Search
PATENT PORTFOLIO
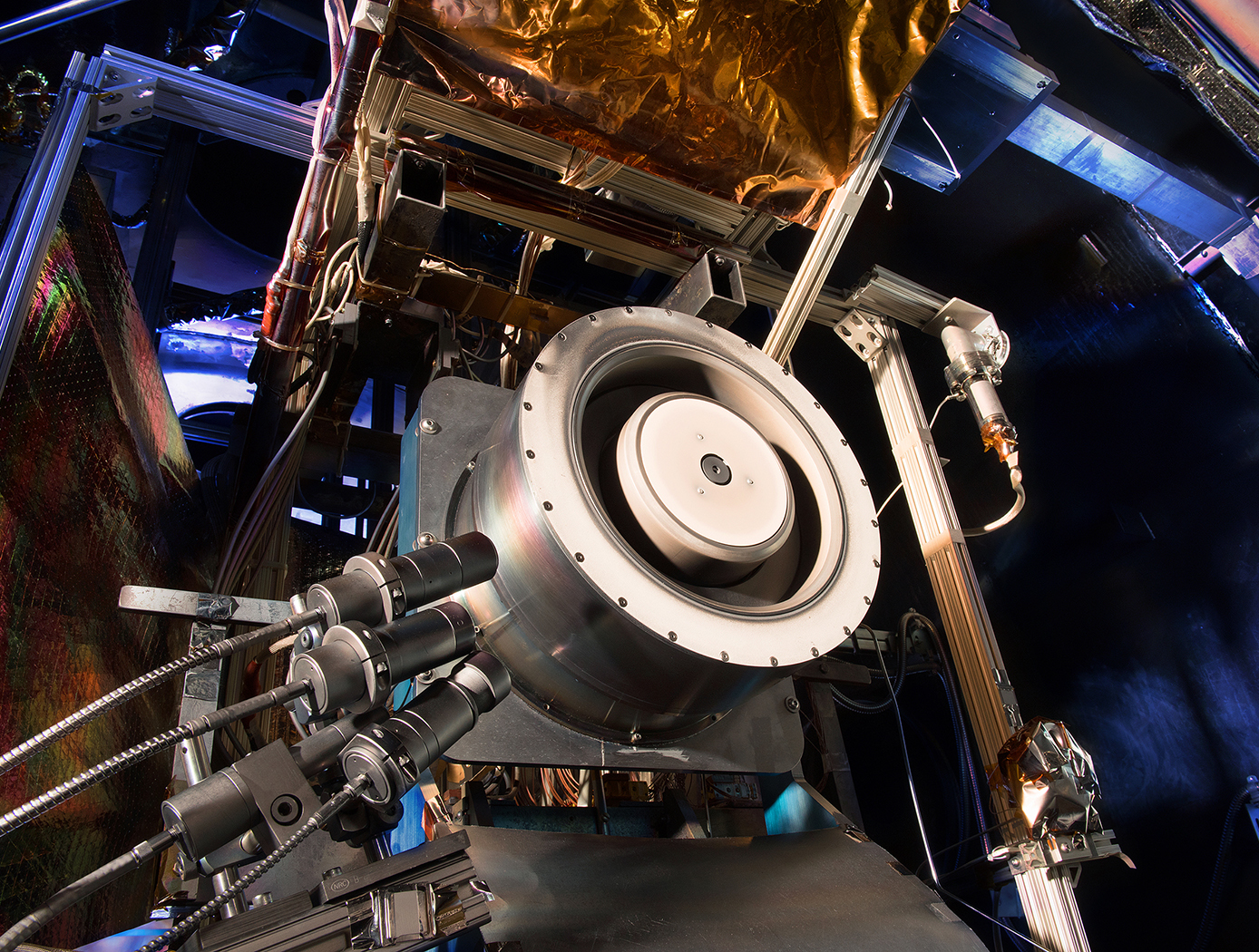
Hall Effect Thruster Technologies
Used for propelling Earth-orbiting satellites and deep-space robotic vehicles, the HET gets its name because it traps electrons with an intense radial magnetic field in an azimuthal Hall current moving around the circumference of an annular ceramic channel. The electrons in the circulating Hall current ionize the onboard propellant - the inert gas xenon - and create an ionized plasma. The xenon plasma is then accelerated axially, via an applied electric field along the coaxial channel, to an exit velocity of up to 65,000 miles per hour to produce thrust. The interaction of the accelerated plasma and the downstream edge of the channel, where the plasma is the most energetic, results in erosion of the surrounding magnetic system used to generate the plasma. One of NASA Glenn's novel designs relies on an azimuthally symmetric configuration that minimizes radial magnetic fields at the discharge chamber walls. This configuration completely shields the walls of the discharge chamber from the high-energy plasma ions. With regard to the discharge-channel-wall replacement innovation, an actuator can be configured to extend the discharge chamber along the centerline axis. The actuator can be either mechanical or programmable. In either case, the sleeve can be extended while an upstream portion of the discharge chamber remains stationary, thereby preventing plasma exposure. These novel designs increase the efficiency and extend the lifetime of the HET to five times that of unshielded thrusters, enabling a new era of space missions.
