Search
materials and coatings
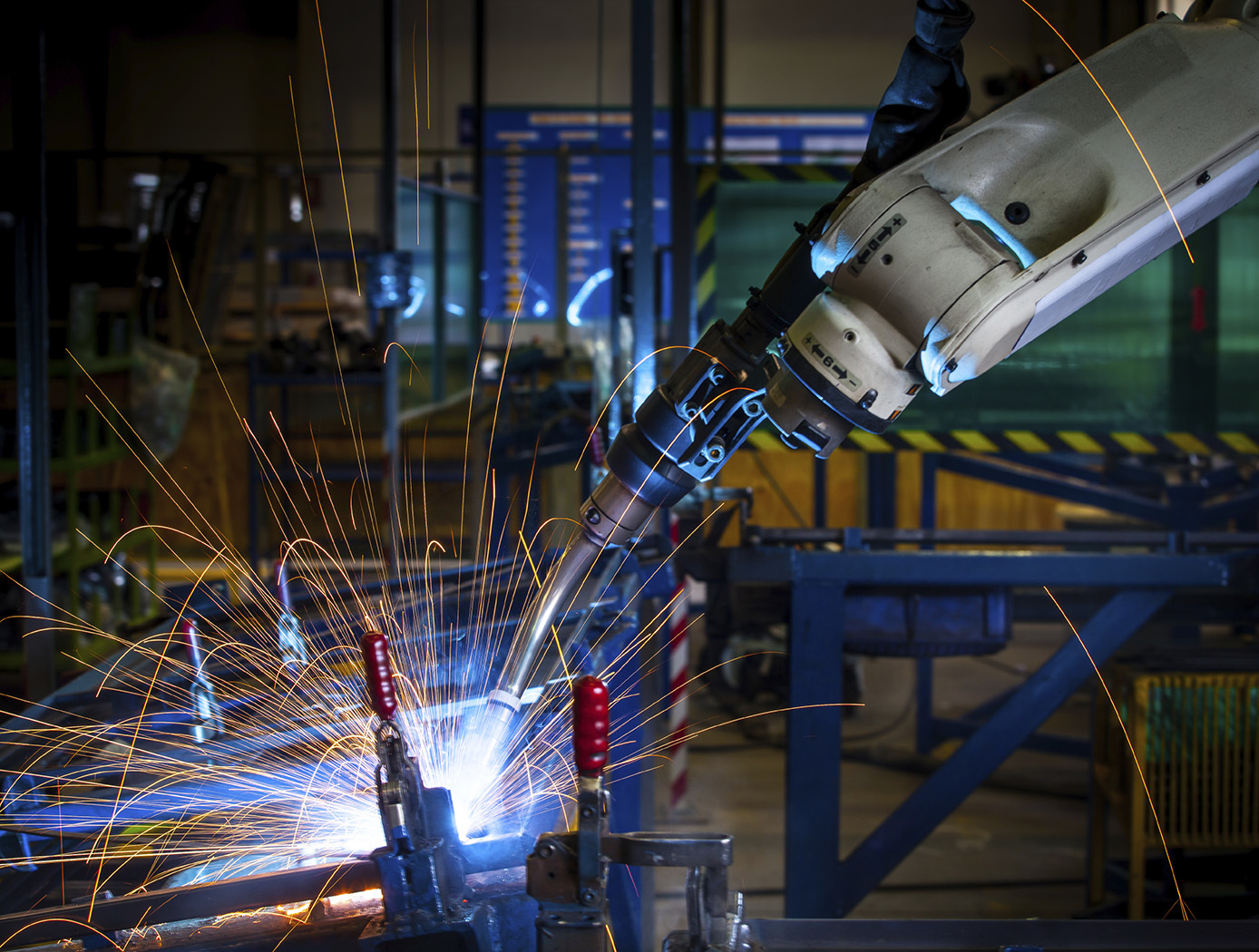
How to Train Shape Memory Alloys
Glenn researchers have optimized how shape memory alloys (SMAs) are trained by reconceptualizing the entire stabilization process. Whereas prior techniques stabilize SMAs during thermal cycling, under conditions of fixed stress (known as the isobaric response), what Glenn's innovators have done instead is to use mechanical cycling under conditions of fixed temperature (the isothermal response) to achieve stabilization rapidly and efficiently. This novel method uses the isobaric response to establish the stabilization point under conditions identical to those that will be used during service. Once the stabilization point is known, a set of isothermal mechanical cycling experiments is then performed using different levels of applied stress. Each of these mechanical cycling experiments is left to run until the strain response has stabilized. When the stress levels required to achieve stabilization under isothermal conditions are known, they can be used to train the material in a fraction of the time that would be required to train the material using only thermal cycling. As the strain state has been achieved isothermally, the material can be switched back under isobaric conditions, and will remain stabilized during service. In short, Glenn's method of training can be completed in a matter of minutes rather than in days or even weeks, and so SMAs become much more practical to use in a wide range of applications.
