Modular Artificial-Gravity Orbital Refinery Spacecraft
Manufacturing
Modular Artificial-Gravity Orbital Refinery Spacecraft (TOP2-299)
Space mining and in-situ resource utilization
Overview
The Modular Artificial-Gravity Orbital Refinery Spacecraft is a novel technology from NASA Ames Research Center for in-situ refining or recycling of materials in space, including mass from asteroids, Mars moons, orbiting "space junk" debris, and for in-situ creation of products from operations in low or micro-gravity environments. There has been considerable interest in the exploration and mining of asteroids with spacecraft as well as mitigating the growing threat of space debris. Refining operations, such as centrifugal refining processes, introduce challenges for operating in space that are not relevant on Earth, including the need for gravity in order for refining operations to function properly. This technology provides an effective and efficient approach to address these needs and challenges.
The Technology
Modular Artificial-Gravity Orbital Refinery Spacecraft is a solution for refining in-situ materials collected in space, such as from asteroids and Mars moons, as well as recycling spacecraft debris, while orbiting in micro-gravity conditions. The spacecraft is coupled with refining modules for refining and recycling different types of materials. It generates artificial gravity for operation in low-gravity environments. The spacecraft is comprised of rotating rings, each generating artificial gravity and angular momentum. When the rotating rings are combined on the spacecraft platform, however, they have a net near-zero angular momentum such that the spacecraft can change its attitude with minimal propellant or rotate at the rate of the object the spacecraft platform is attached to. The spacecraft platform can self-balance to accommodate different sized modules and modules with moving loads. The refined and recycled materials can be used to create products in-situ as well as products too large to launch from Earth, such as construction of orbiting space habitats, large spacecraft, solar-power stations, and observatories.
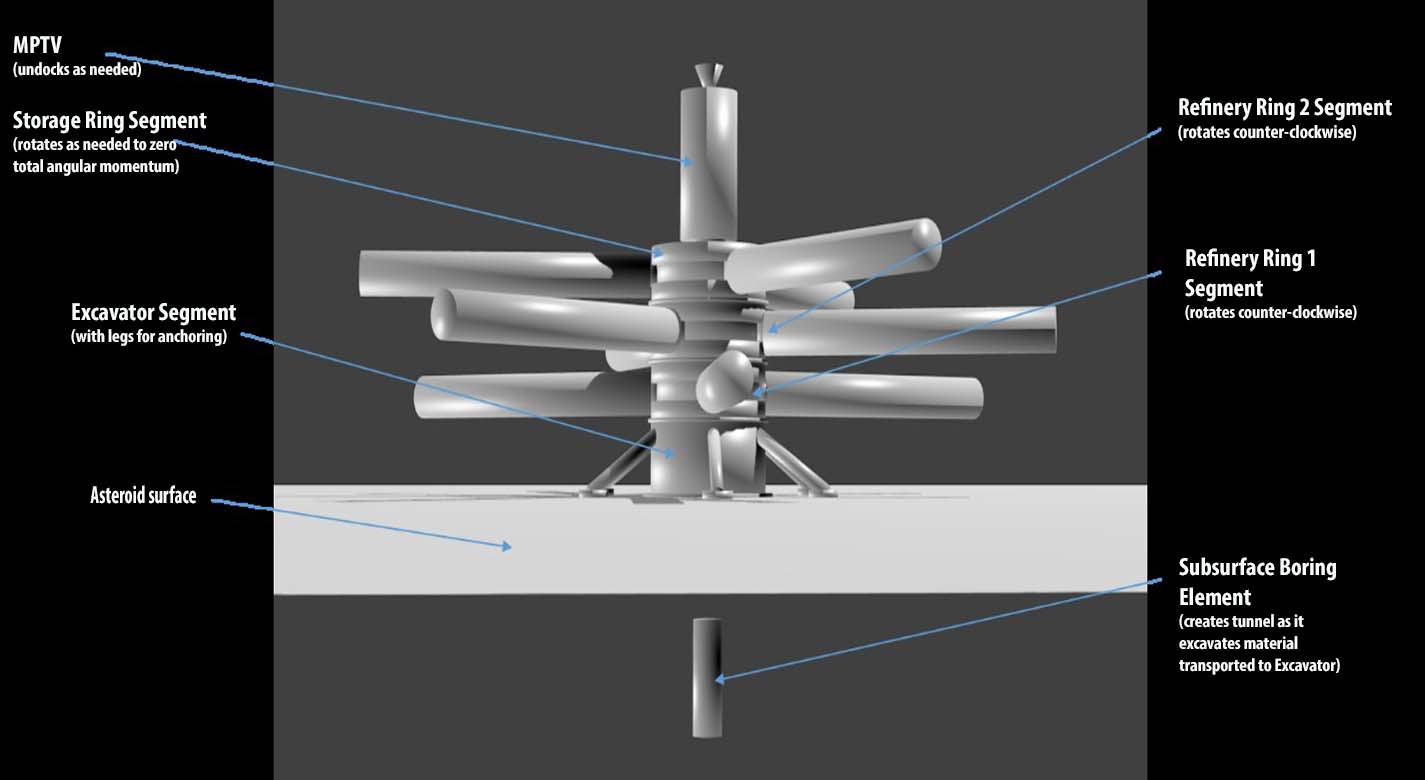
Benefits
- Relevant to emerging industry of asteroid mining
- Refines materials locally in space using artificial gravity rather than using materials mined, refined, and transported from Earth
- Recycles orbiting debris including spacecraft components no longer operational and provides economic incentive for reducing orbital hazards for space travel and on Earth
- Uses zero-angular momentum artificial-gravity spacecraft for minimal-propellant operation
- Uses dynamic balancing to compensate for changes in its center of mass during the refining and casting/extruding processes
- Scalable design for a wide array of applications from spacecraft less than ten meters to greater than one hundred meters in diameter
- Capable of locally producing additional mining and refinery equipment as well as modules for refined material storage and transport
Applications
- Space industry
- Deep space industry
- Mining and refining asteroid and Mars moon mass
- In-situ space resource utilization
- Orbital refinery
- Orbital debris recycling
- Orbital construction
- Space manufacturing
Tags:
|
Similar Results

