Search
Materials and Coatings

Advanced Materials for Electronics Insulation
Many researchers have attempted to use polymer-ceramic composites to improve the thermal and dielectric performance of polymer insulation for high voltage, high temperature electronics. However, using composite materials has been challenging due to manufacturing issues like incomplete mixing, inhomogeneous properties, and void formation. Here, NASA has developed a method of preparing and extruding polymer-ceramic composites that results in high-quality, flexible composite ribbons.
To achieve this, pellets of a thermoplastic (e.g., polyphenylsulfone or PPSU) are coated with an additive then mixed with particles of a ceramic (e.g., boron nitride or BN) as shown in the image below. After mixing the coated polymer with the ceramic particles, the blended material was processed into ribbons or films by twin-screw extrusion. The resulting ribbons are highly flexible, well-mixed, and void free, enabled by the coated additive and by using a particle mixture of micronized BN and nanoparticles of hexagonal BN (hBN).
The polymer-ceramic composite showed tunable dielectric and thermal properties depending on the exact processing method and composite makeup. Compared to the base polymer material, the composite ribbons showed comparable or improved dielectric properties and enhanced thermal conductivity, allowing the composite to be used as electrical insulation in high-power, high-temperature conditions.
The related patent is now available to license. Please note that NASA does not manufacturer products itself for commercial sale.
Materials and Coatings
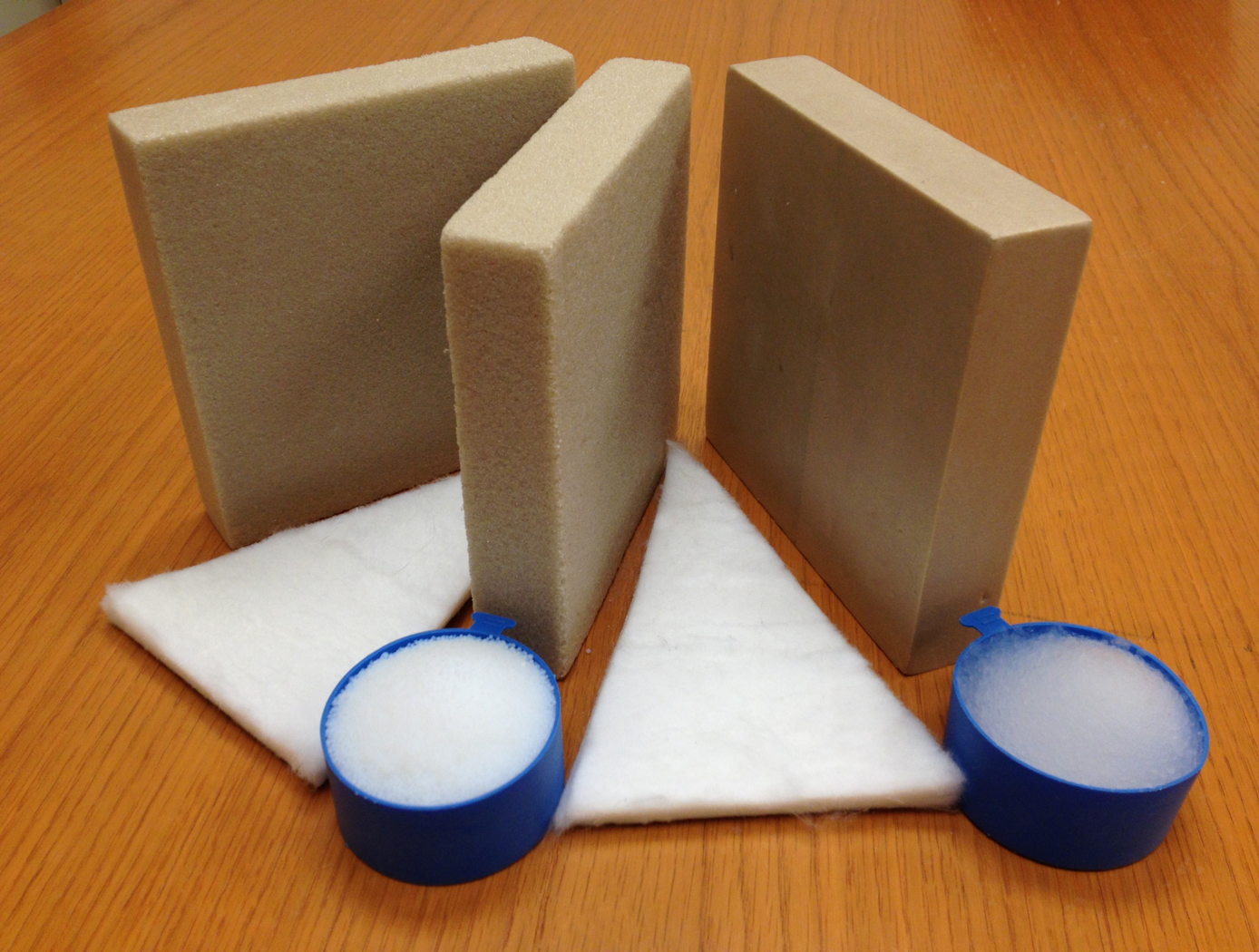
Aerofoam
The Aerofoam composites have superior thermal and acoustic insulation properties when compared to conventional polyimide foams. In addition, they provide greater structural integrity than the fragile aerogel materials can provide independently. In general, polymer foams can provide excellent thermal insulation, and polyimide foams have the additional advantage of excellent high-temperature behavior and flame resistance compared to other polymer systems (they do not burn or release noxious chemicals). Incorporating aerogel material into the polyimide foam as described by this technology creates a composite that has been demonstrated to provide additional performance gains, including 25% lower thermal conductivity with no compromise of the structural integrity and high-temperature behavior of the base polyimide foam. The structural properties of Aerofoam are variable based on its
formulation, and it can be used in numerous rigid and flexible foams of varying densities.
Aerofoam has a number of potential commercial applications, including construction, consumer appliances, transportation, electronics, healthcare, and industrial equipment. In addition, these high-performance materials may prove useful in applications that require insulation that can withstand harsh environments, including process piping, tanks for transporting and storing hot or cold fluids, ship and boat building, and aerospace applications.
