Search
communications

Microwave Power Combiner
MMICs are a type of integrated circuit that operates at microwave frequencies to amplify electronic signals. The system has at least two power amplifiers; input ports to receive power from the amplifiers; at least one power combiner, which receives power from each input port and combines them to produce maximized power; an output port that sends this maximized power to its destination; and an isolated port, either grounded or match-terminated, that receives no or negligible power from the combiner. The output port can be connected to a load, and can employ more than one combiner, so that the power from another combiner and an input port can be combined, for example, in a 3-way unequal power combiner.
Glenn's Ka-band demonstration power combiner has an output return loss better than 20 dB, and a high degree of isolation between the output port and the isolated port, as well as between the two input ports. When the ratio of output power for two MMICs is two-to-one, the combined efficiency is better than 90%. However, the design is not limited to a two-to-one ratio; it can be customized to any arbitrary power output ratio. This means that a low-power gallium arsenide MMIC can be combined with a high-power gallium nitride MMIC, giving designers much more flexibility. The output impedance of the MMIC power amplifier is matched directly to the waveguide impedance, without first transitioning into a transmission line. This technique eliminates the losses associated with a transition and enhances the overall efficiency. Furthermore, the MMIC power combiner is dual purpose- run in reverse it serves as a power divider. To reduce the cost and weight the combiner can be manufactured using 3-D printing and metal-plated plastic. By combining MMIC amplifiers more efficiently, Glenn's technology greatly enhances communications from near-Earth and deep space-to-Earth.
electrical and electronics
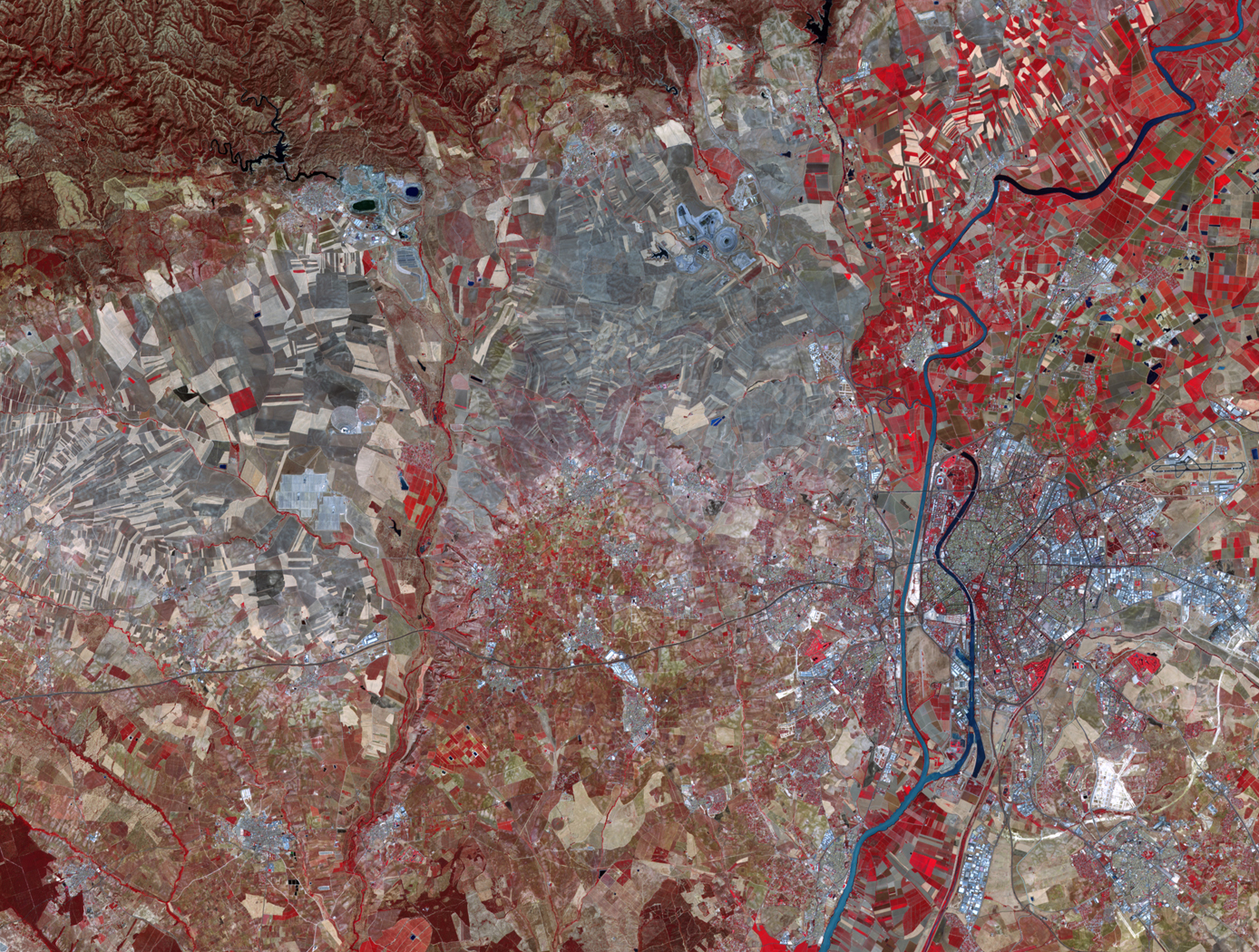
Using the Power Grid for Geophysical Imaging
This technology utilizes the U.S. high-voltage power transmission grid system as an extremely large antenna to extract unprecedented spatiotemporal space physical and geological information from distributed GIC observations. GICs are measured using differential a magnetometer technique involving one fluxgate magnetometer under the transmission line and another reference magnetometer station nearby. The reference station allows subtraction of the natural field from the line measurement, leaving only the GIC-related Biot-Savart field. This allows inversion of the GIC amplitude. The magnetometer stations are designed to operate autonomously. They are low-cost, enabling large scale application with a large number of measurement locations.
