Search
aerospace
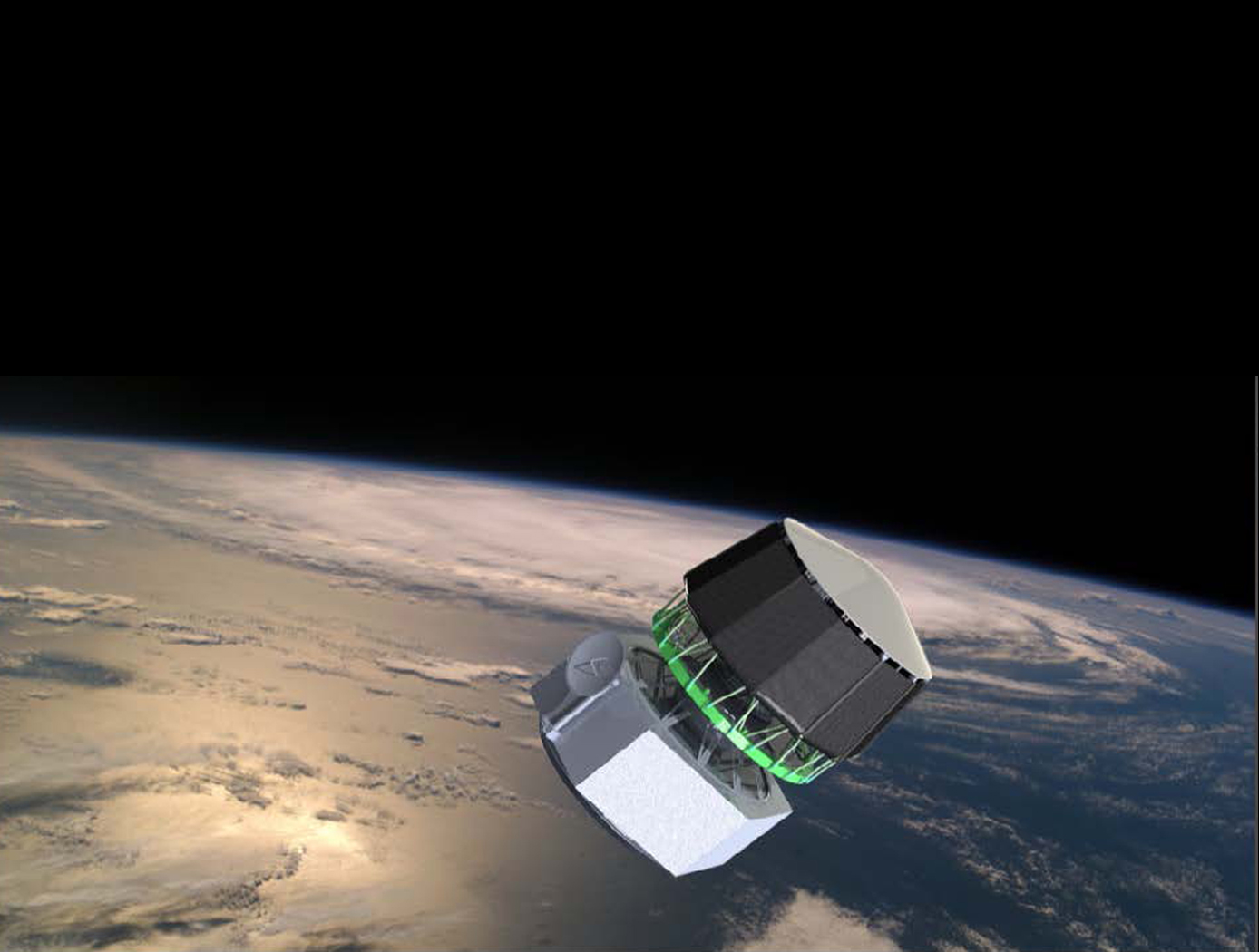
Transformable Hypersonic Aerodynamic Decelerator
The invention allows the deployment of a large aerodynamic decelerator relative to the size of its launch vehicle, which is controllable and can be transformed into a landing system. A structure composed of a radial assembly of ribs and struts in a four bar linkage arrangement fits inside a launch vehicle shroud, expands into a deployed size, and permits rotation about a pivot point along the vehicle axis. The mechanism that deploys the decelerator surface, doubles as the actuation/control mechanism, and triples as the payload surface leveling system. The design permits the use of conformable thermal protection systems at the central part and a flexible TPS, 3-D woven carbon fabric, as skin in the majority of the regions of the aeroshell entry system. The fabric handles both the heat and mechanical load generated during entry. This system is very mass competitive with other lightweight systems such as inflatable and rigid decelerators and is believed to be more reliable and testable at sub-scale. Once the payload reaches its destination, the decelerator structure leverages atmospheric drag to slow the craft from hypersonic travel speeds to an appropriate landing velocity. The decelerator can be actuated during descent to generate lift and steer the payload to its intended destination. Retro propulsion engines provide the final deceleration just before landing, and the decelerator structure is inverted to act as a landing platform and help minimize the impact of landing load.
