Solid-State Lithium-Sulfur Battery Tech Portfolio
Power Generation and Storage
Solid-State Lithium-Sulfur Battery Tech Portfolio (LEW-TOPS-167)
New battery paradigm for energy density, power, reliability and safety
Overview
SABERS, as this portfolio of innovations is named, refers to Solid-state Architecture Batteries for Enhanced Rechargeability and Safety. Developed jointly at NASA’s Glenn, Langley and Ames Research Centers, SABERS includes several advanced material, manufacturing and computational design innovations that enable a new paradigm in battery performance. The primary target application is next-generation electric aviation propulsion systems, yet SABERS will benefit other applications, too. Whether for large electric vehicle systems or small electronic devices, SABERS can potentially set new benchmarks in energy density and power, all while offering the utmost in safety and reliability. And importantly, the inventors intentionally designed environmentally friendly and sustainable materials and manufacturing methods into SABERS' portfolio. SABERS can help address today and tomorrow’s needs for electrification and sustainability.
NASA is seeking industry partners for commercialization. SABERS is available for license as a complete portfolio or as individual component technologies.
The Technology
The SABERS innovators developed novel lithium-sulfur designs, including sulfur-selenium on graphene cathodes, and lightweight bipolar plate stacking and packaging designs. SABERS is unique in several aspects: it deploys graphene-based manufacturing processes for the cathode and bipolar plates, and it uses a solid-state electrolyte in place of the liquid electrolyte found in other lithium-sulfur battery designs. The team has achieved energy densities over 500 W-hr/kg, and further improvements are expected. SABERS can meet the high-power requirements needed for aircraft take-off. SABERS is lightweight, safe, robust, and reliable. Furthermore, its manufacturing processes are scalable and environmentally friendly. Coin cell and pouch prototypes have been demonstrated to date. Development efforts continue and new portfolio innovations are expected. Major component technologies in SABERS include the following (as listed here and shown in the figure below).
S/Se Cathode – Sulfur/Selenium on graphene scaffold
(LAR-19556-1, LEW-20228-1)