Spacecraft with Artificial Gravity Modules
Conventionally, the approaches of creating artificial gravity in space was envisioned as a large rotating space station that creates an inertial force that mimics the effects of a gravitational force. However, generating artificial gravity with large rotating structures poses problems, including (1) the need to mass balance the entire rotating spacecraft in order to eliminate or minimize rotational imbalance causing gyroscopic precession/nutation motions and other oscillations of the rotating spacecraft; (2) the potentially prohibitive cost, time and schedule to build such a large rotating system; (3) the need to mass balance the spacecraft in real-time so as to minimize passenger discomfort and structural stress on the spacecraft; (4) the difficulty in docking other spacecraft to the rotating spacecraft; (5) the absence or minimal presence of non-rotating structure for 0G research and industrial use; and (6) the generation of extraneous Coriolis effect on spacecraft inhabitants. The novel technology can help solve the problems referenced above and other problems by (1) providing a non-rotating space station or structure, and connecting modules that generate artificial gravity by traveling along a circular path around the non-rotating space station; (2) providing modules that are more easily built and balanced; (3) providing a stationary structure that can provide a platform for other components that do not need gravity to function; (4) providing capability to actively interrogate what levels of mass imbalance are acceptable, for use in determining operational constraints; and (5) reducing or eliminating Coriolis effect on occupants in habitation modules. The concepts of the invention are very cost-effective and allow for building a minimal initial system to produce artificial gravity at the first phases of construction, before the full structure is built. An additional benefit is that construction and assembly of new capabilities can be performed without disrupting the ongoing artificial gravity environment of the existing structure.

Modular System for Waste Treatment, Water Recycling, and Resource Recovery
Because resupply of commodities for long duration space missions would be prohibitively expensive and could take an extensive length of time to reach habitats in orbit around or on other planetary bodies, it is critical that astronauts have the ability to recycle and reuse local waste streams to provide resources such as clean water, fuel, and nutrients for growing plants. Scientists at Kennedy Space Center and the University of South Florida have developed a technology that addresses this critical mission need. The modular system design incorporates all wastewater streams and some food waste including urine water, hygiene water, humidity condensate, Sabatier water, fecal waste, laundry water, and organic food waste. These sources are fed simultaneously into the system, and a function-driven, sequential purification process occurs. The primary processes include carbon conversion, phase separation (solid/liquid/gas), disinfection, nutrient/salts management, and salts balancing to generate a clean water stream. The heart of the closed-loop bio-regenerative system is an anaerobic membrane bioreactor (AnMBR), which takes raw wastewater streams and utilizes an anaerobic microbial consortium to carry out the breakdown of the organic matter. An ultrafiltration membrane captures and destroys pathogenic bacteria and viruses. The AnMBR system generates a clean water stream containing fertilizer constituents which can be used to cultivate either microalgae (for food, pharma/nutraceuticals, fuel or bioplastics) in photobioreactors or crops in hydroponic systems. The system also generates methane and hydrogen gas which can be used for fuel (or conversion to bioplastics), and CO2 which can be used to support plant growth.