Materials and Coatings
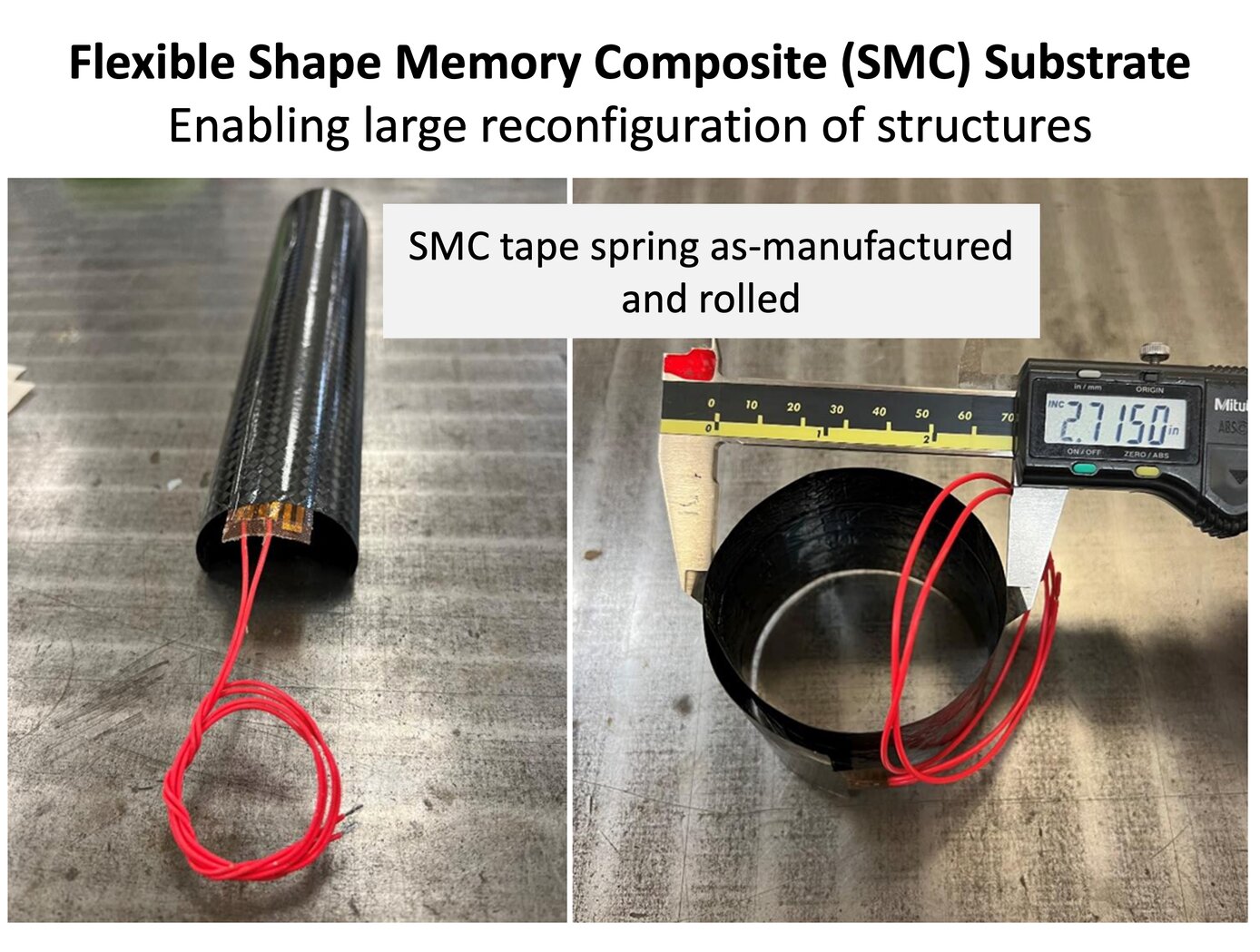
Novel Shape Memory Composite Substrate
The new SMC substrate has four components: a shape memory polymer separately developed at NASA Langley; a stack of thin-ply carbon fiber sheets; a custom heater and heat spreader between the SMC layers; and integrated sensors (temperature and strain). The shape memory polymer allows the as-fabricated substrate to be programmed into a temporary shape through applied force and internal heating. In the programmed shape, the deformed structure is in a frozen state remaining dormant without external constraints. Upon heating once more, the substrate will return slowly (several to tens of seconds) to the original shape (shown below).
The thin carbon fiber laminate and in situ heating solve three major pitfalls of shape memory polymers: low actuation forces, low stiffness and strength limiting use as structural components, and relatively poor heat transfer. The key benefit of the technology is enabling efficient actuation and control of the structure while being a structural component in the load path. Once the SMC substrate is heated and releases its frozen strain energy to return to its original shape, it cools down and rigidizes into a standard polymer composite part. Entire structures can be fabricated from the SMC or it can be a component in the system used for moving between stowed and deployed states (example on the right). These capabilities enable many uses for the technology in-space and terrestrially.
