Search
Sensors
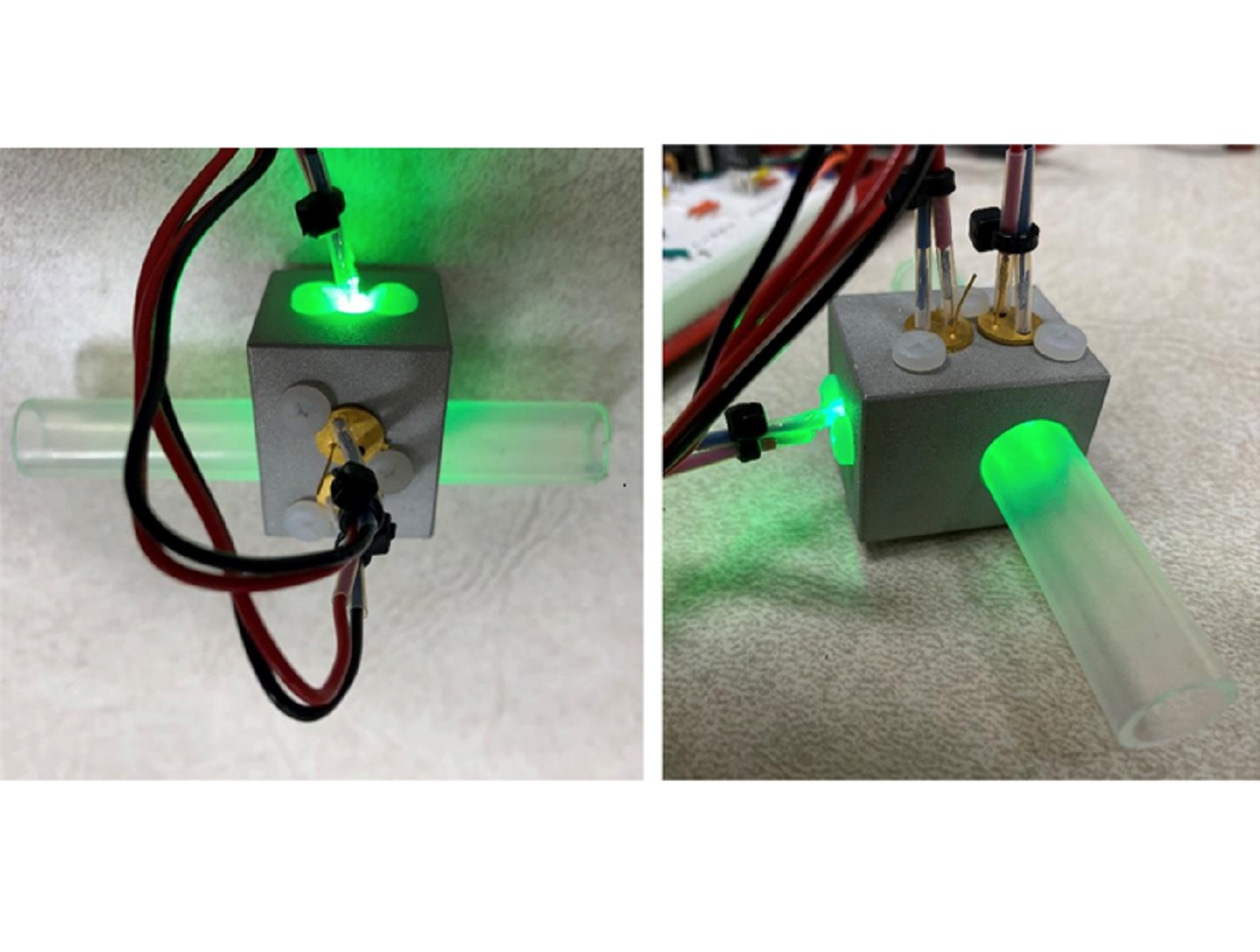
Optical concentration sensor for liquid solution
Typical concentration sensors, like the one initially used in the UWMS, rely on changes in electrical conductivity to measure the concentration of a solution. These measurements using conductivity are prone to voltage drift over time, leading to unreliable measurements as the sensor ages.