electrical and electronics
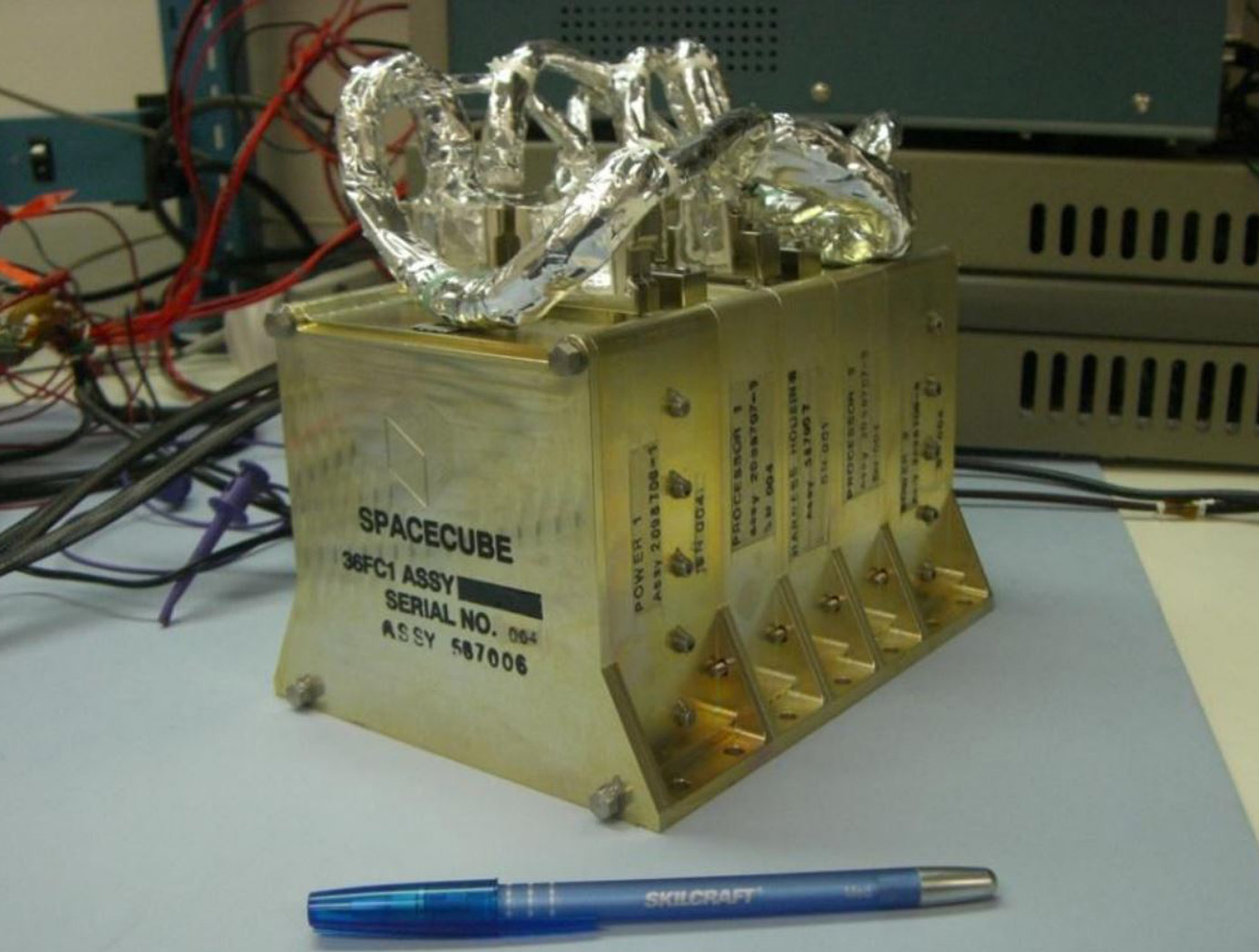
SpaceCube
Next generation instruments are capable of producing data at rates of 108 to 1011 bits per second, and both their instrument designs and mission operations concepts are severely constrained by data rate/volume. SpaceCube is an enabling technology for these next generation missions.
SpaceCube has demonstrated enabling capabilities in Earth Science, Planetary, Satellite Servicing, Astrophysics and Heliophysics prototype applications such as on-board product generation, intelligent data volume reduction, autonomous docking/landing, direct broadcast products, and data driven processing with the ability to autonomously detect and react to events. SpaceCube systems are currently being developed and proposed for platforms from small CubeSats to larger scale experiments on the ISS and standalone free-flyer missions, and are an ideal fit for cost constrained next generation applications due to the tremendous flexibility (both functional and interface compatibility) provided by the SpaceCube system.
Robotics Automation and Control

Advanced Humanoid Robotic Hand Technologies
The R2 hand and forearm assembly represents the cutting edge of humanoid robotics technologies. The highly modular design provides significant improvements over prior humanoid robotic hands, especially in the areas of strength, speed, sensing, and ability to approximate human grasps.
<i>Hand, Finger, and Wrist Assembly Design:</i> The robotic humanoid lower arm design (U.S. Patent No. 9,505,134) includes novel robotic finger (U.S. Patent No. 8,562,049), thumb (U.S. Patent No. 8,424,941), and wrist (U.S. Patent No. 8,498,741) assemblies.