manufacturing
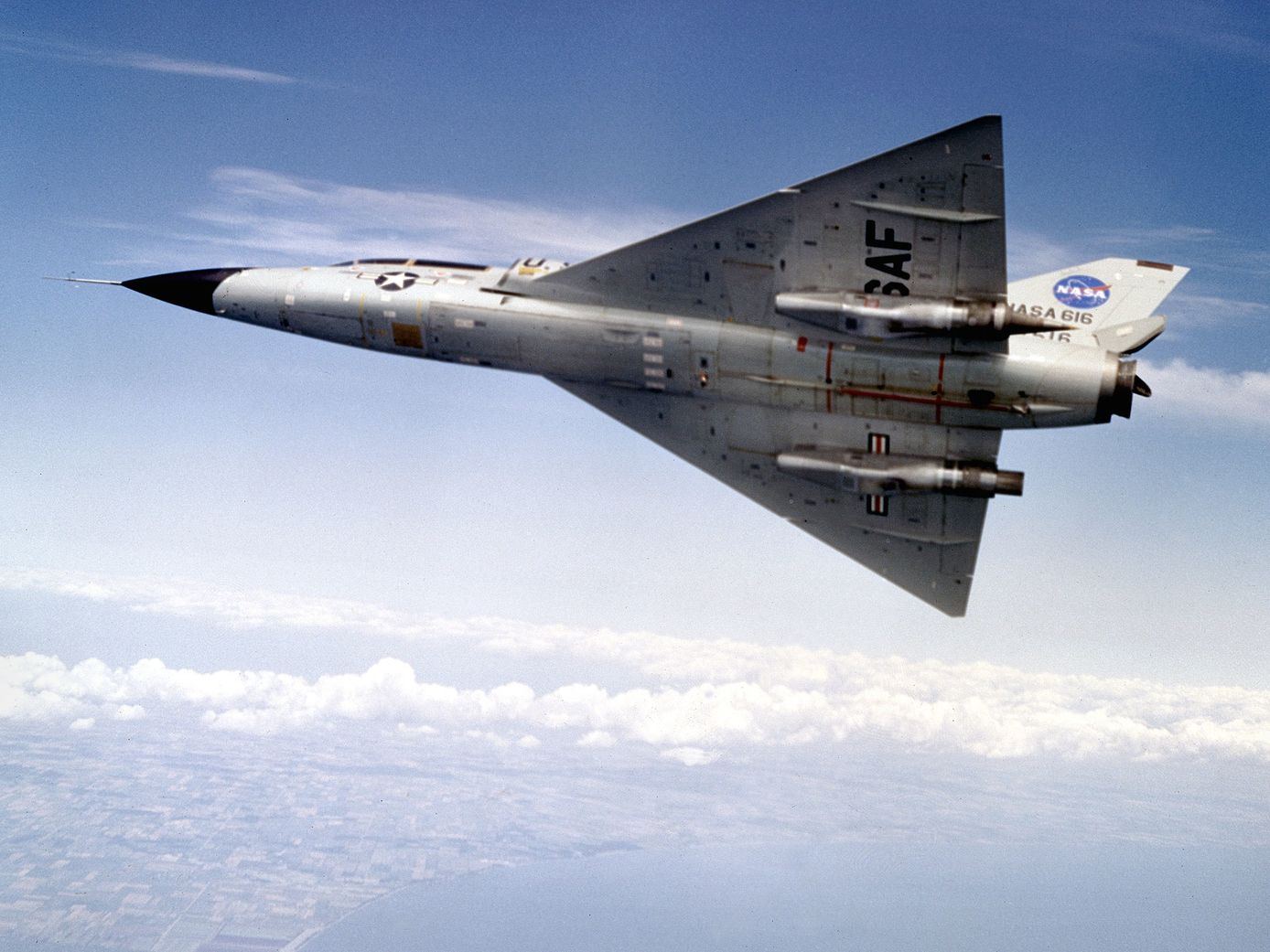
AERoBOND: Large-scale Composite Manufacturing
This technology (AERoBOND) enables the assembly of large-scale, complex composite structures while maintaining predictable mechanical and material properties. It does so by using a novel barrier-ply technology consisting of an epoxy resin/prepreg material with optimal efficiency, reliability, and performance. The barrier-ply materials prevent excessive mixing between conventional composite precursors and stoichiometrically-offset epoxy precursors during the cure process by forming a gel early in the cure cycle before extensive mixing can occur. The barrier ply is placed between the conventional laminate preform and the stoichiometrically-offset ply or plies placed on the preform surface, thus preventing excessive mass transfer between the three layers during the cure process. In practice, the barrier ply could be combined with the offset ply to be applied as a single, multifunctional surfacing layer enabling unitized assembly of large and complex structures. The AERoBOND method is up to 40% faster than state-of-the-art composite manufacturing methods, allows for large-scale processing of complex structures, eliminates the potential for weak bond failure modes, and produces composites with comparable mechanical properties as compared with those prepared by co-cure.
