Search
Mechanical and Fluid Systems

Reverse Vortex Ring (RVR)
Vibration problems, which occur more frequently in high power to weight machines, often lead to costly down time, subsequent redesign, and, in some instances, catastrophic failure. A disproportionate number of vibration problems in rotating machinery can be attributed to highly pre-swirled fluid entering tight clearance locations such as seals and fluid bearings. The relationship between high fluid pre-swirl and undesirable vibration issues is clear. Machines with high levels of fluid pre-swirl are more susceptible to instabilities and vibration problems.
A top priority in rotor dynamic design, therefore, is to develop devices to minimize the level of fluid pre-swirl entering tight clearance locations. The RVR was designed to condition the flow prior to entering the seal (or axial flow fluid-film bearing) so that the flow through the annular clearance is at a minimum purely axial. While conventional swirl brakes have only been shown to reduce pre-swirl by up to 30%, the RVR can actually reverse the direction of the swirl, so that circumferential fluid velocity flows in a direction counter to shaft rotation. Thus, a classic detriment to rotating machinery has now become an asset to ameliorate vibration issues through the RVR.
The RVR is axially efficient, typically increasing the axial length of a smooth annular seal on the order of 10-12%.
The RVR has been extensively tested and is now in use at NASA.
mechanical and fluid systems
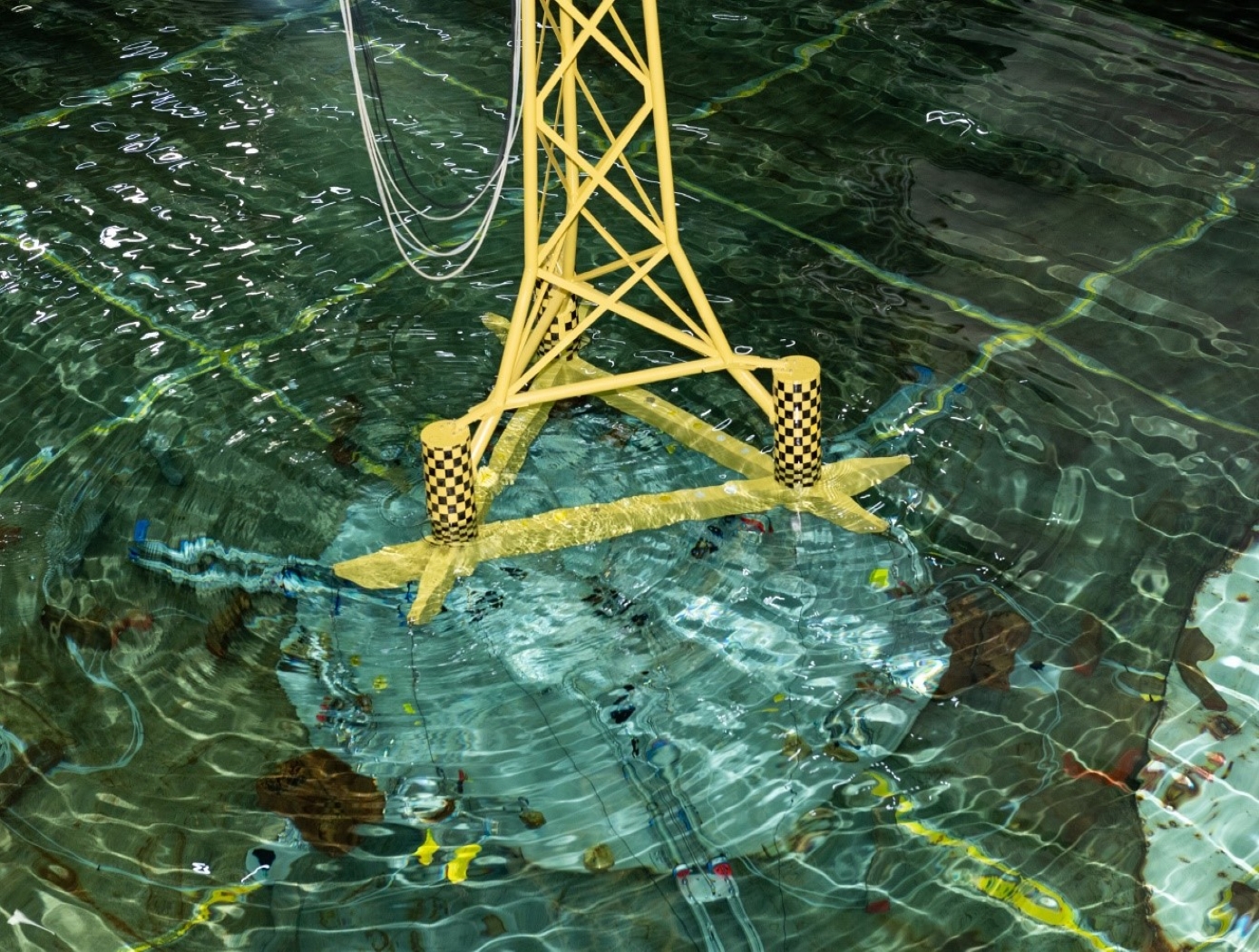
Tension Element Vibration Damping
NASAs Tension Element Vibration Damping technology presents a novel method of managing the dynamic behavior of structures by capturing the vibrational displacement of the structure via a connecting link and using this motion to drive a resistive element. The resistive element then provides a force feedback that manages the dynamic behavior of the total system or structure. The damping force feedback can be a tensile or compressive force, or both. Purely tensile force has advantages for packaging and connection alignment flexibility while combined tensile/compression forces have the advantage of providing damping over a complete vibratory cycle.
This innovation can be readily applied to existing structures and incorporated into any given design as the connecting element is easily affixed to displacing points within the structure and the resistive element to be located in available space or a convenient location. The resistive element can be supplied by any one of either hydraulic, pneumatic or magnetic forces. As such the innovation can provide a wide range of damping forces, a linear damping function and/or an extended dynamic range of attenuation, providing broad flexibility in configuration size and functional applicability.
