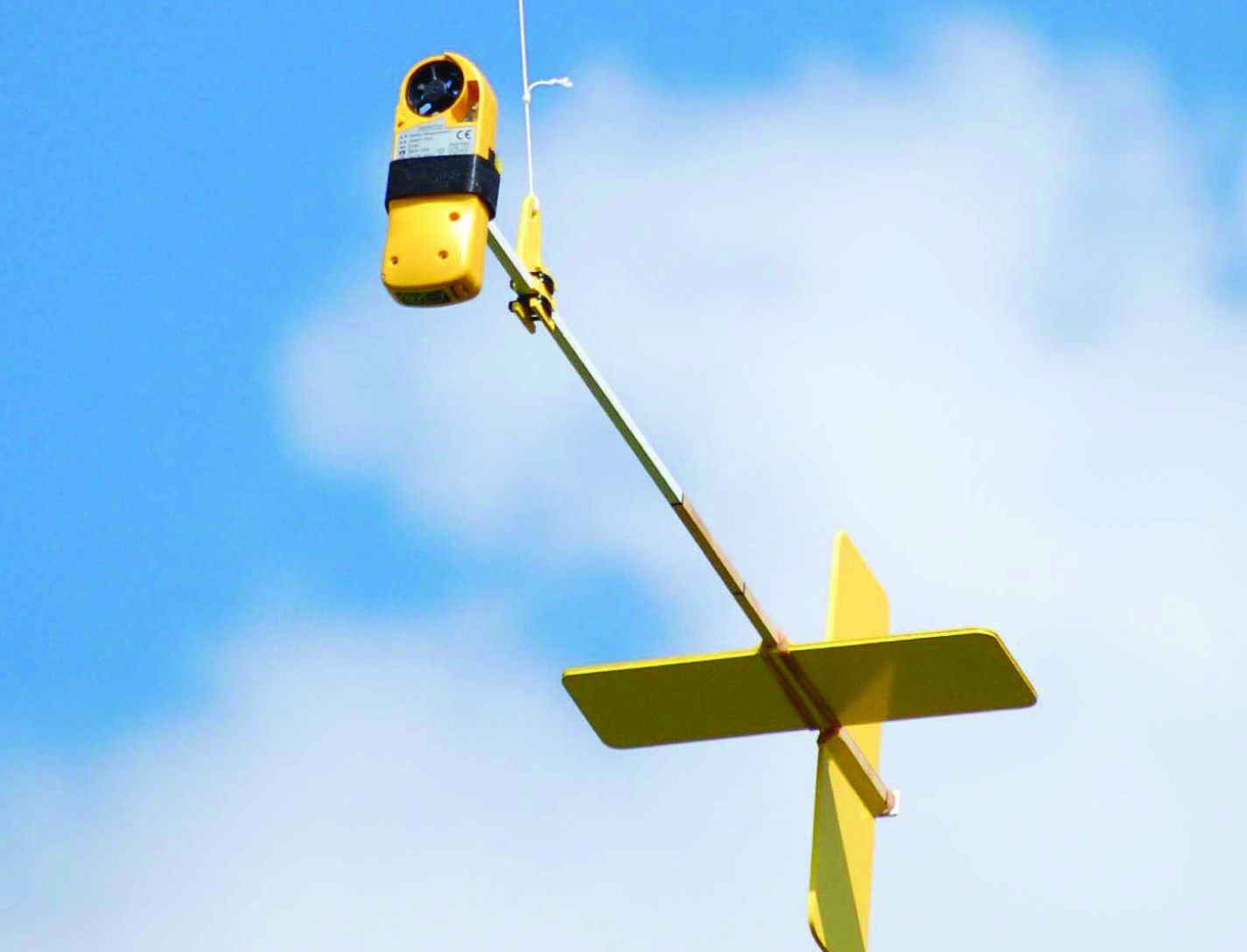
AeroPod
The AeroPods design for steadying and damping payloads includes the use of a tail boom and fin combination. It is a novel design and provides a relatively simple alternative to the traditional methods for suspending equipment from kites or blimps.
The AeroPod is superior to the traditional Picavet pulley-style suspension system for kite-flight because its light weight, simple to construct, and has no moving parts. Furthermore, the AeroPod design is advantageous to the traditional tethered blimp suspension technique where tether motion is translated directly to the sensor system because the AeroPod is free of direct motions of the tether.