mechanical and fluid systems
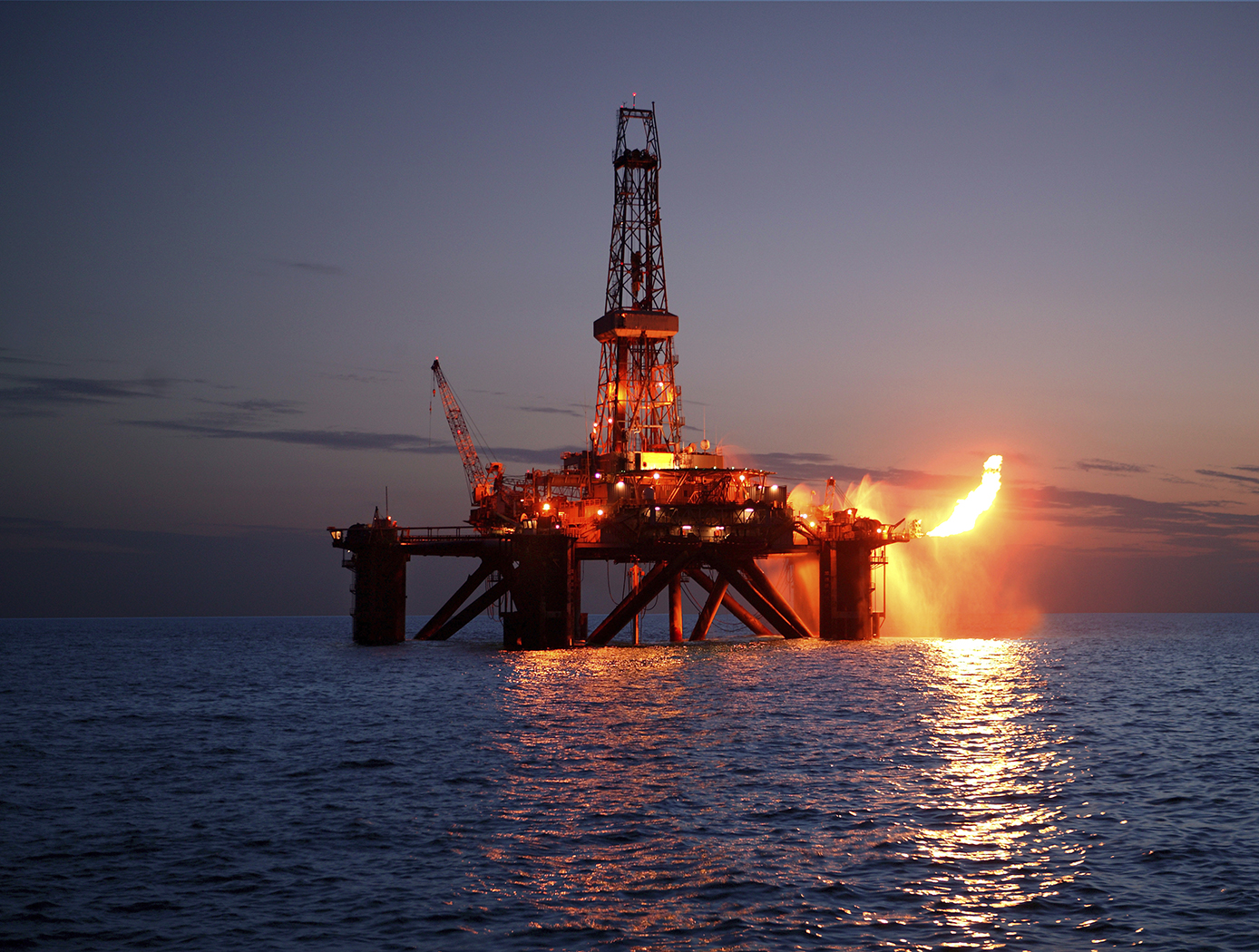
High-Temperature Single Crystal Preloader
For extremely high-temperature sealing applications, Glenn researchers have devised novel methods for fabricating single-crystal preloaders. NASA's high-temperature preloaders consist of investment cast or machined parts that are fabricated in various configurations from single crystal superalloys. Machined preloaders include a variety of spring configurations, compressed axially or radially, fabricated from single crystal slabs. Before machining, the slabs are carefully oriented in a special goniometer using x-diffraction techniques. This helps to maintain proper crystal orientation relative to the machined part and the applied loads. For more complex geometry components which cannot be easily and economically machined, an investment casting approach would be used. Complex preloader geometries include wire coil springs of various configurations. These single crystal preloaders would be designed with the appropriate stiffness for the intended thermal barrier/seal application and placed underneath, or integrated within, the seal/barrier. At extrememly high temperature, the preload device keeps the seal/barrier mated against the opposing surface as the gap between the two surfaces changes, maintaining contact between surfaces and preventing convective heat transfer.
