Advanced Protective Coatings for Graphite-Based Nuclear Propulsion Fuel Elements
materials and coatings
Advanced Protective Coatings for Graphite-Based Nuclear Propulsion Fuel Elements (LEW-TOPS-51)
Protects crucial components from hot hydrogen attack and corrosion
Overview
Scientists at NASA's Glenn Research Center have developed novel ways to protect fuel elements used in hot hydrogen gas-propelled nuclear thermal propulsion (NTP) engines. These fuel elements often feature a graphite (Gr)-based substrate, which can react with the hydrogen to form methane and other hydrocarbons, leading to a hot hydrogen corrosive attack. As a result, the Gr-based substrate erodes with time, thus affecting reactor neutronics and performance and leading to a premature shut-down of the NTP engine. Glenn's researchers have conceptualized a technique to create and layer protective coatings that act as a diffusion barrier between the hydrogen and the substrate. These innovations will potentially have a broad impact, as fuel elements for nuclear reactors increasingly have applications in the commercial nuclear power industry, nuclear powered submarines and ships, and outer space systems.
The Technology
To protect the graphite (Gr)-based substrates in a nuclear systems fuel elements from hot hydrogen attacks, earlier researchers developed a method to deposit (via chemical vapor deposition) a protective niobium carbide (NbC) or zirconium carbide (ZrC) coating in the inner cooling channels of the fuel elements through which the hydrogen propellant flows. Unfortunately, the significant difference in the coefficients of thermal expansion (CTE) between the Gr-based substrate and the ZrC coating leads to debonding at intermediate temperatures, thereby exposing the substrate to hot hydrogen attack despite the NbC or ZrC coating. Innovators at Glenn have proposed a