Materials and Coatings

Carbon Fiber-Carbon Nanotube Yarn Hybrid Reinforcement
NASA's new material is a toughened triaxial braid made from ductile carbon nanotube (CNT) yarn hybridized with carbon fiber, which is ultimately used as reinforcement material to make toughened polymer matrix composites. The CNT yarn component of the reinforcement is solely responsible for adding toughness, while the processes used to optimize the fiber braiding parameters and tensile properties of the carbon fiber-CNT yarn hybrid tow material determine the overall improvement in tensile strength for resin impregnated fiber tows. Bundles of continuous carbon nanotube yarns are combined with a similar format of carbon fiber, yielding an easily scalable process.
Advantages of the material include reduced cost by eliminating use of toughening agents, increased ability to conform to highly complex geometries, greater environmental stability compared to aramid fiber reinforcements such as Kevlar, and possibly decreased density. Many hybrid reinforcements exhibit interfacial compatibility issues, which could lead to premature failure via crack propagation at the polymer matrix interface. In contrast, chemical similarities between the CNT yarn and carbon fiber constituents impart NASA's hybrid reinforcement material with excellent interfacial compatibility.
Potential applications include aerospace components, composite pressure vessels, wind turbine blades, automotive components, prosthetics, sporting equipment, construction reinforcement material, and other use-cases where strength-to-weight ratio is of utmost importance.
materials and coatings
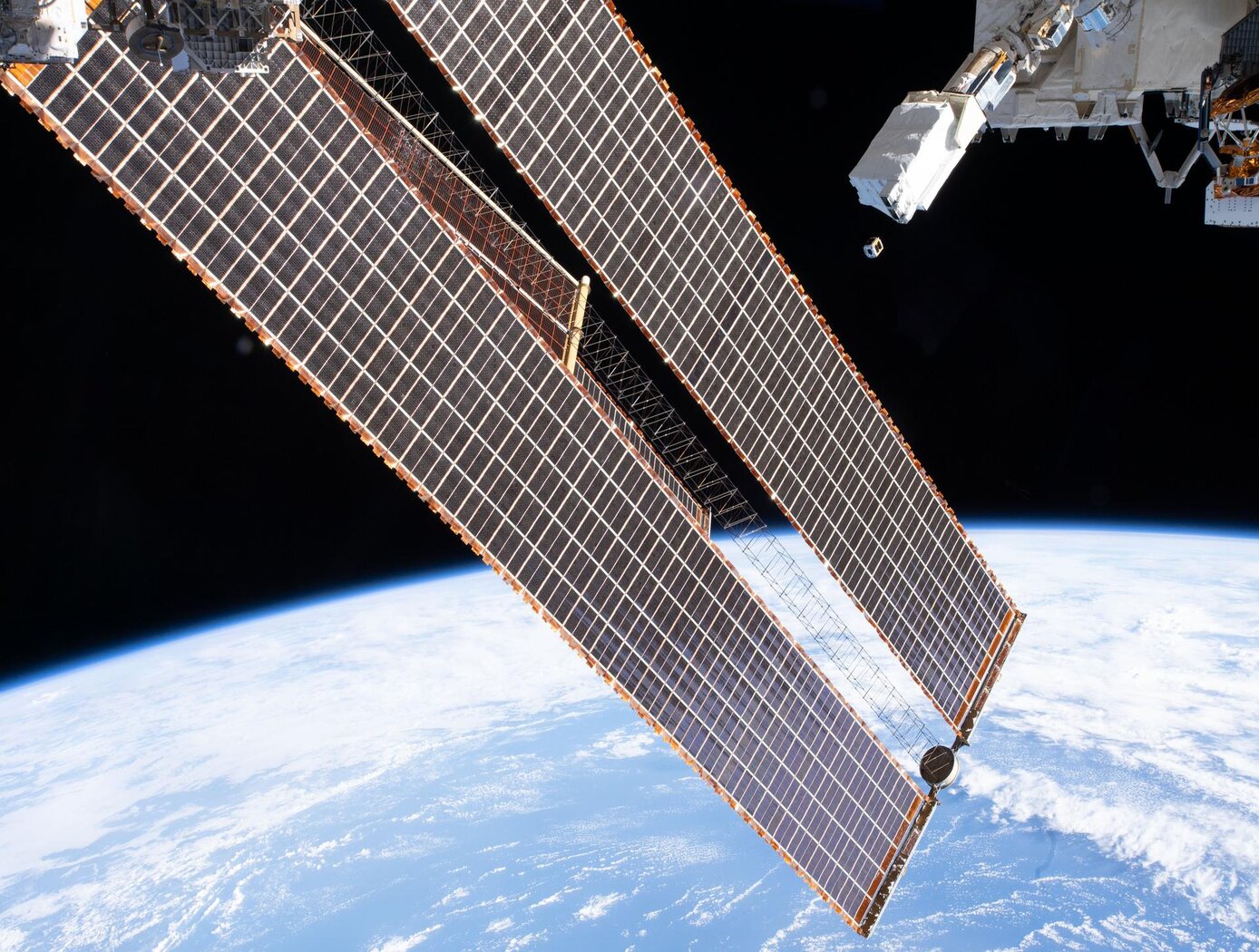
Origami-based Deployable Fiber Reinforced Composites
Deployable space structures often rely upon telescoping or folding structures that either must be manually deployed or deployed by attached motors. These structures are often made from heavier (relative to carbon fiber composites) metals to provide enough strength to support a load. As such, there is a need for in-space structures that are lightweight, can be packaged compactly, and can be deployed easily.