power generation and storage
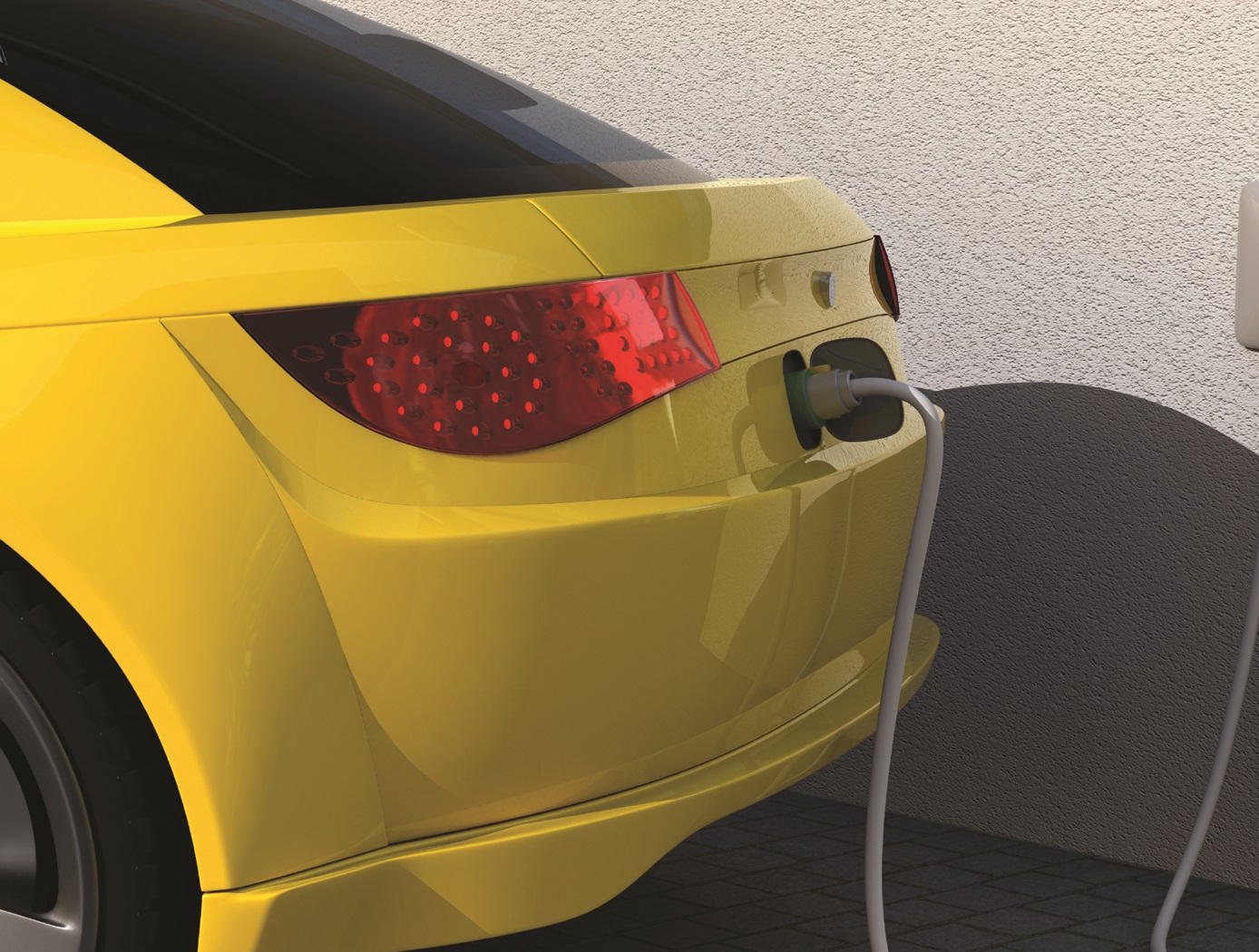
Internal Short Circuit Testing Device to Improve Battery Designs
Astronauts' lives depend on the safe performance and reliability of lithium-ion (Li-ion) batteries when they are working and living on the International Space Station. These batteries are used to power everything such as communications systems, laptop computers, and breathing devices. Their reliance on safe use of Li-ion batteries led to the research and development of a new device that can more precisely trigger internal short circuits, predict reactions, and establish safeguards through the design of the battery cells and packs. Commercial applications for this device exist as well, as millions of cell phones, laptops, and electronic drive vehicles use Li-ion batteries every day. In helping manufacturers understand why and how Li-ion batteries overheat, this technology improves testing and quality control processes.