solution to this problem by introducing additional layers of compliant metallic coatings to accommodate the differences in CTE between the ZrC and the Gr-substrate,thereby potentially increasing life and durability. In this configuration,the innermost layer is composed of molybdenum carbide (Mo2C), and additional outer layers are made of molybdenum (Mo) and niobium (Nb) layers. The MoC acts as a diffusion barrier to minimize the diffusion of carbon into the refractory metal layers and the diffusion of Mo or Nb into the Gr-based substrate. The Mo layer is deposited on top of the Mo2C layer. A Nb layer is deposited on the Mo layer with the ZrC forming the outside layer of the coating. A thin Mo layer on the ZrC helps to seal the cracks on the ZrC and acts a diffusion barrier to hydrogen diffusion into the coating.The Mo and Nb layers are compliant so that differences in the thermal expansion of ZrC and other layers can be accommodated without significant debonding or cracking. They also act as additional diffusion barriers to hydrogen diffusion towards the Gr-substrate. Overall, Glenn's pioneering use of layered coatings for these components will potentially increase the durability and performance of nuclear propulsion rockets.
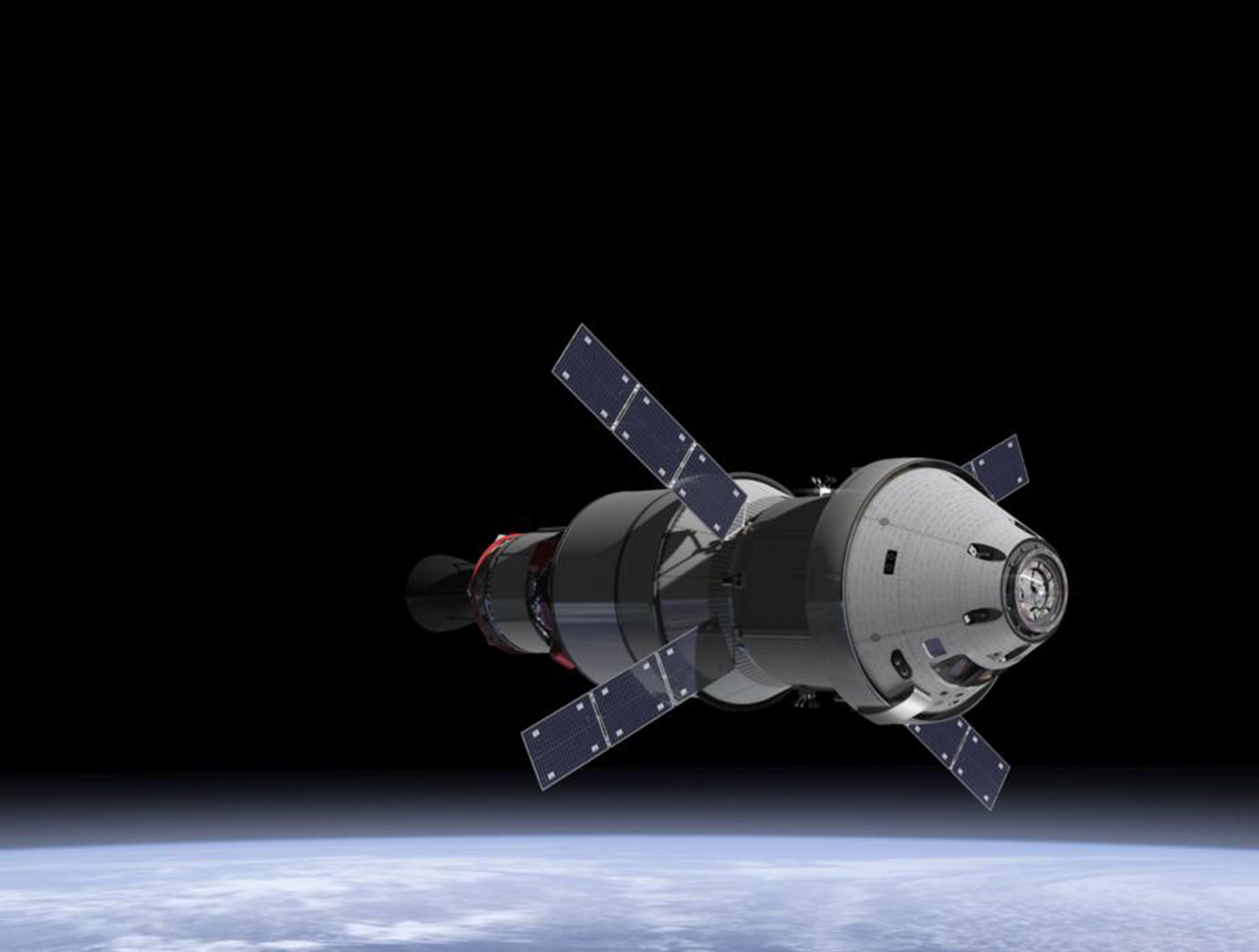
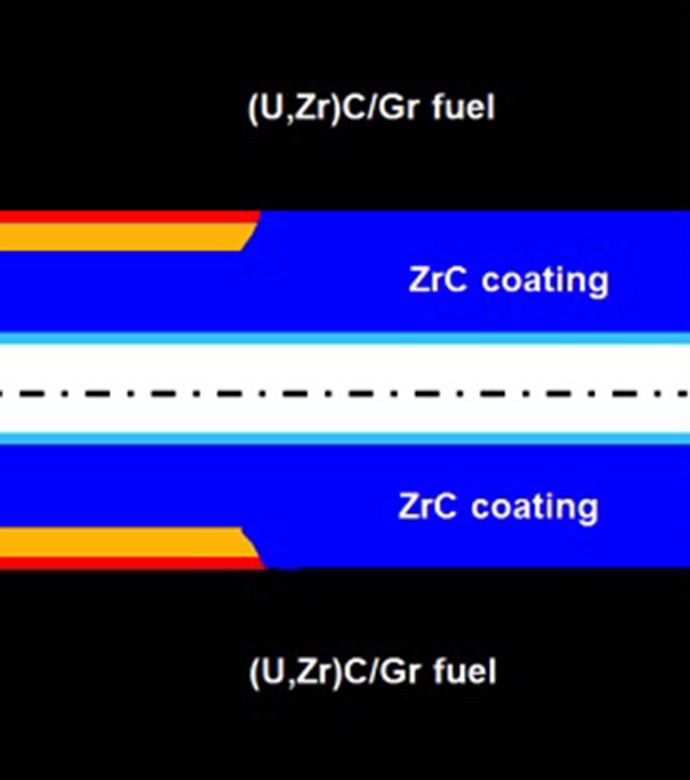
Benefits
- Increased efficiency: Prevents damage within fuel rods and thus keeps nuclear systems running without generating problems leading to a shutdown
- Decreased cost: Lessens the need to replace corroded or damaged components in nuclear systems
- Improved durability: Reduces debonding between the coating and the substrate, thus keeping out destructive hydrogen
Applications
- Aerospace (e.g., outer space systems)
- Commercial nuclear power generation
- Military transport (e.g., nuclear-powered submarines and ships)
Similar Results