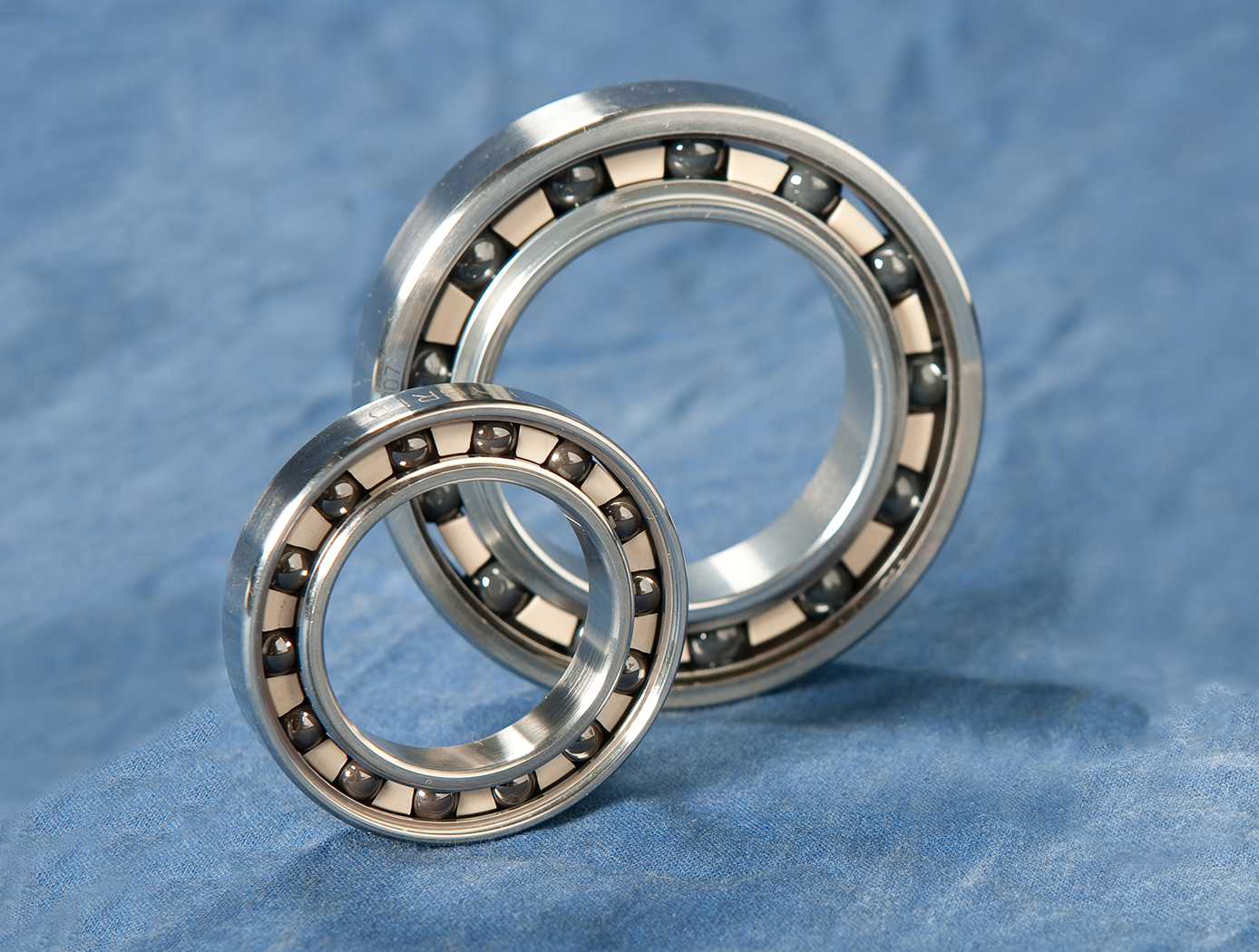
Oil-Free Lubricants
In applying PS400 using the plasma spray-coating process, a 0.010 inch layer is deposited onto a metal surface. This composite coating often includes a metallic-based binder, a metal-bonded hardener, a high-temperature lubricant, and/or a low- temperature lubricant. PS400's improved metallic-based binder alloy greatly increases the structural strength and durability of the composite with respect to the operating temperature and the bearing load, and provides superior dimensional stability. PS400's metal-bonded oxide hardening agent provides additional hardness, wear resistance, and thermal stability, while also exhibiting a low coefficient of friction when used in sliding contacts. It is also significantly less expensive in terms of both acquisition and grinding processes.
Depending on the desired environment, high- and low-temperature lubricants may be added to the composite coating. The preferred high-temperature lubricant is a metal fluoride and the optional optional low-temperature lubricant is composed of metals, such as silver or copper, that are soft enough to provide lubrication at low temperature while maintaining oxidation resistance with a sufficiently high melting point. These qualities permit the materials to be used over a broad temperature range. Once the spray coating has been applied, the metal surface is ground and polished to produce a smooth, self-lubricating surface before use. Unlike some coatings that must be diamond-ground, PS400 is readily ground with a substantially less expensive abrasive, such as silicon carbide. This grinding process generally yields a coating thickness of 200 to 400 micrometers.
In instances when a coating is not convenient or possible, powder metallurgy techniques using PM400 can be used to make freestanding self-lubricating components such as bushings and wear plates.