The uniqueness of this device can be attributed to its simplicity. In a particular embodiment, it is comprised of a small copper and aluminum disc, a copper puck, polyethylene or polypropylene separator, and a layer of wax as thin as the diameter of one human hair. After implantation of the device in a cell, an internal short circuit is induced by exposing the cell to higher temperatures and melting the wax, which is then wicked away by the separator, cathode, and anode, leaving the remaining metal components to come into contact and induce an internal short. Sensors record the cell's reactions. Testing the battery response to the induced internal short provides a 100% reliable testing method to safely test battery containment designs for thermal runaway.
This jointly developed and patented technology is available for your company to license and develop into a commercial product. NASA does not manufacture products for commercial sale.
Aerospace
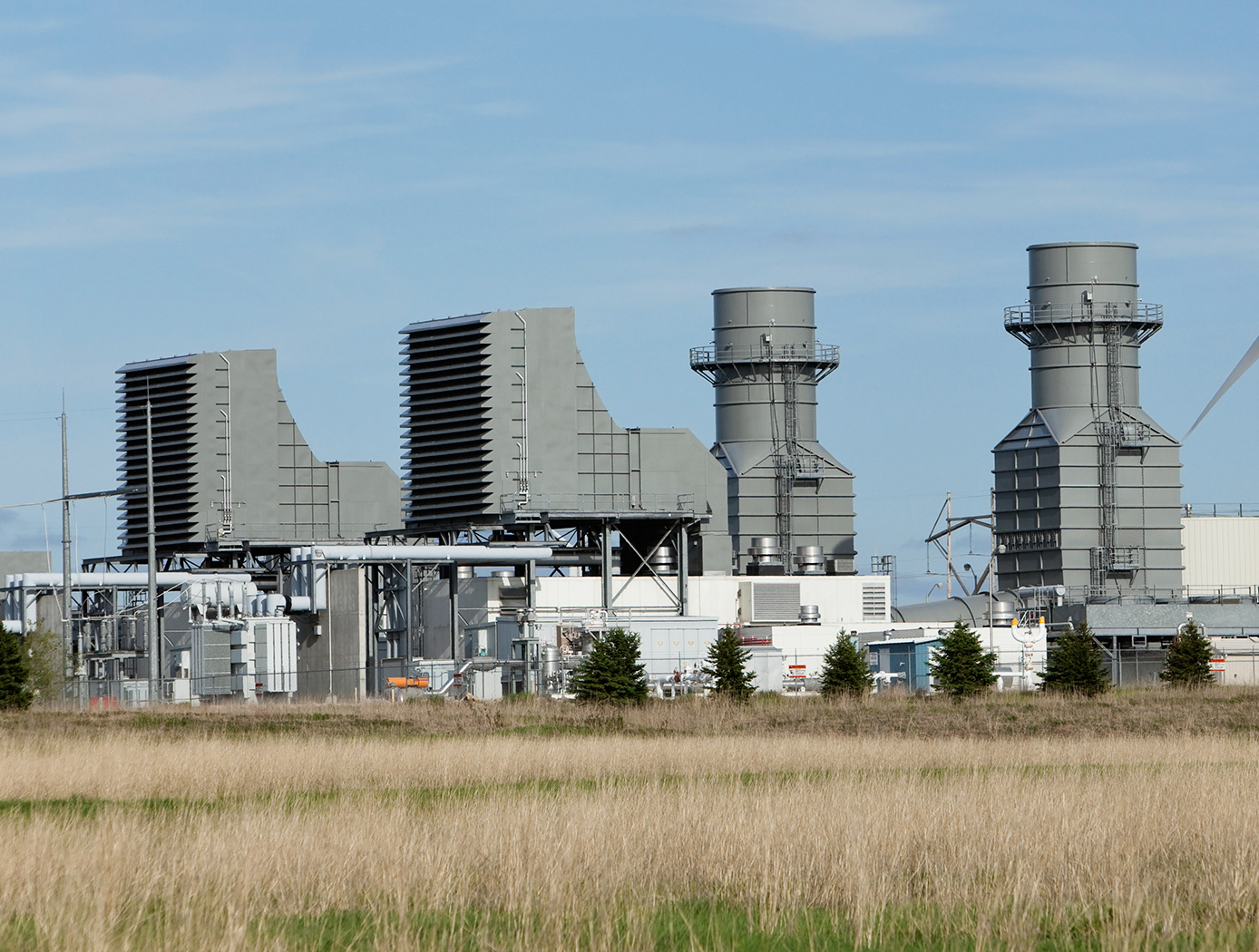
New Concepts in Film Cooling for Turbine Blades
In one of NASA Glenn's innovations, a shaped recess can be formed on a surface associated with fluid flow. Often V-shaped, this shaped recess can be configured to create or induce fluid effects, temperature effects, or shedding effects. For example, the shaped recess can be paired (upstream or downstream) with a cooling channel. The configuration of the shaped recess can mitigate the lift-off or separation of the cooling jets that are produced by the cooling channels, thus keeping the cooling jets trained on turbine blades and enhancing the effectiveness of the film-cooling process. The second innovation produced to improve film cooling addresses problems that occur when high-blowing ratios, such as those that occur during transient operation, threaten to diminish cooling effectiveness by creating jet detachment. To keep the cooling jet attached to the turbine blade, and also to spread the jet in the spanwise direction, NASA Glenn inventors have successfully used cooling holes that reduce loss by blowing in the upstream direction. In addition, fences may be used upstream of the holes to bend the cooling flow back toward the downstream direction to further reduce mixing losses. These two innovations represent a significant leap forward in making film cooling for turbine blades, and therefore the operation of turbine engines, more efficient.
