Carbonated Cement for Production of Concrete with Improved Properties
Materials and Coatings
Carbonated Cement for Production of Concrete with Improved Properties (MFS-TOPS-68)
Supporting CO2 Emissions Reduction in Cement Manufacturing
Overview
NASA's Marshall Space Flight Center has developed a new cement composition and manufacturing method that enables carbon dioxide (CO2) emissions reduction in cement manufacturing while also providing a cement with improved performance capabilities. Building off of their expertise in life-support oxygen-control systems for spacecraft, the researchers have demonstrated a process whereby carbon is reduced to solid form from captured CO2 emissions, and becomes an inherent component of the cement product. The inventors, along with their collaborators at California State University-Chico, have demonstrated the technical viability of the innovation with laboratory testing that has indicated that, in addition to reduced CO2 emissions, cement compositions with enhanced properties can be attained. The inventors are pursuing opportunities to evaluate this innovation in actual cement-making applications.
The Technology
The NASA cement innovation describes a method to make solid carbon material from CO2 captured during the cement-making process, and for using that carbon material in the mixture to improve cement properties. Doing so provides a direct use for the captured CO2, eliminating any CO2 storage/disposal issues and providing an improved cement product.
The innovation employs a chemical reaction, known as the Bosch process, which uses hydrogen gas and catalysis to reduce the CO2 to solid carbon and water. Cement manufacturing is uniquely suited to the use of the Bosch process. Cement manufacturing requires high temperatures, and harnessing this excess heat limits the total energy required to maintain a Bosch process at a cement plant. Also, cement contains iron, a metal shown to be an exceptional catalyst for the Bosch process. Thus, the cement product itself can be used as the catalyst for the reaction, also serving as a carbon sink. This eliminates any requirements for the storage or disposal of the waste carbon captured from CO2 emissions.
Test evaluations at the bench scale have provided encouraging indications of enhanced mechanical properties for the carbon-containing cement materials. In particular, the findings suggest that the carbon in the concrete might delay the environmental breakdown of concrete due to the blocking effect of the carbon on harmful ions (e.g., chlorine).
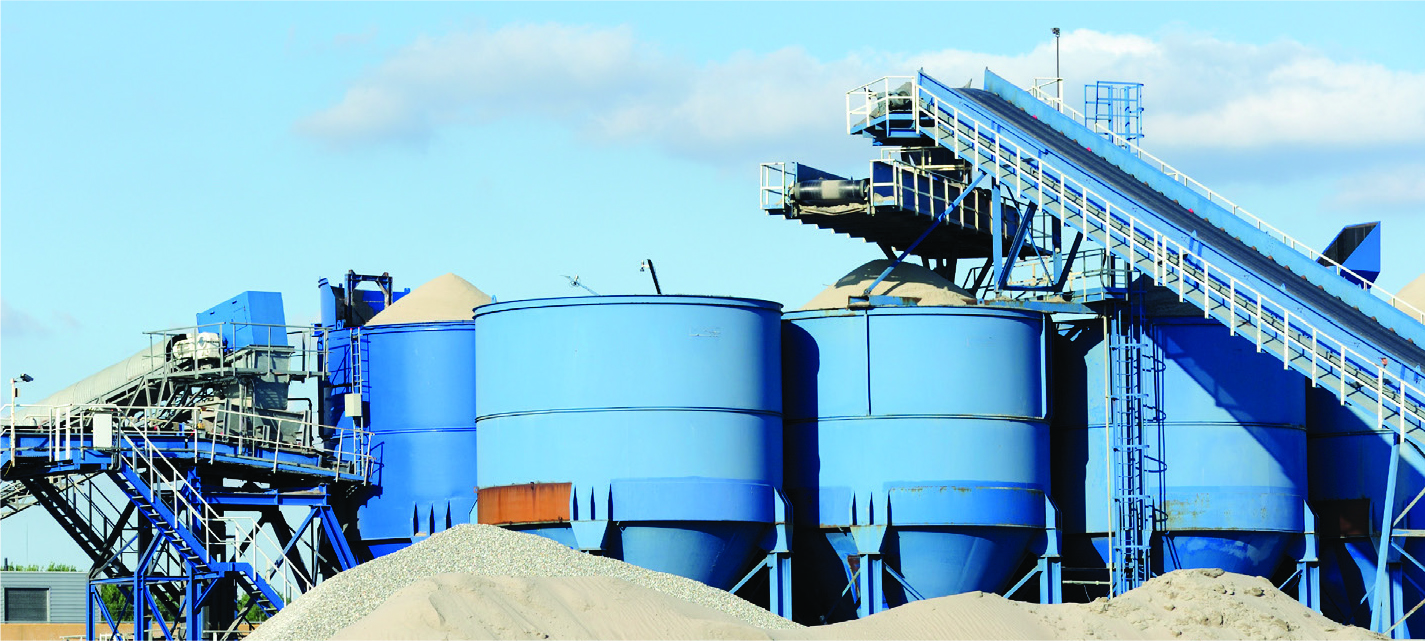
Benefits
- Provides an integrated systems approach to reducing CO2 emissions from cement manufacturing with capture as well as storage/use in the cement product itself
- Demonstrates the potential to enhance cement properties via a carbon-containing additive, particularly in durability against salt effects
- Uses waste heat from cement manufacturing to drive the carbon capture reaction
- Uses iron present in the cement as the key catalyst for the Bosch process
Applications
- Energy and manufacturing – Cement manufacturing process with integrated carbon capture and storage
- Materials – Novel cement material composition with improved properties
Tags:
|
|
Related Links:
|
Similar Results
Cryogenic Oxygen Storage Modules COSM
The COSM employs NASA's Cryogenic Flux Capacitor core to store liquid oxygen (at 90 K) in silica aerogel material at ambient pressure, and then discharges cold oxygen gas into an in-line flow loop in response to heat input. If the composition of the incoming effluent stream contains gases with condensation or freezing points above the 90 K oxygen storage temperature--such as carbon dioxide or water vapor--these gasses can be removed from the stream as it moves through the COSM. The current COSM is sized to be wearable on the person but can be easily scaled to much larger sizes and various geometries.
COSM is designed with a long "cold path" which provides for greater residence times which increase the probability that condensable/freezable gases will be trapped in the COSM. Also, the longer the cold path, the longer the time a COSM can be used prior to the oxygen being depleted and the scrubbed gasses liberated. Two COSM geometries have been designed, built, and tested-a round spiral and a prismatic serpentine--to achieve long cold paths, and intrinsic vapor cooling to manage heat loads.