electrical and electronics
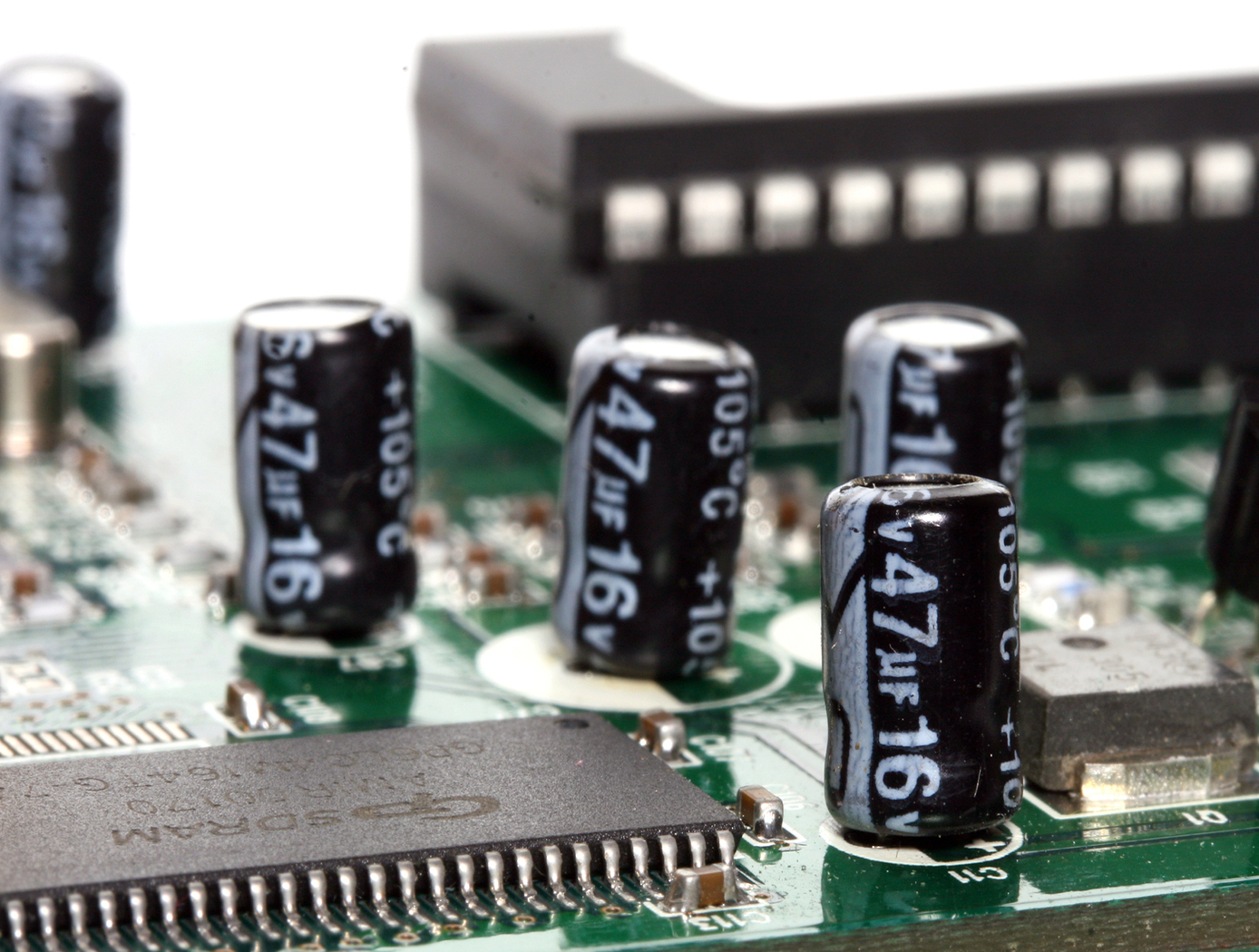
Metal Oxide-Vertical Graphene Hybrid Supercapacitors
The electrodes are soaked in electrolyte, separated by a separator membrane and packaged into a cell assembly to form an electrochemical double layer supercapacitor. Its capacitance can be enhanced by a redox capacitance contribution through additional metal oxide to the porous structure of vertical graphene or coating the vertical graphene with an electrically conducting polymer. Vertical graphene offers high surface area and porosity and does not necessarily have to be grown in a single layer and can consist of two to ten layers. A variety of collector metals can be used, such as silicon, nickel, titanium, copper, germanium, tungsten, tantalum, molybdenum, & stainless steel.