power generation and storage
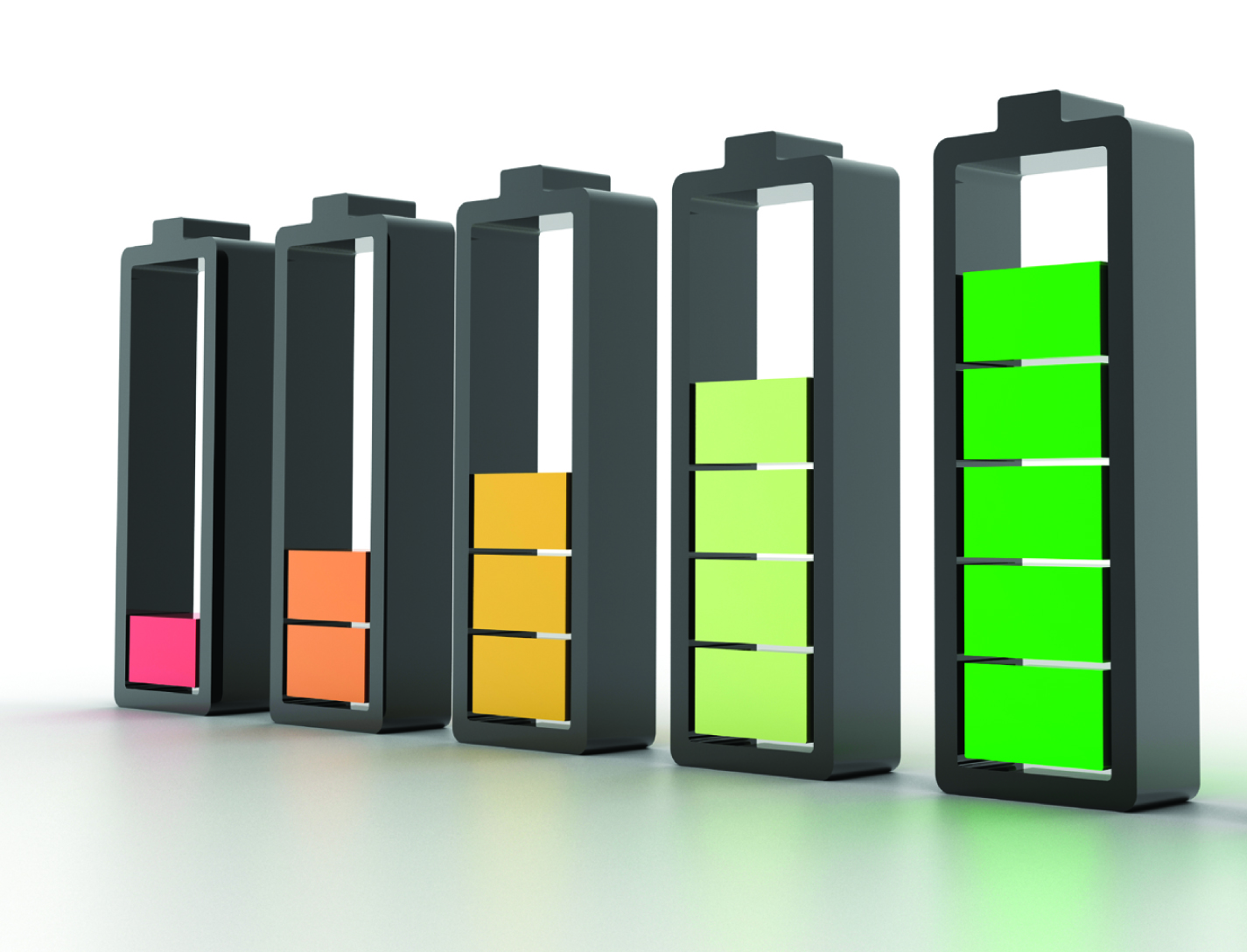
Battery Charge Equalizer System
The innovation consists of a transformer array connected to a battery array through rectification and filtering circuits. The transformer array is connected to a drive circuit and a timing and control circuit, which enables individual battery cells or cell banks to be charged. The timing and control circuit connects to a charge controller that uses battery instrumentation to determine which battery bank to charge. The system is ultra lightweight because it uses much fewer than one transformer per battery cell. For instance, 40 battery cells can be balanced with an array of just five transformers. The innovation can charge an individual cell bank at the same time while the main battery charger is charging the high-voltage battery system.
Conventional equalization techniques require complex and costly electrical circuitry to achieve cell monitoring and balancing. Further, such techniques waste the energy from the most charged cells through a dummy resistive load (regulator), which is inefficient and generates excess heat. In contrast, this system equalizes battery strings by selectively charging cells that need it. The technology maintains battery state-of-charge to improve battery life and performance. In addition, the technology provides a fail-safe operation and a novel built-in electrical isolation for the main charge circuit, further improving the safety of high-voltage Li-ion batteries.
mechanical and fluid systems
Feedthrough for Severe Environments and Temperatures
Space and ground launch support related hardware often operate under extreme pressure, temperature, and corrosive conditions. When dealing with this type of equipment, it is frequently necessary to run wiring, tubes, or fibers through a barrier separating one process from another with one or both operating in extreme environments. Feedthroughs used to route the wiring, tubes, or fibers through these barriers must meet stringent sealing and leak tightness requirements.
