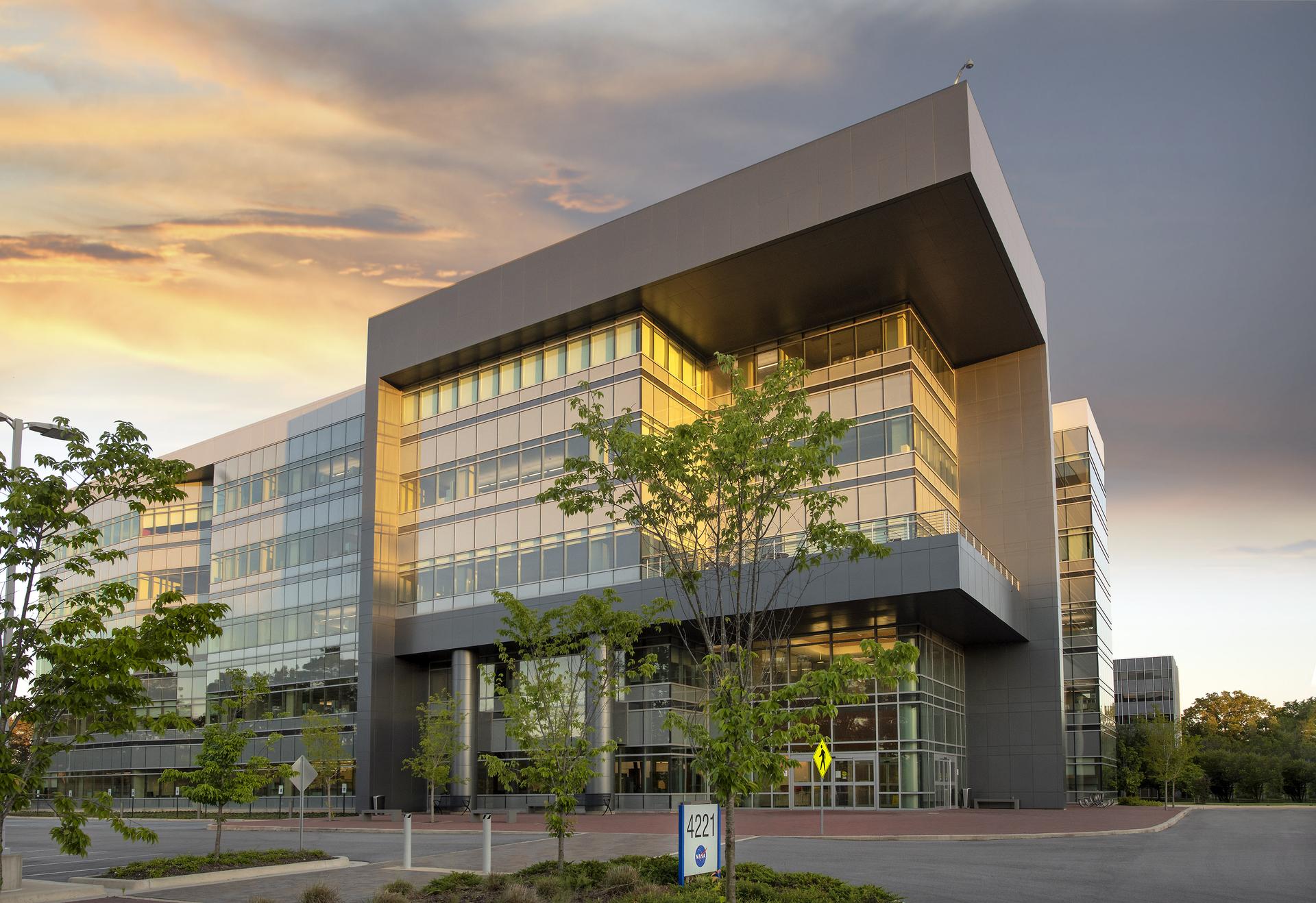
Marshall Space Flight Center (MSFC) makes some of the most vital propulsion systems and hardware for NASA’s flagship launch vehicles and has anchored the north Alabama region since the 1960s.
In 1950, Dr. Wernher von Braun's team moved to the Redstone Arsenal near Huntsville, Alabama, where they designed the Army's Redstone and Jupiter ballistic missiles, as well as the Jupiter C, Juno II, and Saturn I launch vehicles.