Holey Carbon Allotropes
This invention is for scalable methods that allows preparation of bulk quantities of holey nanocarbons with holes ranging from a few to over 100 nm in diameter. The first method uses metal particles as a catalyst (silver, copper, e.g.) and offers a wider range of hole diameter. The second method is free of catalysts altogether and offers more rapid processing in a single step with minimal product work-up requirements and does not require solvents, catalysts, flammable gases, additional chemical agents, or electrolysis. The process requires only commercially available materials and standard laboratory equipment; and, it is scalable. Properties that can be controlled include: surface area, pore volume, mechanical properties, electrical conductivity, and thermal conductivity.

Environmental Barrier Coatings for Ceramic Matrix Composites
CMCs are a game-changer for a number of applications because of their lighter weight, higher temperature capability, and resistance to oxidation. It has been estimated that aircraft designs relying on CMCs can decrease fuel consumption by 10% by 2020. EBCs are used to protect CMCs from water vapor and other corrosive gases inside engines and other extreme environments. The current state of the art for EBCS features a silicon bond coat that is not viable beyond its melting point of 1482°C. By contrast, Glenn's EBCs have demonstrated a steam oxidation life of at least 500 hours at 1482°C, making them ideal durable coatings for next-generation CMCs. These EBCs are slurries, with either a mullite-based bond coat or a rare earth disilicate-based bond coat comprising at least three and two layers, respectively. Mullite is often used as a refractory material for furnaces, reactors, etc. because of its high melting point (1840°C). Rare earth disilicates also have high melting points (~1800°C). These bond coats can be fabricated by preparing a mixture of a coating material, a primary sintering aid, at least one secondary sintering aid, and a solvent. The mixture is then processed (e.g., in a milling media) to form a slurry that can be deposited to a CMC substrate. The sintering aids have two primary functions: 1) densifying deposited slurry by generating liquid phases via reactions with the coating material and other sintering aids, so that the liquid fills gaps between particles of coated material; 2) enhancing bonding and performance of the coating by generating reaction products that enhance those qualities. One great advantage of this EBC is that it can be fabricated via various low-cost methods - including dipping, spinning, spin-dipping, painting, and spraying - in addition to plasma-spraying. Glenn's innovation rises to meet the need for a new class of EBCs that can keep up with CMCs' increasing ability to withstand higher temperatures and stresses than ever before.

High-Temperature Single Crystal Preloader
For extremely high-temperature sealing applications, Glenn researchers have devised novel methods for fabricating single-crystal preloaders. NASA's high-temperature preloaders consist of investment cast or machined parts that are fabricated in various configurations from single crystal superalloys. Machined preloaders include a variety of spring configurations, compressed axially or radially, fabricated from single crystal slabs. Before machining, the slabs are carefully oriented in a special goniometer using x-diffraction techniques. This helps to maintain proper crystal orientation relative to the machined part and the applied loads. For more complex geometry components which cannot be easily and economically machined, an investment casting approach would be used. Complex preloader geometries include wire coil springs of various configurations. These single crystal preloaders would be designed with the appropriate stiffness for the intended thermal barrier/seal application and placed underneath, or integrated within, the seal/barrier. At extrememly high temperature, the preload device keeps the seal/barrier mated against the opposing surface as the gap between the two surfaces changes, maintaining contact between surfaces and preventing convective heat transfer.

High Atomic Number Coatings for Fabrics
High atomic number materials, such as tantalum, do not bond well to oxygen- and hydroxyl-rich surfaces, such as glass fibers. These metals often form surface oxides when layered on glass fabric, resulting in flaking of the high atomic number material off the fabric during cutting, folding, and/or handling.
To improve coating durability, this invention applies a lower atomic number metal as a tie down layer first before applying the high atomic number metal layer. The tie down layer reduces oxide formation between the substrate and the high atomic number material, promoting adhesion. Titanium has shown strong adhesion with different metals and is effective at reducing oxide formation when diffusion bonded to itself or other materials. It has been shown to be effective at improving durability when thermally sprayed onto a glass fiber fabric as a tie down layer for a subsequent tantalum layer (also applied via RF plasma spray). The titanium layer is only approximately 1 mil thick but results in strong adhesion of the tantalum layer by inter-metallic or diffusion bonding. A thermal spray process may be used, as well.
This innovation enables the delivery of high atomic metal coating on glass fiber fabrics and other polymeric substrates that are lower cost, lighter weight, and durable to form a flexible cloth material with Z-graded radiation shielding. Coated samples have been produced and the technology is currently at a technology readiness level (TRL) of 4 (prototype).

Cryogenic Selective Surfaces
These materials, which are composed of highly optically transmissive materials, are engineered to provide near-perfect reflection of the full solar spectrum in space. The materials are finely divided such that they scatter and reflect the incoming radiation from the UV down into the mid-IR and are also coated in some fashion with silver to extend the reflectance down into the far IR region of the solar spectrum. With this near-perfect reflectance of the complete solar spectrum, the scientists envision use of these materials for maintaining cryogenic temperatures for extended periods of time in space. The materials have also been developed into highly flexible, moisture resistant selective surface paint.The use and storage of cryogenics fluids is critical to many space operations, and while there are thermal control coatings in use today for spacecraft, none can provide this near-perfect reflection required for long-term maintenance of cryogenic temperatures.