Search
materials and coatings

Multi-layered Self-healing Material System for Impact Mitigation
This innovation utilizes a tri-layered structure, comprised of solid plastic front and back layers sandwiching a viscous, reactive liquid middle layer. Combined, this system provides rapid self-healing following high velocity ballistic penetrations. Self-healing in the front and back layers occurs when the puncture event creates a melt state in the polymer materials and the materials melt elasticity snaps back and closes the hole. The viscous middle layer augments the self-healing properties of the other layers by flowing into the gap created by a ballistic puncture and concurrently solidifying due to the presence of oxygen. Thus, this innovation has two tiers of self-healing: a puncture-healing mechanism triggered by the projectile and a second mechanism triggered by the presence of oxygen.
Materials and Coatings
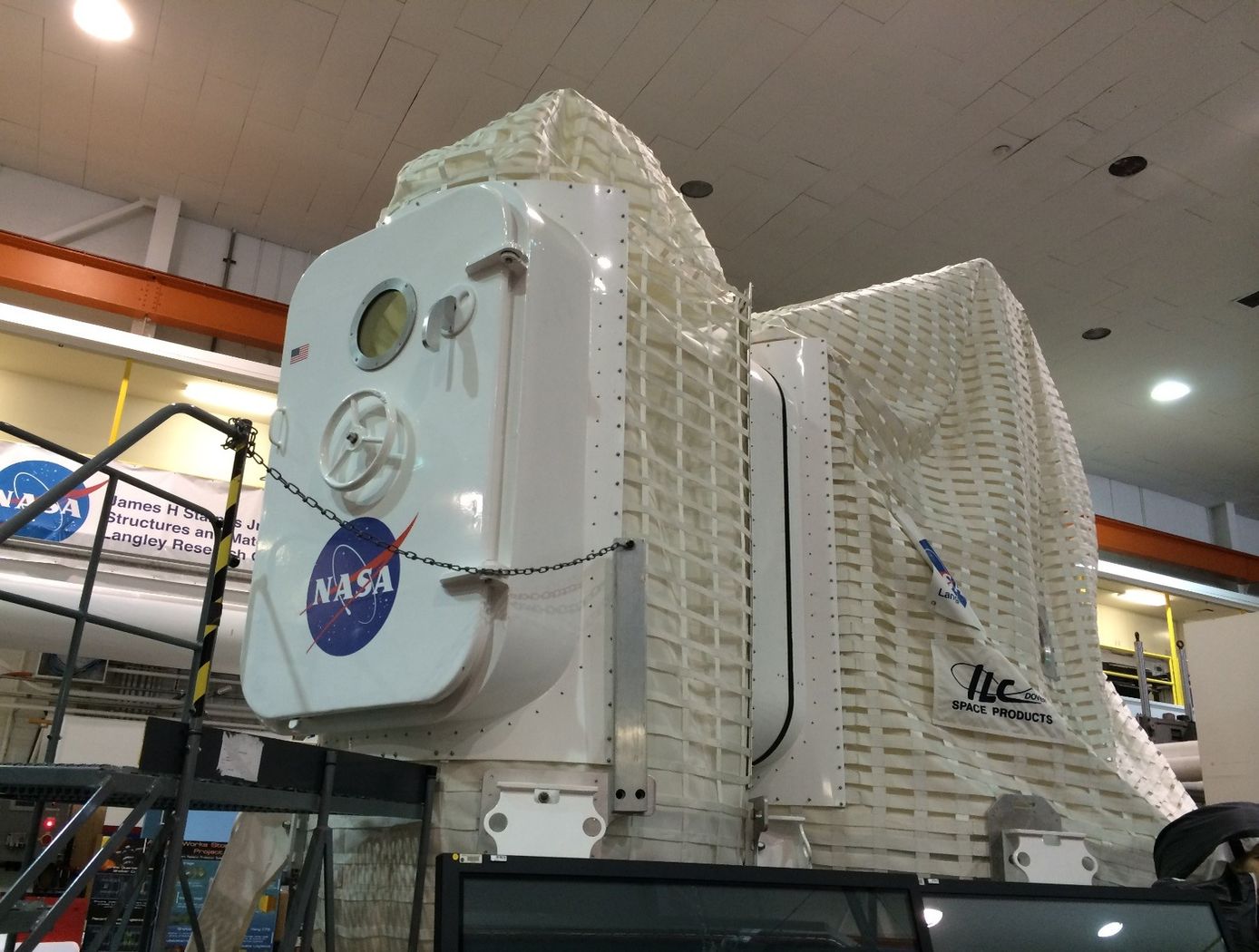
Mechanoresponsive Healing Polymers
The method chemically introduces mechanically sensitive chemical groups into the structure of a resin. By introducing mechanoresponsive functional groups to a polymer, it is possible to induce self-healing through the transformation of such chemical groups to where mechanical properties of a structure are almost completely restored. The forces imparted by a damage event can therefore be used to enable healing or repair of the structure.
