Multirotor Aircraft Noise Reduction
aerospace
Multirotor Aircraft Noise Reduction (LAR-TOPS-325)
Phase-locked rotors reduce noise
Overview
Multirotor aircraft typically create a significant amount of tonal noise from each rotor. Groups of rotors operating at the same rotation rate with an appropriate phase offset can be used to reduce the tonal noise of the aircraft when there are multiple rotors on each side of the aircraft.
Reducing tonal noise, depending on the aircraft design, can effectively reduce the total noise output for a given flight scenario. Aircraft can be designed with this technology to prioritize quieter take-off and landing, or can be designed for decreased noise in cruise. Existing designs may benefit from this technology as well, but what type of benefits can be gained depend on the design of the aircraft.
Using this method, multiple rotors can be significantly quieter than a single rotor, without sacrificing thrust.
The Technology
Noise produced by multirotor vehicles may be objectionable to some, especially as industry moves toward drone deliveries and potentially air taxi operations.
However, noise reductions can now be attained by synchronizing the rotation rate and then controlling the phase offset between neighboring rotors. The optimal phase offset is uniquely defined based on the number of blades and the relative location of each rotor and does not depend on the rotation rate, blade geometry, or other aspects of the vehicle design.
This technology is not viable for all multirotor aircraft but is applicable if the rotation rate of neighboring rotors can be synchronized mechanically or electronically.
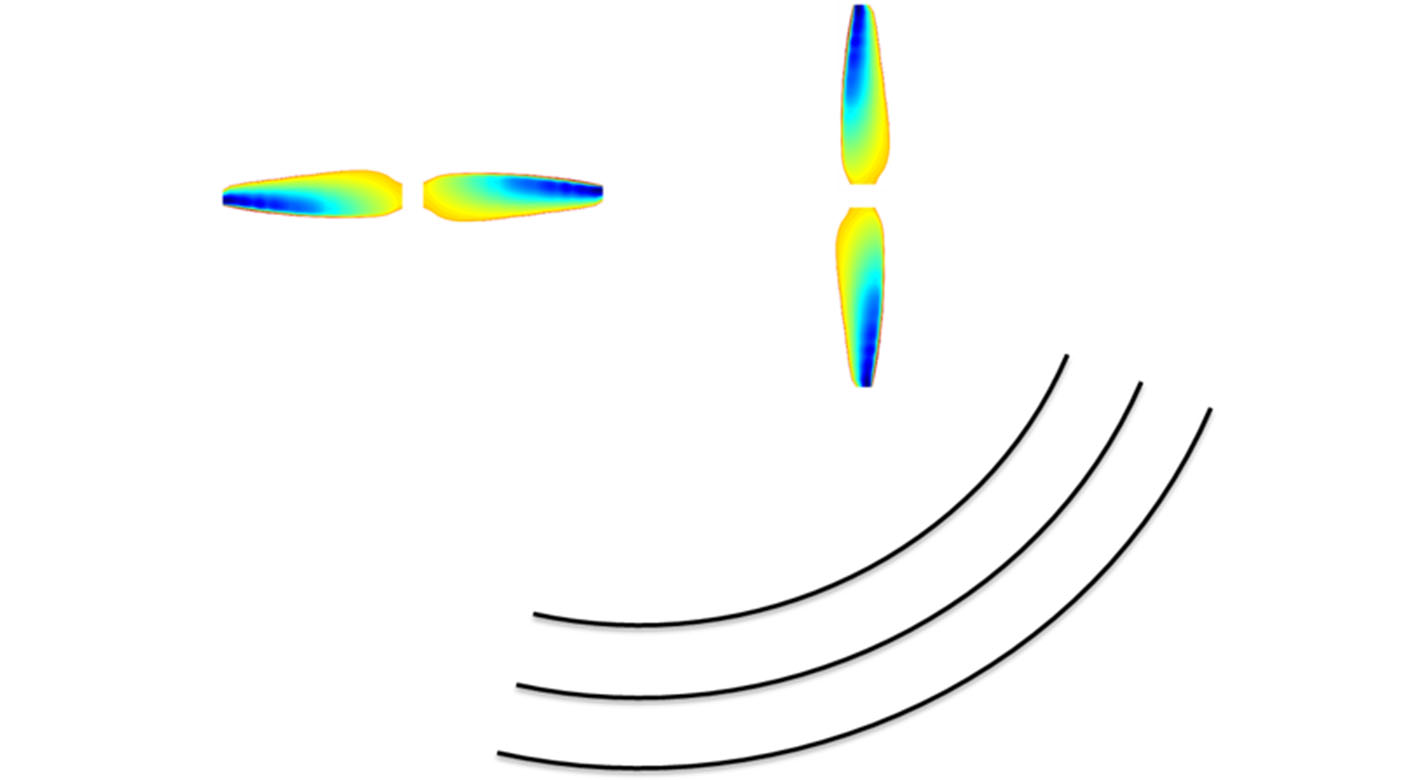
Benefits
- Quieter aircraft operations
Applications
- UAV Deliveries
- Air Taxis
- Professional and hobby drone pilots
Similar Results