<i>Actuation & Control System:</i> A novel finger actuation system (U.S. Patent No. 8,467,903) – comprised of an actuator, tendon, conduit, tension sensor (U.S. Patent No. 8,371,177), and terminator – is perhaps the primary enabling technology for R2’s compact, high performance robotic hand. The actuation system is packaged in the wrist (U.S. Patent No. 8,401,700) and reduces the number of actuators, providing significant space savings. Control systems include methods for tensioning (U.S. Patent Nos. 8,412,376, 8,618,762, & 8,056,423) and controlling torque (U.S. Patent No. 8,565,918) of the tendon-driven robotic fingers. The finger actuation control system (U.S. Patent No. 8,489,239) can operate using force- or position-based control laws.
<i>Tactile System:</i> R2’s hands feature an innovative tactile system that grant the robot a sense of touch (e.g., measurement of external contact forces, shear force, and slippage of objects held in the hand) – an important requirement for robots designed to perform complex tasks in an automated fashion. The tactile system is enabled by novel six degree of freedom (DoF) force torque sensors (U.S. Patent No. 7,784,363), three of which are integrated into the fingers (at the proximal, medial, and distal phalanges) and two in the thumb (medial and distal phalanges). A calibration system (U.S. Patent No. 8,265,792) ensures the sensors maintain high accuracy throughout operation.
<i>Autonomous Grasping:</i> A novel grasp assist device (U.S. Patent No. 9,878,452 & 9,067,319) enables reliable, autonomous interaction with a broad range of objects (e.g., tools). A particle filter-based contact state estimation device (U.S. Patent No. 8,280,837) performs object localization and characterization.
Robotics Automation and Control

Visual Inspection Posable Invertebrate Robot (VIPIR)
Initially developed as a close quarters inspection tool capable of accessing hard to reach, tight, or visibly restricted, areas of satellites, the VIPIR system can be used to remotely inspect inaccessible locations such as behind a sheet of thermal blanketing material, into a satellites plumbing, or perhaps even deep inside the otherwise unreachable crevasses of a spacecraft bus. The VIPIR system incorporates a number of subassemblies for incredible operational freedom and capabilities for imaging and dissemination of componentry.
VIPIR’s Video Borescope Assembly (VBA) is a flexible snake-camera capable of multidirectional articulations, making steering and control simple and intuitive for an operator. The VBA also includes at least one imaging sensor and lighting to see in dark, confined spaces. Real-time, high-resolution visual information can be fed back to an operator for live analysis. A reel system extends and retracts the VBA with the use of a spool, and includes position indicators for deployment tracking. The Tendon Management System (TMS), not unlike human tendons, utilizes pulleys and tensioners to articulate the VBA in the confined spaces. A seal system ensures the VBA is free of contamination.
VIPIR underwent space-based testing on the ISS during the Robotic Refueling Phase 2 (RRM-2) mission designed to showcase and test several NASA advanced robotic satellite servicing technologies. During this mission, VIPIR demonstrated state-of-the-art near and midrange inspection capabilities. NASA’s VIPIR system is available for licensing to industry, and may be desirable to companies focused on satellite servicing, on-orbit assembly, and other applications requiring detailed inspection of assets in space.
mechanical and fluid systems
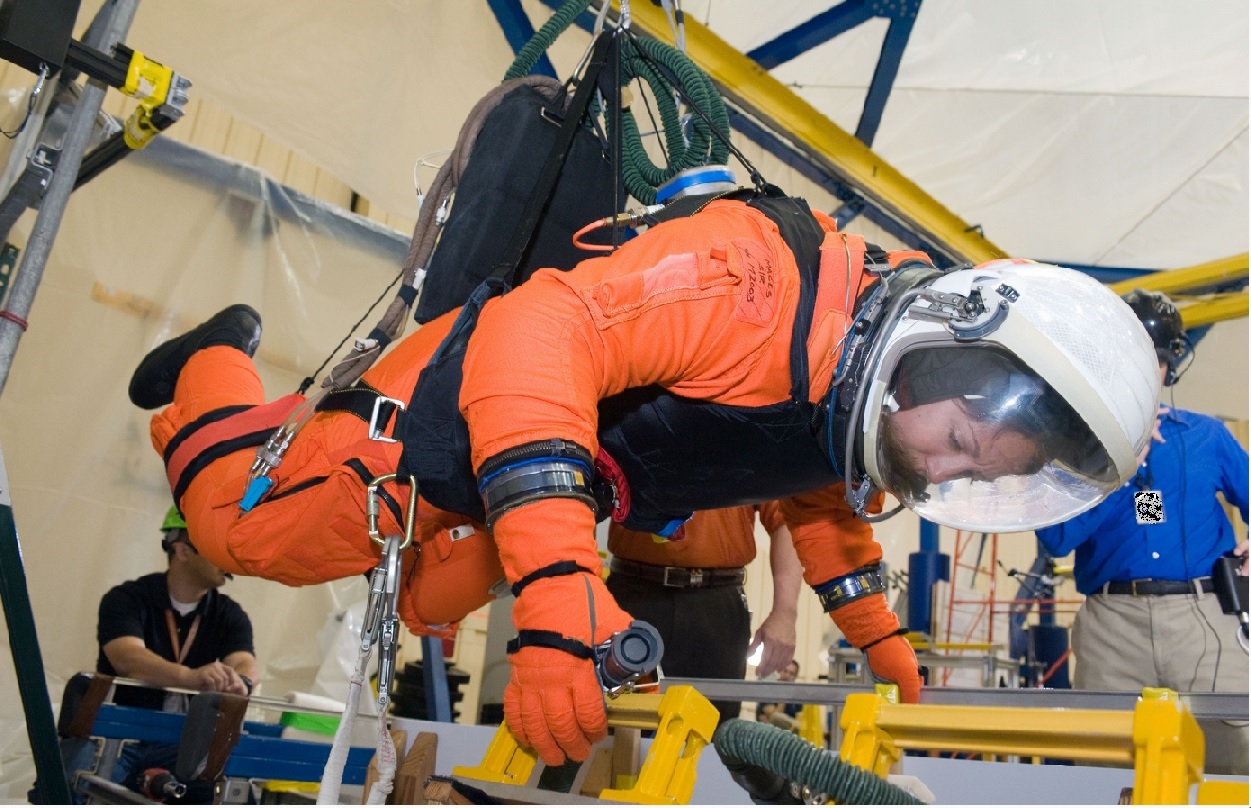
Full-Size Reduced Gravity Simulator For Humans, Robots, and Test Objects
The Active Response Gravity Offload System (ARGOS) provides a simulated reduced gravity environment that responds to human-imparted forces. System capabilities range from full gravity to microgravity. The system utilizes input/feedback sensors, fast-response motor controllers, and custom-developed software algorithms to provide a constant force offload that simulates reduced gravity.