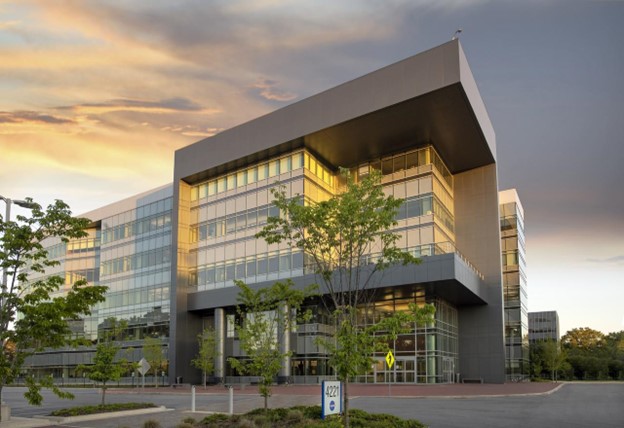
By 1960, President Eisenhower reassigned von Braun’s team of rocket scientists from the Army to the newly established National Aeronautics and Space Administration (NASA). Their mission: to develop the powerful Saturn rockets. Since those formative years, Marshall Space Flight Center has grown into a workforce of 7,000 individuals. We have undertaken groundbreaking projects such as testing and developing the Space Shuttle boosters, the Ares rocket, the Hubble Space Telescope, and the Artemis Program.
MSFC includes a facility located in New Orleans, Louisiana called Michoud Assembly Facility (MAF). Being one of the largest manufacturing buildings in the world, it is the perfect spot to assemble large scale space structures. MAF is currently working on assembling NASA’s second rocket within the Artemis Program. The rocket will be the first to propel astronauts around the moon since the end of the Apollo Program.
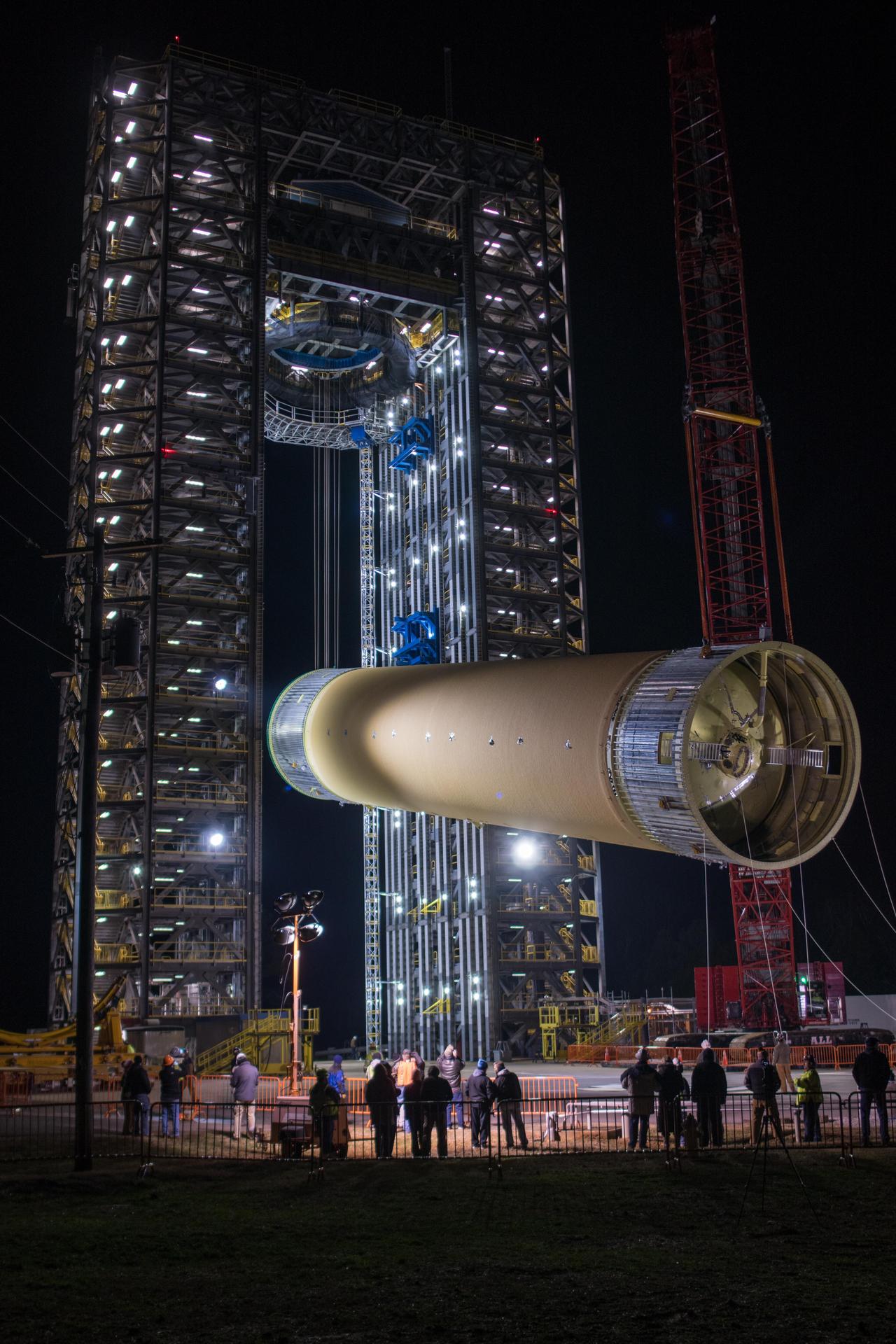
A host to many pioneers of space exploration, MSFC has developed multiple technologies that benefit mankind both on Earth and in outer space. Our mission is to make sure that these technologies are readily available to the public. MSFC specifically excels at aerospace, materials and coatings, environments, and manufacturing. All of MSFC’s patented technologies can be viewed online in our Patent Portfolio.