Supercapacitors are superior to batteries in that they can provide high power density (in units of kw/kg) and the ability to charge and discharge in a matter of seconds. Aside from its excellent power density, a supercapacitor also has a longer life cycle and can undergo many more charging sequences in its lifespan than batteries. This long life cycle means that supercapacitors last for longer periods of times, which alleviates environmental concerns associated with the disposal of batteries.
manufacturing
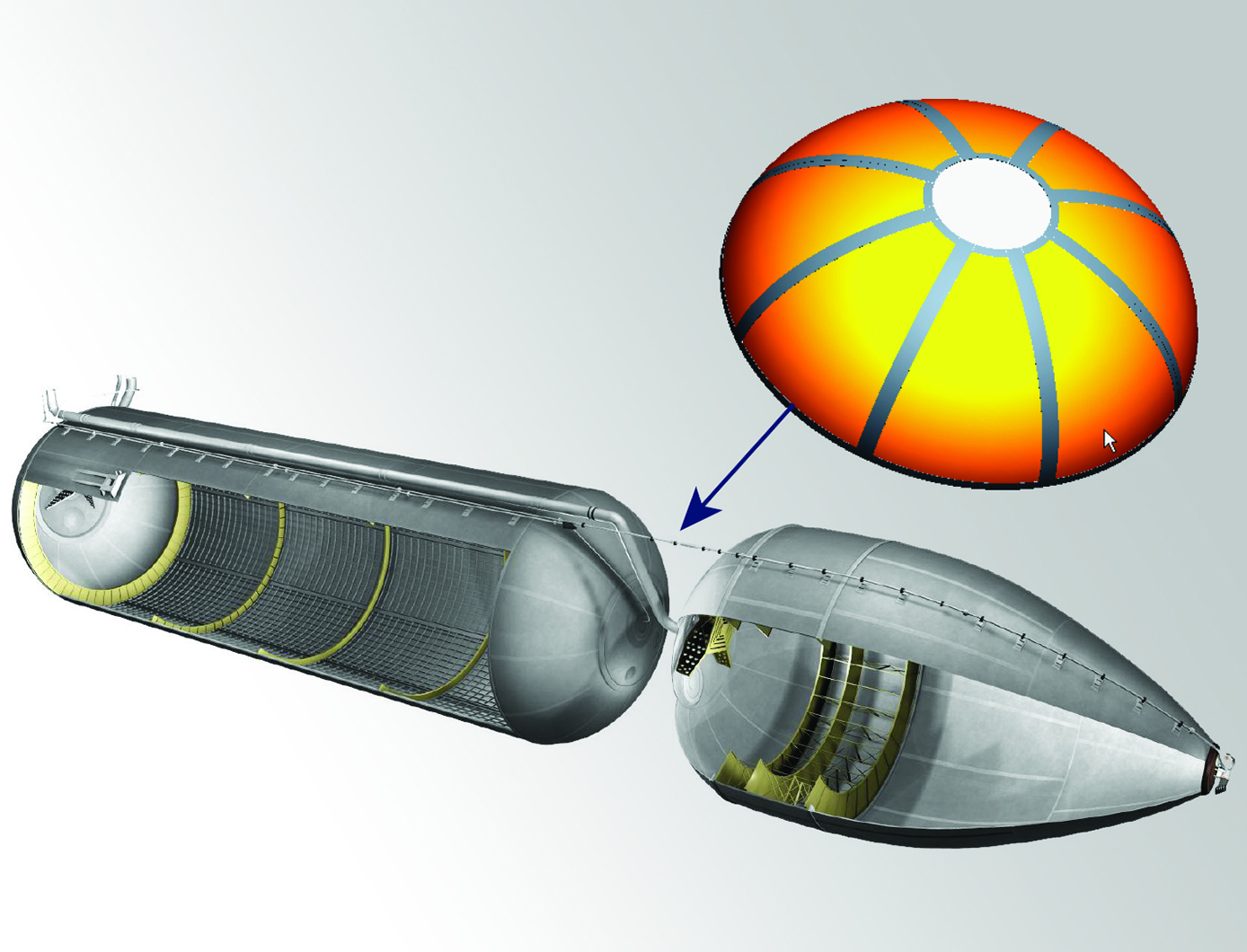
Improving Formability of Al-Li Alloys
Via this NASA innovation, a product is first heated to a temperature within the range of 204 to 343 degrees C for an extended soak of up to 16 hours. The product is then slowly heated to a second temperature within the range of 371 to 482 degrees C for a second soak of up to 12 hours. Finally, the product is slowly cooled to a final soak temperature of 204 to 343 degrees C before cooling to room temperature. The product so treated will exhibit greatly improved formability.