Low-Temperature Oxidation/
Reduction Catalysts
The low-temperature oxidation catalyst technology employs a novel catalyst formulation, termed platinized tin oxide (Pt/SnOx). The catalysts can be used on silica gel and cordierite catalyst supports, and the latest developments provide sprayable formulations for use on a range of support types and shapes. Originally developed for removal of CO, the catalyst has also proven effective for removal of formaldehyde and other lightweight hydrocarbons.
NASA researchers have also extended the capability to include reduction of NOx as well as developed advanced chemistries that stabilized the catalyst for automotive catalytic converters via the engineered addition of other functional components. These catalyst formulations operate at elevated temperatures and have performed above the EPA exhaust standards for well beyond 25,000 miles. In addition, the catalyst can be used in diesel engines because of its ability to operate over an increased temperature range.
For use as a gas sensor, the technology takes advantage of the exothermic nature of the catalytic reaction to detect formaldehyde, CO, or hydrocarbons, with the heat being produced proportional to the amount of analyte present.

Liquid Sorbent Carbon Dioxide Removal System
NASA's Liquid Sorbent Carbon Dioxide Removal System was designed as an alternative to the current CO2 removal technology used on the International Space Station (ISS), which uses solid zeolite media that is prone to dusting, has a low absorption capacity, and requires high regeneration temperatures and frequent maintenance. Motivated by CO2 removal systems on submarines, NASA innovators began investigating the use of liquid sorbents. Liquid sorbents have a capacity four times greater than solid zeolites, require low regeneration temperature, and need fewer unreliable moving mechanical parts than solid based systems. While submarine CO2 scrubbers spray an adsorbing chemical directly into the air stream and allow the liquid to settle, NASA's new system uses a capillary driven 3D printed microchannel direct air/liquid contactor in a closed loop system. The Liquid Sorbent Carbon Dioxide Removal System is robust and reliable, while being low in weight, volume, and power requirements. The system is capable of reaching equilibrium when the liquid sorbent surface is being regenerated at a rate equal to the rate of absorption into the liquid.

In-Situ Resource Utilization (ISRU): Methylotrophic Microorganisms Expressing Soluble Methane Monooxygenase Proteins
Microorganisms are unique from the standpoint that they can be employed as self-replicating bio-factories to produce both native and engineered mission relevant bio-products. Methane (CH4) usage in In-Space Manufacturing (ISM) platforms has been discussed previously for human exploration and has been proposed to be used in physicochemical systems as a propulsion fuel, supply gas, and in fuel cells. Carbon Dioxide (CO2) is abundant on Mars and manned spacecraft. On the International Space Station (ISS), NASA reacts excess CO2 with Hydrogen (H2) to generate CH4 and Water (H2O) using the Sabatier System (Figure 1). The resulting water is recovered in the ISS, but the methane is vented to space. Recapturing this methane and using it for microbial manufacturing could provide a unique approach in development of in-space bio-manufacturing. Thus, there is a capability need for systems that convert methane into valuable materials. Methane (CH4) is a potential carbon substrate for methanotrophic microorganisms which are able to metabolize CH4 into biomass. The innovative technology from NASA Ames Research Center ports Soluble Methane Monooxygenase (sMMO) to Pichia, that is, it moves the methane metabolism into a robust microbial factory (Pichia pastoris) (Figure 2). The yeast Pichia pastoris is a refined microbial factory that is used widely by industry because it efficiently secretes products. Pichia could produce a variety of useful products in space. Pichia does not consume methane but robustly consumes methanol, which is one enzymatic step removed from methane. This novel innovation engineers Pichia to consume methane thereby creating a powerful methane-consuming microbial factory and utilizing methane in a robust and flexible synthetic biology platform.

Air Revitalization for Vacuum Environments
The NASA life support system uses a regenerable vacuum swing adsorption process, known as Sorbent-Based Air Revitalization (SBAR), to separate water and carbon dioxide for disposal. The SBAR system is an adsorbent-based swing bed system that has been optimized to provide both humidity and carbon dioxide control for a spacecraft cabin atmosphere.
The system comprises composite silica gel and zeolite-packed beds for adsorption and a bypass system for flow control. Under normal operating conditions, the disposal system would require a high-quality vacuum environment to operate. Improvements to the SBAR system include an enhanced inherent capacitance that extends the operation time within a non-vacuum environment for up to 4.5 hours. Flight time can be further expanded with multiple SBAR systems to allow for system regeneration. By scheduling periodic thermal regenerations—nominally during sleep periods—the SBAR technology may be suitable for missions of unlimited duration.