Search
Power Generation and Storage

Carbon Fiber Sleeve Tempers Battery Thermal Runaway
The CFRP sleeve was originally intended for crewed space flight lithium-ion 18650 battery packs rated over 80 Watt-hours (Wh), which are required to be passively propagation-resistant for increased safety. Previous battery designs have addressed SWR propagation by using aluminum or steel interstitial materials to prevent SWRs from directly impacting neighboring cells, but these materials were underperforming.
During testing of 18650 battery cells, it was discovered that cells over 2.6Ah in capacity can have an undesirable failure mode in which the cell wall will rupture or breach during a thermal runaway (TR) event sending heat and ejecta into an undesirable direction. TR is typically triggered when heat produced by the battery cell’s exothermic reaction leads to increased and escalating internal cell temperature, pressure, and boiling of the electrolytes. When internal cell pressure exceeds the cell’s safety relief mechanism, rupture or bursting can occur, initiating a cell-to-cell propagation that in turn results in a battery pack fire.
By adding a carbon fiber reinforced polymer (CFRP) sleeve to cylindrical battery cells, a sidewall rupture (SWR) can be prevented from occurring or propagating. In initial testing, there were no SWRs of a battery cell using a CFRP sleeve. This result is believed to be due in part to a unique characteristic of CFRP sleeves compared to other materials. Carbon fiber material has a negative coefficient of expansion and accordingly shrinks when heated, while steel and aluminum expand. The shrinking of the CFRP sleeve when heated compresses the cell located within it, significantly aiding in the prevention of SWR.
This technology can be implemented into other multi-physics battery safety models to guide the design of the next generation of battery cells and battery packs.
This thermal runaway propagation resistant technology has a technology readiness level (TRL) of 6 (System/sub-system model or prototype demonstration in an operational environment) and is now available for patent licensing. Please note that NASA does not manufacture products itself for commercial sale.
Electrical and Electronics
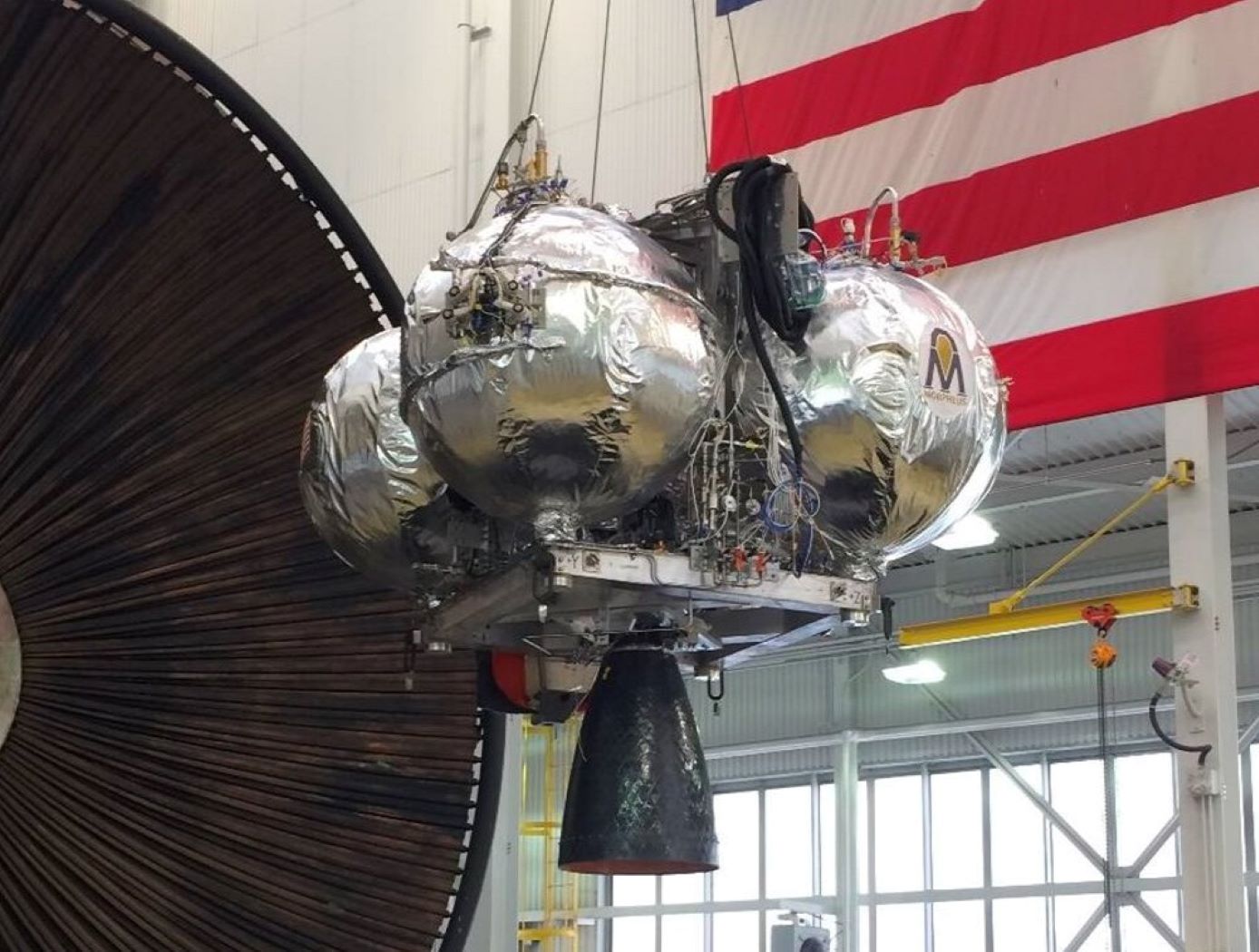
Coil-On-Plug Igniter for Reliable Engine Starts
