Chemical and Topographical Surface Modifications for Insect Adhesion Mitigation
materials and coatings
Chemical and Topographical Surface Modifications for Insect Adhesion Mitigation (LAR-TOPS-183)
Synergistic method to reduce insect adhesion on aluminum surfaces
Overview
NASA Langley Research Center, in collaboration with ATK Space Systems, has developed a method to reduce insect adhesion on metallic substrates, polymeric materials, engineering plastics, and other surfaces. The method topographically modifies a surface using laser ablation patterning followed by chemical modification of the surface. This innovation was originally developed to enhance aircraft laminar flow by preventing insect residue buildup, but the method provides a permanent solution for any application requiring insect adhesion mitigation as well as adhesion prevention of other typical environmental contaminants.
The Technology
The technology is a method of mitigating insect residue adhesion to various surfaces upon insect impact. The process involves topographical modification of the surface using laser ablation patterning followed by chemical modification or particulate inclusion in a polymeric matrix. Laser ablation patterning is performed by a commercially available laser system and the chemical spray deposition is composed of nanometer sized silica particles with a hydrophobic solution (e.g. heptadecafluoro-1,1,2,2-tetrahydrodecyltriethoxysilane) in an aqueous ethanol solution. Both topographic and chemical modification of the substrate is necessary to achieve the desired performance.
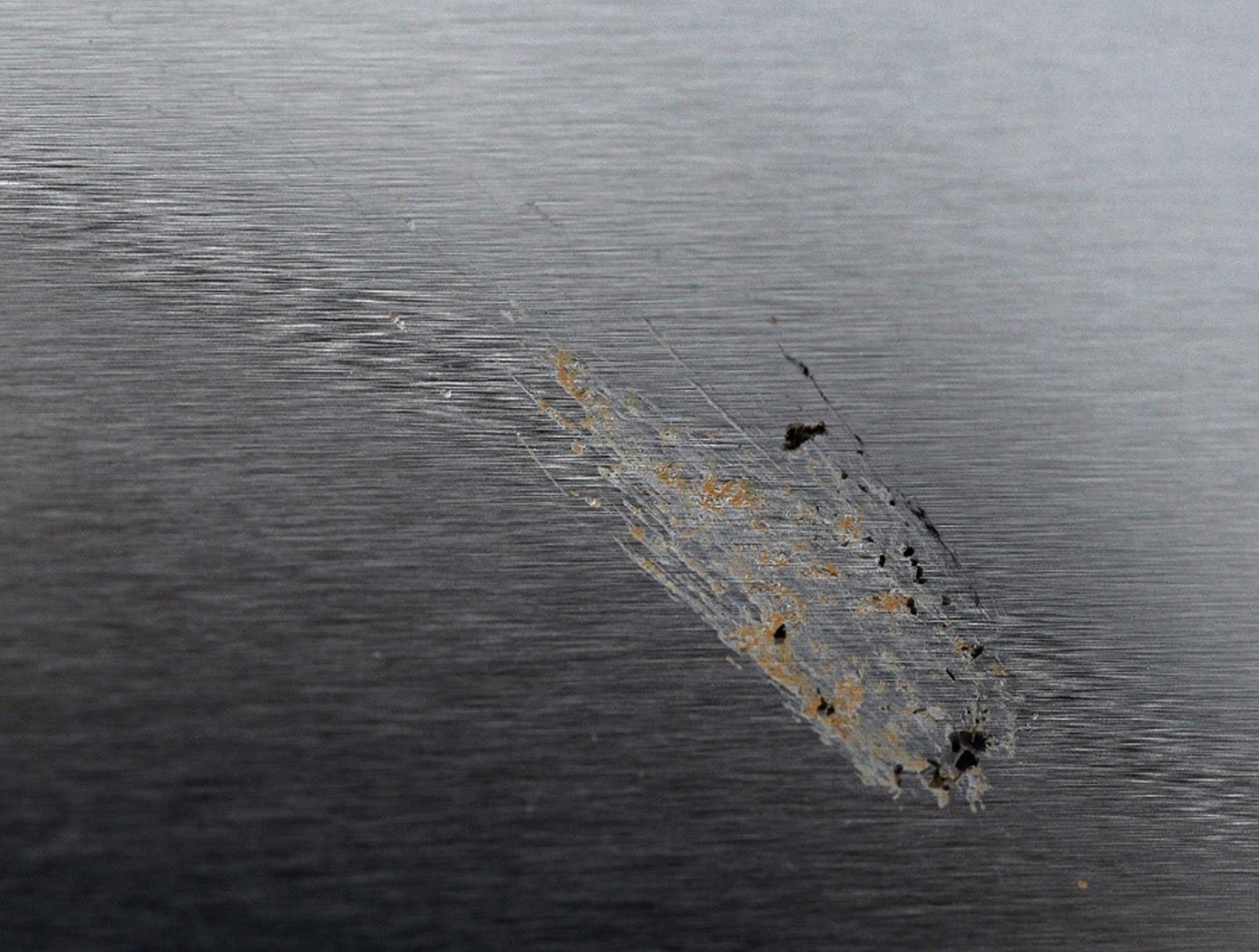
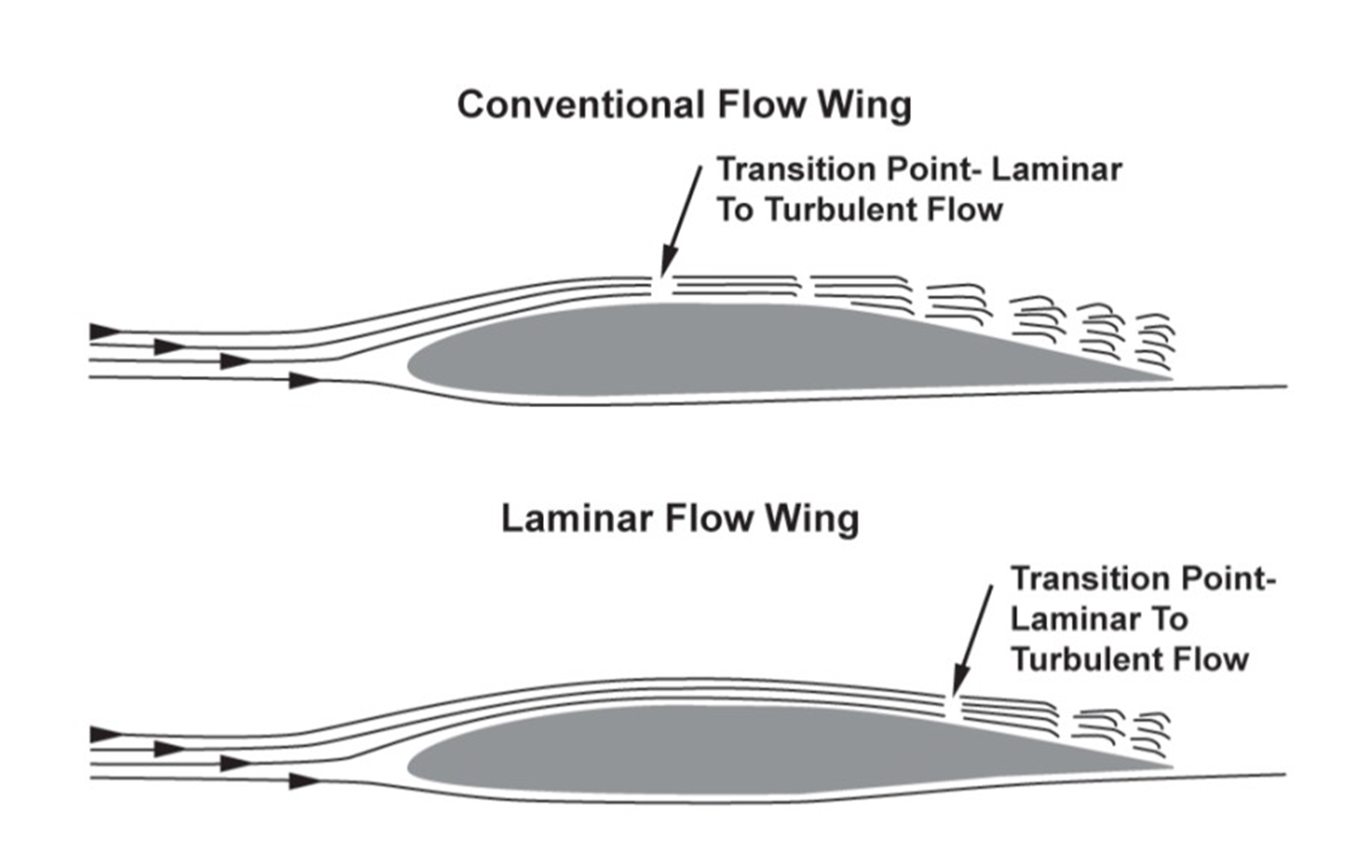
Benefits
- Increased ability to mitigate adhesion of insect residue upon impact compared to currently available solutions in order to significantly reduce laminar flow disruptions
- Surface roughness is not affected by the process
- Permanent insect mitigation solution
Applications
- Aerospace
- Marine
- Automotive
- Wind Energy
Similar Results