The optical sensor developed here uses light scattering to measure the solution concentration without the issue of voltage drift. In this sensor, light from a green LED is passed into the sensor housing where it hits a first detector (i.e., a photodiode) to establish a reference of the amount of light before scattering. Simultaneously, the light from the LED scatters through the pretreat solution and then hits a second photodiode to measure the amount of light after scattering. The difference between the amount of light measured by the two detectors is used to calculate the concentration of the pretreat solution (based upon Beer’s Law). The optical concentration sensor has been demonstrated to effectively measure pretreat concentrations in both still and flowing liquid conditions and is resistant to contamination issues as necessitated by the UWMS.
The optical pretreat concentration sensor is at technology readiness level (TRL) 4 (component and/or breadboard validation in laboratory environment) and is available for patent licensing.
Mechanical and Fluid Systems
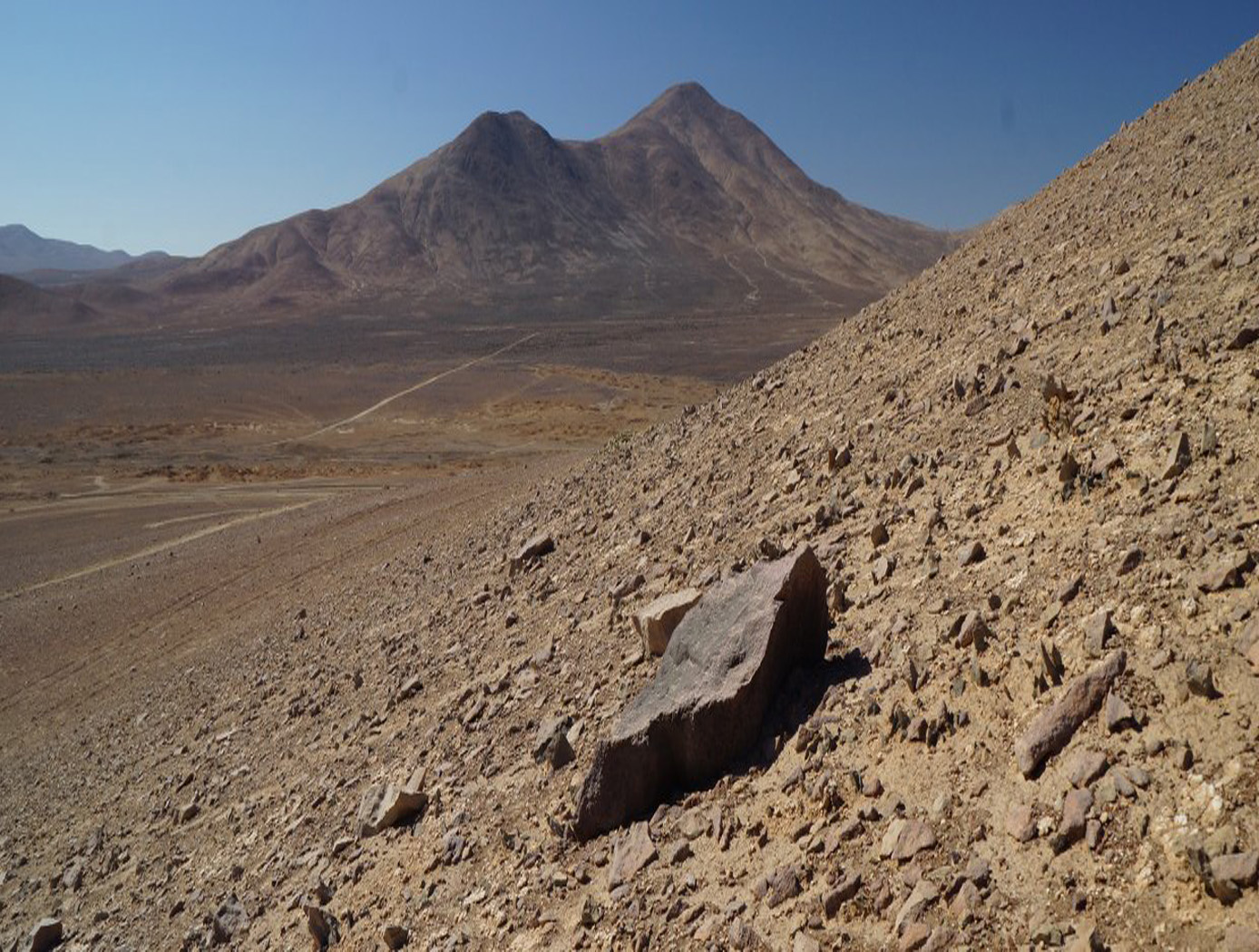
Extractor for Chemical Analysis of Lipid Biomarkers in Regolith (ExCALiBR)
The technology provides miniaturized techniques for extracting trace amounts of organic molecules (lipids) from natural samples. It operates as an autonomous, miniaturized fluidic system, integrating lab techniques for lipid analysis while minimizing reagent volumes and concentrating organics for analysis, thereby increasing signal-to-noise ratios by orders of magnitude. The non-aqueous fluidic system described herein for astrobiological and life-detection missions (either in situ or returned sample) is configured to extract lipid organics from regolith using (1) a fluidic sample processor made of materials compatible with organic solvents and (2) a machine-learning system to select processing steps and parameters to maximize lipid yield. A critical gap is bridged by integrating technologies into a system that replicates analytical lab procedures autonomously on a spaceflight instrument scale with fidelity to original lab techniques. Automated fluidic devices combine controlled handling of liquids with sequential operations and parallelization of replicate processes. By designing such systems to closely interface with both sample-delivery and analytical measurement systems, laboratory analyses are automated. The technology adapts best practice laboratory methods for lipid analysis, overcoming analytical challenges like low organic abundance, interference of minerals/salts, and degradation of origin-diagnostic molecular structures. The extraction and concentration techniques from rock/soil samples can be applied to any biomarkers by changing the solvent, temperature, and agitation.