The ARGOS system attaches to a human subject in a gimbal and/or harness through a cable. The system then maintains a constant offload of a portion of the subjects weight through the cable to simulate reduced gravity. The system supports movements in all 3 dimensions consistent with the selected gravity level. Front/back and left/right movements are supported via a trolley on an overhead runway and bridge drive system, and up/down movements are supported via a precisely positioned cable. The system runs at a very high cycle rate, and constantly receives feedback to ensure the human subjects safety.
information technology and software
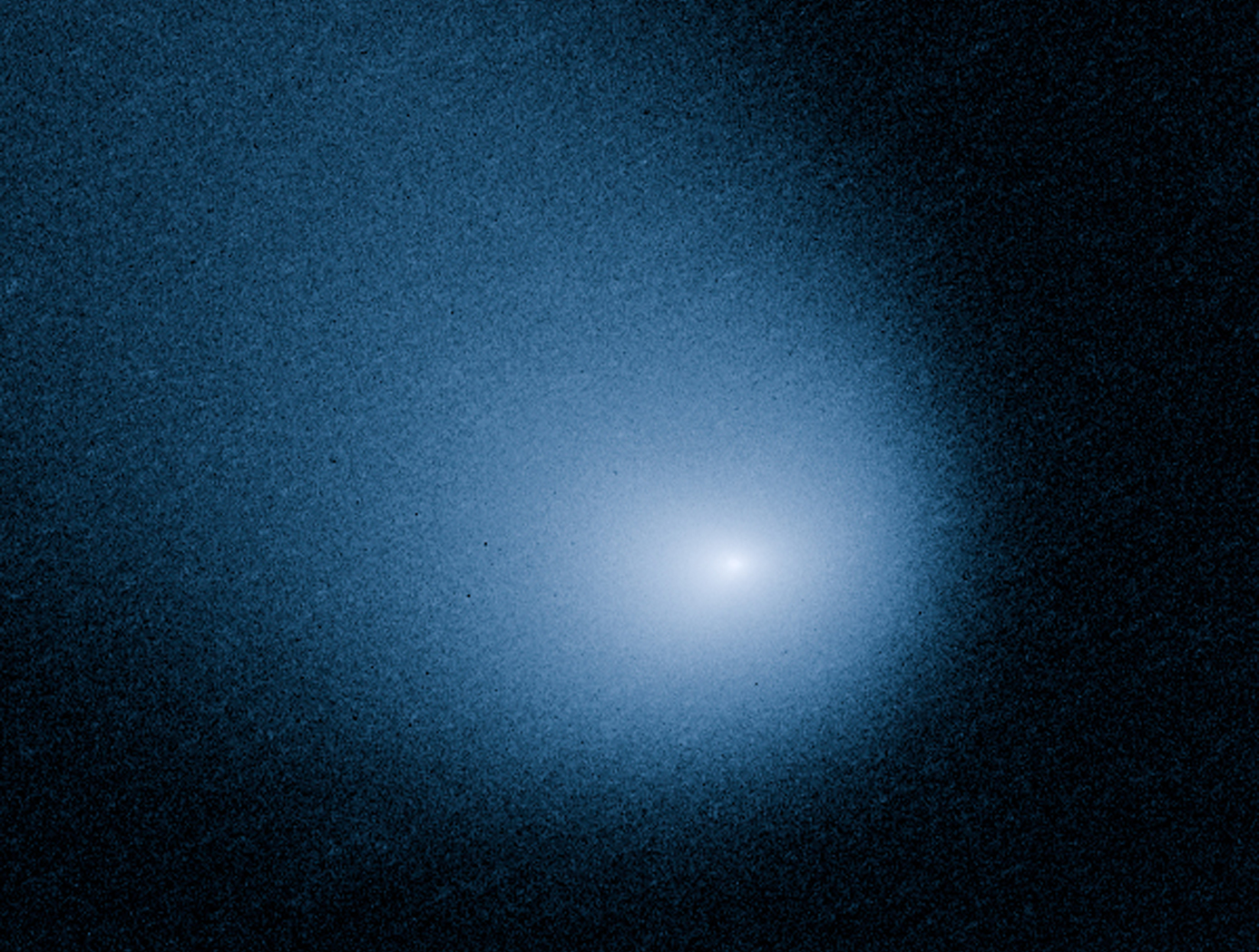
Automata Learning in Generation of Scenario-Based Requirements in System Development
In addition, the higher the level of abstraction that developers can work from, as is afforded through the use of scenarios to describe system behavior, the less likely that a mismatch will occur between requirements and implementation and the more likely that the system can be validated. Working from a higher level of abstraction also provides that errors in the system are more easily caught, since developers can more easily see the big picture of the system.