NASA-built prototypes have been shown to be highly effective on a 170-foot long wind turbine blade in test beds at the University of Maine.
Mechanical and Fluid Systems
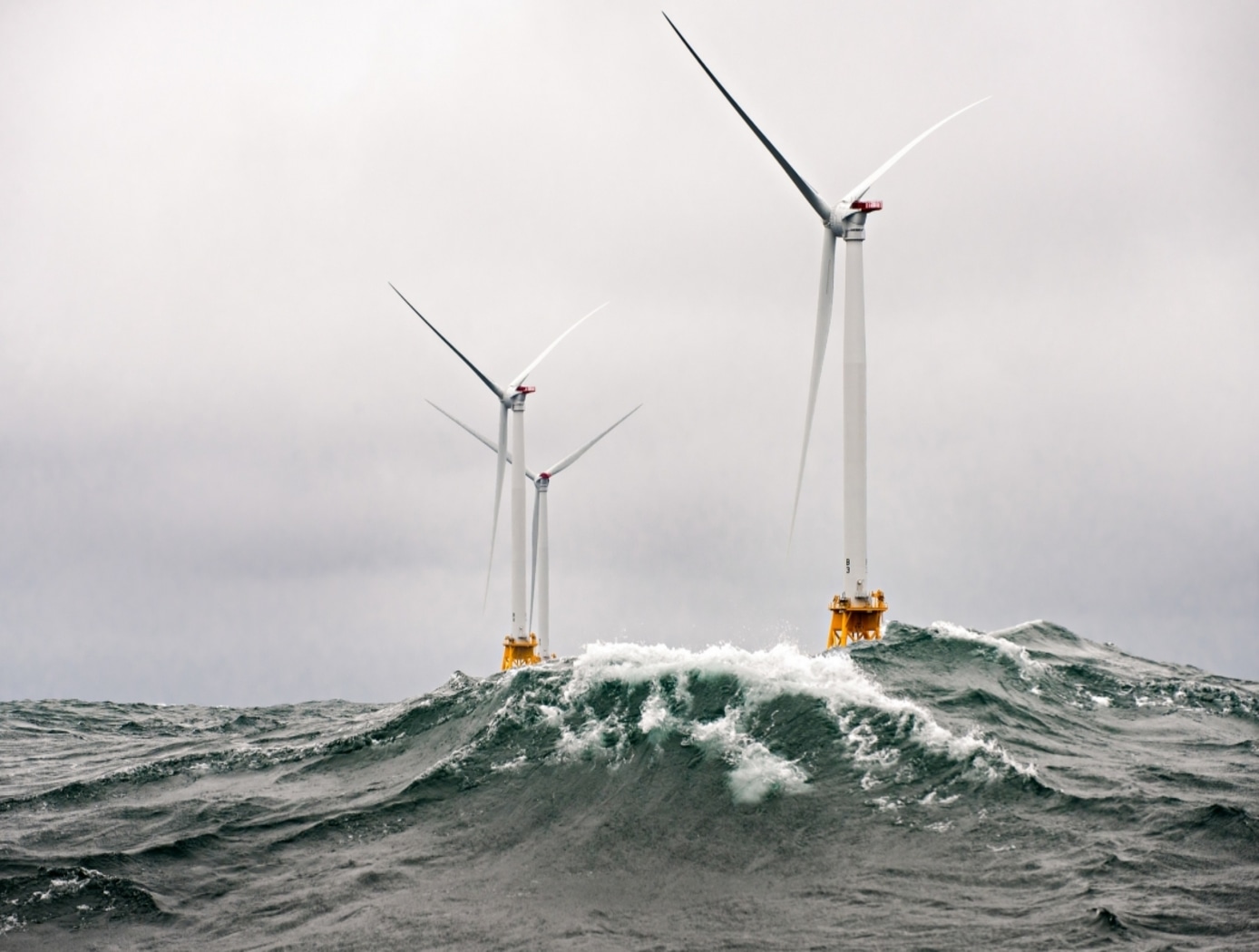
Tension Element Damping (TED) – With Hydraulics for Large Displacements
The Rotational Tension Element Damper (RTED) uses a controlled tension line, backed by hydraulics, to damp large displacements in large structures. NASA built RTED prototypes that have been successfully tested on a 170-foot long wind turbine blade in test beds at the University of Maine. In this case, the RTED device damps the vibration of the large, tall turbine blades relative to a stationary anchor structure on the ground using a line and spring coupled to both the blade and the anchor, and controlled by a spool fitted with a one-way clutch. When force is applied, from heavy wind for example, the resulting movement of the tall structure triggers the necessary tension and compression cycles in the system to engage the rotating damper. The reaction force interferes with the rotation speed of the spool and disrupts and damps the vibration in the tall structure. The figure below shows test data for the RTED used on the wind turbine.