Regolith Advanced Surface Systems Operations Robot (RASSOR) Excavator
Regolith excavation is desired in future space missions for the purpose of In Situ Resource Utilization (ISRU) to make local commodities, such as propellants and breathing air, and to pursue construction operations. The excavation of regolith on another planetary body surface, such as the Moon, Mars, an asteroid, or a comet is extremely difficult because of the high bulk density of regolith at lower depths. Additionally, because of the low gravity in these space surface environments, the mass of the excavator vehicle does not provide enough reaction force to enable the excavation blade to penetrate the regolith if traditional terrestrial methods are used.
RASSOR uses counterrotating bucket drums on opposing arms to provide near-zero horizontal and minimal vertical net reaction force so that excavation is not reliant on the traction or weight of the mobility system to provide a reaction force to counteract the excavation force in low-gravity environments. The excavator can traverse steep slopes and rough terrain, and its symmetrical design enables it to operate in reverse so that it can recover from overturning by continuing to dig in the new orientation. The system is capable of standing up in a vertical position to dump into a receiving hopper without using a ramp. This eliminates the need for an onboard dump bin, thus reducing complexity and weight.
During loading, the bucket drums excavate soil/regolith by scoops mounted on the drums exteriors that sequentially take multiple cuts of soil/regolith while rotating at approximately 20 revolutions per minute. During hauling, the bucket drums are raised by rotating the arms to provide clearance above the surface being excavated. The mobility platform can then travel while the soil/regolith remains in the raised bucket drums. When the excavator reaches the dump location, the bucket drums are commanded to reverse their direction of rotation, which causes soil/regolith to be expelled out of each successive scoop. RASSOR has wireless control, telemetry, and onboard transmitting cameras, allowing for teleoperation with situational awareness. The unit can be programmed to operate autonomously for selected tasks.

Low-Temperature Oxidation/
Reduction Catalysts
The low-temperature oxidation catalyst technology employs a novel catalyst formulation, termed platinized tin oxide (Pt/SnOx). The catalysts can be used on silica gel and cordierite catalyst supports, and the latest developments provide sprayable formulations for use on a range of support types and shapes. Originally developed for removal of CO, the catalyst has also proven effective for removal of formaldehyde and other lightweight hydrocarbons.
NASA researchers have also extended the capability to include reduction of NOx as well as developed advanced chemistries that stabilized the catalyst for automotive catalytic converters via the engineered addition of other functional components. These catalyst formulations operate at elevated temperatures and have performed above the EPA exhaust standards for well beyond 25,000 miles. In addition, the catalyst can be used in diesel engines because of its ability to operate over an increased temperature range.
For use as a gas sensor, the technology takes advantage of the exothermic nature of the catalytic reaction to detect formaldehyde, CO, or hydrocarbons, with the heat being produced proportional to the amount of analyte present.

In-Situ Resource Utilization (ISRU): Methylotrophic Microorganisms Expressing Soluble Methane Monooxygenase Proteins
Microorganisms are unique from the standpoint that they can be employed as self-replicating bio-factories to produce both native and engineered mission relevant bio-products. Methane (CH4) usage in In-Space Manufacturing (ISM) platforms has been discussed previously for human exploration and has been proposed to be used in physicochemical systems as a propulsion fuel, supply gas, and in fuel cells. Carbon Dioxide (CO2) is abundant on Mars and manned spacecraft. On the International Space Station (ISS), NASA reacts excess CO2 with Hydrogen (H2) to generate CH4 and Water (H2O) using the Sabatier System (Figure 1). The resulting water is recovered in the ISS, but the methane is vented to space. Recapturing this methane and using it for microbial manufacturing could provide a unique approach in development of in-space bio-manufacturing. Thus, there is a capability need for systems that convert methane into valuable materials. Methane (CH4) is a potential carbon substrate for methanotrophic microorganisms which are able to metabolize CH4 into biomass. The innovative technology from NASA Ames Research Center ports Soluble Methane Monooxygenase (sMMO) to Pichia, that is, it moves the methane metabolism into a robust microbial factory (Pichia pastoris) (Figure 2). The yeast Pichia pastoris is a refined microbial factory that is used widely by industry because it efficiently secretes products. Pichia could produce a variety of useful products in space. Pichia does not consume methane but robustly consumes methanol, which is one enzymatic step removed from methane. This novel innovation engineers Pichia to consume methane thereby creating a powerful methane-consuming microbial factory and utilizing methane in a robust and flexible synthetic biology platform.