The composite material developed here does not require high temperature baking to cure the polymer, rather relying on UV light to solidify the polymer component. The composite is then included into origami-based structures that can fold and deploy using the polymer shape memory effect. The composite is first trained to assume the deployed structural shape when heated; it is then folded like origami and frozen into the packaged shape for storage and launch. Combining the composite material with the origami-inspired design leads to high strength structures (can hold at least 600 kg on Earth). To date, a ~5-inch prototype structural bar has been produced using the UV-curable composite and further development is on-going at NASA Langley.
The deployable origami composite structures are at technology readiness level (TRL) 4 (component and/or breadboard validation in laboratory environment) and are available for patent licensing.
materials and coatings

Conductive Carbon Fiber Polymer Composite
The new composite developed by NASA incorporates PGS and CNTs to enhance its thermal conductivity while preserving the mechanical properties of the underlying carbon fiber polymer composite. NASA has also improved the composite manufacturing process to ensure better thermal conductivity not only on the surface, but also through the thickness of the material. This was achieved by adding perforations that enable the additives to spread through the composite.
The process for developing this innovative, highly thermally conductive hybrid carbon fiber polymer composite involves several steps. Firstly, a CNT-doped polymer resin is prepared to improve the matrix's thermal conductivity, which is then infused into a carbon fiber fabric. Secondly, PGS is treated to enhance its mechanical interface with the composite. Thirdly, perforation is done on the pyrolytic graphite sheet to improve the thermal conductivity through the thickness of the material by allowing CNT-doped resin to flow and better interlaminar mechanical strength. Finally, the layup of PGS and CNT-CF polymer is optimized.