This technology is a technique for fully tractable code generation from requirements, which has an application in other areas such as generation and verification of scripts and procedures, generation and verification of policies for autonomic systems, and may have future applications in the areas of security and software safety. The approach accepts requirements expressed as a set of scenarios and converts them to a process based description. The more complete the set of scenarios, the better the quality of the process based description that is generated. The proposed technology using automata learning to generate possible additional scenarios can be useful in completing the description of the requirements.
Environment
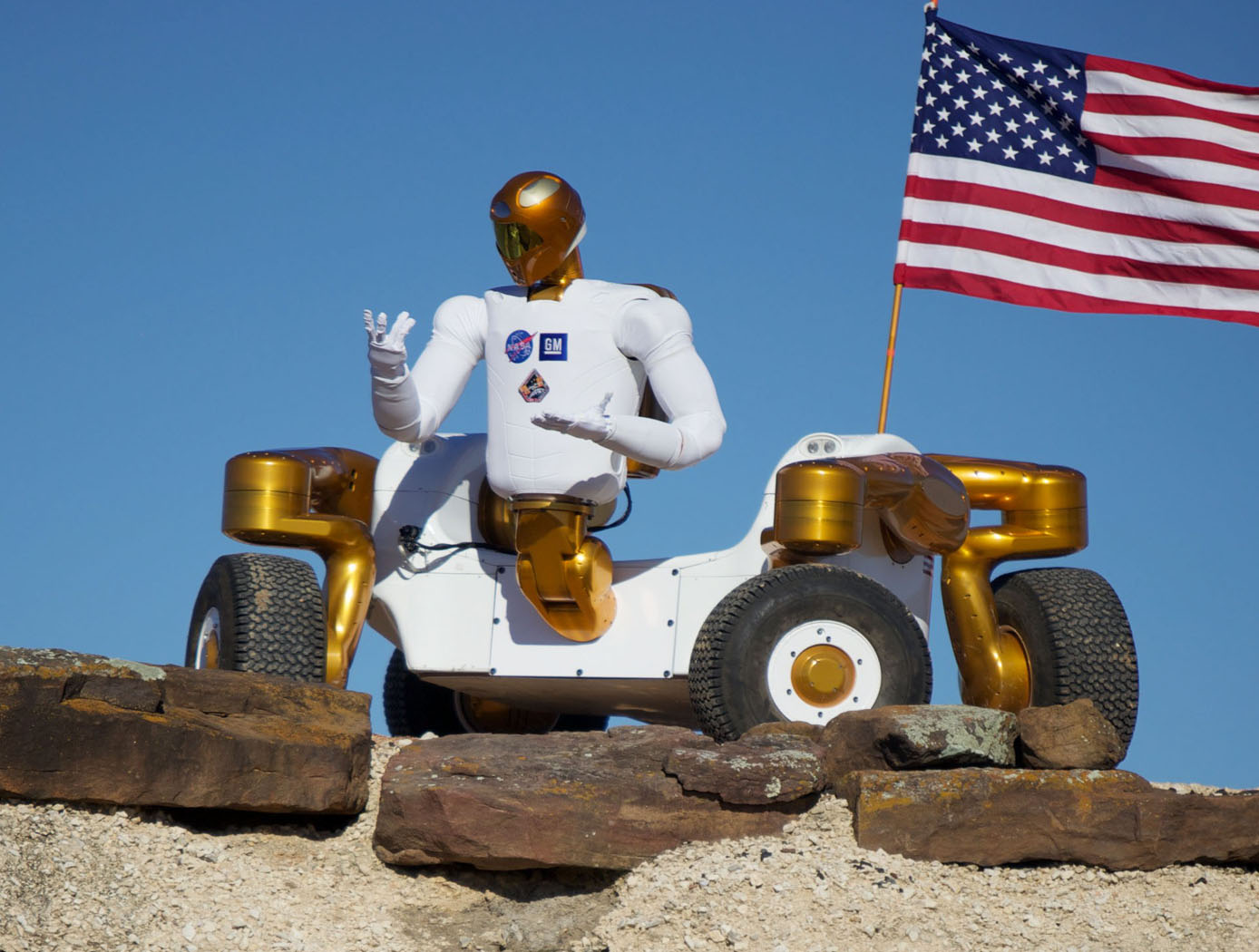
Robonaut 2: Hazardous Environments
Robonaut 2 (R2) has the capability of functioning autonomously or it can be controlled by direct teleoperations, which is advantageous for hazardous environments. When functioning autonomously, R2 understands what to do and how to do it based on sensory input. R2's torso holds the control system while the visor holds several cameras that are incorporated into the visual perception system. With these capabilities, R2 can reduce or eliminate the need for humans to be exposed to dangerous environments. R2 also has a very rugged four-wheel base called the Centaur 2. The Centaur 2 base can lower or raise itself to and from the ground and turn its wheels in any direction, allowing it to turn in place and drive forward or sideways. This enables the R2 to enter hazardous areas or tackle difficult terrain without endangering its human operator.