Spark-ignition devices have proven to be a high-reliability option for LOX/LCH4 ignition during development of the Integrated Cryogenic Propulsion Test Article (ICPTA) main and reaction control engines (RCEs); however, issues including spark plug durability (ceramic cracking) and corona discharge during simulated altitude testing have been observed, contributing to degraded spark output and no-light engine-start conditions. Innovators discovered that ignition system reliability could be improved and weight reduced by eliminating the traditional coil and spark plug wire. To achieve this result, engineers made the innovation by modifying an automotive coil-on-plug igniter to provide new high sparking energies at the point of combustion using low supply voltages. The coil was modified by vacuum-potting it into a threaded interface that mounts into existing spark plug ports on the ICPTA main engine and the RCEs. Engineers fabricated custom electrode tips that were thread-mounted into the potted coil body. Epoxy insulation was chosen with high dielectric strength to maintain insulation between the electrode and threaded adapter. Vacuum potting successfully prevented pressure or vacuum leakage into the coil body and maintained spark energy and location at the electrode tip. Successful hot-fire ignition was observed at sea-level, altitude, and thermal-vacuum for both ICPTA RCE and main engine igniters down to 10^-3 torr, which approaches the vacuum of cislunar space.
This technology is at technology readiness level (TRL) 7 (system prototype demonstration in an operational environment), and the related patent is now available to license. Please note that NASA does not manufacture products itself for commercial sale.
Aerospace

Aerodynamic Framework for Parachute Deployment from Aerial Vehicle
For rapid parachute deployment simulation, the framework and methodology provided by the simulation database uses parametrized aerodynamic data for a variety of environmental conditions, air taxi design parameters, and landing system designs. The database also includes a compilation of drag coefficients, thrust and lift forces, and further relevant aerodynamic parameters utilized in the simulated flight of a proposed air taxi. The database and framework can be constructed using simulated data that accounts for oscillatory breathing of parachutes. The methodology can further employ an overset grid of body-fitted meshes to accurately capture deployment of an internally-stored parachute, as well as descent of the air taxi and deployed parachute.