Initial testing of the composite has shown significant increases in thermal conductivity compared to typical carbon fiber composites, with a more than tenfold increase. The composite also has higher thermal conductivity than aluminum alloys, with more than twice the thermal conductivity of the Aluminum 6061 typically used in the aerospace industry. For this new material, NASA has completed a proof-of-concept demonstration and work continues to use the material in a heat exchanger system and further characterize the properties including longevity and radiation impact analysis.
materials and coatings
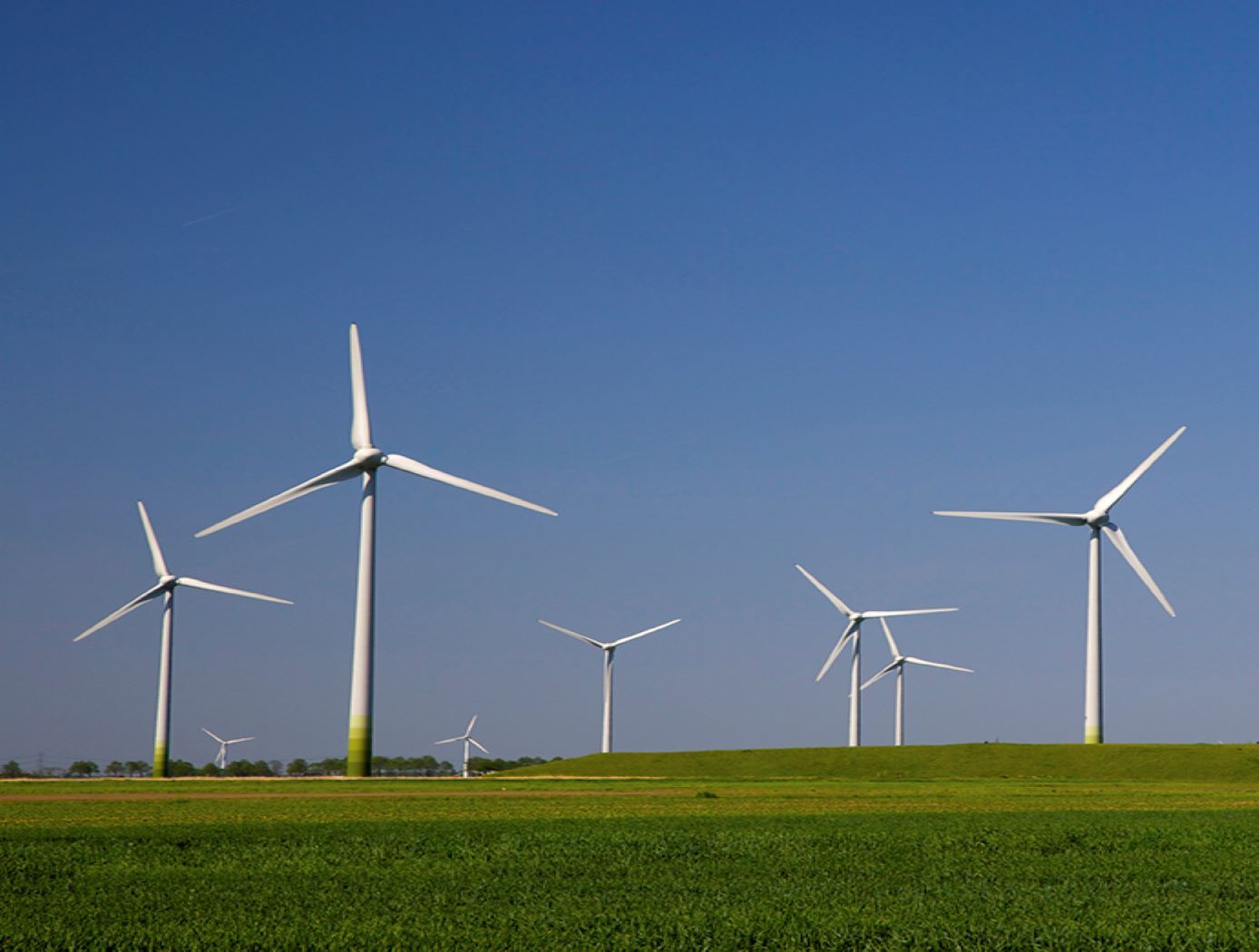
Vertically Aligned Carbon Nanotubes
Formation of the inventive polymer composite matrix begins by growing carbon nanotubes directly on a veil substrate. The carbon nanotubes are grown from both sides of a non woven carbon fiber mat. The carbon nanotubes can be single or multi walled and can be grown to predetermined lengths. The veiled substrate is positioned between carbon fiber/ polymer prepreg layers such that the carbon nanotubes protrude into the reinforcement layers. The polymer composite matrix formed following curing of the resin exhibits improved interlaminar strength, fracture toughness and impact resistance. Because of the thinness of the veil layer, electricity can pass from conductive carbon nanotubes on one side of the veil to conductive carbon nanotubes on the other side of the veil. Electricity can also pass between two veils intercalated into the same reinforcement layer when the length of the nanotubes is sufficiently long enough to provide overlap within the reinforcement layers.