Optics
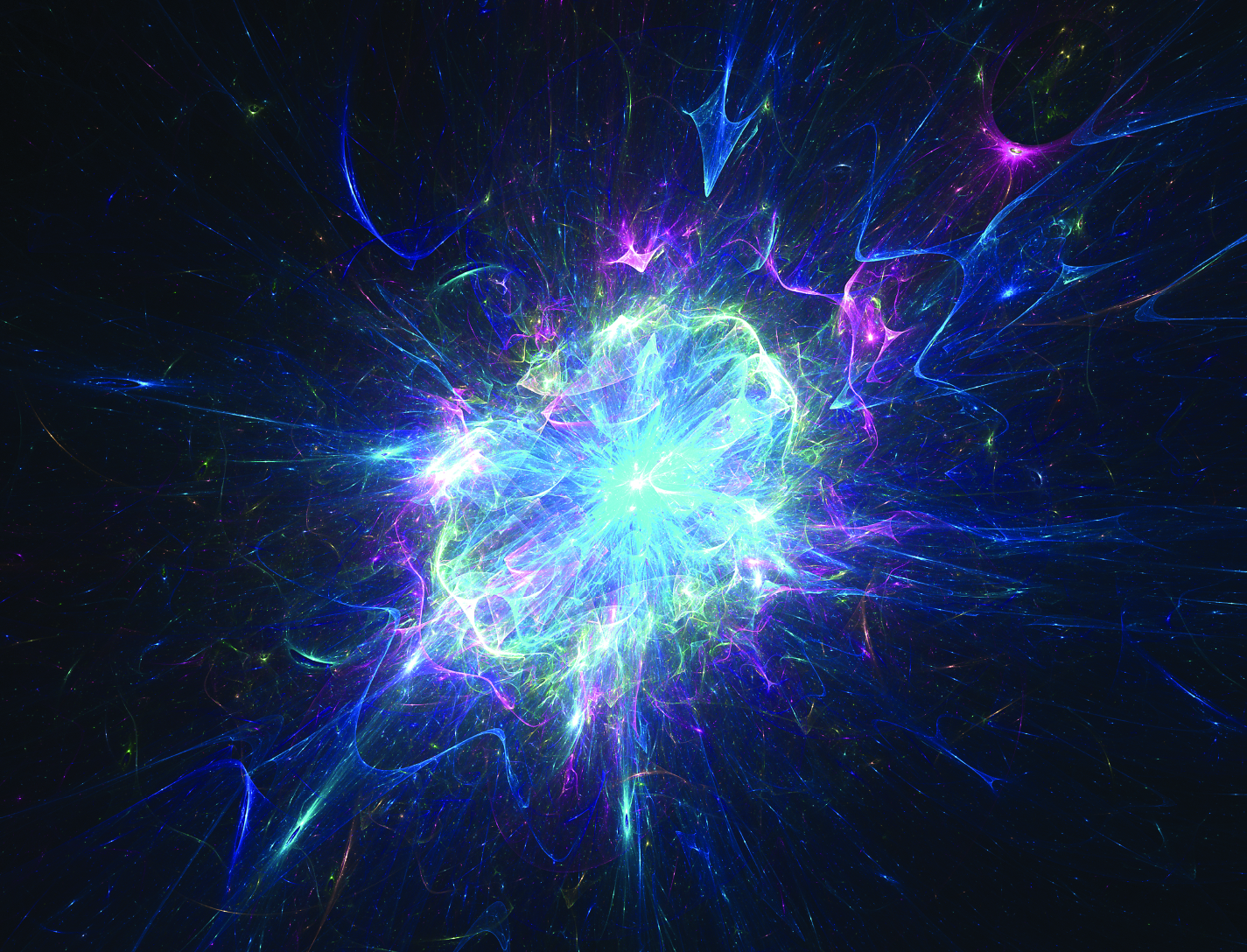
Nested Focusing Optics for Compact Neutron Sources
Conventional neutron beam experiments demand high fluxes that can only be obtained at research facilities equipped with a reactor source and neutron optics. However, access to these facilities is limited. The NASA technology uses grazing incidence reflective optics to produce focused beams of neutrons (Figure 1) from compact commercially available sources, resulting in higher flux concentrations. Neutrons are doubly reflected off of a parabolic and hyperbolic mirror at a sufficiently small angle, creating neutron beams that are convergent, divergent, or parallel. Neutron flux can be increased by concentrically nesting mirrors with the same focal length and curvature, resulting in a convergence of multiple neutron beams at a single focal point. The improved flux from the compact source may be used for non-destructive testing, imaging, and materials analysis.
The grazing incidence neutron optic mirrors are fabricated using an electroformed nickel replication technique developed by NASA and the Harvard-Smithsonian Center for Astrophysics (Figure 2). A machined aluminum mandrel is super-polished to a surface roughness of 3-4 angstroms root mean square and plated with layers of highly reflective nickel-cobalt alloy. Residual stresses that can cause mirror warping are eliminated by periodically reversing the anode and cathode polarity of the electroplating system, resulting in a deformation-free surface. The fabrication process has been used to produce 0.5 meter and 1.0 meter lenses.