Solid Electrolyte – Solid-state electrolyte composites
(LEW-20445-1)
Bipolar Stack – Graphene plates
(LAR-20257-1)
Li-Metal Anode
(Proprietary, under development)
Packaging
(Proprietary, under development)
Robust computational models have been developed to support the battery materials design and are available to licensees to evaluate and optimize different materials combinations and performance targets.
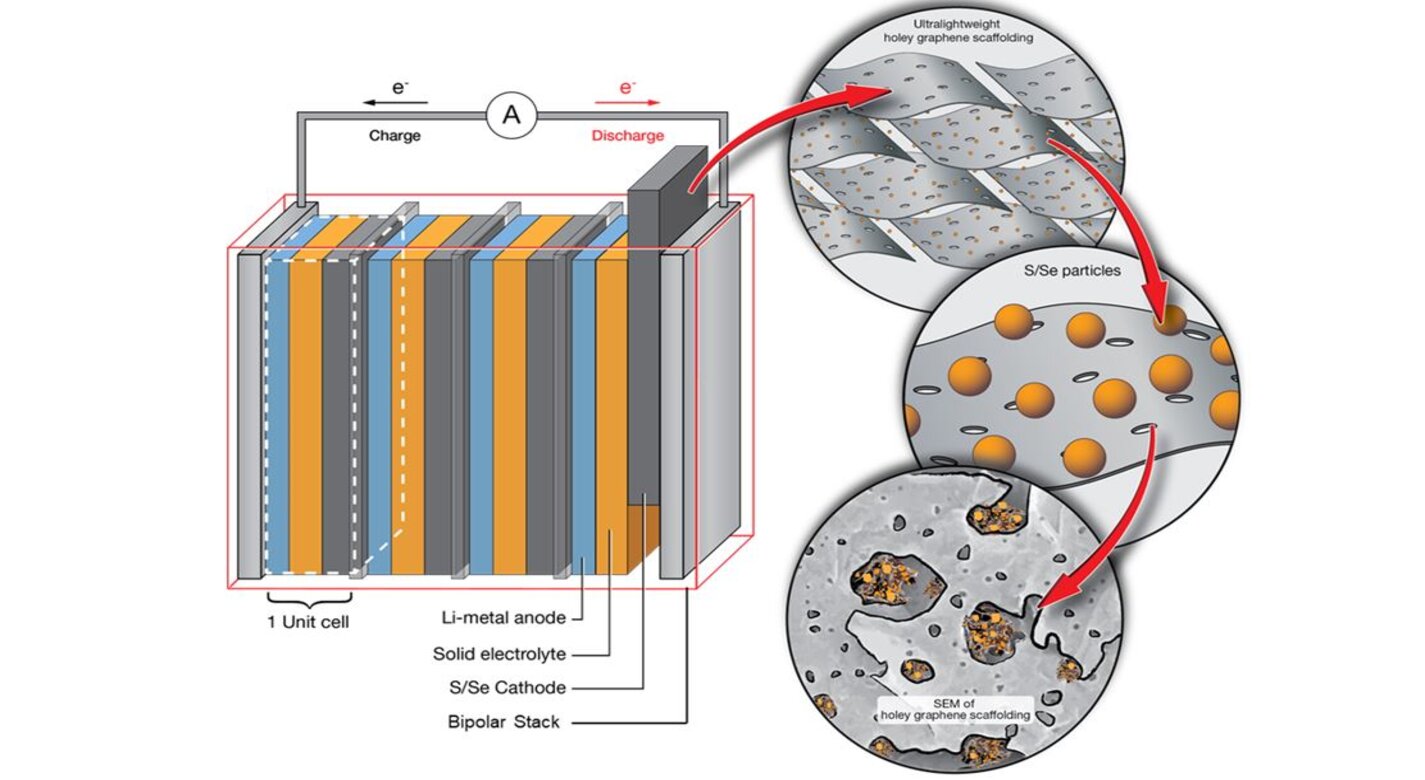
Benefits
- Novel Battery Chemistry and Design: Lithium-Sulfur/Selenium with a solid-state electrolyte, enabled by graphene cathode and bipolar plate technology.
- High Performance: Energy density more than double current generation Li-Ion batteries. High discharge rates to power aircraft takeoff. Lightweight and robust.
- Safety: Solid-state design provides high damage tolerance and eliminates fire risks.
- Sustainability: The battery itself can enable electrification to help meet carbon emission climate goals and is amenable to recycling. Battery materials and manufacturing processes are environmentally friendly.
- Scalability: Based on readily scaled manufacturing processes.
- Patented: Several issued patents and pending patents. Additional patents anticipated.
- Suite of Technologies: This is not just one innovation, but an entire suite of innovations optimized in combination to meet performance goals. Based on the collective efforts of innovators at multiple NASA research centers.
- Prototype Demonstration: Coin-cell and pouch type batteries have been successfully demonstrated, and research is still on-going to optimize the design and performance.
Applications
- Aviation: Battery-powered propulsion systems for next generation electric aircraft
- Automotive: Lightweight batteries that can offer improved safety, sustainability and driving range of electric cars and trucks.
- Other: Military/Defense, Electronics, etc.
Technology Details
Power Generation and Storage
LEW-TOPS-167
LEW-20228-1
LEW-20445-1
US Patents 9,120,677, 9,567,225, 10,836,137, and
11,413,850
Patents Pending
Dry Pressing Neat Active Materials into Ultrahigh Mass
Loading Sandwich Cathodes Enabled by Holey Graphene Scaffold, https://pubs.acs.org/doi/full/10.1021/acsaem.0c00582
Holey Graphene–Enabled Solvent-Free Preparation of
Ultrahigh Mass Loading Selenium Cathodes for High Areal Capacity Lithium–Selenium Batteries, https://www.frontiersin.org/articles/10.3389/fenrg.2021.
