Fluid Measurement Sensor
sensors
Fluid Measurement Sensor (LAR-TOPS-11)
A wireless, powerless, passive inductor-capacitor sensor for measuring fluid level, pitch and roll angles, and volume
Overview
NASA's Langley Research Center researchers have developed a wireless, thin-film fluid measurement sensor that uses a magnetic field response measurement acquisition system to provide power to the sensor and to acquire physical property measurements from it. In addition to measuring
fluids within an enclosed container, it can be placed external to a non-conductive container to measure the level of any non-gaseous substance, including liquids, solids, and semi-solids such as powder or granular substances.
The Technology
The fluid measurement sensor is configured with a spiral electrical trace on flexible substrate. The sensor receives a signal from the accompanying magnetic field data acquisition system. Once electrically active, the sensor produces its own harmonic magnetic field as the inductor stores and releases magnetic energy. The antenna of the measurement acquisition system is switched from transmitting to receiving mode to acquire the magnetic-field response of the sensor. The magnetic-field response attributes of frequency, amplitude, and bandwidth of the inductor correspond to the physical property states measured by the sensor. The received response is correlated to calibrated data to determine the physical property measurement. When multiple sensors are inductively coupled, the data acquisition system only needs to activate and read one sensor to obtain measurement data from all of them.
Fluid level measurement occurs in several ways. In the immersion method, the capacitance of the sensor circuit changes as it is immersed in fluid, thus changing the frequency response as the fluid level rises or falls. Fluid level can also be measured from the outside of a non-conductive container. The response frequency from the sensor is dependent upon the inductance of the container plus the combination of fluid and air inside it, which corresponds to the level of liquid inside the container. Roll and pitch are measured by using three or more sensors in a container. With any given orientation, each sensor will detect a different fluid level, thus providing the basis for calculating the fluid angle. Volume can be measured in the same way, using the angle
levels detected by the sensors and the geometric characteristics of the container to perform the volume calculation.
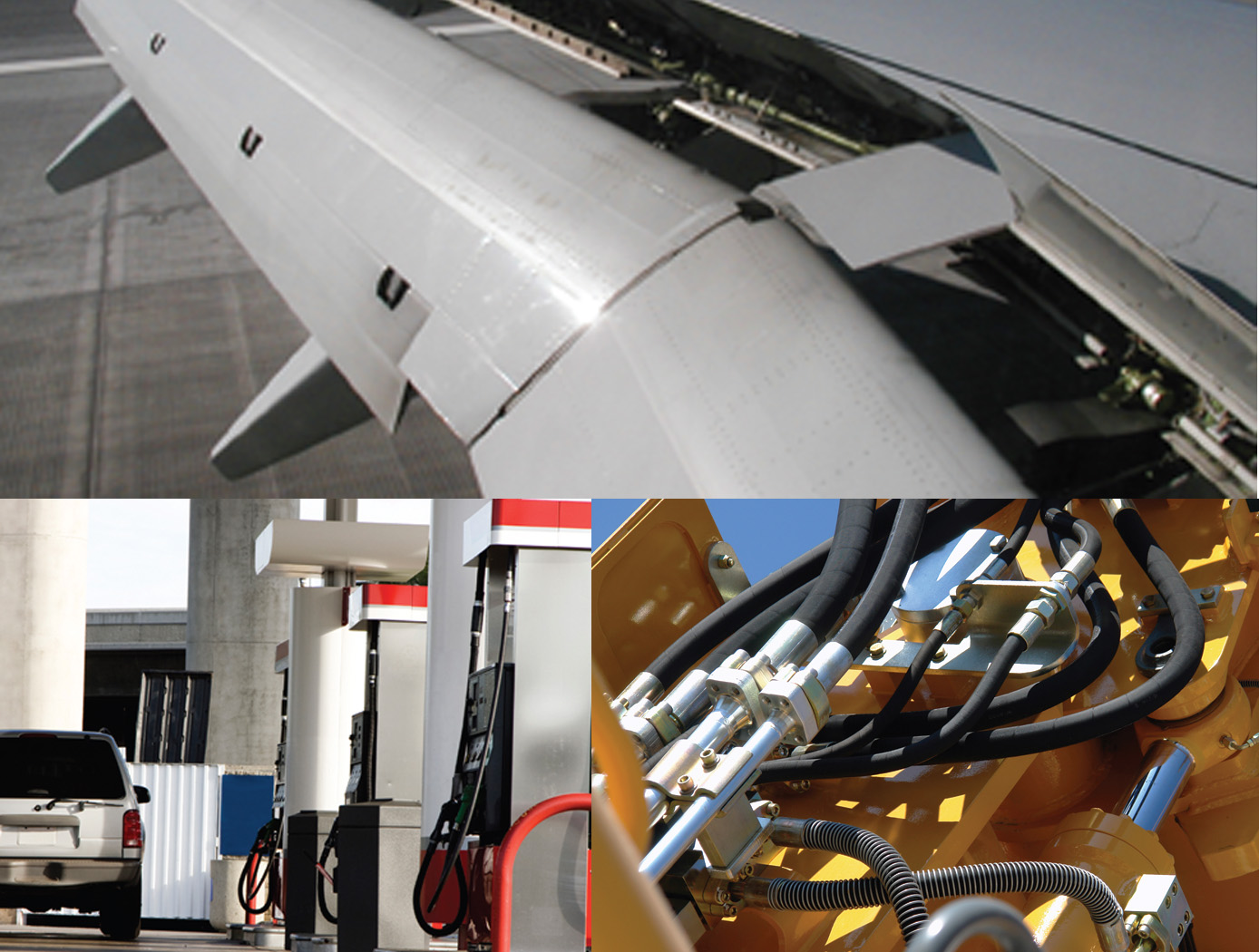
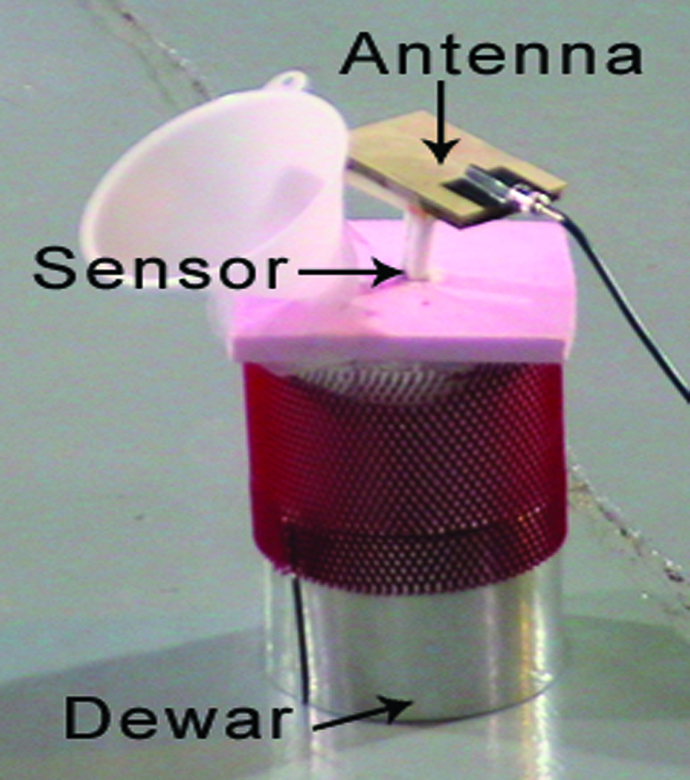
Benefits
- Receives power wirelessly, eliminating the need for a sensor power source
- Sends signals wirelessly to the data acquisition device, eliminating signal wiring
- Reduces system weight due to less wiring
- Non-mechanical method for fluid measurement - no moving parts, reducing the probability of failure
- Eliminates potential for arcing (safer use in fuel tanks)
- Lightweight
- Can measure fuels without opening the tank, reducing emission of harmful gases
Applications
- Fuel and other liquid measurements in vehicles
- Above or below ground fuel storage tanks
- Cryogenic fluid tanks
Tags:
|
Similar Results

Low-Profile Wireless Sensor
The low-profile sensor is configured with a spiral electrical trace on flexible substrate. In typical inductor designs, the space between traces is designed to minimize parasitic conductance to reduce the impact of the capacitance to neighboring electronics. In the low-profile sensor, however, greater capacitance is desired to allow the operation of an inductor-capacitor circuit. This allows the traces to be closer together, decreasing the
overall size of the spiral trace.