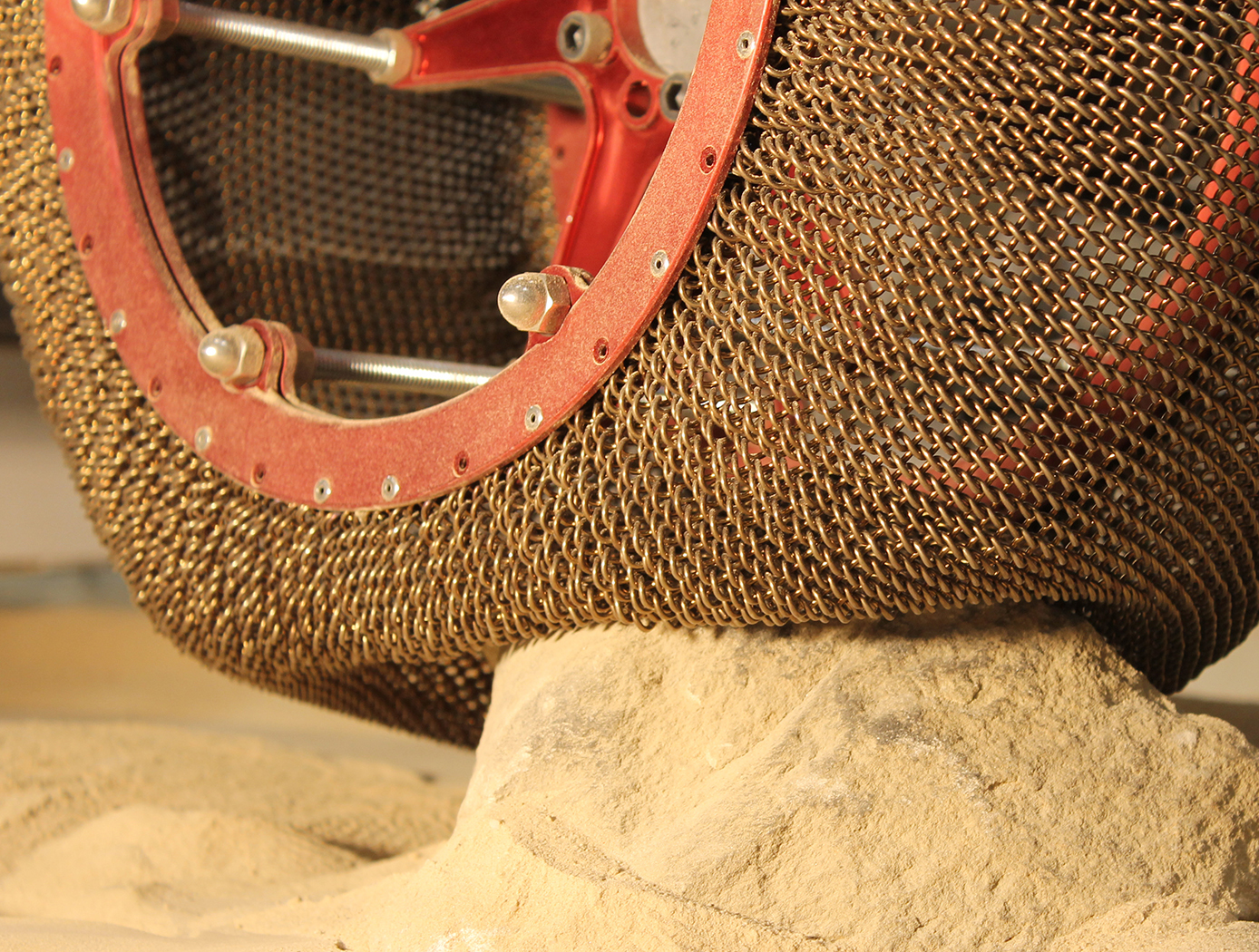
Superelastic Tire
This NASA Glenn innovation comprises a non-pneumatic, compliant tire utilizing shape memory alloys (mainly NiTi and its derivatives) as load bearing components. These shape memory alloys are capable of undergoing significant reversible strain (up to 10%), enabling the tire to withstand an order of magnitude more deformation than other non-pneumatic tires before undergoing permanent deformation. Commonly used elastic-plastic materials (e.g. spring steels, composites, etc.) can only be subjected to strains on the order of ~ 0.3-0.5% before yielding. Hence, the use of a NiTi shape memory alloy produces a superelastic tire that is virtually impervious to plastic deformation. In addition, the utilization of shape memory alloys provides enhanced control over the effective stiffness as a function of the deformation, providing increased design versatility. For instance, the Glenn Superelastic Tire can be made to soften with increased deflection, reducing the amount of energy transferred to the vehicle during high deformation events. In addition, the use of shape memory alloys in the form of radial stiffeners, as opposed to springs, provides even more load carrying potential and improved design flexibility. This type of compliant tire would allow for increased travel speeds in off-road applications.