To date, the low formability issue has limited the use of lightweight Al-Li alloys for large rocket fuel tank dome applications. Manufacturing a dome by stretch forming typically requires multiple panels as well as multiple welding and inspection steps to assemble these panels into a full-scale fuel tank dome. Complex tensile and bending stresses induced during the stretch forming operations of Al-Li alloys have resulted in high rates of failure for this process. To spin form a large rocket dome, the spin blank must be prepared by joining smaller plates together using friction stir welding. However, friction stir welding produces a distinct metallurgical structure inside and around the friction stir weld that makes it very susceptible to cracking during spin forming.
manufacturing
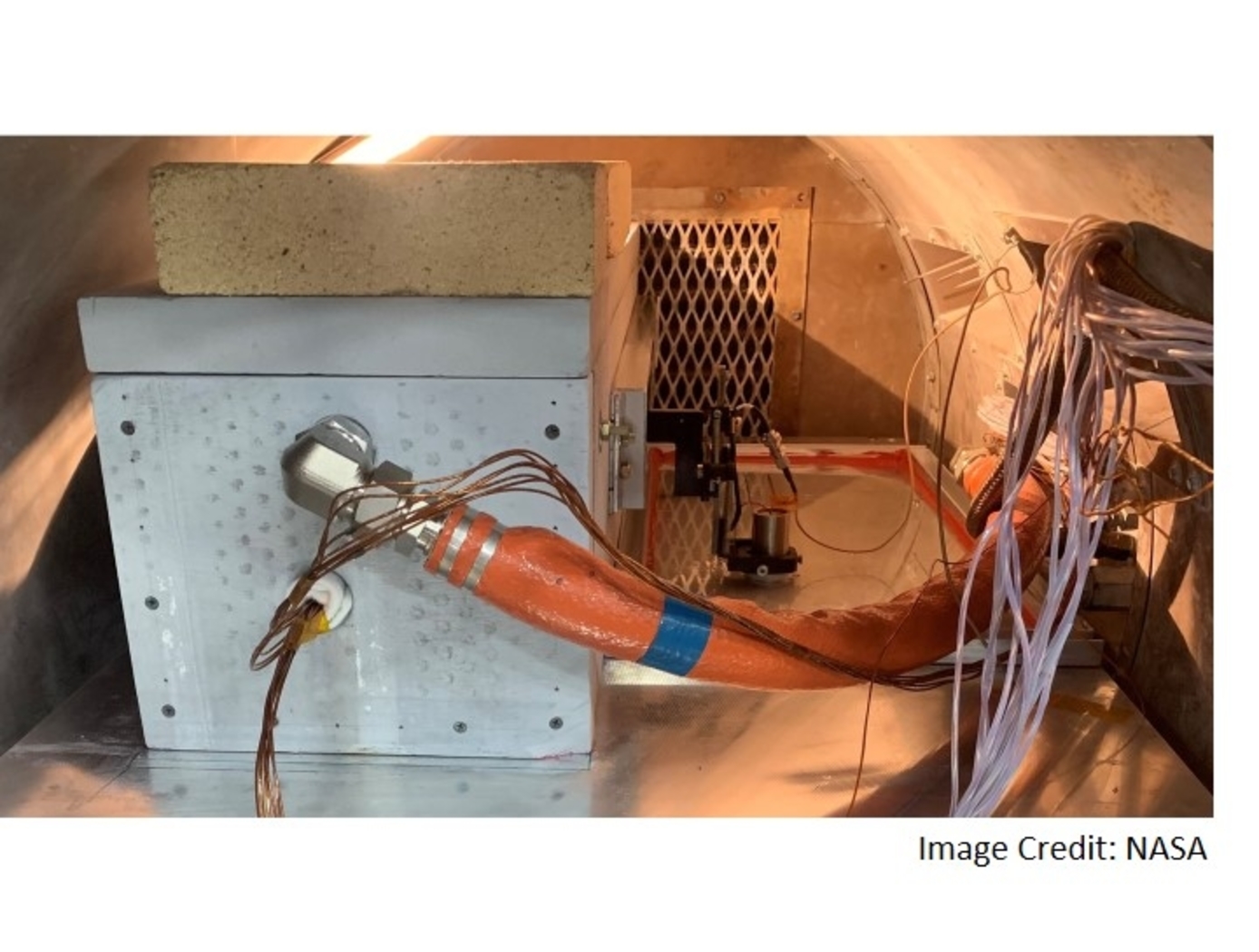
System for In-situ Defect Detection in Composites During Cure
NASA's System for In-situ Defect (e.g., porosity, fiber waviness) Detection in Composites During Cure consists of an ultrasonic portable automated C-Scan system with an attached ultrasonic contact probe. This scanner is placed inside of an insulated vessel that protects the temperature-sensitive components of the scanner. A liquid nitrogen cooling systems keeps the interior of the vessel below 38°C. A motorized X-Y raster scanner is mounted inside an unsealed cooling container made of porous insulation boards with a cantilever scanning arm protruding out of the cooling container through a slot. The cooling container that houses the X-Y raster scanner is periodically cooled using a liquid nitrogen (LN2) delivery system. Flexible bellows in the slot opening of the box minimize heat transfer between the box and the external autoclave environment. The box and scanning arm are located on a precision cast tool plate. A thin layer of ultrasonic couplant is placed between the transducer and the tool plate. The composite parts are vacuum bagged on the other side of the tool plate and inspected. The scanning system inside of the vessel is connected to the controller outside of the autoclave. The system can provide A-scan, B-scan, and C-scan images of the composite panel at multiple times during the cure process.