The systems and methods of the disclosed technology can be utilized with existing CFD solvers in a plug-and-play manner, such that the framework can be integrated to directly improve the performance of these solvers and the machines on which they are installed. The framework itself can employ parallelization to enable distributed solution of intensive CFD simulations to build a robust database of simulated data. Further, as up to 90% of computational time is spent in the calculation of aerodynamic parameters for use in coupled trajectory equations, the framework can significantly reduce the computational costs and design time for safe landing systems for air taxis. These reductions can lead to lower costs for design processes, while enabling rapid design and testing prior to physical prototyping.
Aerospace
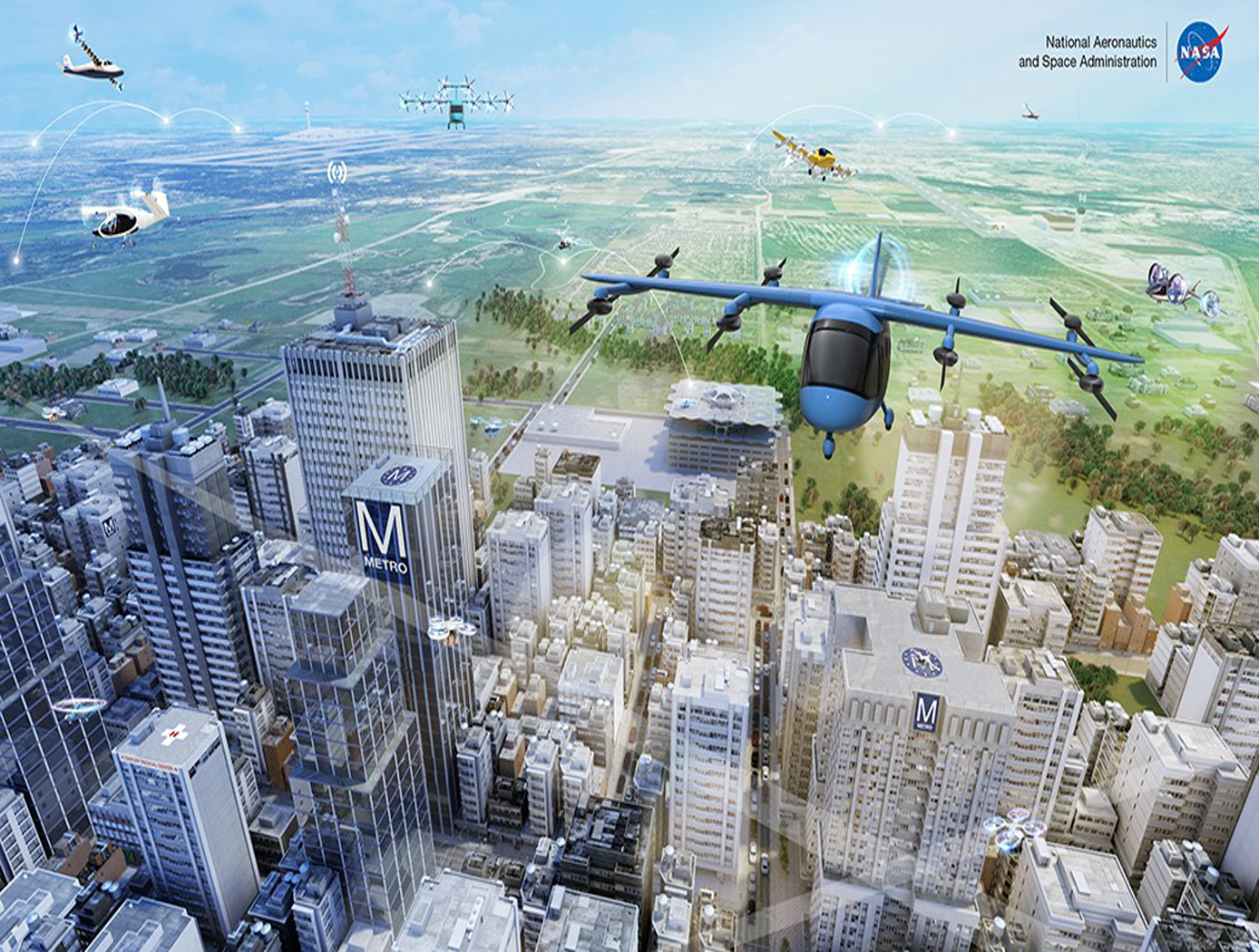
Active Turbulence Suppression System for Electric Vertical Take-Off and Landing (eVTOL) vehicles
The Active Turbulence Suppression (ATS) system for electric Vertical Take-Off and Landing (eVTOL) vehicles employ existing lifting propellers to dampen instabilities during flight, such as Dutch-roll oscillations and other gust-induced oscillations. When a roll angle of an eVTOL aircraft has deviated or is about to deviate from a current stable aircraft state to an undesirable, unstable, and oscillating aircraft state, the ATS system queries a turbulence suppression database that stores a set of propeller speed profiles for mitigation a deviation of a given roll angle for a particular aircraft with specified propellers. Using this data, the eVTOL flight controller adjusts the speed of the propellers for a certain duration of time, according to the propeller speed profiles for mitigating the deviation. In models of aircraft with adjustable propeller angles, the database includes