Robonaut 2 as a whole, or some of its components, can be an invaluable tool for land mine detection, bomb disposal, search and rescue, waste recycling, medical quarantined area, and so much more. The suite of technologies provides an ability to manipulate tools to help with a task, or it can tackle many tasks in a row, where a standard robot may not have the dexterity or sensing capability to get the job done. R2 could pick through nuclear waste, measure toxicity levels, and survey areas too remote or dangerous for human inspection. R2 could deal with improvised explosive devices, detect and dispose of bombs or landmines, and operate equipment that can break through walls or doors.
materials and coatings
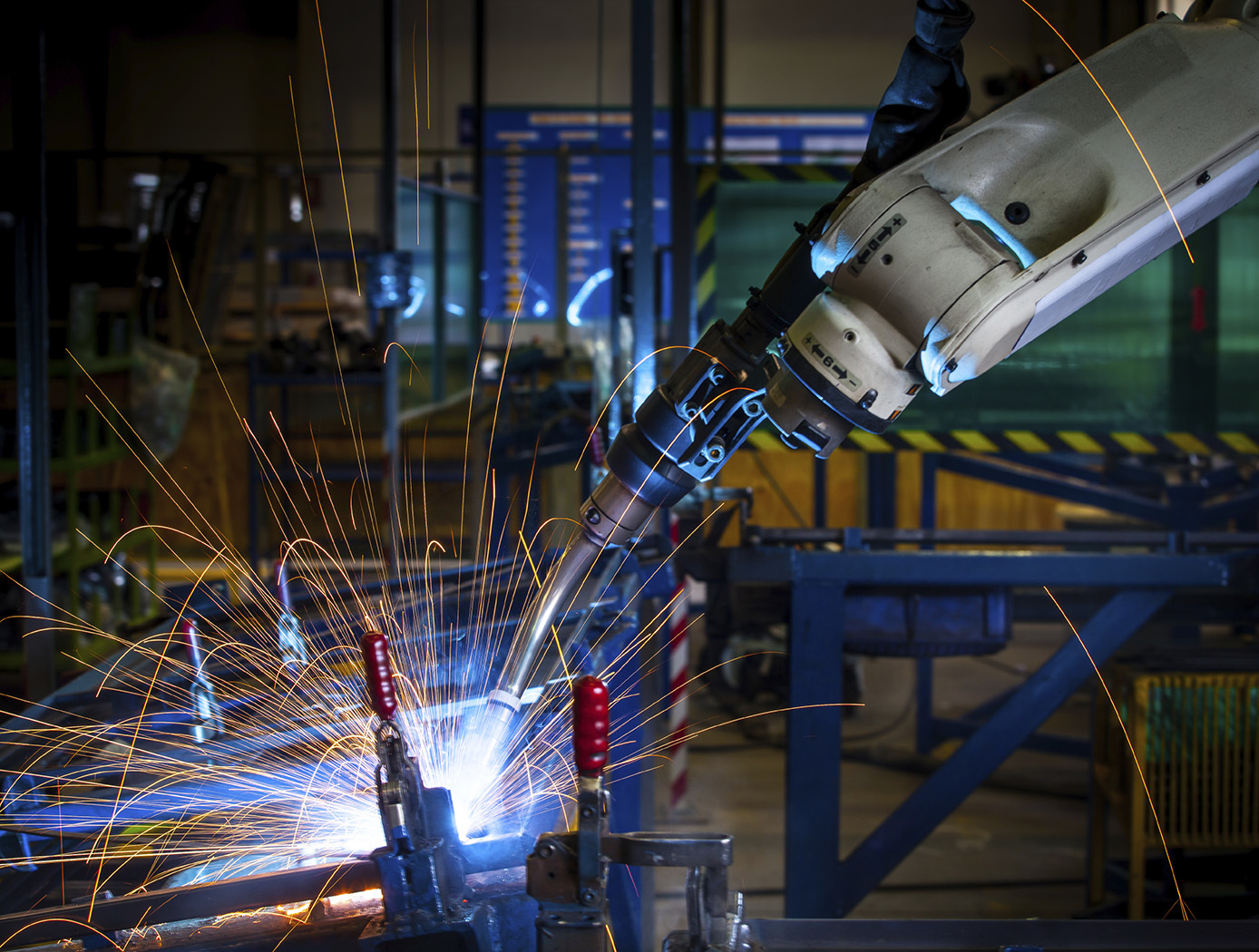
How to Train Shape Memory Alloys
Glenn researchers have optimized how shape memory alloys (SMAs) are trained by reconceptualizing the entire stabilization process. Whereas prior techniques stabilize SMAs during thermal cycling, under conditions of fixed stress (known as the isobaric response), what Glenn's innovators have done instead is to use mechanical cycling under conditions of fixed temperature (the isothermal response) to achieve stabilization rapidly and efficiently. This novel method uses the isobaric response to establish the stabilization point under conditions identical to those that will be used during service. Once the stabilization point is known, a set of isothermal mechanical cycling experiments is then performed using different levels of applied stress. Each of these mechanical cycling experiments is left to run until the strain response has stabilized. When the stress levels required to achieve stabilization under isothermal conditions are known, they can be used to train the material in a fraction of the time that would be required to train the material using only thermal cycling. As the strain state has been achieved isothermally, the material can be switched back under isobaric conditions, and will remain stabilized during service. In short, Glenn's method of training can be completed in a matter of minutes rather than in days or even weeks, and so SMAs become much more practical to use in a wide range of applications.