Aerospace: As our primary focus is space travel, MSFC has developed many different rocket engine configurations, propulsion techniques, and flight simulating software. One technology that is available for licensing is the Integral Tuned Mass Absorber for Turbine Blades. The unique design of this technology allows for the vibration reduction device to be fabricated right into the blade at no extra cost. It provides a significant reduction in turbine blade resonant vibration and can be used in many different fields that use rocket engine turbo pumps, jet engines, or turbomachinery.
MSFC is developing a lightweight one-piece regeneratively-cooled thrust chamber assembly (TCA) for liquid rocket engines. Liquid rocket engines create thrust through the expansion of combusted propellants within the TCA. Standard manufacturing of TCAs involves individually building the injector, main combustion chamber and nozzle, and then bolting or welding the components together at the joints. However, potential seal failures in these complex joints can cause catastrophic damage.

NASA researchers are eliminating complex joints by manufacturing a 1-piece TCA utilizing 3D printing and large-scale additive manufacturing technologies to directly deposit the nozzle onto the combustion chamber. And, by replacing a traditional solid metal jacket with a composite overwrap for support, the overall weight is reduced by over 40%. Developed under the Rapid Analysis and Manufacturing Propulsion Technology (RAMPT) project, NASA seeks public-private partnerships to develop specialized large-scale additive manufacturing vendors and accelerate reliable spaceflight hardware to the U.S. supply chain.
Materials and Coatings: MSFC has developed many high strength alloys in its pursuit for human space travel. While most are rated to withstand the elements of space, these technologies can be used in earthly applications as well. Al-Li alloys are used in aerospace for rocket and fuel tank domes and other large panels or extruded structures produced by stretch forming or spin forming. Improving heat treatments for other Al-Li alloys would expand potential applications in aerospace as well as in recreation, transportation, and other industries in which high-strength, lightweight structures are needed. Innovators developed a new cement composition and manufacturing method that enables carbon dioxide (CO2) emissions reduction in cement manufacturing while also providing a cement with improved performance capabilities.