Anti-Phase Noise Suppression Rotor Technologies
Rotor noise and vibration are two sources of operational challenges for all aircraft operating with open rotors such as helicopters, unmanned aerial vehicles (UAVs), urban air mobility personal air vehicles, drones, and aircraft operating with ducted fans such as passenger aircraft. One disadvantage of convention rotor design is the noise due to noise-induced shed vortices generated by rotor blades. The unique problem with rotor noise and vibration is the periodic blade passage that causes a harmonic reinforcement and causes the rotor blades to vibrate and generate noise sources. This technology from NASA Ames seeks to optimize the implementation of anti-phase trailing edge designs and asymmetric blade tip treatments for rotor noise suppression and integrated aircraft noise solutions by incorporating the anti-phase rotor design concepts into an aircraft flight control system to reduce noise footprint. There are several embodiments of the invention, which include the following: (1) an anti-phase trailing edge design whereby the trailing edge pattern of the leading rotor blade is offset by a phase shift from the trailing edge pattern of the following blade; (2) an anti-phase rotor design implementing asymmetric blade tips with inverted airfoil; and (3) other anti-phase enabled concepts such as unequal blade length, ducted rotors with non-radial unequally spaced struts, and multi-axis tilt rotor design incorporating the anti-phase rotor design.

Propeller/Rotor Phase Control for Reduction of Community Noise from Distributed Propulsion Vehicles
This innovation comprises a method of adjusting the relative angular positions of the propeller and/or rotor blades from a distributed propulsion system to favorably modify the spatial distribution of noise emanated by the vehicle, that is, the directivity pattern, for the purpose of reducing community noise. Adjusting these angular positions shows a great ability to act as a noise-canceling technique by way of destructive wave interference. Effectively, the acoustic energy can be steered away from noise-sensitive areas, e.g., schools, communities, etc. In the initial implementation, the phase angles can be calculated prior to flight. These depend on the propeller/rotor rotation rate, observer location, and relative propeller/rotor spacing, the latter being constant for a given vehicle. Optimization techniques determine the set of phase angles over the parametric space.

Device for Providing Real-Time Rotorcraft Noise Abatement Information
The magnitude and direction of rotor noise radiation is determined by the aerodynamic operating state of the rotor commonly referred to as the "Blade-Vortex Interaction" which occurs when the wake vortex trailing from a preceding rotor blade interacts with the front edge of the following rotor blade. The wake vortex causes a rapid change in the blade loading, which results in the generation of high amplitude, impulsive, and highly directional noise. The occurrence, magnitude, and directionality of Blade-Vortex Interaction noise is very sensitive to the rotor operating state because it is dependent on the relative positions of the rotor and its vortex wake. By providing the rotorcraft pilot with information about annoying noise levels currently being emitted by the rotorcraft and its effects on the ground, corrective action can be taken to change the operating state of the vehicle to minimize or avoid annoyance due to such rotor noise sources.
During operation, the pilot would activate the device before or during operation of the rotorcraft. The device displays the noise abatement information through a display unit, informing the pilot about the current acoustic state of the vehicle and providing guidance on how to change the vehicle performance and acoustic state to avoid objectionable blade-vortex Interaction noise. Annoyance footprint information can then be used by the pilot to change the flight path of the vehicle such that the annoyance footprint will not extend into noise sensitive areas.

Statistical Audibility Prediction (SAP) Algorithm
A method for predicting the audibility of an arbitrary time-varying noise (signal) in the presence of masking noise is described in "An Algorithm for Statistical Audibility Prediction (SAP) of an Arbitrary Signal in the Presence of Noise" published in the Journal of the Audio Engineering Society (Vo. 69, No. 9, September 2021). The SAP method relies on the specific loudness, or loudness perceived through the individual auditory filters, for accurate statistical estimation of audibility vs. time. As such, this work investigated a new hypothesis that audibility is more accurately discerned within individual auditory filters by a higher-level, decision-making process. Audibility prediction vs. time is intuitive since it captures changes in audibility with time as it occurs, critical for the study of human response to noise. Concurrently, time-frequency prediction of audibility may provide valuable information about the root cause(s) for audibility useful for the design and operation of sources of noise. Empirical data, gathered under a three-alternative forced-choice (3AFC) test paradigm for low-frequency sound, has been used to examine the accuracy of SAPs.
Future work should involve additional studies to examine the performance of SAP with realistic ambient noise and signals with higher-frequency content.

Autonomous Slat-Cove Filler Device
NASA Langley designed the shape memory alloy slat-cove filler to provide significant broad-band noise reduction to any aircraft wing structure that has a leading-edge, high-lift device and that is distinct from the main-wing element. The design can be retrofitted to existing aircraft structures and can be easily incorporated into the existing or future designs for aircraft wing structures. The concept involves very few components, requires no additional mechanical support from pneumatic or hydraulic systems, and makes use of existing slat-actuation systems for retraction. The design is autonomous, simple, and constitutes low-weight addition. The concept is also considered fail-safe because the lift would not be diminished in the event that the slat cove filler failed to deploy.
Several advancements have been devised to accommodate complex features encountered in application to practical airframe structures. Graphics from a computational model of a 2D physical demonstration system show the configuration and strain in the slat-cove filler in the deployed and stowed conditions. Features enabling stowage of a large curvilinear length (sliding hinge) and maintenance of the optimized outer mold line (auxiliary component) are highlighted. Other advancements for application to 3D, flight airframes are visible in the image from a model for one entire section of a slat-cove-filler treatment for a wide-body, transport-class aircraft.
NASA Langley also offers a design for a deformable structure that is deployed from the leading edge of the main-wing element, termed the slat-gap filler. It closes and covers the gap between the slat and the main-wing element, but can be readily and autonomously opened in emergency to regain the baseline high-lift configuration and its corresponding lift performance at high angles of attack. This approach has similar benefits as the slat-cove filler device.