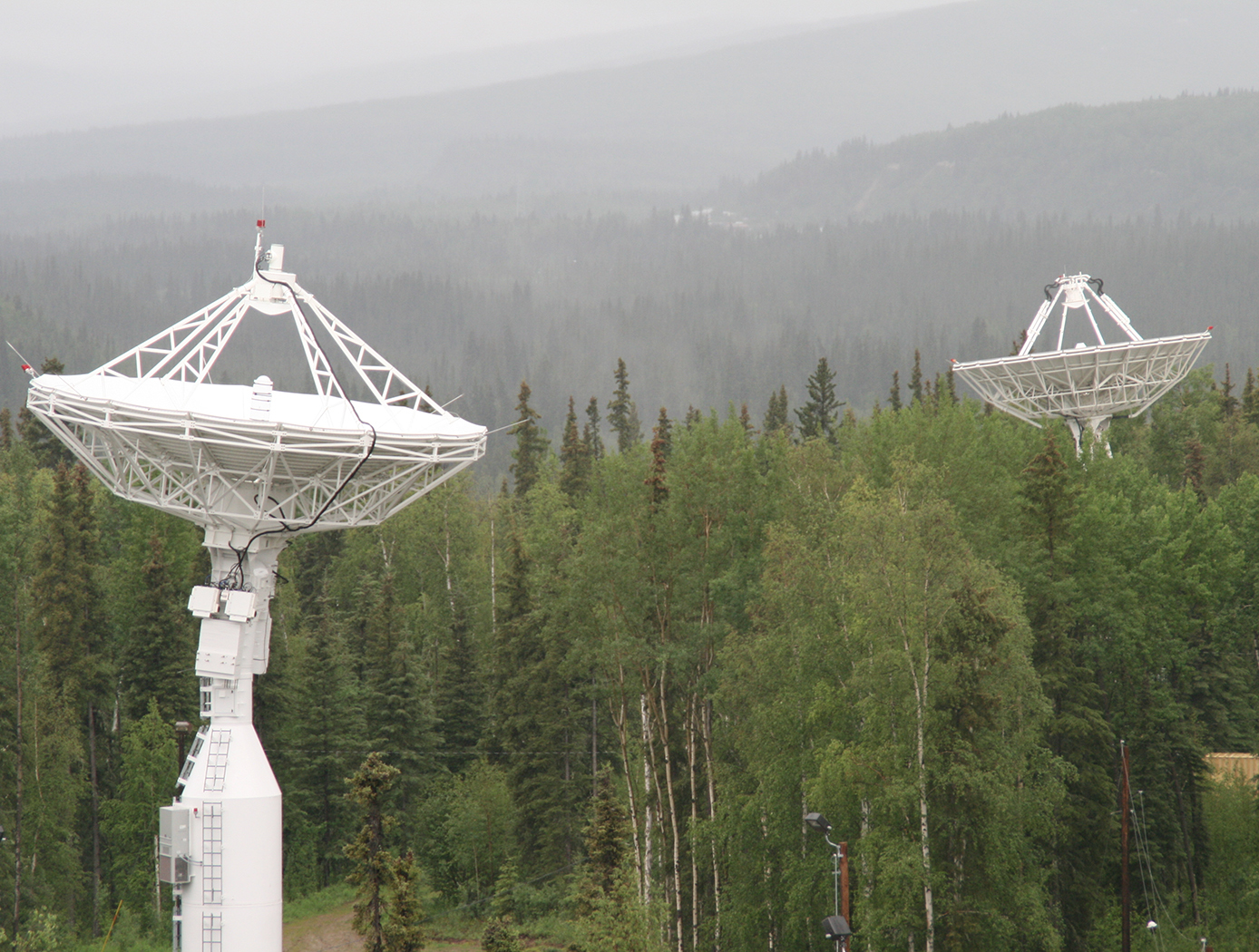
Signal Combiner for Wideband Communication
Through low-loss signal combination, Glenn is leading the way to optimize radio transmission remotely during self-checking routines. Glenn's signal combiner offers a simple method to minimize signal loss significantly when combining two signals. Using conventional combiners in bit-error-rate testing results in a loss of 3 to 4 dB per band, and with a directional coupler the secondary signal experiences losses of 10 dB or more. Moreover, during signal measurements, the additional components must be placed and later removed to prevent any impact to the measurement, making for a cumbersome process. Glenn's solution is to combine the primary and secondary signals in the frequency domain through the use of a frequency division diplexer/multiplexer in combination with a wideband ADC. The multiplexer selects one or more bands in the frequency domain, and the ADC performs a non-linear conversion to digital domain by folding out-of-band signals in with the primary signal. NASA makes use of subsampling a given band within the ADC bandwidth to fold it into another band of interest, effectively frequency-shifting them to a common frequency bandwidth.
Glenn's breakthrough method has two significant advantages over the conventional use of a power combiner or directional coupler in bit-error-rate testing: 1) it combines signal and noise (secondary signal) with very low loss, and 2) it enables the selection of the desired signal-to-noise ratio with no need for the later cumbersome removal of components. This streamlined process allows for invaluable in-situ or installed measurement. Glenn's novel technology has great potential for satellite, telecommunications, and wireless industries, especially with respect to equipment testing, measurement, calibration, and check-out.