This affordable NASA feedthrough meets or exceeds all sealing and leak requirements utilizing easy-to-assemble commercial-off-the-shelf hardware with no special tooling. The feedthrough is a fully reconfigurable design; however, it can also be produced as a permanent device. Thermal cycling and helium mass spectrometer leak testing under extreme conditions of full cryogenic temperatures and high vacuum have proven the sealing capability of this feedthrough with or without potting (epoxy fill) on the ends. Packing material disks used in the construction of the device can be replaced as needed for rebuilding a given feedthrough for another job or a different set of feeds if potting is not used for the original feedthrough build. (Potting on one or both sides of the sleeve provides double or triple leak sealing protection). Variable Compression Ratio (VCR) connectors were adapted for the pressure seal on the feedthrough; however, any commercial connector can be similarly adapted. The design can easily be scaled up to larger (2" diameter) and even very large (12" or more) sizes.
power generation and storage
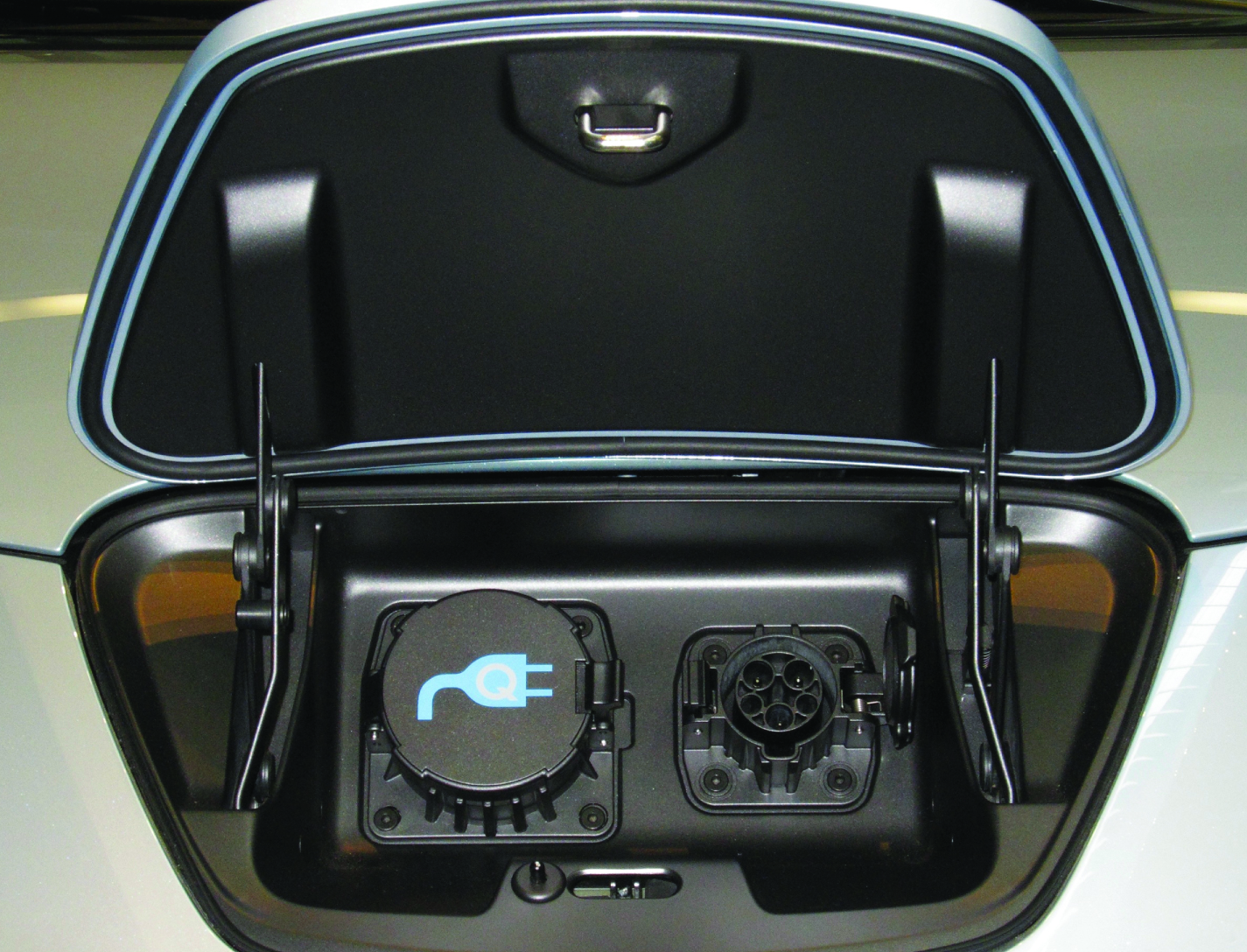
Battery Management System
The technology is comprised of a simple and reliable circuit that detects a single bad cell within a battery pack of hundreds of cells and it can monitor and balance the charge of individual cells in series. NASA's BMS is cost effective and can enhance safety and extend the life of critical battery systems, including high-voltage Li-ion batteries that are used in electric vehicles and other next-generation renewable energy applications.
