Standardized Coarse Azimuth Pointing System
propulsion
Standardized Coarse Azimuth Pointing System (GSC-TOPS-255)
A functional and operating coarse-pointing system for any balloon-borne platform with a suspended payload less than 5,500 lbs.
Overview
The legacy rotator, currently used on balloon missions, is a standardized balloon flight subsystem that is mounted right above the payload, and it separates the rotation of the gondola from the balloon. The legacy rotator is about 124 lbs., was designed to support a maximum payload of 8,000 lbs., and was designed to withstand a 10G axial termination load factor. A majority of balloon payloads are no greater than 5,500 lbs., thus the legacy rotator is over designed for most balloon missions. Reduction of mass of the rotator is important. Depending on the balloon launch vehicle, a reduction of mass allows for more instrumentation to be added to the payload or for a longer flight duration. This would allow for more science data to be collected per balloon flight. There is a need for a designed coarse azimuth pointing system that was at least 25% lighter than the legacy rotator, that was capable of carrying a 5,500 lb. maximum suspended payload, and capable of withstanding a 10G axial termination load factor. The Standardized Coarse Azimuth Pointing System is 34% lighter than the legacy rotator, while meeting other requirements.
The Technology
The Standardized Coarse Azimuth Pointing System is a system for any balloon-borne platform with a suspended payload that was less than 5,500 lbs. It separates the rotation of the gondola and the payload from the balloon. The rotator utilizes GPS and solar sensors for command orientation of the payload. There are solar sensors at the top of the rotator providing a 360-degree view. A guidance, navigation, and control system commands sensors to look at a specific point. For example, sensors can detect the position of the sun. The sensor command is sent through the avionics packages on board to start the motor and turn the shaft until the sensors send feedback that they are at the commanded position. The rotator holds the payload at that position until commanded otherwise. The rotator is designed to have a 5 arc-minute pointing capability, and it has demonstrated a 1.4 arc-minute accuracy. The motor runs on a 28V battery source. The system is designed to be operational in a thermal range of -80 degrees Celsius to +50 degrees Celsius. The system can also accommodate the option of integrating a slip ring with 20 separate channels for power, DSL link, and AART communications.
The Standardized Coarse Azimuth Pointing System features a hollow titanium shaft, 3-D printed solar sensor mounts, 3-D printed avionics package mounts, and a custom motor frame mount. The system also utilizes 3-D printed templates to standardize the assembly of both rotators, so that nonuniform match drilling is not a problem.
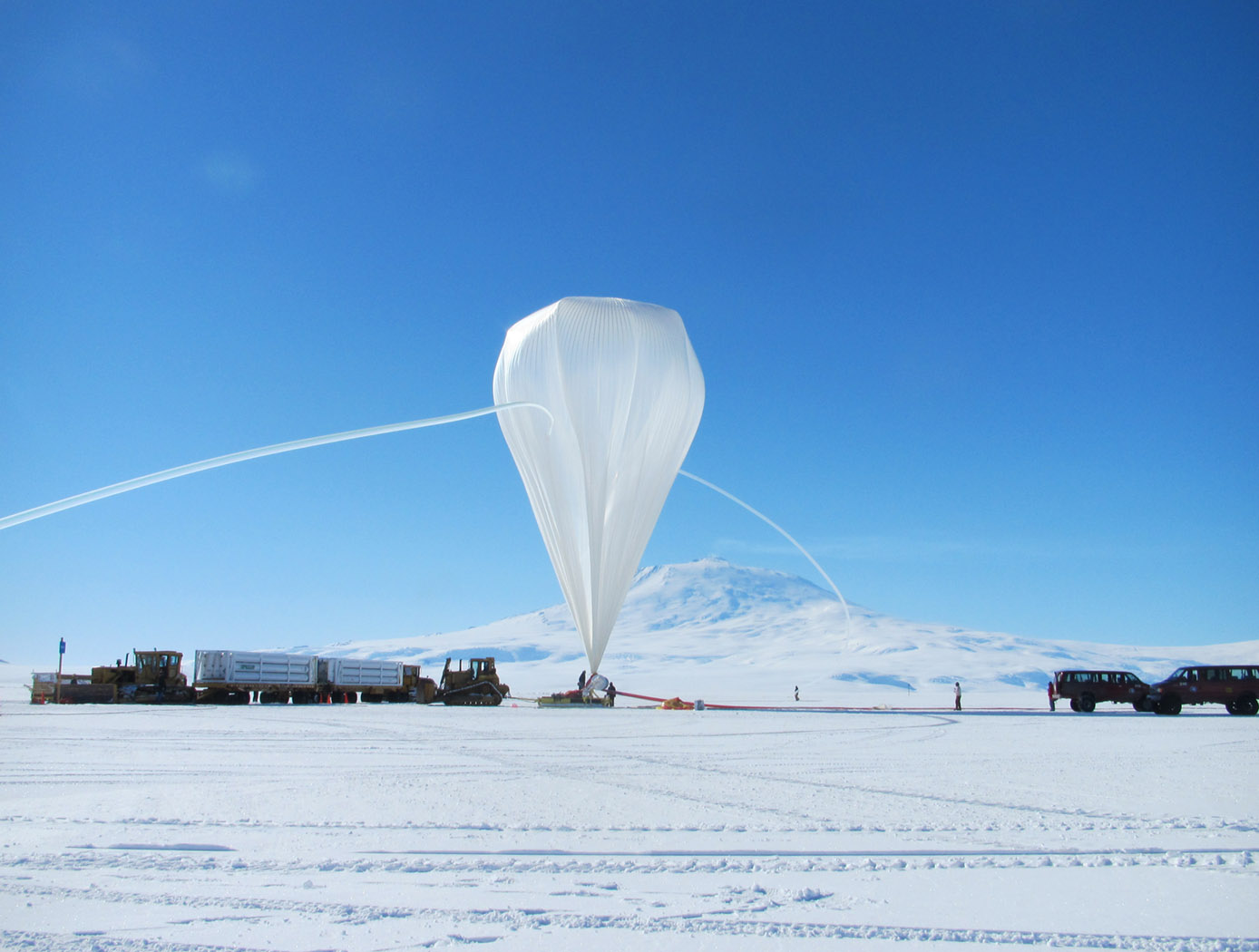
Benefits
- Minimizes size and weight restrictions
- Enables more payload
- Easy to assemble
Applications
- High-altitude balloon systems
- Near space balloon systems
Technology Details
propulsion
GSC-TOPS-255
GSC-18240-1
Similar Results