703676/full
Practical considerations in designing solid state Li-S cells for electric aviation, https://www.sciencedirect.com/science/article/abs/pii
/S0013468621016960
Li-Ion Permeability of Holey Graphene in Solid State Batteries: A Particle Dynamics Study, https://pubs.acs.org/doi/full/10.1021/acsami.2c03012
Relevant NTR numbers and information sheets for the SABERS suite of technology include:
LAR-19556-1
LEW-20228-1
LAR-18334-1
LEW-20445-1
LAR-20257-1
LAR-188671-1
LAR-188671-2
LAR-TOPS-302 (Graphene-based Manufacturing)
LAR-TOPS-165 (Other Graphene-based Manufacturing)
11,413,850
Patents Pending
Dry Pressing Neat Active Materials into Ultrahigh Mass
Loading Sandwich Cathodes Enabled by Holey Graphene Scaffold, https://pubs.acs.org/doi/full/10.1021/acsaem.0c00582
Holey Graphene–Enabled Solvent-Free Preparation of
Ultrahigh Mass Loading Selenium Cathodes for High Areal Capacity Lithium–Selenium Batteries, https://www.frontiersin.org/articles/10.3389/fenrg.2021.
703676/full
Practical considerations in designing solid state Li-S cells for electric aviation, https://www.sciencedirect.com/science/article/abs/pii
/S0013468621016960
Li-Ion Permeability of Holey Graphene in Solid State Batteries: A Particle Dynamics Study, https://pubs.acs.org/doi/full/10.1021/acsami.2c03012
Relevant NTR numbers and information sheets for the SABERS suite of technology include:
LAR-19556-1
LEW-20228-1
LAR-18334-1
LEW-20445-1
LAR-20257-1
LAR-188671-1
LAR-188671-2
LAR-TOPS-302 (Graphene-based Manufacturing)
LAR-TOPS-165 (Other Graphene-based Manufacturing)
Similar Results

High-Voltage Power System for Hybrid Electric Aircraft Propulsion
Glenn's novel system supports the NASA Aeronautics Research Mission Directorate (ARMD) strategic plan to leverage advancements in technologies over the next 25 years and beyond, leading to new aircraft configurations with enhanced performance, improved energy efficiency, and reduced CO2 emissions. The electric system is a multi-megawatt micro-grid that converts mechanical energy to electric via generators, and electric energy to mechanical via motor-driven fans. This innovation would use the variation in aircraft throttle settings to produce a high-voltage (20 kilovolts), variable-frequency 9-phase AC distribution system. Using doubly fed electric machines (generator, propulsor, and flywheel) allows for field excitation that can cause variable-frequency or variable speed operation around the commanded throttle setting. The flywheel enables an energy storage system that recovers and reuses energy, while the flywheel slews with the throttle control using the electromagnetic torque produced by the doubly fed electric machine. This design permits both sub-synchronous and super-synchronous operation using limited field excitation power provided through power converters. Finally, the reduced switchgear mass facilitated through the use of a high-frequency AC system, setting-less protection zones, and simplified switches for fault clearance provides enhanced operational capability. This system can be controlled so that fault energy is minimized, preventing collateral damage to aircraft structures even with high voltage distribution. Glenn's innovative system adds performance, efficiency, reliability, and cost savings to cutting-edge hybrid electric technology.
This is an early-stage technology requiring additional development, and Glenn welcomes co-development opportunities.

Novel, Solid-State Hybrid Ultracapacitor Battery
The subject technology is an extension of closely related, solid-state ultracapacitor innovations by the same team of inventors. The primary distinction for this specific technology is the addition of co-dopants to affect the dielectric behavior of the barium titanatebased perovskite materials. These co-dopants include lanthanum and other rare earths as well as hydroxyl ions. The materials are processed at the nano scale, and are subjected to carefully designed thermal treatments as well.
The presence of the hydroxyl ions has been shown to provide several orders of magnitude increase in the capacitance of the dielectric material. Additionally, these high capacitance values are obtained at relatively low voltages found in current consumer and industrial electronics.