The BMS uses saturating transformers in a matrix arrangement to monitor cell voltage and balance the charge of individual battery cells that are in series within a battery string. The system includes a monitoring array and a voltage sensing and balancing system that integrates simply and efficiently with the battery cell array, limiting the number of pins and the complexity of circuitry in the battery. The arrangement has inherent galvanic isolation, low cell leakage currents, and allows a single bad or imbalanced cell in a series of several hundred to be identified. Cell balancing in multi-cell battery strings compensates for weaker cells by equalizing the charge on all the cells in the chain, thus extending battery life. Voltage sensing helps avoid damage from over-voltage that can occur during charging and from under-voltage that can occur through excessive discharging.
mechanical and fluid systems
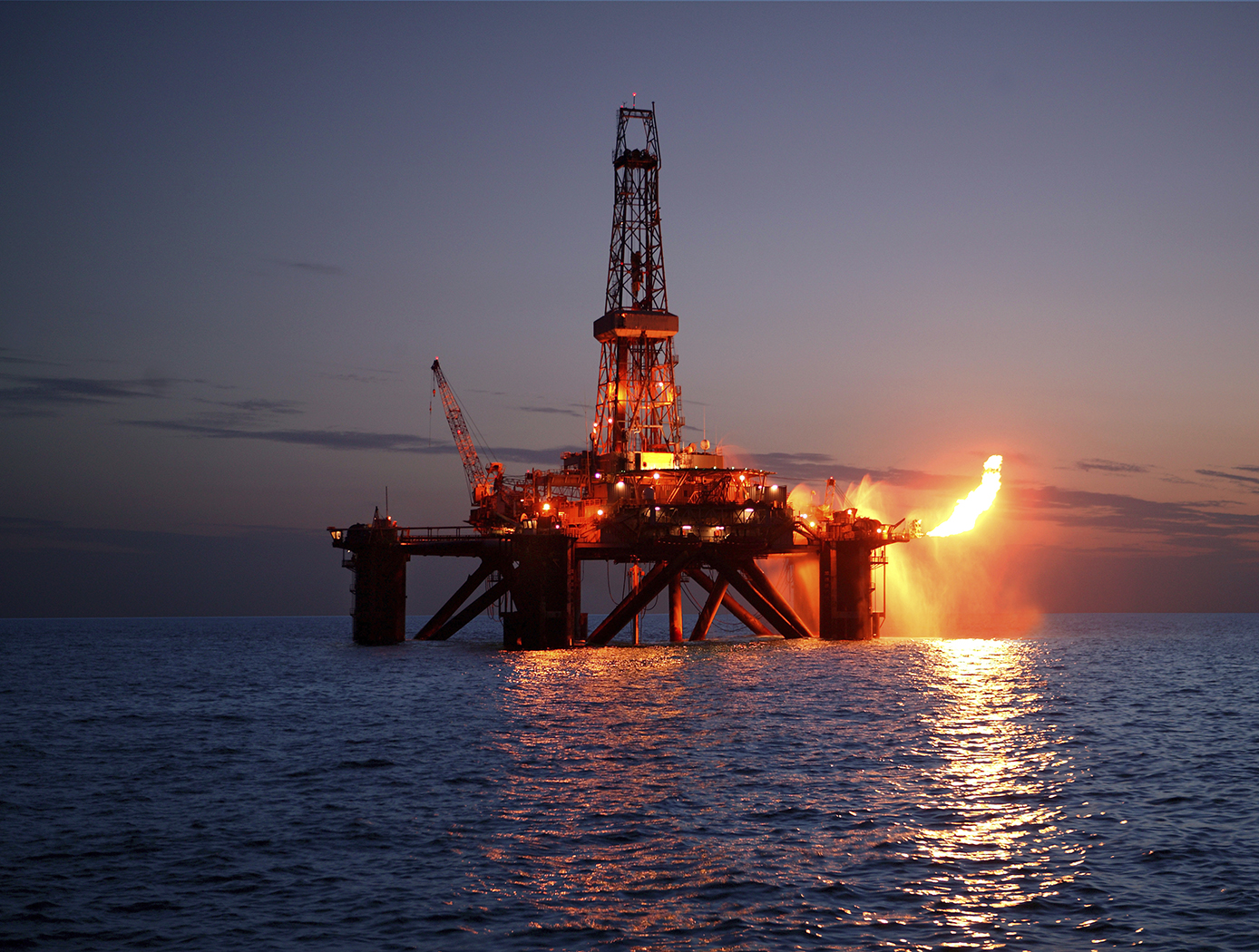
High-Temperature Single Crystal Preloader
For extremely high-temperature sealing applications, Glenn researchers have devised novel methods for fabricating single-crystal preloaders. NASA's high-temperature preloaders consist of investment cast or machined parts that are fabricated in various configurations from single crystal superalloys. Machined preloaders include a variety of spring configurations, compressed axially or radially, fabricated from single crystal slabs. Before machining, the slabs are carefully oriented in a special goniometer using x-diffraction techniques. This helps to maintain proper crystal orientation relative to the machined part and the applied loads. For more complex geometry components which cannot be easily and economically machined, an investment casting approach would be used. Complex preloader geometries include wire coil springs of various configurations. These single crystal preloaders would be designed with the appropriate stiffness for the intended thermal barrier/seal application and placed underneath, or integrated within, the seal/barrier. At extrememly high temperature, the preload device keeps the seal/barrier mated against the opposing surface as the gap between the two surfaces changes, maintaining contact between surfaces and preventing convective heat transfer.