VTOL UAV With the Cruise Efficiency of a Conventional Fixed Wing UAV
The core technology that enables the Greased Lightning UAV is the aerodynamic efficiency it achieves in its cruise configuration. Electric motors at each propeller negate the need for drive shafts and gearing which enables this Distributed Electric Propulsion (DEP) aircraft configuration. The design is intended to utilize a hybrid electric drive system that includes small diesel engines which drive alternators to power the electric motors and to charge an on-board battery system. The batteries provide the power boost needed for VTOL and hovering. Numerous other novel design elements are incorporated, such as folding propellers to minimize drag when not in operation, such that the propulsive efficiency can be nearly ideal at both hover and wing borne flight conditions.

COROTUB Corrugated Rollable Tubular Boom
Deployable composite booms are particularly attractive in space constrained applications. Their high packaging volume efficiency enables relatively large spacecraft systems required for power generation, communications, or propulsion to be housed within small volumes. COROTUB is a monolithic closed-section tubular thin-shelled structure that’s been shown to scale efficiently up to 50m yet maintain its strength. COROTUB’s two corrugated thin shells form a closed section, which yields high bending and torsional stiffness, allowing for high dimensional stability. Computational analysis and early tests show that the corrugation provides increased strength against buckling, enabling longer booms and targeting more demanding structural applications than non-corrugated designs. The corrugation geometry that dictates the boom cross-section shape was informed by parametric studies to optimize the parameters that most influence the cross-section’s area moment of inertia and torsional constant. The corrugated designs were found to improve the boom bending and axial strength and to shorten the length of the boom transition from flat/rolled to deployed.

Axial Magnetic Flux Airflow Integrated Compressor-Generator-Motor Turbojet
The innovation uses the rotating blades of the compressor section to act as structural support for the generator. Since the compressor is the coolest part of the engine, it will reduce the potential for interference with magnetics and associated curie points of the permanent magnets. The placement of the generator in the cooler part of the engine flowpath (fan or compressor) will also improve the electrical insulation system's degradation and serve to improve overall system lifetime.
The configuration proposed by Armstrong's design would be an axial magnetic flux permanent magnet generator or motor. The electrical/mechanical interface could serve to deliver power to the shaft of the turbojet/fan or extract power from the shaft.
This axial electromagnetic flux design is more efficient for the combined function of aero-thermal heat transfer and generation of electricity. This is due to the relative amount of available cooling surface area, which has an advantage over radial designs given the total system volumetric aspect ratio of the generator/compressor section. When the system is viewed as a thermodynamic cycle, it is more efficient because it is essentially a regenerative cycle, with the heat of generation being fed back into the cycle instead of being released into the ambient surroundings

Powered Kite with Enhanced Aerial Position Control
Skyvator offers enhanced positional capabilities. Skyvator can perform maneuvers such as pointing into or perpendicular to the wind, maintaining level flight, climbing, descending, and station-keeping at desired altitudes. These movements are enabled by the power system, incorporated in the wing or other location on the kite, which are attached to the controller, and in turn is connected to one or more actuators, such as motors and drivers. These motors and drivers can be located in various portions of the kite to cause one part or another to move. Additionally, the controller can be connected to one or more instrument systems for data collection and measurement purposes. These include sensors for detecting windspeed, direction, pressure, GPS, temperature, humidity, imagers, atmospheric particle detectors, and gas detectors, among others. The improved positional control and information allows a user to collect data more effectively and accurately.Skyvator is designed to be used across a wide range of altitudes, from a few feet above the ground to over 18,000 feet above the surface. Additionally, Skyvator prototypes have demonstrated the ability to maintain stready, controllable flight exceeding 60 – 70 mph winds. Please note that NASA does not manufacturer products itself for commercial sale.

Reverse Vortex Ring (RVR)
Vibration problems, which occur more frequently in high power to weight machines, often lead to costly down time, subsequent redesign, and, in some instances, catastrophic failure. A disproportionate number of vibration problems in rotating machinery can be attributed to highly pre-swirled fluid entering tight clearance locations such as seals and fluid bearings. The relationship between high fluid pre-swirl and undesirable vibration issues is clear. Machines with high levels of fluid pre-swirl are more susceptible to instabilities and vibration problems.
A top priority in rotor dynamic design, therefore, is to develop devices to minimize the level of fluid pre-swirl entering tight clearance locations. The RVR was designed to condition the flow prior to entering the seal (or axial flow fluid-film bearing) so that the flow through the annular clearance is at a minimum purely axial. While conventional swirl brakes have only been shown to reduce pre-swirl by up to 30%, the RVR can actually reverse the direction of the swirl, so that circumferential fluid velocity flows in a direction counter to shaft rotation. Thus, a classic detriment to rotating machinery has now become an asset to ameliorate vibration issues through the RVR.
The RVR is axially efficient, typically increasing the axial length of a smooth annular seal on the order of 10-12%.
The RVR has been extensively tested and is now in use at NASA.