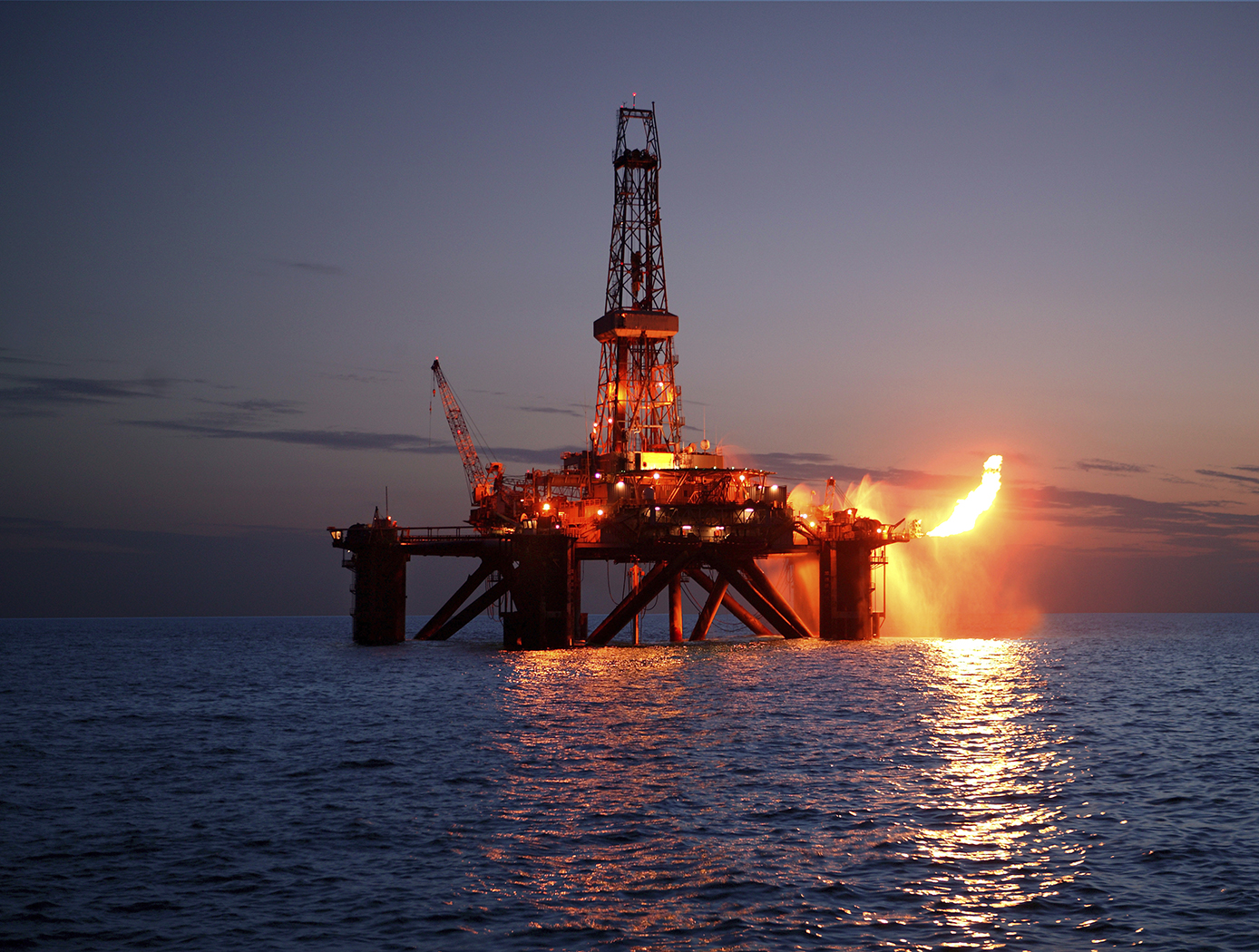
High-Temperature Single Crystal Preloader
For extremely high-temperature sealing applications, Glenn researchers have devised novel methods for fabricating single-crystal preloaders. NASA's high-temperature preloaders consist of investment cast or machined parts that are fabricated in various configurations from single crystal superalloys. Machined preloaders include a variety of spring configurations, compressed axially or radially, fabricated from single crystal slabs. Before machining, the slabs are carefully oriented in a special goniometer using x-diffraction techniques. This helps to maintain proper crystal orientation relative to the machined part and the applied loads. For more complex geometry components which cannot be easily and economically machined, an investment casting approach would be used. Complex preloader geometries include wire coil springs of various configurations. These single crystal preloaders would be designed with the appropriate stiffness for the intended thermal barrier/seal application and placed underneath, or integrated within, the seal/barrier. At extrememly high temperature, the preload device keeps the seal/barrier mated against the opposing surface as the gap between the two surfaces changes, maintaining contact between surfaces and preventing convective heat transfer.