Manufacturing
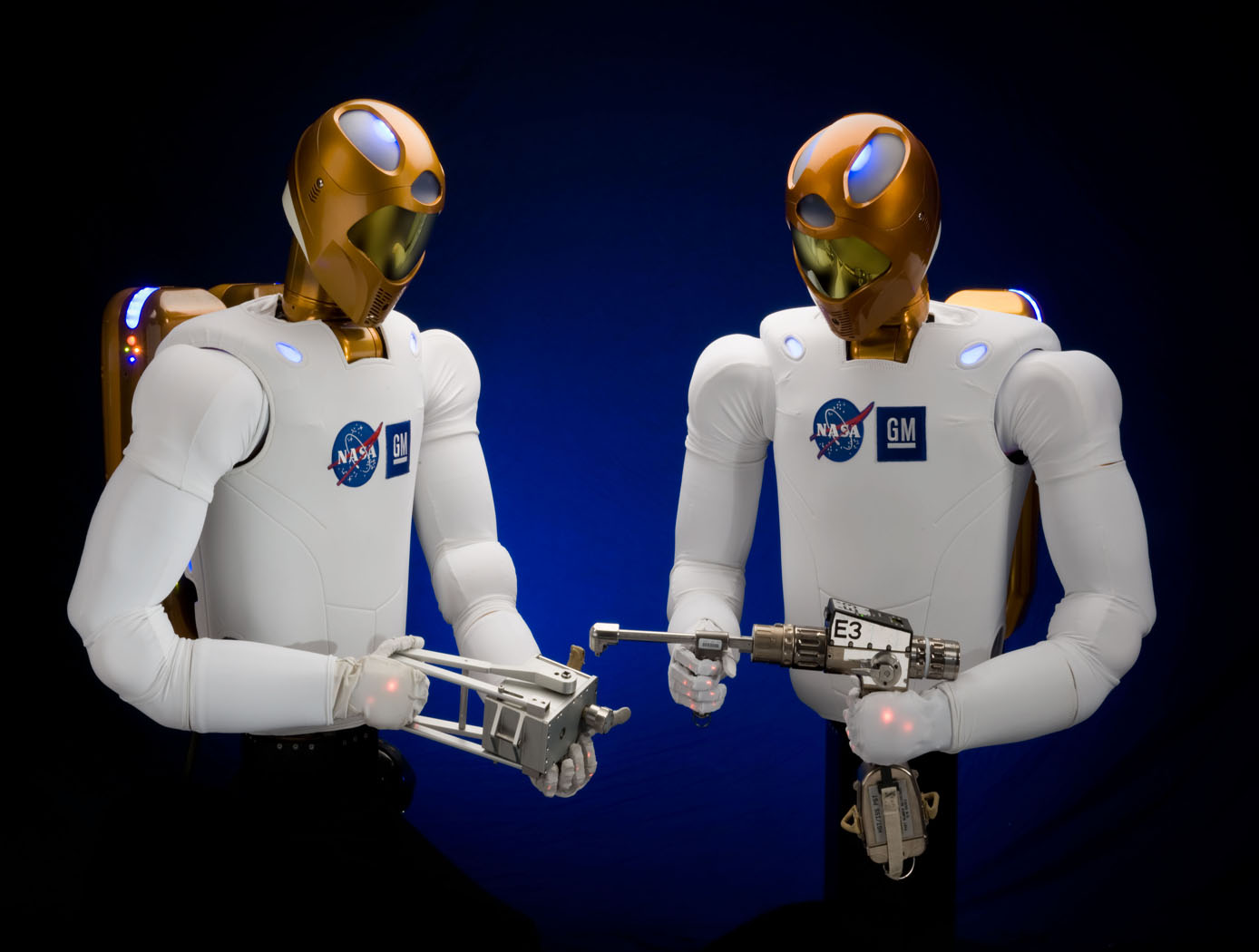
Robonaut 2: Industrial Opportunities
NASA, GM, and Oceaneering approached the development of R2 from a dual use environment for both space and terrestrial application. NASA needed an astronaut assistant able to function in space and GM was looking for a robot that could function in an industrial setting. With this in mind, R2 was made with many capabilities that offer an enormous advantage in industrial environments. For example, the robot has the ability to retool and vary its tasks. Rather than a product moving from station to station on a conveyor with dozens of specialized robots performing unique tasks, R2 can handle several assembly steps at a single station, thereby reducing manufacturing floor space requirements and the need for multiple robots for the same activities. The robot can also be used in scenarios where dangerous chemicals, biological, or even nuclear materials are part of the manufacturing process.