blade angle profiles for mitigating the effects of turbulent conditions. Timing and rate of propeller activation can be pre-computed using higher order computational modeling performed with NASA’s super computing resources. Because the data is pre-computed, the use of the ATS system onboard does not require significant computing resources to implement on eVTOL vehicles. The technology, a mechanism by which existing eVTOL propellers are leveraged to suppress gust-induced oscillations enables a safe and comfortable passenger experience at low-cost and without added hardware.
information technology and software
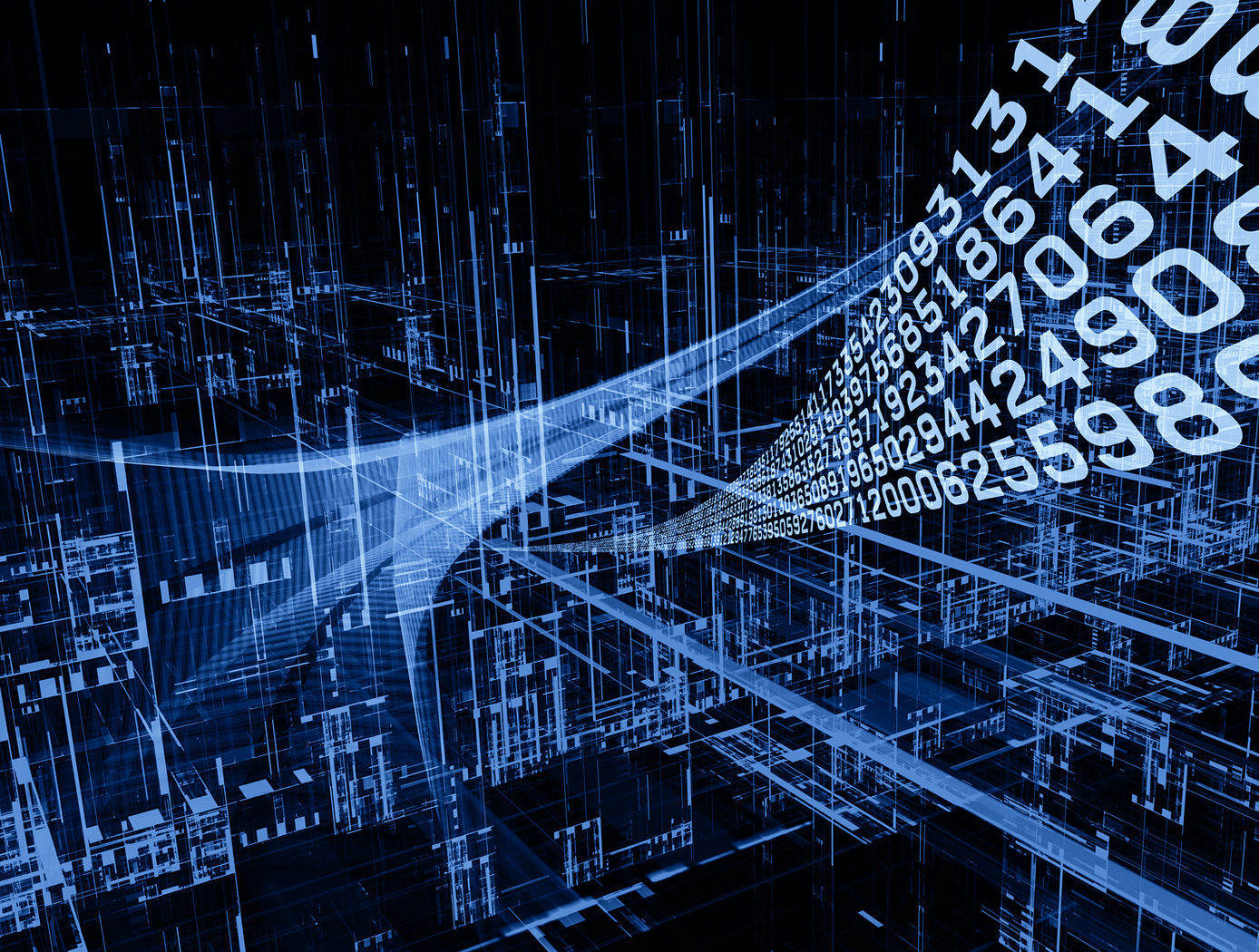
Enhancing Fault Isolation and Detection for Electric Powertrains of UAVs
The tool developed through this work merges information from the electric propulsion system design phase with diagnostic tools. Information from the failure mode and effect analysis (FMEA) from the system design phase is embedded within a Bayesian network (BN). Each node in the network can represent either a fault, failure mode, root cause or effect, and the causal relationships between different elements are described through the connecting edges.
This novel approach can help Fault Detection and Isolation (FDI), producing a framework capable of isolating the cause of sub-system level fault and degradation.
This system:
Identifies and quantifies the effects of the identified hazards, the severity and probability of their effects, their root cause, and the likelihood of each cause;
Uses a Bayesian framework for fault detection and isolation (FDI);
Based on the FDI output, estimates health of the faulty component and predicts the remaining useful life (RUL) by also performing uncertainty quantification (UQ);
Identifies potential electric powertrain hazards and performs a functional hazard analysis (FHA) for unmanned aerial vehicles (UAVs)/Urban Air Mobility (UAM) vehicles.