The capacitors tested to date are simple, single-layer devices. Ultimately, a range of manufacturing methods are possible for making commercial devices. Features of the technology enable manufacturing via traditional thick-film processing methods widely used in the capacitor industry, or via advanced printing methods for state-of-the-art printed electronics.
Future efforts will be made to advance the manufacturing and packaging processes to increase device energy density, including multilayer devices and packages

Wind-Optimal Cruise Airspeed Mode for Flight Management Systems (FMS)
The novel approach for optimizing airspeed for both actual and predicted wind conditions in electric Vertical Takeoff and Landing (eVTOL) aircraft with Distributed Electric Propulsion (DEP) systems includes the process of creating a lookup table for wind‐optimal airspeed as a function of wind magnitude, considering the direction of the wind relative to the cruise segment, considering the cruise altitude for an aircraft type, and incorporating the wind-optimal airspeed lookup table in the performance database for real‐time access by the Flight Management Systems (FMS) to predict wind-optimal airspeed at waypoints of the flight plan. The target wind‐optimal airspeed is updated in real-time throughout the cruise portion of a flight.
In a test of the wind-optimal airspeed targeting technique using a multi-rotor aircraft model, results obtained show benefits of flying at the wind‐optimal cruise airspeed compared to the best‐range airspeed. In headwind conditions, energy consumption was reduced by up to 7.5%, and flight duration was reduced by up to 28%. Under uncertain wind magnitudes, flying at wind-optimal airspeed offered lower variability and higher predictability in energy consumption than flying at best‐range airspeed.

High Efficiency Megawatt Motor
The HEMM is a is a wound-field partially superconducting machine that implements a combination of rotor superconducting and stator normal conductor elements, along with an integrated acoustic cryocooler, to achieve some of the benefits of a superconducting motor without the need for an external cryogenic system. The combination of the described elements allows a motor to be built which essentially operates like any other motor when viewed as a black box, but substantially enhanced performance can be achieved. The incorporation of superconductors on the rotor to create a high-level magnetic field results in a specific power and efficiency that could not be achieved any other way. The HEMM can achieve over 98% efficiency in a lightweight electric machine with an operating power greater than 1.4 MW, a specific power greater than 16 kW/kg (ratio to electromagnetic mass), and a rated operating speed of 6800 RPM. The HEMM can be used as both a motor or a generator, offering a wide range of applications including propulsion systems for hybrid aircraft, electric trains, hybrid cars, and turboelectric ships, as well as generator systems for wind turbines, power plants, or motors for other industrial machinery.

Coil-On-Plug Igniter for Reliable Engine Starts
Spark-ignition devices have proven to be a high-reliability option for LOX/LCH4 ignition during development of the Integrated Cryogenic Propulsion Test Article (ICPTA) main and reaction control engines (RCEs); however, issues including spark plug durability (ceramic cracking) and corona discharge during simulated altitude testing have been observed, contributing to degraded spark output and no-light engine-start conditions. Innovators discovered that ignition system reliability could be improved and weight reduced by eliminating the traditional coil and spark plug wire. To achieve this result, engineers made the innovation by modifying an automotive coil-on-plug igniter to provide new high sparking energies at the point of combustion using low supply voltages. The coil was modified by vacuum-potting it into a threaded interface that mounts into existing spark plug ports on the ICPTA main engine and the RCEs. Engineers fabricated custom electrode tips that were thread-mounted into the potted coil body. Epoxy insulation was chosen with high dielectric strength to maintain insulation between the electrode and threaded adapter. Vacuum potting successfully prevented pressure or vacuum leakage into the coil body and maintained spark energy and location at the electrode tip. Successful hot-fire ignition was observed at sea-level, altitude, and thermal-vacuum for both ICPTA RCE and main engine igniters down to 10^-3 torr, which approaches the vacuum of cislunar space.
This technology is at technology readiness level (TRL) 7 (system prototype demonstration in an operational environment), and the related patent is now available to license. Please note that NASA does not manufacture products itself for commercial sale.