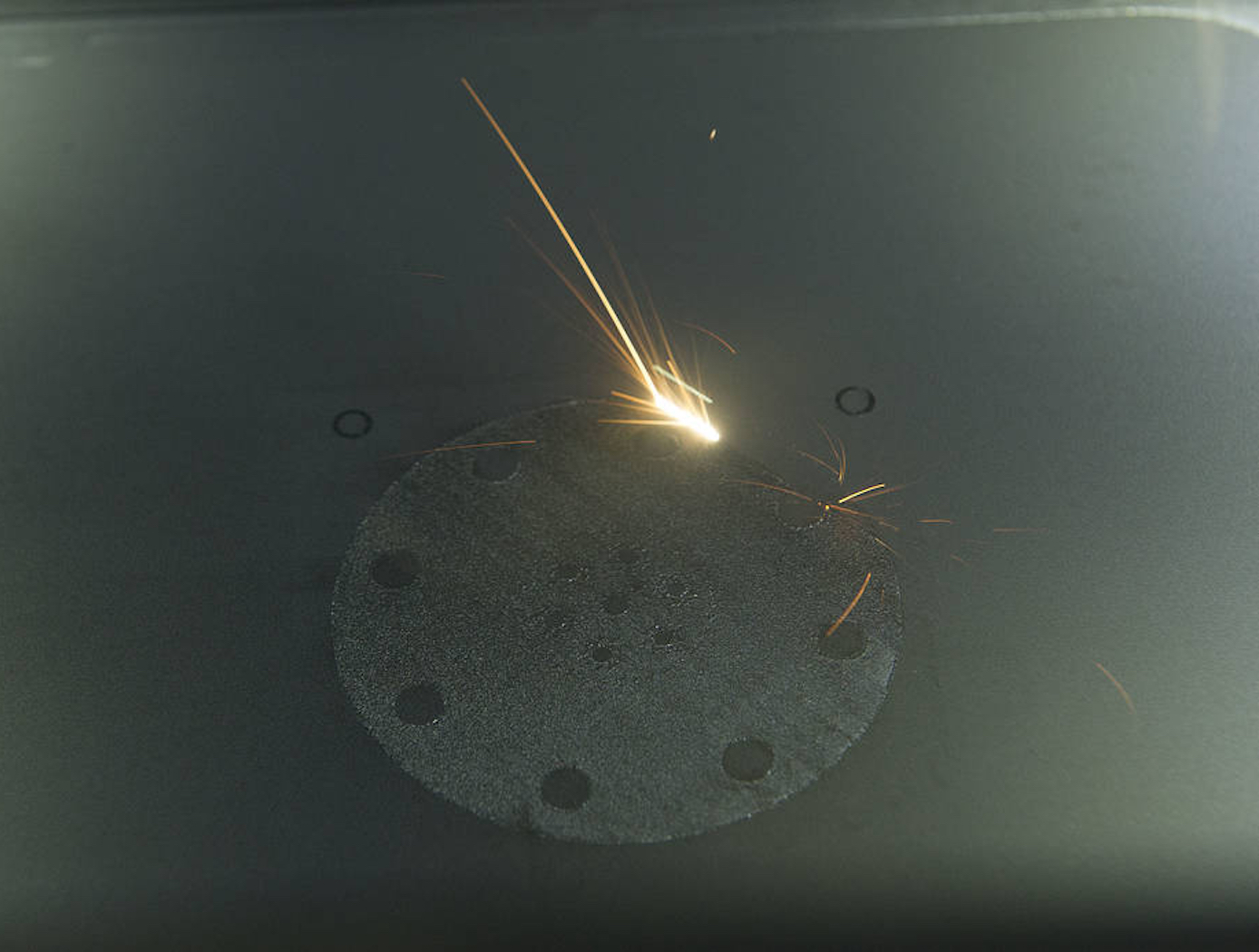
3D-Printed Composites for High Temperature Uses
NASA's technology is the first successful 3D-printing of high temperature carbon fiber filled thermoset polyimide composites. Selective Laser Sintering (SLS) of carbon-filled RTM370 is followed by post-curing to achieve higher temperature capability, resulting in a composite part with a glass transition temperature of 370 °C.
SLS typically uses thermoplastic polymeric powders and the resultant parts have a useful temperature range of 150-185 °C, while often being weaker compared to traditionally processed materials. Recently, higher temperature thermoplastics have been manufactured into 3D parts by high temperature SLS that requires a melting temperature of 380 °C, but the usable temperature range for these parts is still under 200 °C.
NASA's thermoset polyimide composites are melt-processable between 150-240 °C, allowing the use of regular SLS machines. The resultant parts are subsequently post-cured using multi-step cycles that slowly heat the material to slightly below its glass transition temperature, while avoiding dimensional change during the process. This invention will greatly benefit aerospace companies in the production of parts with complex geometry for engine components requiring over 300 °C applications, while having a wealth of other potential applications including, but not limited to, printing legacy parts for military aircraft and producing components for high performance electric cars.

Polyamide Aerogels
Polyamides are polymers that are similar to polyimides (another polymer that has been developed for use in aerogels). However, because the amide link is a single chain while the imide link is a ring structure, polyamide aerogels can be made less stiff than polyimides, even though a similar fabrication process is used. The precursor materials can be made from any combination of diamine and diacid chloride. Furthermore, NASA Glenn researchers have found methods for using combinations of diamines and disecondary amines to produce polyamide aerogels with tunable glass transition temperatures, for greater control of features such as flexibility or water-resistance.
In the first step of the fabrication process, an oligomeric solution is produced that is stable and can be prepared and stored indefinitely as stock solutions prior to cross-linking. This unique feature allows for the preparation and transport of tailor-made polyamide solutions, which can later be turned into gels via the addition of a small amount of cross-linker. When the cross-linking agent is added, the solution can be cast in a variety of forms such as thin films and monoliths. To remove the solvent, one or more solvent exchanges can be performed, and then the gel is subjected to supercritical drying to form a polyamide aerogel. NASA Glenn's polyamide aerogels can be fully integrated with the fabrication techniques and products of polyimide aerogel fabrication, so hybrid materials which have the properties of both classes are easily prepared. As the first aerogels to be composed of cross-linked polyamides, these materials combine flexibility and transparency in a way that sets them apart from all other polymeric aerogels.