Mechanical and Fluid Systems
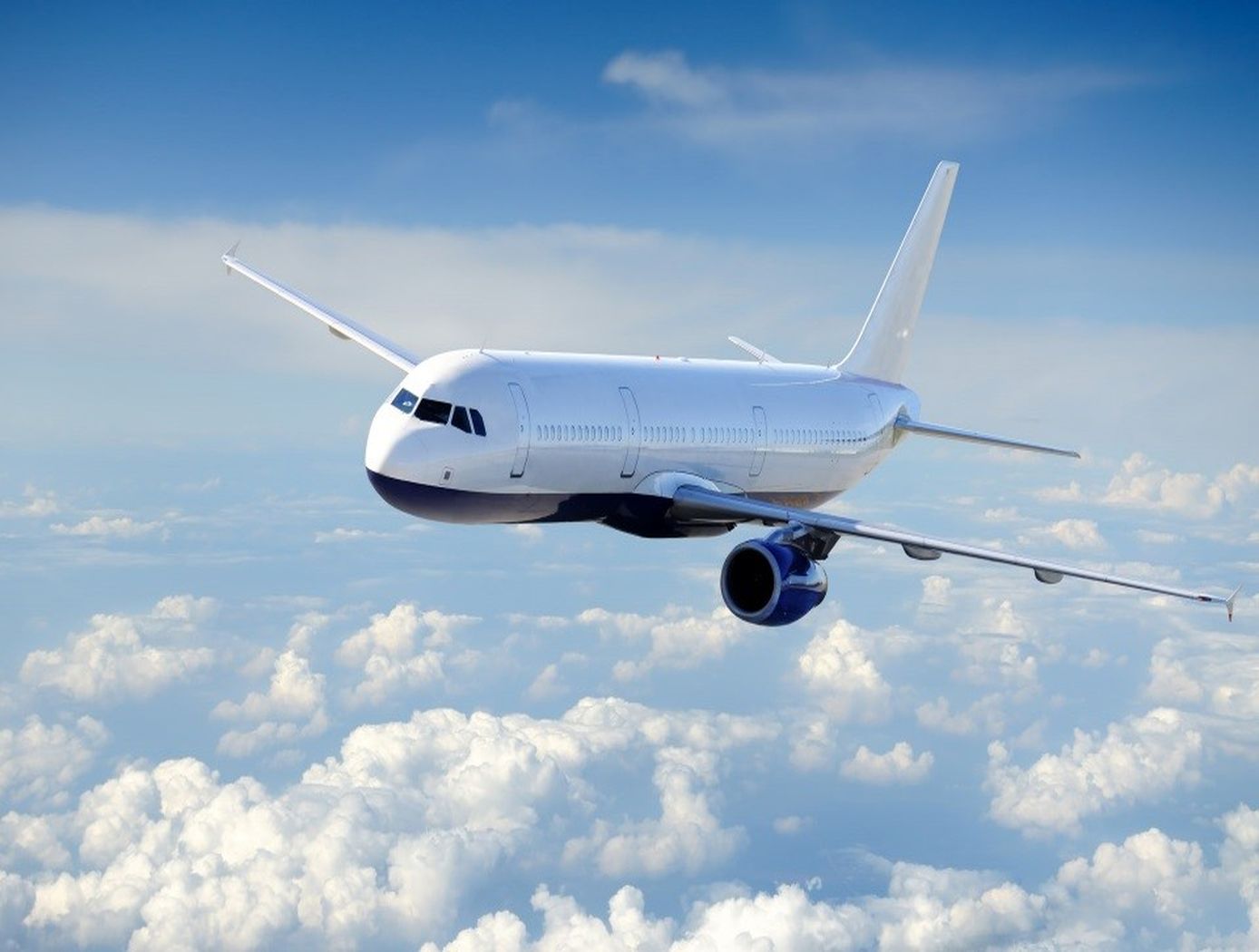
Healable Carbon Fiber Reinforced Composites
A composite fabrication process cycle was developed from composite precursor materials developed at LaRC to fabricate composite laminates. The precursor material is a pre-impregnated unidirectional carbon fiber preform, or prepreg. In the pre-pregging process, the high strength, structural reinforcing carbon fiber is wetted by a solution containing a self-healing polymer. The resulting material is of aerospace quality and exhibits a significant decrease of internal damage following impacts tests (using ASTM D 7137 standard).
manufacturing

Ultrasonic Stir Welding
Ultrasonic Stir Welding is a solid state stir welding process, meaning that the weld work piece does not melt during the welding process. The process uses a stir rod to stir the plasticized abutting surfaces of two pieces of metallic alloy that forms the weld joint. Heating is done using a specially designed induction coil. The control system has the capability to pulse the high-power ultrasonic (HPU) energy of the stir rod on and off at different rates from 1-second pulses to 60-millisecond pulses. This pulsing capability allows the stir rod to act as a mechanical device (moving and stirring plasticized nugget material) when the HPU energy is off, and allowing the energized stir rod to transfer HPU energy into the weld nugget (to reduce forces, increase stir rod life, etc.) when the HPU energy is on. The process can be used to join high-melting-temperature alloys such as titanium, Inconel, and steel.
