Flexible Lightweight Radiation Shielding
Materials and Coatings
Flexible Lightweight Radiation Shielding (LAR-TOPS-354)
Method of making thin flexible Z-shielding integrated with common textiles
Overview
Lead-filled aprons are currently used for atomic number (Z)-grade radiation shielding in the medical industry to protect personnel from hazardous gamma radiation. These apron garments are made with lead-filled elastomeric sheets encased in polymeric fabrics and are both heavy and bulky to meet necessary shielding requirements. In addition, there are environmental safety concerns surrounding disposal of these garments due to their lead content. An innovator at NASA Langley Research Center has developed a novel method for making thin, lightweight radiation shielding that can be sprayed or melted onto common textiles used in clothing such as cotton, nylon, polyester, Nomex and Kevlar. The lead-free shielding is more effective at blocking radiation as compared with similar thicknesses of lead while being up to 25% lighter. The shielding can also be formed into a variety of garments such as shirts, vests, jackets, and pants with significantly greater comfort and conformity than the aprons currently in use.
The Technology
The thin, lightweight radiation shielding is comprised of a low Z/high Z/low Z layered structure wherein the low Z layer is composed of titanium and the high Z layer is composed of either tantalum or antimony. Modelling of radiation shielding performance from a Cobalt 57 source shows a 10 times reduction in gamma radiation when using tantalum and a 25 times reduction when using antimony as compared with a single layer of lead. In addition, the Z-shielding is 25% lighter than a single lead layer with the same thickness (0.35-0.36 mm). The direct textile spraying innovation outlined by this invention enables the ability to shape this shielding into garments via the sewing of metal coated fibers. The refractory metal shielding can be added onto a variety of commodity-based fabrics including glass fabrics.

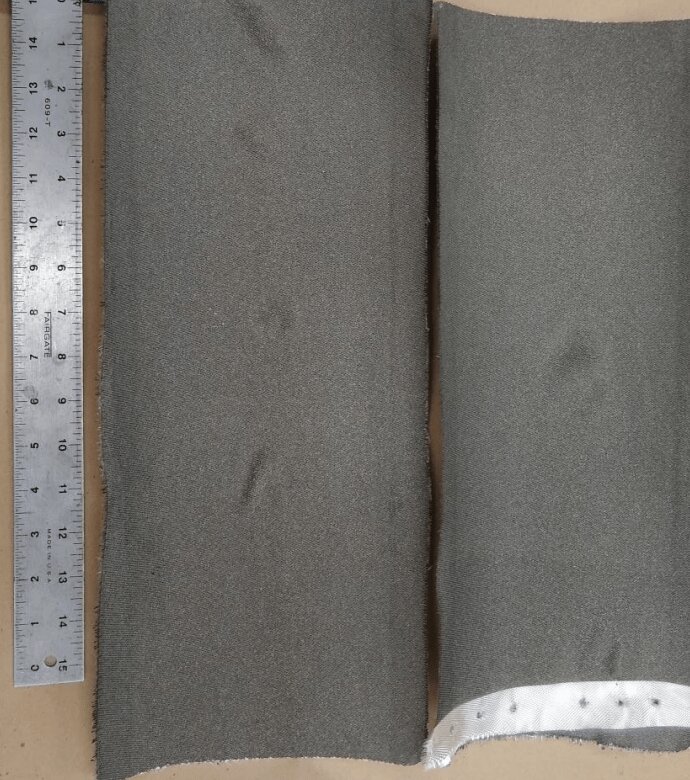
Benefits
- Lead-free
- 10 to 25 times greater radiation shielding performance compared to similar thicknesses of lead
- 25% lighter than equivalent thicknesses of lead
- Shielding can be applied to commercial fabrics to create a flexible material that can be shaped and woven into a wide variety of conformable garments and coverings
Applications
- Medical: personal protective equipment for personnel in hospital radiation environments
- Medical: radiation shielding for hospital facilities and equipment
- Electronics: radiation protection for electronic instrumentation
- Aerospace: shielding for spacecraft, satellites, and personnel
Tags:
|
Similar Results

Atomic Number (Z)-Grade Radiation Shields from Fiber Metal Laminates
This technology is a flexible, lighter weight radiation shield made from hybrid carbon/metal fabric and based on the Z-grading method of layering metal materials of differing atomic numbers to provide radiation protection for protons, electrons, and x-rays. To create this material, a high density metal is plasma spray-coated to carbon fiber. Another metal with less density is then plasma spray-coated, followed by another, and so on, until the material with the appropriate shielding properties is formed. Resins can be added to the material to provide structural adhesion, reducing the need for mechanical bonding. This material is amenable to molding and could be used to build custom radiation shielding to protect cabling and electronics in situations where traditional metal shielding is difficult to place.

High Atomic Number Coatings for Fabrics
High atomic number materials, such as tantalum, do not bond well to oxygen- and hydroxyl-rich surfaces, such as glass fibers. These metals often form surface oxides when layered on glass fabric, resulting in flaking of the high atomic number material off the fabric during cutting, folding, and/or handling.
To improve coating durability, this invention applies a lower atomic number metal as a tie down layer first before applying the high atomic number metal layer. The tie down layer reduces oxide formation between the substrate and the high atomic number material, promoting adhesion. Titanium has shown strong adhesion with different metals and is effective at reducing oxide formation when diffusion bonded to itself or other materials. It has been shown to be effective at improving durability when thermally sprayed onto a glass fiber fabric as a tie down layer for a subsequent tantalum layer (also applied via RF plasma spray). The titanium layer is only approximately 1 mil thick but results in strong adhesion of the tantalum layer by inter-metallic or diffusion bonding. A thermal spray process may be used, as well.
This innovation enables the delivery of high atomic metal coating on glass fiber fabrics and other polymeric substrates that are lower cost, lighter weight, and durable to form a flexible cloth material with Z-graded radiation shielding. Coated samples have been produced and the technology is currently at a technology readiness level (TRL) of 4 (prototype).

Highly Thermal Conductive Polymeric Composites
There has been much interest in developing polymeric nanocomposites with ultrahigh thermal conductivities, such as with exfoliated graphite or with carbon nanotubes. These materials exhibit thermal conductivity of 3,000 W/mK measured experimentally and up to 6,600 W/mK predicted from theoretical calculations. However, when added to polymers, the expected thermal conductivity enhancement is not realized due to poor interfacial thermal transfer.
This technology is a method of forming carbon-based fillers to be incorporated into highly thermal conductive nanocomposite materials. Formation methods include treatment of an expanded graphite with an alcohol/water mixture followed by further exfoliation of the graphite to form extremely thin carbon nanosheets that are on the order of between about 2 and about 10 nanometers in thickness. The carbon nanosheets can be functionalized and incorporated as fillers in polymer nanocomposites with extremely high thermal conductivities.

Multilayered Fire Protection System
The Multilayered Fire Protection system uses technology from the space craft flexible heat shield for future planetary missions. By optimizing this material for the fire environment, utilizing heat shield test methods, and experimenting with different materials, the NASA team developed a multilayered fire protection system. This system includes an outer textile layer which reflects over 90 percent of the radiant heat, an insulated layer which protects against convective heat and hot gases, and a non-porous film layer which is a gas barrier layer.

Novel Radiation Shielding Material for Dramatically Extending the Orbit Life of Cubesats
A high density metal, such as tantalum or tungsten is coated onto thin aluminum sheet in precise ratios and thicknesses. The combined sheet is then easily formed into standardized enclosures compatible with CubeSat design and performance specifications.