Mechanical and Fluid Systems
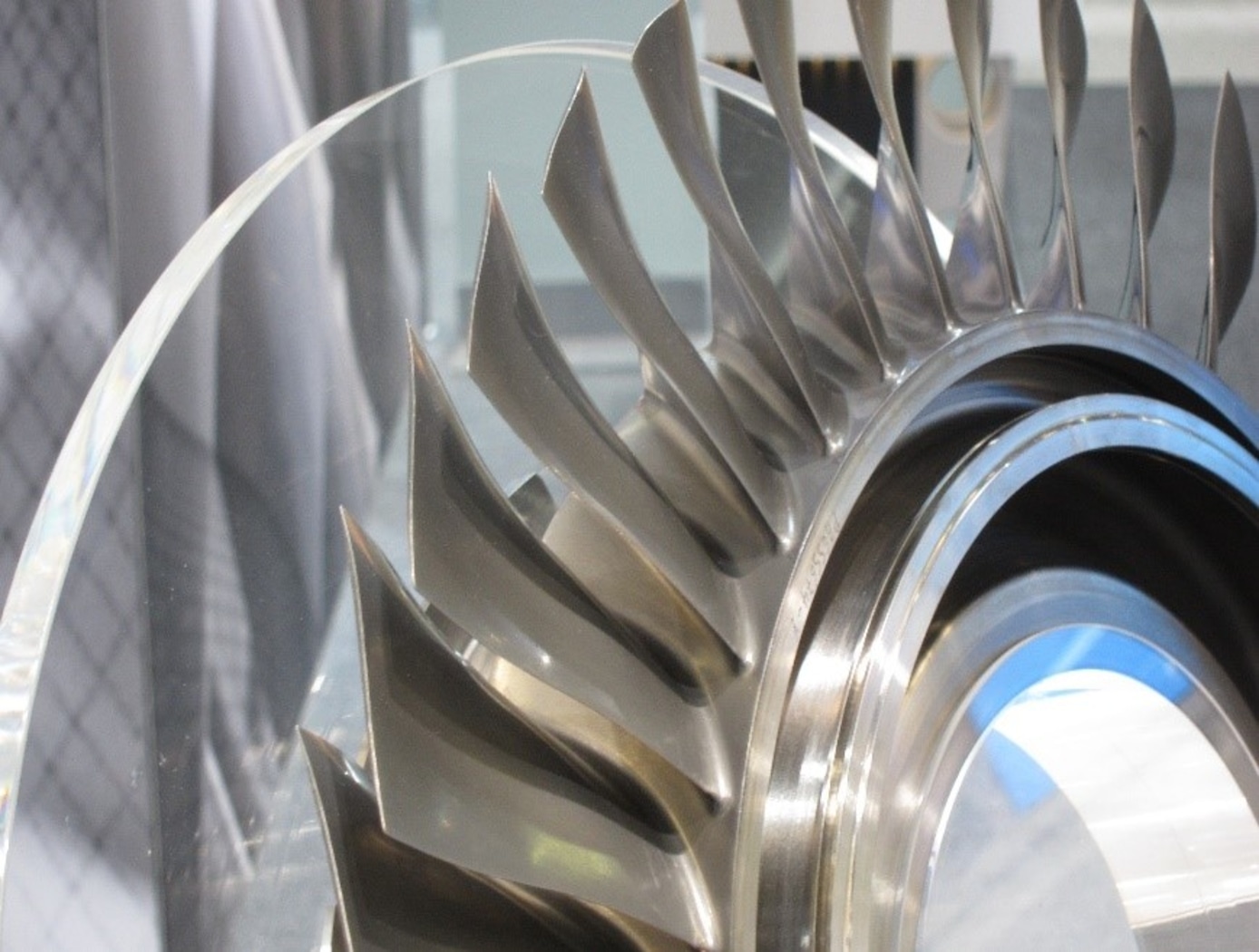
Integral Tuned Mass Absorber for Turbine Blades
Additive manufacturing methods (e.g. Laser Metal Sintering) are used to integrally fabricate a tuned-mass vibration absorber inside a turbine blade. The design approach uses an internal column manufactured as part of the blade that is optimized such that the dynamics of the blade damper system are rearranged and reduced according to the well-known science of tuned mass-absorption (TMA). The TMA concept has been implemented successfully in applications ranging from skyscrapers to liquid oxygen tanks for space vehicles. Indeed, this theory has been conceptually applied to bladed-disk vibration, but a practical design has not previously been reported.
The NASA innovation addresses another important challenge for turbine blade vibration damper designs. All existing blade damper solutions are essentially incapable of being reliably predicted, so an expensive post-design test program must be performed to validate the expected response. Even then, the actual magnitude of the response reduction under actual hot fire conditions may never be known. The dynamic response of this tuned-mass-absorber design is both substantial and can be analytically predicted with high confidence, and thus the response can be incorporated fully into the up-front design process.