R2 uses stereovision to locate human teammates or tools and a navigation system. The robot was also designed with special torsional springs and position feedback to control fine motor movements in the hands and arms. R2's hands and arms sense weight and pressure and stop when they come in contact with someone or something. These force sensing capabilities make R2 safe to work side-by-side with people on an assembly line, assisting them in ergonomically challenging tasks or working independently.
This NASA Technology is available for your company to license and develop into a commercial product. NASA does not manufacture products for commercial sale.
Aerospace
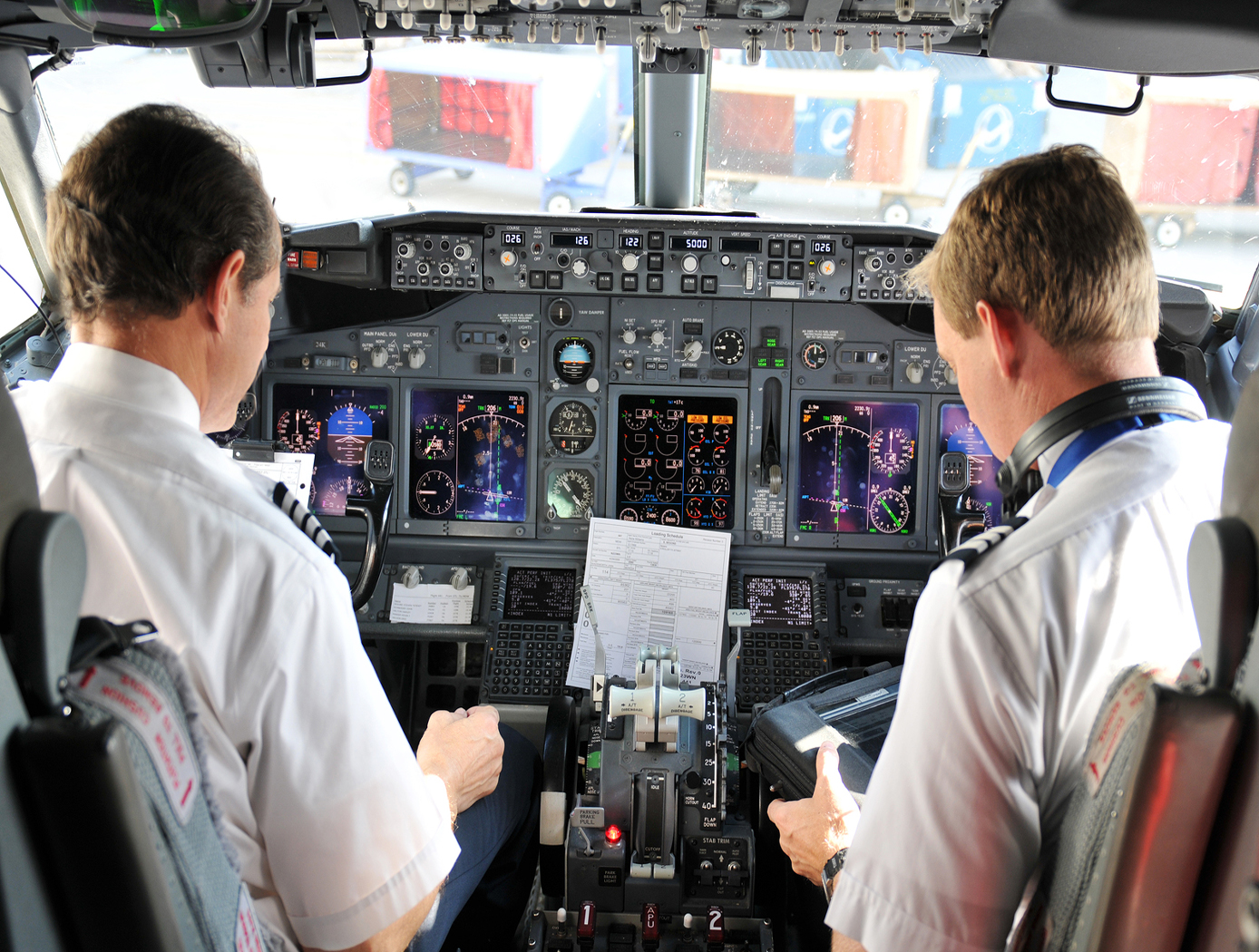
Foot Pedal Controller
The Foot Pedal Controller enables an operator of a spacecraft, aircraft, or watercraft, or a simulation of one in a video game, to control all translational and rotational movement using two foot pedals. This novel technology allows control across all six degrees of freedom, unlike any technology on the market. The components of the technology are a support structure, a left foot pedal, a right foot pedal, and supporting electronics. The Foot Pedal Controller is intuitive, easy to learn, and has ergonomic features that accommodate and stabilize the operator's feet. A working prototype is available to demonstrate key technology features to potential licensees.
The Foot Pedal Controller technology could be used in designs for the flight deck of the future, video game controls, drone operations and flight simulators. This technology can be useful in any application where it is preferred or desirable to use the feet to control motion rather than using the hands. A potential market could be foot control of equipment by people with arm or hand disabilities. A unique aspect of the innovation is the consideration of natural foot mechanics in the design and placement of the sensors and actuators to reduce operator fatigue. The axes of rotation of the Controller align with the joints of the foot so the foot moves naturally to control the movement of the craft. NASA seeks collaborations with companies interested in licensing and partnering to further develop and commercialize the technology.