Sensors

Hybrid carbon nanotube-gold nanoparticle composite for Nitric Oxide (NO) detection
A hybrid thin film is fabricated by a simple drop-casting method. Functionalized single-walled carbon nanotubes (SWCNTs) and gold nanoparticles (AuNPs) with a diameter of ≈15 nm are drop-casted onto a printed circuit board (PCB) substrate equipped with interdigitated electrodes. The addition of AuNPs to the carbon nanotube networked films enhance sensitivity and lower the detection limit to low parts-per-billion (ppb) concentrations. The gold particle to carbon nanotube ratio is optimized to find the optimum gold nanoparticle loading.
The composite films were tested in both air and nitrogen environments across a wide relative humidity range (0-97%), which is suitable for dissolved Nitric Oxide (NO) detection in sea water for oceanographic study and for human breath analysis in medical diagnosis. The sensors exhibited high selectivity, particularly to NO, outperforming other tested gases. Notably, the sensor reliably detected NO at 10 ppb levels with response times within 10 seconds and recovery time around 1 minute, showcasing excellent reproducibility across sensors and operational efficiency within diverse humidity conditions.
sensors

Solid State Carbon Dioxide (CO2) Sensor
The technology is a solid state, Carbon Dioxide (CO2) sensor configured for sensitive detection of CO2 having a concentration within the range of about 100 Parts per Million (ppm) and 10,000 ppm in both dry conditions and high humidity conditions (e.g., > 80% relative humidity). The solid state CO2 sensor achieves detection of high concentrations of CO2 without saturation and in both dynamic flow mode and static diffusion mode conditions. The composite sensing material comprises Oxidized Multi-Walled Carbon Nanotubes (O-MWCNT) and a metal oxide, for example O-MWCNT and iron oxide (Fe2O3) nanoparticles. The composite sensing material has an inherent resistance and corresponding conductivity that is chemically modulated as the level of CO2 increases. The CO2 gas molecules absorbed into the carbon nanotube composites cause charge-transfer and changes in the conductive pathway such that the conductivity of the composite sensing material is changed. This change in conductivity provides a sensor response for the CO2 detection. The solid state CO2 sensor is well suited for automated manufacturing using robotics and software controlled operations. The solid state CO2 sensor does not utilize consumable components or materials and does not require calibration as often as conventional CO2 sensors. Since the technology can be easily integrated into existing programmable electronic systems or hardware systems, the calibration of the CO2 sensor can be automated.