electrical and electronics
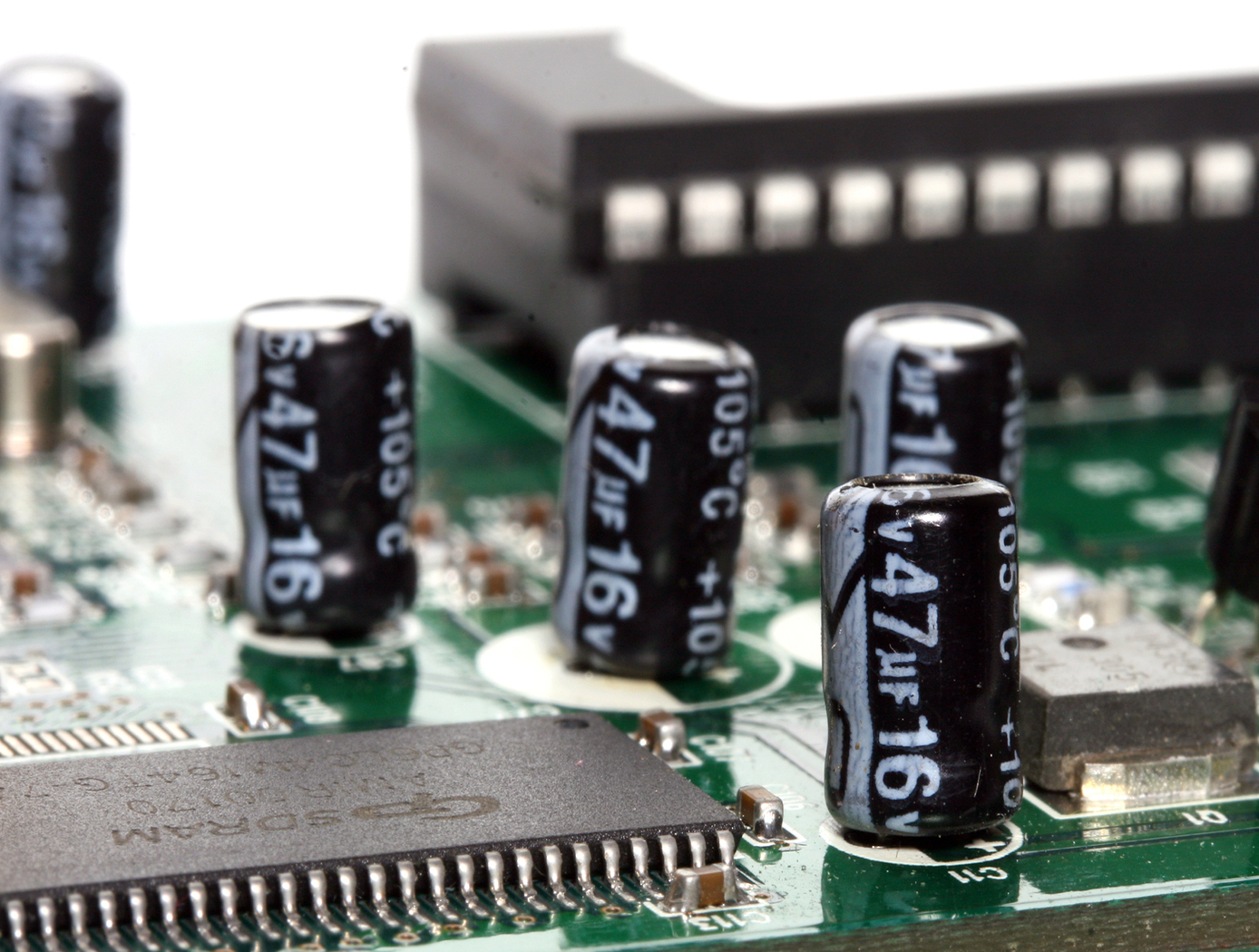
Metal Oxide-Vertical Graphene Hybrid Supercapacitors
The electrodes are soaked in electrolyte, separated by a separator membrane and packaged into a cell assembly to form an electrochemical double layer supercapacitor. Its capacitance can be enhanced by a redox capacitance contribution through additional metal oxide to the porous structure of vertical graphene or coating the vertical graphene with an electrically conducting polymer. Vertical graphene offers high surface area and porosity and does not necessarily have to be grown in a single layer and can consist of two to ten layers. A variety of collector metals can be used, such as silicon, nickel, titanium, copper, germanium, tungsten, tantalum, molybdenum, & stainless steel.