The sensor receives a signal from the accompanying magnetic field data acquisition system. Once electrically active, the sensor produces its own harmonic magnetic field as the inductor stores and releases magnetic energy. The antenna of the measurement acquisition system is switched from a transmitting to a receiving mode to acquire the magnetic-field response of the sensor. The magnetic-field response attributes of frequency, amplitude, and bandwidth of the inductor correspond to the physical property states measured by the sensor. The received response is correlated to calibration data to determine the physical property measurement. When multiple sensors are inductively coupled, the data acquisition system needs to activate and read
only one sensor to obtain measurement data from all of them.
Wireless Sensor for Pharmaceutical Packaging and Monitoring Applications
The SansEC sensor is an electrically open circuit without electrical connections. Having a device without circuits eliminates a common failure source of electrical systems. It consists of a uniquely designed thin-film electrically conductive geometric pattern that stores energy in both electric and magnetic fields. When wirelessly interrogated from the portable data acquisition system, the sensor becomes electrically active and emits a wireless response. The magnetic field response attributes of frequency, amplitude, and bandwidth of the inductor correspond to the physical property states measured by the sensor. Container damage, temperature, spoilage, or substance level is detected by changes in resonant frequency read by the accompanying magnetic
field data acquisition system. A unique feature of the sensor is its ability to measure more than one physical attribute at the same time. In addition, by eliminating electrical connections, damage to any area of the sensor will not prevent it from being powered or interrogated.

Damage and Tamper Detection Sensor System
The SansEC sensor system consists of multiple pairs of inductor-capacitor sensors with no electrical connections, which are placed throughout the material being monitored for damage. The sensors are embedded in or placed directly onto the surface of the material. Strains and breaks are detected by changes in resonant frequency read by the accompanying magnetic field data acquisition system. When pulsed by a sequence of magnetic field harmonics from the acquisition system, the sensors become electrically active and emit a wireless response. The magnetic field response attributes of frequency, amplitude, and bandwidth of the inductor correspond to the physical property states measured by the sensor. The received response is correlated to calibration data to determine the physical property measurement. Because each sensor pair has its own frequency response, when damage occurs to that circuit the frequency response changes. This change identifies the damage location within the material.
A unique feature achieved by eliminating electrical connections is that damage to a single point will not prevent the sensor from being powered or interrogated. If a sensor is broken, two concentric inductively coupled sensors are created, thus identifying tamper or damage location.

Wireless Electrical Devices Using Floating Electrodes
The technology presents a fundamental change in the way electrical devices are designed, using an open circuit in conjunction with a floating electrode, or an electrically conductive object not connected to anything by wires, and powered through a wireless device. This system uses inductor-capacitor thin-film open circuit technology. It consists of a uniquely designed, electrically conductive geometric pattern that stores energy in both electric and magnetic fields, along with a floating electrode in proximity to the open circuit. When wirelessly pulsed from the handheld data acquisition system (U.S. Patent Number 7,159,774, Magnetic Field Response Measurement Acquisition System), the system becomes electrically active and develops a capacitance between the two circuit surfaces. The result is a device that acts as a parallel plate capacitor without electrical connections.

Highly Accurate Level Sensor
The FAA and Aircraft Industry recognize the need to reduce fuel tank explosion risk
by eliminating ignition sources and changing fuel tank design and maintenance.
This technology can be utilized to wirelessly sense the level of fuel in aircrafts, thus
mitigating risk of inadvertent electrical failures and sparks. NO wires enter the fuel
tank and the radio frequency transponder typically requires 10 milliwatts of power or
less.
The technology can be used for dielectric tanks, by simply applying the sensors to the
tank surface (as pictured). Through certain techniques the technology can be applied
on metal tanks with no wires entering the tank from the outside.
Currently, there are more than 20,910 jet aircraft in service. This presents a large
market opportunity for retrofitting this technology onto existing airplane fuel tanks
Rapidly evolving aviation services are expected to spur worldwide requirement for
36,770 new jet aircraft by 2033. This presents a growing market for new installations.