Materials and Coatings

Rapid Fabrication of Boron Nitride Fine Fibers
Polymer derived ceramics (PDCs) refers to ceramic materials formed through the pyrolysis of a pre-ceramic polymer. The use of the PDC process enables the fabrication of complex, lightweight, mechanically robust shapes that are too difficult to machine otherwise. The PDC process also allows for granular control over the chemistry, resulting in better fiber homogeneity and allowing for application-specific tailoring.
NASA’s PDC process to rapidly fabricate multifunctional h-BN nanofibers entails the following steps. First a liquid-based polymer precursor solution containing boron and nitrogen is made. Next, the precursor undergoes a forcespinning process, which causes the solvent to evaporate, leaving behind only polymeric nanofiber preforms. These preforms are then cured via UV exposure or other means to link the polymer chains to one another. Finally, the crosslinked polymers are heat treated under specific conditions to convert the polymer fibers into ceramics.
This NASA innovation offers the ability to make low-cost, layered h-BN fiber mats or weaved fabrics of flexible h-BN from spun yarns at scale. The size of the fibers (> 200 nm) makes them easier to handle and disperse relative to nanotubes or nanosheets and mitigates respiratory hazards. The process offers high yields relative to alternative fabrication processes such as electrospinning. The resulting h-BN nanofibers have a broad range of potential applications and are poised to enable the development of new, multifunctional materials.
Communications

Integrated-Photonic Electromagnetic Signal Detector
NASA’s ESD is a small form-factor electromagnetic signal detector fabricated on a photonic crystal substrate (e.g., silicon-on-insulator wafer, III-V platform). It integrates a (1) miniature on-chip antenna (e.g., microstrip antenna) aligned to the desired operational frequency, (2) 2-D photonic crystal, and (3) electro-optic polymer (located on the photonic crystal).
At the heart of the detector is the 2D photonic crystal. Using an array of carefully sized pores or “nano-cavities,” a waveguide is formed that governs the crystal’s optical transmission properties. An electro-optic polymer (a material that shifts its refractive index in response to external electric fields) is used to coat the photonic crystal. The combination of the 2D photonic crystal and EO polymer make up the resonator.
A compact antenna with separate active feed and ground regions is placed near the photonic crystal, creating a gap through which the electromagnetic signal couples to the photonic crystal structure. Under normal conditions (no external signal), the EO polymer’s refractive index remains unchanged, producing a stable resonant notch in the device’s optical transmission. When the antenna intercepts an electromagnetic wave, the resulting electric field modifies the EO polymer’s refractive index, causing a measurable shift in the resonator’s optical output. By monitoring this shift, a photodetector can accurately determine the presence and magnitude of the incoming electromagnetic wave.
NASA’s low SWaP-C, high precision ESD can be adapted for use in a variety of systems including remote sensing instruments (e.g., radiometers, spectrometers), transceivers for 5G communications networks, and other electromagnetic signal detection applications. The invention is available for patent licensing.