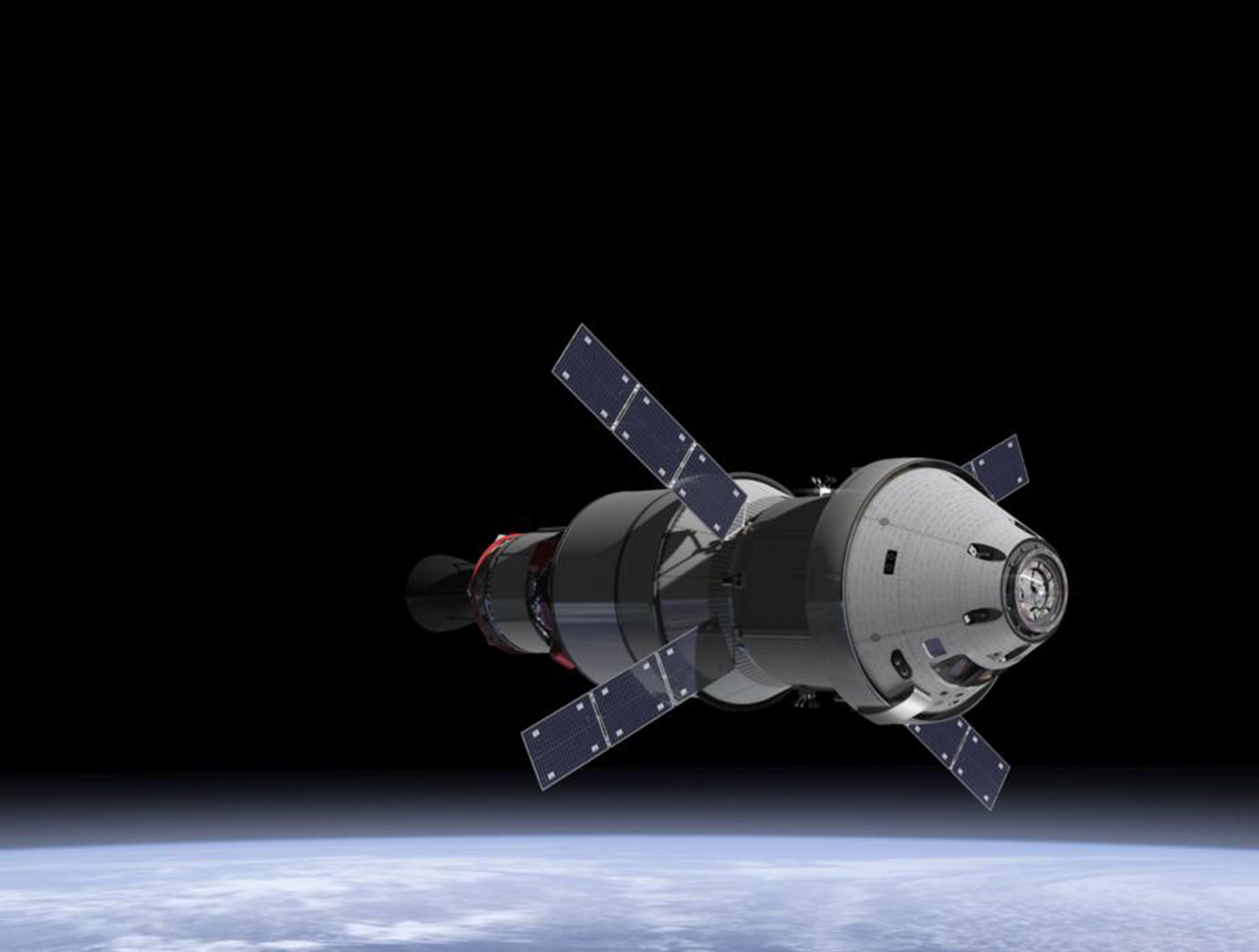
Advanced Protective Coatings for Graphite-Based Nuclear Propulsion Fuel Elements
To protect the graphite (Gr)-based substrates in a nuclear systems fuel elements from hot hydrogen attacks, earlier researchers developed a method to deposit (via chemical vapor deposition) a protective niobium carbide (NbC) or zirconium carbide (ZrC) coating in the inner cooling channels of the fuel elements through which the hydrogen propellant flows. Unfortunately, the significant difference in the coefficients of thermal expansion (CTE) between the Gr-based substrate and the ZrC coating leads to debonding at intermediate temperatures, thereby exposing the substrate to hot hydrogen attack despite the NbC or ZrC coating. Innovators at Glenn have proposed a solution to this problem by introducing additional layers of compliant metallic coatings to accommodate the differences in CTE between the ZrC and the Gr-substrate,thereby potentially increasing life and durability. In this configuration,the innermost layer is composed of molybdenum carbide (Mo2C), and additional outer layers are made of molybdenum (Mo) and niobium (Nb) layers. The MoC acts as a diffusion barrier to minimize the diffusion of carbon into the refractory metal layers and the diffusion of Mo or Nb into the Gr-based substrate. The Mo layer is deposited on top of the Mo2C layer. A Nb layer is deposited on the Mo layer with the ZrC forming the outside layer of the coating. A thin Mo layer on the ZrC helps to seal the cracks on the ZrC and acts a diffusion barrier to hydrogen diffusion into the coating.The Mo and Nb layers are compliant so that differences in the thermal expansion of ZrC and other layers can be accommodated without significant debonding or cracking. They also act as additional diffusion barriers to hydrogen diffusion towards the Gr-substrate. Overall, Glenn's pioneering use of layered coatings for these components will potentially increase the durability and performance of nuclear propulsion rockets.