Despite being developed for and demonstrated with an application to an electric UAV, the methodology is generalized and can be implemented in other domains, ranging from manufacturing facilities to various autonomous vehicles.
Power Generation and Storage

Triggering Li-ion Battery Cells with Laser Radiation
This technology is based upon a 120-watt IR laser is coupled to a fiber optic cable that is routed from the output of the laser into a series of focusing optics which directs energy onto a battery cell mounted to a test stand. When activated, heat from the laser penetrates the metal housing, heating the internals of the cell. At a specific temperature, the separator in the first few layers of the cell melts allowing the anode and cathode to make contact and initiates an internal short circuit. The internal short circuit then propagates throughout the battery eventually causing thermal runaway. The lower the wavelength of the laser used to produce the thermal runaway, the more heat-energy will be absorbed into the cell producing a faster result. The fiber optic cable can be terminated into a series of optics to focus the laser at a specific target, or the fiber optic cable can be stripped bare and placed next to the target to heat an isolated location. This method can also be used on a wide variety of cells, including Li-ion pouch cells, Li-ion cylindrical cells and Li-ion Large format cells.
The innovation Triggering Li-ion Cells with Laser Radiation is at TRL 6 (which means a system/subsystem prototype has been demonstrated in a relevant environment) and the related patent application is now available to license and develop into a commercial product. Please note that NASA does not manufacture products itself for commercial sale.