Aerospace

Anti-Phase Noise Suppression Rotor Technologies
Rotor noise and vibration are two sources of operational challenges for all aircraft operating with open rotors such as helicopters, unmanned aerial vehicles (UAVs), urban air mobility personal air vehicles, drones, and aircraft operating with ducted fans such as passenger aircraft. One disadvantage of convention rotor design is the noise due to noise-induced shed vortices generated by rotor blades. The unique problem with rotor noise and vibration is the periodic blade passage that causes a harmonic reinforcement and causes the rotor blades to vibrate and generate noise sources. This technology from NASA Ames seeks to optimize the implementation of anti-phase trailing edge designs and asymmetric blade tip treatments for rotor noise suppression and integrated aircraft noise solutions by incorporating the anti-phase rotor design concepts into an aircraft flight control system to reduce noise footprint. There are several embodiments of the invention, which include the following: (1) an anti-phase trailing edge design whereby the trailing edge pattern of the leading rotor blade is offset by a phase shift from the trailing edge pattern of the following blade; (2) an anti-phase rotor design implementing asymmetric blade tips with inverted airfoil; and (3) other anti-phase enabled concepts such as unequal blade length, ducted rotors with non-radial unequally spaced struts, and multi-axis tilt rotor design incorporating the anti-phase rotor design.
Mechanical and Fluid Systems

Improving VTOL Proprotor Stability
Proprotors on tiltrotor aircraft have complex aeroelastic properties, experiencing torsion, bending, and chord movement vibrational modes, in addition to whirl flutter dynamic instabilities. These dynamics can be stabilized by high-frequency swashplate adjustments to alter the incidence angle between the swashplate and the rotor shaft (cyclic control) and blade pitch (collective control). To make these high-speed adjustments while minimizing control inputs, generalized predictive control (GPC) algorithms predict future outputs based on previous system behavior. However, these algorithms are limited by the fact that tiltrotor systems can substantially change in orientation and airspeed during a normal flight regime, breaking system continuity for predictive modeling.
NASA’s Advanced GPC (AGPC) is a self-adaptive algorithm that overcomes these limitations by identifying system changes and adapting its predictive behavior as flight conditions change. If system vibration conditions deteriorate below a set threshold for a set time interval, the AGPC will incrementally update its model parameters to improve damping response. AGPC has shown significant performance enhancements over conventional GPC algorithms in comparative simulations based on an analytical model of NASA’s TiltRotor Aeroelastic Stability Testbed (TRAST). Research for Hardware-In-the-Loop testing and flight vehicle deployment is ongoing, and hover data show improved vibration reduction and stability performance using AGPC over other methods.
The example presented here is an application to tiltrotor aircraft for envelope expansion and vibration reduction. However, AGPC can be employed on many dynamic systems.
mechanical and fluid systems
.jpg)
Fluid-Filled Frequency-Tunable Mass Damper
NASA MSFC’s Fluid-Filled Frequency-Tunable Mass Damper (FTMD) technology implements a fluid-based mitigation system where the working mass is all or a portion of the fluid mass that is contained within the geometric configuration of either a channel, pipe, tube, duct and/or similar type structure. A compressible mechanism attached at one end of the geometric configuration structure enables minor adjustments that can produce large effects on the frequency and/or response attributes of the mitigation system.
Existing fluid-based technologies like Tuned Liquid Dampers (TLD) and Tuned Liquid Column Dampers (TLCD) rely upon the geometry of a container to establish mitigation frequency and internal fluid loss mechanisms to set the fundamental mitigation attributes. The FTMD offers an innovative replacement since the frequency of mitigation and mitigation attributes are established by the compressible mechanism at the end of the container. This allows for simple alterations of the compressible mechanism to make frequency adjustments with relative ease and quickness.
FTMDs were recently successfully installed on a building in Brooklyn, NYC as a replacement for a metallic TMD, and on a semi-submersible marine-based wind turbine in Maine.
The FTMD technology is available for non-exclusive licensing and partially-exclusive licensing (outside of building construction over 300 feet).