Synthesis and Development of Polyurethane Coatings Containing Fluorine Groups for Adhesive Applications
Coatings offer an advantage over previous strategies due to ease of application, potentially negligible weight penalty, reduced environmental concerns, better economics, and continual function throughout the flight profile. In this present innovation, a particular coating has been developed that is similar to the basic component of a majority of aerospace coatings used on commercial aircraft. This coating was then sprayed from a solvent on various substrates. Once spray-coated on a substrate and dried, the coatings were then tested for adhesion mitigation of insect residues in a controlled insect impact facility propelled toward the engineered surface at approximately 150 mph. Once impacted, these coatings demonstrated hydrophobicity and a significant reduction in contaminant adhesion. The coatings were further tested in an operational environment on the eco-demonstrator Boeing 757 aircraft. The coatings resulted in lower insect accumulation than the control surface (no coating). The durability of these coatings was comparable to state-of-the-art formulations and satisfies current aircraft manufacturing requirements. These coatings likely have advantageous use in aerospace applications, wind turbine systems, and automotive industry, among other industries.
This innovation not only appears to solve a problem that has persisted, thus fulfilling an unmet need, but also comprises a new composition of matter that can lead to numerous unforeseen applications.

Hydrophobic Epoxy Coating for Insect Adhesion Mitigation
This technology is a copolymeric epoxy coating that is loaded with a fluorinated aliphatic chemical species and nano- to microscale particle fillers. The coating was developed as a hydrophobic and non-wetting coating for aerodynamic surfaces to prevent accumulation of insect strike remains that can lead to natural laminar flow disruption and aerodynamic inefficiencies. The coating achieves hydrophobicity in two ways. First, the fluorinated aliphatic chemical species are hydrophobic surface modification additives that preferentially migrate to the polymer surface that is exposed to air. Secondly, the incorporation of particle fillers produces a micro-textured surface that displays excellent resistance to wetting. Combined, these two factors increase hydrophobicity and can also be used to readily generate superhydrophobic surfaces.

Particle Contamination Mitigation Methods
The following methods can be used individually or in combination to generate superhydrophobic surfaces:
Synthesis of novel copolyimide oxetanes with unique surface properties
The technology is the synthesis of a polyimide coating or film with a modified surface chemistry shown in Figure 1. A minor amount of an oxetane reactant containing fluorine is added to the polyimide, and the oxetane preferentially migrates to the surface, enabling relatively high concentrations of fluorine at the surface, without compromising the functional performance of the bulk of the polymide coating/film.
The copolymers exhibit mitigation of particle adhesion and fouling from exposure to various particulate and biological contaminants and exhibit reduced surface energy and increased surface fluorine content at extremely low oxetane loadings relative to the imide matrix (see Figure 2). Additionally, the short fluorinated carbon chains do not bioaccumulate, reducing the environmental impact of these materials.
Modifying surface energy via laser ablative surface patterning
This method uses a laser to create nanoscale patterns in the surface of a material to increase the hydrophobicity of the surface (see Figure 2). The benefits of hydrophobic surfaces include decreases in friction and increases in self-cleaning properties. This is an advantageous method of surface modification because it is fast and single-step, promises to be scalable, requires no chemicals, could be applied to a variety of materials, and does not require a planar surface for patterning.

Alternative Transparent Coating Lotus Suitable for Optics with Vacuum Deposition Layer
In addition to previous LOTUS coating formulations, an additional optical formulation may be applied via vacuum deposition. This coating forms a top layer and may be applied in different thicknesses that serve to enhance its hydrophobic properties. The vacuum deposited material may comprise fluorinated ethylene propylene or a similar material. This coating is transparent and can be used on optical components or any other applications requiring a clear coating.

Atomic Number (Z)-Grade Radiation Shields from Fiber Metal Laminates
This technology is a flexible, lighter weight radiation shield made from hybrid carbon/metal fabric and based on the Z-grading method of layering metal materials of differing atomic numbers to provide radiation protection for protons, electrons, and x-rays. To create this material, a high density metal is plasma spray-coated to carbon fiber. Another metal with less density is then plasma spray-coated, followed by another, and so on, until the material with the appropriate shielding properties is formed. Resins can be added to the material to provide structural adhesion, reducing the need for mechanical bonding. This material is amenable to molding and could be used to build custom radiation shielding to protect cabling and electronics in situations where traditional metal shielding is difficult to place.