The in-situ system provides higher resolution data to find, characterize, and track defects during cure better than other cure monitoring techniques. In addition, this system also shows the through-thickness location of any composite manufacturing defects during cure with real-time localization and tracking. This has been demonstrated for both intentionally introduced porosity (i.e., trapped during layup) as well processing induced porosity (e.g., resulting from uneven pressure distribution on a part). The technology can be used as a non-destructive evaluation system when making composite parts in in an oven or an autoclave, including thermosets, thermoplastics, composite laminates, high-temperature resins, and ceramics.
Sensors

Advanced Thermal Inspection with Pulsed Light Emitting Diodes (PLED) Technology
NASA’s PLED thermal inspection system consists of an array of high- powered LED chips configured to deliver controlled pulses of visible light. The system includes 8 LED chip arrays, mounted on an aluminum heat sink and housed in a hood configuration. The inspection hood is specially designed with filters to prevent internal reflections. The LEDs are powered by regulated power supplies and controlled via a computer interface that synchronizes heat pulses with an infrared camera. An acrylic filter is placed over the LEDs to block residual infrared radiation, ensuring that only visible light reaches the target surface. The system’s infrared camera, operating in the mid-wave infrared (MWIR) range does not detect the visible light and captures the transient thermal response of the material, allowing for precise defect detection. By eliminating the need for high-intensity broadband infrared sources, the PLED system provides a cleaner and more accurate thermal response, particularly for unpainted metals and additively manufactured (AM) components.
Performance validation of the PLED system has demonstrated significant advantages over traditional flash thermography. In tests on aluminum samples with material loss and AM Ti-6Al-4V metal specimens, the PLED system successfully detected defects with superior contrast and no heat source reflections. Principal Component Analysis (PCA) applied to PLED inspection data revealed clearer defect indications compared to flash-based methods, which introduced unwanted artifacts due to transient reflections. Additionally, the PLED system enabled quantitative thermal diffusivity measurements, offering a new approach to single-sided material characterization.
NASA's PLED thermal inspection technology is available for patent licensing. Potential applications include corrosion detection in aerospace components, quality control of AM metal parts, structural health monitoring of industrial materials, and more.