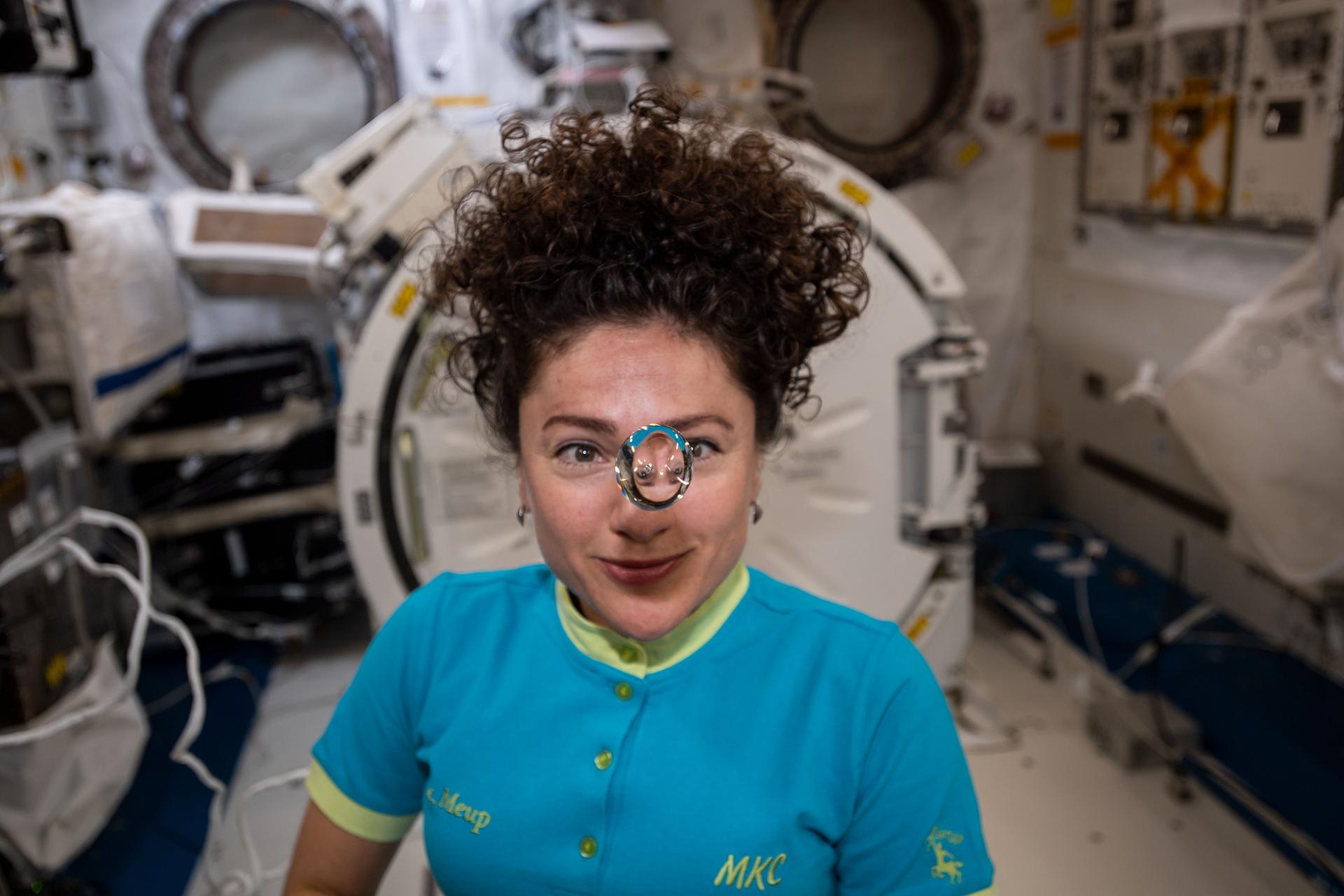
Environments: MSFC has developed many different technologies that improve the environment on the International Space Station (ISS), one of which is the Environmental Control Life Support System (ECLSS). This system preserves the natural resources found on Earth that astronauts need to survive in outer space. One of the three key components is the air revitalization system, which is dedicated to cleaning the circulating cabin air. This involves removing trace contaminants produced by electronics, plastics, and human off-gassing, including carbon dioxide exhaled by the crew during normal respiration.
While on board the ISS, NASA scientists were looking to take pictures. To meet this need, MSFC developed a ruggedized infrared camera system for harsh environments. The camera is built to survive high-vibration environments (e.g., launch) and improve heat removal for operation in a range of harsh conditions including vacuum. The camera can be used both in low Earth orbit mounted to SmallSats, CubeSats, or other spacecrafts. Or the device could be used here on Earth for first responders, unmanned vehicles, or recreational use.
Manufacturing: MSFC has one of the largest additive manufacturing facilities in the world with the capability to 3D print rocket engines. AM has become a revolutionary way to manufacture and build technologies. One of the best qualities is its capability to build intricate channels. MSFC has invented a technology that clears out any left-over residue within these chambers called the High Flow Differential Cleaning. The invention uses a large volume of pressurized air to quickly enter and clean a chamber.
MSFC also builds large metal components by using friction stir welding. This technique is significantly more robust and cost-effective than alternatives. The IFR Tool mitigates the internal friction that occurs between the weld pin and crown-shoulder during a self-reacting friction stir weld. This technology can be used in multiple industries such as aerospace, railway cars, construction, ship building, and even in plastic welding.
Huntsville, Alabama, coined the “Rocket City”, is home to numerous commercial space partners and missile defense companies. As Marshall Space Flight Center paves the way in space propulsion systems, NASA remains committed to making these novel technologies accessible to the commercial sector.