materials and coatings
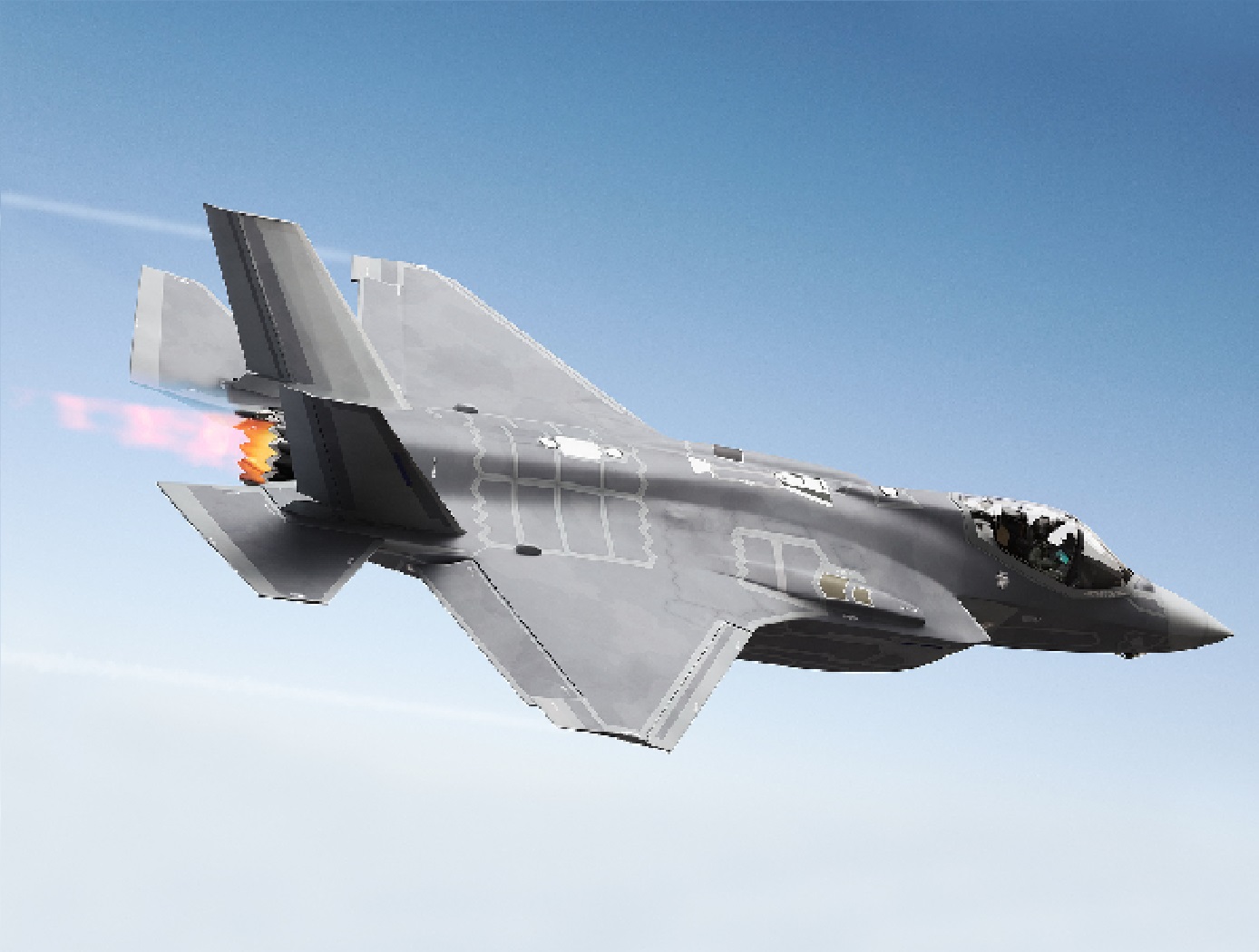
Enhanced Software Suite Maximizes Non-Destructive Evaluation (NDE) Methods
This technology provides comprehensive, detailed, and accurate NDE detection and characterization of subsurface defects in composites and some metallic hardware. This complete software suite normalizes and calibrates the data, which provides more stable measurements and reduces the occurrence of errors due to the operator and to camera variability.
When using flash IR thermography to evaluate materials, variations in the thermal diffusivity of the material manifest themselves as anomalies in the IR image of the test surface. Post-processing of this raw IR camera data provides highly detailed analysis of the size and characterization of anomalies. The newly incorporated Transient and Lock-In Thermography methods allow the analysis of thicker material and with better flaw resolution than Flash Thermography alone.
The peak contrast and peak contrast time profiles generated through this analysis provide quantitative interpretation of the images, including detailed information about the size and shape of the anomalies. The persistence energy and persistence time profiles provide highly sensitive data for detected anomalies. Peak contrast, peak time, persistence time, and persistence energy measurements also enable monitoring for flaw growth and signal response to flaw size analysis.
This technology is at a technology readiness level (TRL) of 7 (system prototype demonstration in an operational environment), and the innovation is now available for your company to license. Please note that NASA does not manufacture products itself for commercial sale.