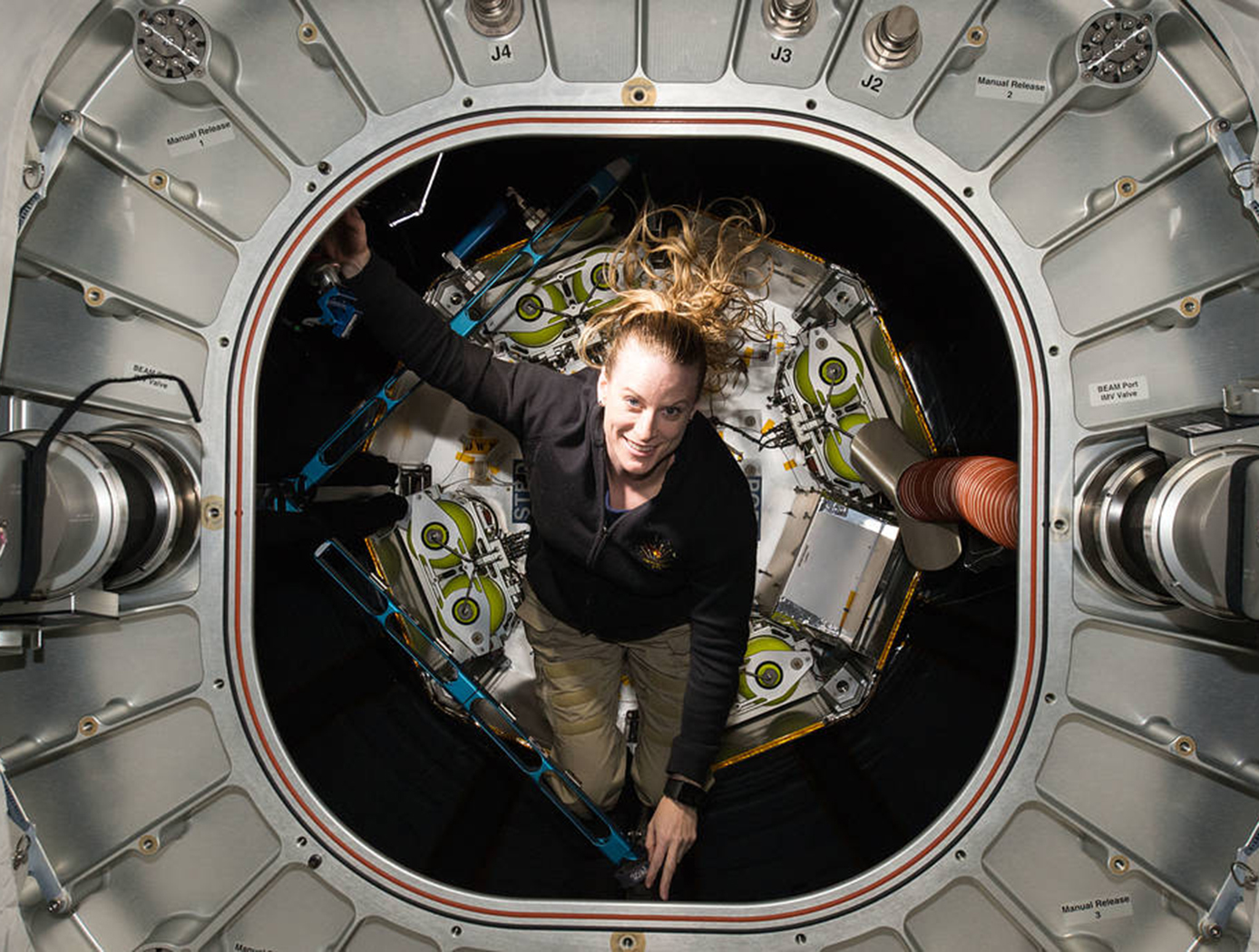
Multi-Stage Filtration System
While HEPA filter elements can last for years without intervention, pre-filtering systems that remove larger particles before they reach the HEPA filter need to be treated (most often by cleaning or replacement) as often as once a week. These treatments can be resource-intensive and expensive, especially in extreme environments. Glenn's innovative system combines a pre-filtration impactor and a scroll filter that reduces the need to replace the more sensitive or expensive filters, extending the system's working life. The system uses an endless belt system to provide the impaction surface. A thin layer of low-toxicity grease is applied to the impaction surface to increase particle adhesion. A high flow turning angle near the impaction surface causes relatively large particles to impact and stick to the surface while smaller particles stay within the air flow. When the surface is covered with particles - or if a layer of particles has grown to a thickness that impairs adhesion - the surface is regenerated. The band is rotated so that the loaded surface passes by a scrapper, removing the layer of particles and a clean segment of the band revolves to become the new impaction surface.
A further innovation is the scroll filter which allows the filtration media to be rotated out of the airflow when fully loaded, providing multiple changes of the filter through a motorized scrolling or indexing mechanism. When nearly fully loaded with dust particles, the exposed media is mechanically rolled up on one side of the filter to both contain and compactly store the dust. The spools that hold the clean and spent filter media are mounted on roller bearings to facilitate the scrolling operation and reduce motor power requirements. Nearly any grade of filter media can be used to meet the desired filtration specification. Additional media rolls can be added after the original roll is spent to further increase filter life.
View more patents