Supercapacitors are superior to batteries in that they can provide high power density (in units of kw/kg) and the ability to charge and discharge in a matter of seconds. Aside from its excellent power density, a supercapacitor also has a longer life cycle and can undergo many more charging sequences in its lifespan than batteries. This long life cycle means that supercapacitors last for longer periods of times, which alleviates environmental concerns associated with the disposal of batteries.
electrical and electronics
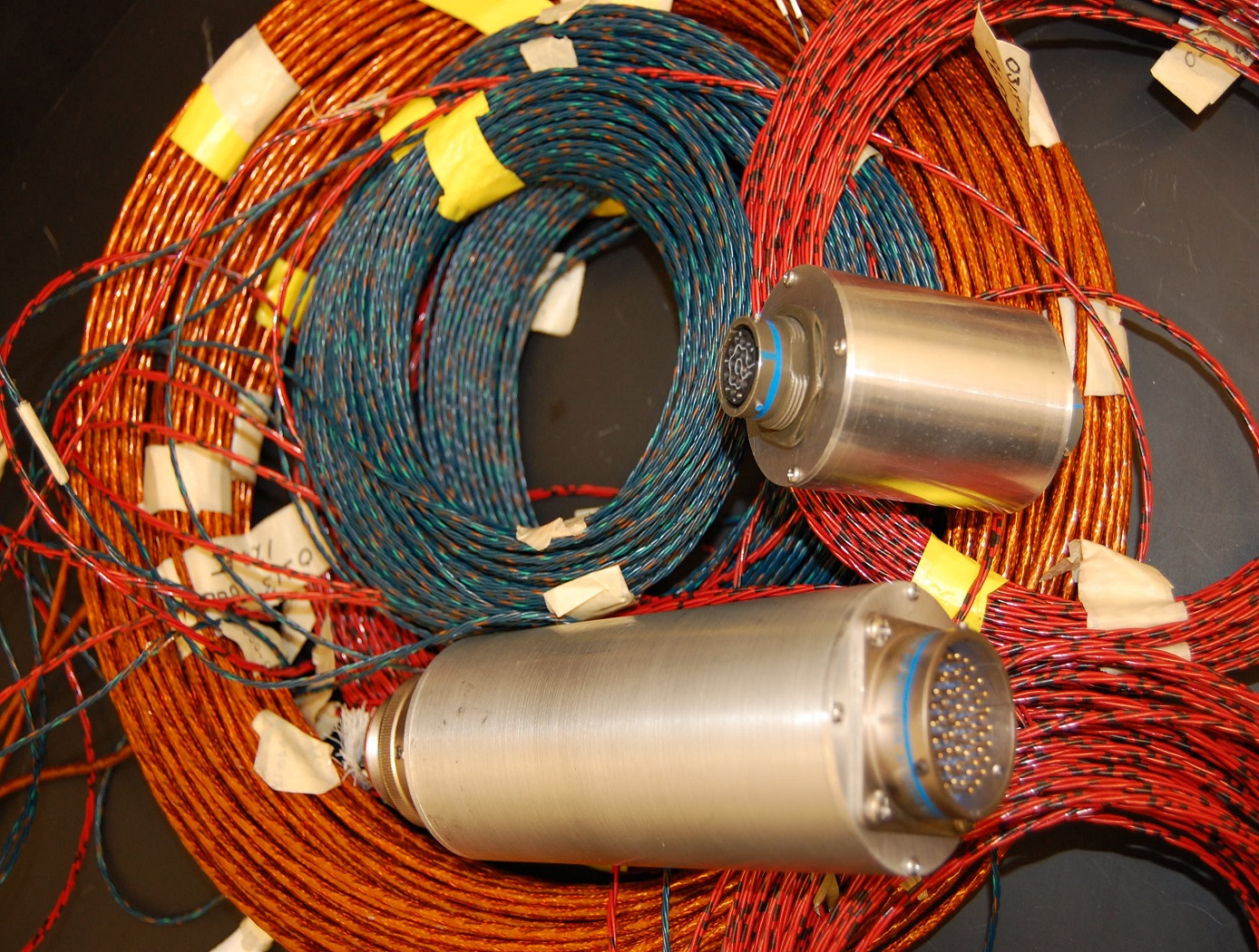
Self-Healing Wire Insulation
Insulation is necessary on electrical wires in order to protect electrical systems from shorting. In high voltage systems such shorting can lead to sparking and fires. Many lives have been lost due to electrical wire insulation failure. Many man hours are also expended in the repair and inspection of electrical wiring in order to attempt to prevent wire failure. Wire insulation with a built in "self-healing" capability would greatly improve the safety of systems containing electrical wiring. Such insulation would require far less inspection and repair time over the lifetime of the system.
Polyimides such as Kapton are an integral part of high performance electrical wire insulation. Traditional polyimides are very inert to solvents and do not melt. A new set of polyimides, developed for use as films for the manual repair of high performance electrical wire insulation, have a low melting point and can be dissolved in special solvents. These properties can be taken advantage of in self-healing polyimide films. Microcapsules containing a solvent soluble polyimide are prepared using industry standard inter-facial or in situ polymerization techniques. These capsules are then incorporated into a low melt polyimide film for use as either a primary electrical wire insulation or as one of several layers of a composite wire insulation. The low melt polyimide film substrate in which the microcapsules are incorporated has good solubility with the solvent used to dissolve the polyimide which makes up the fluid inside the microcapsule. Such a capsule filled insulation, when cut or otherwise damaged, will result in the release of the capsule contents into the cut or damage area. The solvent then dissolves a small amount of the surrounding polyimide insulation but will also begin the process of evaporation. The combination of these two processes allows for excellent intermingling of the healant and the surrounding substrate, resulting in a repair with superior bonding and physical properties.